|
2. Создание новых типов и усовершенствование конструкций конвейеров
УДК 621.867.65.011.8
В Англии за последние годы наметился прогресс в конструировании и производстве ленточных конвейеров для открытых горных разработок. Одним из преимуществ ленточных конвейеров является их высокая производительность при транспортировании различных материалов, что часто влияет на определение горнодобывающего оборудования и методы добычных работ. С другой стороны, размеры кусков и конструкция питающих приспособлений могут также влиять на ширину ленты конвейера и другие параметры системы, от чего зависит потенциальная производительность ленточного конвейера и его стоимость. В связи с этим необходима тщательная увязка всех факторов, влияющих на подбор типа и размеров конвейера.
Основные проблемы при эксплуатации ленточных конвейеров возникают, главным образом, в трех областях: приводная часть конвейера, загрузка конвейерной ленты и перемещение ленты по соответствующим опорам. Обращается внимание на необходимость центральной загрузки ленты конвейера. Глубокая желобчатость и центральная загрузка конвейера обычно редко создают проблемы в перемещении конвейерной ленты. Вместе с тем периодическая подача материала на конвейер и перегрузка его всегда приводят к затруднениям в работе. Определенные трудности в работе создаются и при нарушении нормального прохождения ленты на обратной ветви конвейера. При неудовлетворительном входе ленты на концевой барабан она может сойти с центрального положения, что ухудшает работу загрузочного устройства. Для регулирования центрального положения ленты на обратной ветви обычно применяются вертикальные направляющие ролики, дающие лучший эффект по сравнению с использованием простых направляющих, приводящих к усиленному износу краев ленты. Хорошие результаты дает применение V -образных возвратных роликов, способствующих самоцентрированию ленты под влиянием собственного веса. Однако в этом случае возрастает влияние ветровых нагрузок [51].
У ленточных конвейеров длиной 240-480 м до 40% стоимости приходится на стоимость конвейерной ленты, причем с увеличением длины конвейера этот показатель возрастает до 75%. Поэтому важное значение приобретает проблема существенного увеличения срока службы лент. Наиболее эффективный путь решения этой проблемы - правильный выбор типа электропривода и его мощности с точки зрения обеспечения оптимальных условий в период пуска и вхождения в режим. Имеются следующие типы электроприводов: 1 ) не позволяющие регулировать нагрузку в пусковой период; 2) позволяющие регулировать эту нагрузку; 3) позволяющие стабилизировать эту нагрузку не только в пусковой период, но и при работе конвейера на нормальном режиме. Приводы первого типа создаются на базе двигателей с коротко замкнутым ротором и пригодны для конвейеров малой длины и производительности: приводы второго типа, создаваемые на базе асинхронных двигателей с контактными кольцами, пригодны для средней дальности транспортирования; приводы третьего типа, предназначенные для конвейеров большой длины и производительности, разрабатываются на базе различных двигателей, управляемых с использованием автоматических схем на тиристорах [52].
При транспортировании материалов на большие расстояния целесообразно применение ленточного конвейера специальной конструкции (Stereoduc), размещенного в галерее, расположенной на поперечных металлических траверсах, уложенных на подсыпке из балласта. Через каждые 5 - 10 км галерея примыкает к зданиям шириной 10 - 15 м и длиной 30 - 80 м, в которых размещаются приводные и натяжные станции, электропусковая аппаратура и устройства для телевизионного контроля за оборудованием. Достоинством системы является почти полное отсутствие обслуживающего персонала, сравнительно небольшой износ вращающихся частей конвейера [53].
За рубежом применяется конвейер типа Serpentix. Его лента состоит из отдельных звеньев, прикрепляемых одно к другому болтами. Каждое звено представляет собой сложенную вдвое резиновую прокладку, соединенную методом вулканизации с двумя лоткообразными стальными пластинами. Когда звенья соединены в бесконечную ленту, каждая из пластин образует половину лотка. Складывающиеся резиновые прокладки допускают резкие перегибы ленты и служат своеобразными карманами для удержания транспортируемого материала на горизонтальных и вертикальных кривых. В горизонтальной плоскости такая лента может изгибаться под углом до 90 при радиусе закругления всего 2,13 м. При помощи этого конвейера возможно транспортирование как порошковых, так и крупнокусковых материалов при углах подъема до 40 без применения какого-либо оборудования. Лента приводится в движение при помощи бесконечной цельносварной тяговой цепи, прикрепляемой к донной части каждого стального лотка. У каждого четвертого звена тяговая цепь крепится к роликовой каретке, скользящей вдоль стальных швеллерных рельсов. На каждой каретке предусмотрены два горизонтальных и два вертикальных ролика. Необходимое натяжение обеспечивается при помощи грузового блочного устройства, либо посредством подпружиненных натяжных стержней. Лента может обеспечить боковую разгрузку материала путем ее наклона в процессе движения до угла 90°. Для этой цели используются направляющие швеллеры, по которым скользят опорные ролики кареток [54].
Запатентован пневматический конвейер для транспортирования сыпучих с.-х. продуктов (зерно, клевер, люцерна и т.д.). Особенность конвейера - наличие направляющего щита за выходным раструбом вентилятора в начале прямолинейного транспортного желоба, облегчающего заполнение конвейера. Кроме того, относительно большое пространство для засыпки транспортируемого материала позволяет производить загрузку транспортируемого средства без промежуточных операций по перекидке механизированным или ручным способом. К выходному раструбу вентилятора 1 (рис. 7) присоединена своим большим диаметром промежуточная переходная часть 2 конвейера, с которой соединен прямолинейный желоб 3, ведущий к выходной горловине 4 конвейера. Желоб 3 может также непосредственно присоединяться к вентилятору 1 без переходной части 2. По бокам желоба 3 сделаны продольные каналы, частично открытые внутрь желоба. Вертикальные стены этих каналов, расположенные внутри желоба, создают стены открытого лотка 7, заполняемого транспортируемой массой. Боковые стены каналов открыты внутрь желоба благодаря продольным прорезям, проходящим почти по всей длине желоба 3. При этом длина А транспортного желоба больше его ширины В не менее, чем в 1,5 раза. Поперечное сечение частично открытых боковых каналов желоба в их начальной части увеличено, что создает так называемые входные диффузоры 8. На остальной длине сечение каналов остается постоянным.
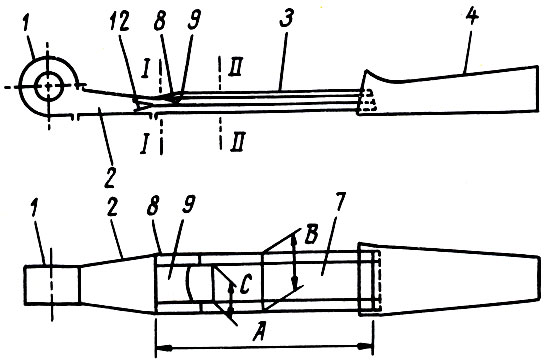 Рис. 7. Пневматический конвейер
Расположенный в начале желоба 3 щит для направления воздуха из вентилятора выполнен в виде наклонной плиты 9, помещенной между открытыми боковыми каналами желоба, или клина в переходе 2, выходная кромка которого направлена в сторону вентилятора 1 (на рисунке не показана). Ширина С направляющего щита 9 меньше ширины В желоба 3 и равна ширине открытого засыпного пространства конвейера. Для повышения производительности конвейера можно устроить нижний канал, проходящий по всей длине желоба или только по его части. Для создания такого канала над днищем желоба 3 параллельно ему укрепляется промежуточная перегородка. В переходной части 2 конвейера устанавливается регулировочная заслонка 12, которая при использовании промежуточной перегородки управляет распределением воздуха, подаваемого над перегородкой и под ней. Промежуточная перегородка, находящаяся над днищем желоба 3, может быть съемной и заменяться другой - со щелями или от-эерстиями. Вместо нижнего канала, устраиваемого между перегородкой и днищем желоба, конвейер может быть снабжен также двумя закрытыми дополнительными каналами, сделанными вне открытых боковых каналов, упомянутых выше. При работе конвейера вентилятор 1 нагнетает воздух в переход 2, где регулировочная заслонка 12 распределяет его в определенной пропорции над перегородкой и под ней в зависимости от вида и удельного веса транспортируемого материала, расстояния транспортирования и т.д. Транспортируемая масса подается в открытое наполнительное пространство 7 желоба 3, падая сверху или подгребается с уровня земли. Оттуда она увлекается воздухом, протекающим между днищем желоба 3 и промежуточной перегородкой и по открытым боковым каналам подается к горловине конвейера 4 [55].
В 1970 - 1971 гг. широкое применение на шахтах, рудниках и обогатительных фабриках нашли вибрационные транспортирующие машины. Исследования вибротранспортирования липких насыпных грузов, в том числе и марганцевой руды показали, что оптимальным режимом работы грузонесущего органа является бигармонический режим колебания; установки с такими колебаниями рабочих органов признаны одним из перспективных средств транспорта. Известные в настоящее время виброустановки для руды с бигармоническими колебаниями рабочего органа УВР-1, УВР-3 показали возможность значительного повышения скорости транспортирования отбитой руды. При этом уменьшились вредные резонансные явления, связанные с пуском и выбегом рабочего органа. Несмотря на нкоторые конструктивные недостатки виброконвейеров, их целесообразно и экономически выгодно использовать в качестве средств доставки грузов, особенно по нисходящим выработкам. Виброконвейер с бигармоническим возмущением рабочего органа может дать гораздо большую эффективность, чем виброконвейер гармонического возмущения. Транспортирование отбитой руды на короткие расстояния при помощи виброустановок, работающих на оптимально подобранных бигармонических режимах колебания, может найти широкое применение на открытых разработках и обогатительных фабриках. Проведенные в ин-те горной механики АН Грузинской ССР исследования показали, что вибротранспортирующие машины можно применять для среднекусковатой марганцевой руды, а скорость вибротранспортирования наиболее эффективна при сдвиге фаз первой и второй гармонии на 90°. Наибольший технико-экономический эффект ожидается при использовании вибротранспортных установок в качестве питателя на коротких расстояниях [56].
Для участковых выработок шахт Карагандинского бассейна разработан виброконвейер-бункер, который состоит (рис. 8) из одной приводной 2 и линейных 1 секций перекрывающегося лотка 4 и маслостанции 3. В приводной секции имеются два рештака 5, которые не связаны один с другим и совершают колебания в противофазах. Рештаки опираются на раму привода при помощи резиновых амортизаторов 6. Привод конвейера включает электродвигатель 7, одноступенчатый редуктор 8 и четыре шатуна 9. Последние попарно крепятся к желобам. Линейная секция состоит из рештака и рамы, соединенных между собой резиновыми амортизаторами. Борта рештаков наращиваются листами 10. Одна из сторон днища, перекрывающая лоток 4, связана шарниром 11 с головной линейной секцией. Гидроцилиндр 12 крепится к днищу лотка масляного насоса [57].
За последние 15 лет значительное развитие получили электромагнитные приводы вибрационных конвейеров. Их преимущества: 1) отсутствие вращающихся или скользящих элементов, минимальный уход, возможность работы в любых климатических условиях, взрывопожаробезопасность; 2) возможность бесступенчатого регулирования и дистанционного управления, например, с центрального пульта, удаленного на многие километры; 3) четкая работа в качестве бункерных затворов и питателей, выдающих груз потоком заданной производительности независимо от крупности частиц и исключающих дополнительное оборудование по борьбе со сводообразованисм; 1) отсутствие периодов разгона и замедления, определяющее их гибкость при регулировании потоков грузов и четкость работы в автоматизированных системах.
Современные конструкции электромагнитных вибраторов обеспечивают их устойчивую работу при любых колебаниях напряжения в силовой сети. Характерно применение специальных сталей повышенной прочности, износоустойчивости, стойкости против коррозии действия химических веществ высоких температур, а также пластмасс (твердого полиэтилена, полиуретана) и резин различных марок [58].
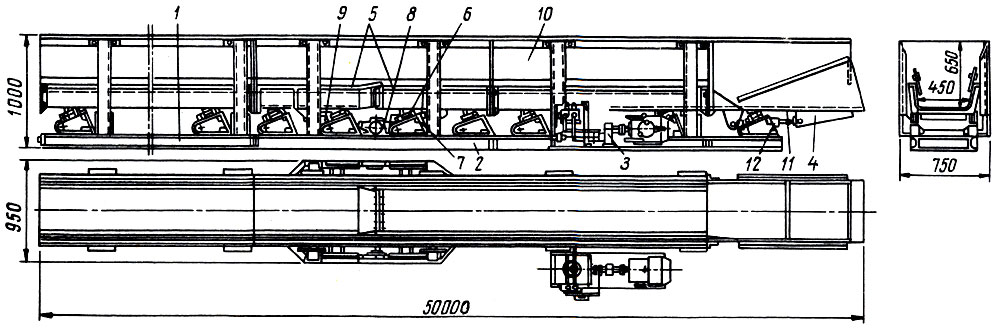 Рис. 8. Виброконвейер-бункер
На одной из электростанций Франции для транспортирования золы от четырех котельных установок к сборному бункеру установлен катковый пластинчатый конвейер специальной конструкции фирмы Auround Fbrdererbau (ФРГ), Пластины конвейера, выполненные в виде лотка, опираются одним концом на ось, прикрепленную к пластинчатым цепям, другим - на катковую ось, перемещающуюся по рельсам. На этот конец впереди находящейся пластины, опирающейся на ролики, ложится последующая пластина, концевая часть которой опирается на цепную ось, в результате чего, помимо перекрытия пластин, осуществляется одновременно разгрузка тяговых цепей от вертикальных усилий. При разгрузке на промежуточной разгрузочной станции передний конец пластин, прикрепленный к натянутым цепям, продолжает перемещаться горизонтально на прежнем уровне, а конец, прикрепленный к каткам, опускается вместе с ними по изогнутому, опускающемуся контуру рельсов, обеспечивая наклон пластин и их разгрузку. После сравнения различных вариантов транспортных установок для указанного случая был выбран вариант с одним замкнутым кольцевым конвейером, проходящим одновременно под всеми четырьмя выпускными отверстиями котельных установок, расположенных по углам четырехугольника. Диаметр кольцевого конвейера составляет 8,3 м. Преимущество этого варианта - наличие лишь одного конвейера и отсутствие обрат-вой нижней ветви. Вместо дорогостоящей цепи в качестве тягового органа конвейера были применены кольца, изготовленные из швеллеров, которые соединяются через определенные промежутки распорными поперечными трубами, служащими одновременно несущими осями для пластин конвейера. Пластины длиной 800 мм имеют в плане трапециевидную форму для того, чтобы они легко входили одна в другую. Привод конвейера фрикционный. Различная окружная скорость вращения тяговых колец достигается в результате применения фрикционных дисков разного диаметра. Получающееся различие высот опорных поверхностей выравнивается за счет использования для колец швеллеров разного профиля. Двигатель привода, имеющий мощность 4 л .с, при 20 об/мин, создает крутящий момент на выходном валу, равный 143 кГм, который передается терез упругую муфту на приводной вал. Требуемая производительность транспортирования золы 200 кг/ч при ее насыпном весе 1,6 т/м несмотря на небольшую ширину пластин, равную 300 мм, обеспечивается при скорости транспортирования 0,1 м/сек. Конвейер собирает горячую золу от всех четырех котельных установок и перемещает ее к разгрузочному месту, расположенному перед приводом. В этом месте направляющие рельсы опускаются, пластины наклоняются и материал высыпается в сборный бункер подъемника. При заполнении бункера автоматически включается подъемник и одновременно отключается конвейер. После 6 лет эксплуатации описанного конвейера не обнаружено заметного износа трущихся элементов [59].
В шахте putnam Coal Mine (США) добывается битуминозный каменный уголь, который транспортируется цельным односекшюнным канатно-ленточным конвейером протяженностью 8,2 км. Выбору наземных средств транспортирования угля предшествовало тщательное изучение всех возможных вариантов, в том числе: мощных большегрузных автопоездов; нерасчленяемых ж.-д. составов, а также новейших транспортных систем, включая систему Deshaveyor. В итоге выбраны высокопроизводительные ленточные конвейеры.
Добываемый в шахте уголь транспортируется на поверхность с помощью наклонного ленточного конвейера протяженностью 573 м, общий подъем которого составляет 156 м. Производительность этого конвейера 1440 т/ч. После взятия пробы, обработки и временного хранения уголь равномерно загружается на наземный канатно-ленточный конвейер, ведущий к береговой углепогрузочной установке. Благодаря использованию промежуточного склада и равномерной загрузке ленты, предполагается обеспечить устойчивую производительность конвейера, равную 1080 т /ч. Конвейер выгружает уголь в береговой силос емк. 10800 т, откуда с помощью ленточного конвейера длиной 671 м уголь грузится в баржи.
Фирме Cable Belt, Ltd (Англия) был сделан заказ на изготовление и монтаж канатно-ленточного конвейера. Экономический анализ показал, что по капитальным и эксплуатационным расходам и по продолжительности строительства, а также с точки зрения надежности канатно-ленточный конвейер имеет существенные преимущества перед другими типами ленточных конвейеров: отсутствие промежуточных перегрузочных станций, минимальное количество подшипников и точек контактирования ленты с прочими элементами системы. Количество подшипников здесь примерно в 4 раза меньше, чем у обычного ленточного конвейера, отсутствуют желобчатые роликоопоры и роликоопоры холостой ветки ленты. Из движущихся элементов контактируют только стальные проволочные канаты и шкивы. При канатно-ленточном конвейере нет контакта ленты с роликоопорами и транспортируемый материал не налипает, как обычно, на роликоопоры. Привод конвейера сосредоточен, и потребная мощность составляет всего 40% по сравнению с обычным конвейером. Износ боковых кромок ленты исключен, поскольку последняя лежит на несущих стальных канатах. Наиболее слабое место канатно - ленточного конвейера - его стальные канаты, которые подвергаются интенсивному натяжению и являются несущим органом системы. Естественно, канаты изнашиваются здесь в наибольшей степени. Ознакомление с 20 канатно-ленточными конвейерными системами показало, что срок службы канатов колеблется от 1,5 до 6 лет [60],
Повышению срока службы конвейерных лент служат испытания нового типа гибкой опоры, проведенные на ленточных конвейерах, установленных на шлакоперерабатывающем заводе фирмы Slag Engineering Со. (Чикаго), обслуживающем сталелитейные заводы International Harvesters Wisconsin Steel Division. Срок службы конвейерных лент здесь составлял 6 месяцев. Интенсивный износ лент был вызван тяжелыми условиями, связанными с круглосуточной, непрерывной эксплуатацией конвейерной системы завода, перерабатывающей горячий (с температурой до 80°), влажный гранулированный шлак, а также в результате заклинивания опорных роликов из-за засорения шлаком.
Опорный ролик гибкой опоры типа Limberoller выполняется из отрезка стального троса с напрессованным поверхностным слоем из мягкого неопрена и напрессованными дисками из жесткого неопрена. Каждый такой гибкий опорный ролик вращается в подшипниках, располагаемых на его концах. Испытания проводились на наиболее напряженных участках конвейерной системы при падении на конвейерную ленту 300 мм кусков шлака с высоты 3,6 м. При использовании гибкой опоры, воспринимающей ударные нагрузки, срок эксплуатации конвейерных лент увеличился с 6 до 2 6 м-цев. Значительно сократились затраты на техническое обслуживание и замену поврежденных опорных роликов и очистку конвейеров. Замена стального опорного ролика осуществлялась двумя рабочими в течение 1 ч. На замену неопренового ролика нового типа требуются минуты .Благодаря внедрению гибких опор из неопрена производительность конвейерных систем увеличилась на 40% [61].
Запатентовано устройство ленточного конвейера с изгибом в центральной части перевода ленты из горизонтального положения в наклонное. Ранее применяемые схемы конвейеров подобного типа выполнялись из отдельных элементов и имели существенные недостатки. Предлагаемый конвейер (рис. 9) имеет наружную 8 и внутреннюю 9 ленты. Перевод внутренней ленты из горизонтального положения в наклонное осуществляется путем установки ролика 5 на верхней ветви конвейера и ролика 7 на нижней ветви конвейера. Привод внутренней ленты производится от переднего приводного ролика 1. Задний ролик 2 - ведомый. Груз транспортируют на наружной ленте 8 . Эта лента натянута между роликами 3 и 4. Привод наружной ленты осуществляется за счет трения, создаваемого между внутренней и наружной лентами. Верхние ветви лент конвейера поддерживаются роликами 1 0 для образования желобчатости, а нижние - горизонтальным роликом 11. Указанная конструкция позволяет ликвидировать углубление в месте перегиба, т.е. избежать основного недостатка существующих конвейеров. Горизонтальная ветвь конвейера расположена под землей и транспортируемый материал подается на нее через отверстия [62].
Фирмой Pikrose, Ltd (Англия) изготовлен удлиняющийся ленточный конвейер Super 500, который предназначен для работы в подземных выработках. Для конвейера достаточна высота штрека 1,52 м. Специальный узел обеспечивает натяжение и изменение длины ленты в пределах 64 м без прекращения работы конвейера. Конвейер имеет гидравлическую лебедку, убирающую ленту на кольцевой приемник при обратном ходе конвейера. При прямом ходе лента выбирается из приемника в соответствии с продвижением забойного оборудования. Натяжение ленты автоматически контролируется микровыключателем и гидроцилиндром. В случае падения давления ниже 70,3 кг/см2 микровыключатель включает лебедку для восстановления необходимого натяжения ленты. Если давление превышает 105,5 кг/см2, выключаются замки и забойное оборудование получает возможность выбирать ленту из магазина для удаления конвейера. Предусмотрена возможность подсоединения дополнительных секций ленты для удлинения конвейера за пределы 64 м [63].
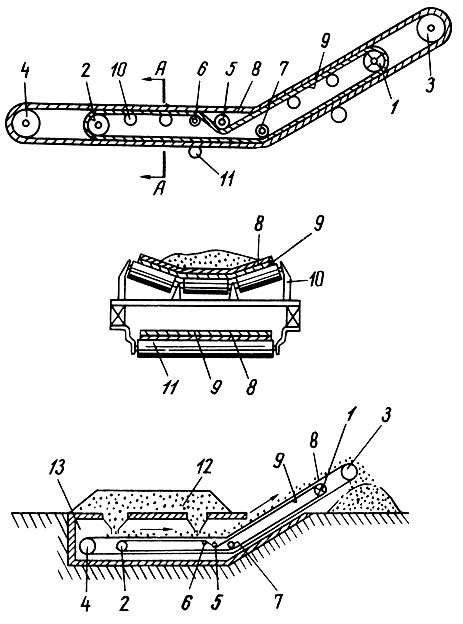 Рис. 9. Ленточный конвейер с усовершенствованием в месте вертикального перегиба
Фирма Fried Krupp GmbH Maschinen - mid Stahlbau Rheinhausen 1 ФРГ] получила заказ от Испанского государственного горно-строительного общества спроектировать систему ленточных конвейеров длиной около 100 км, по которой, начиная с 1972 г., предполагается транспортировать до 2000 т/ч фосфата от рудника Bucraa в Западной Сахаре до порта El Aaiun на атлантическом побережье. Конвейерная система будет состоять из 11 конвейеров длиной 9 и 11 км. Конвейерная лента, изготовленная из резины со стальной основой, имеет ширину 1000 мм и общую длину 200 км. Она будет доставляться отдельными кусками длиной по 400 м и на месте соединяться путем вулканизации. Скорость ленты, перемещающейся более чем на 100 000 роликов составит 4,5 м/сек. При этом тяговое усилие достигнет 45 тыс.кг. Управление и контроль за системой автоматические. Роликовые опоры в конвейерах будут размещены в верхней ветви на расстоянии 4000 мм, и в нижней 8000 мм. Увеличение расстояния между роликовыми опорами дает значительную экономию в конструкции, поскольку уменьшается количество роликов, снижаются расходы на их доставку и хранение и упрощается техническое обслуживание.
Лента закрыта сверху и с боков, что предотвращает распыление груза и защищает его от дождя и солнечных лучей. Проведенные на специальных установках опыты показали, что такая конструкция лучше отводит тепло, т.к. внутри полузакрытой конвейерной системы возникает незначительное движение воздуха. Специальная защита разработана также от песчаной пыли. Так, шарикоподшипники роликовых осей имеют долговременную смазку и лабиринтовое уплотнение. Предполагаемый срок службы 20 лет. Бесперебойность работы конвейерной линии во многом зависит от работоспособности несущих роликов. Для наблюдения за ними и обслуживания используют одиннадцать транспортных механизмов, на два человека каждый. Объезд 10 - км участка каждая бригада будет совершать ежедневно. Будут установлены также детекторы, с помощью которых можно регистрировать необычайные шумы в несущих роликах. Для определения веса транспортируемого грунта в начале конвейерной системы устанавливаются весы [64].
Производственно - исследовательским отделом Национального управления угольной промышленности Англии совместно с технологическим отделом этого же управления разработаны 3 программы для расчета конвейерных систем, используемых на угольных шахтах для подачи ископаемого от забоев к шахтному подъемнику. Наиболее простая программа Simbelt предназначена для ориентировочных расчетов суммарной емкости бункеров в точке перевалки грузов, при условии, что производительность конвейерной системы претерпевает изменения во времени, тогда как производительность подъемника остается постоянной. Программа дает возможность производить более детальные расчеты как системы в целом, так и отдельных ее составляющих, включая выбор мест расположения бункеров, через которые стыкуются конвейерные системы.
Программы опробовались в течение трех лет и после соответствующей корректировки переданы для внедрения. Работы велись на ЭВМ IBM 360/50, установленной в вычислительном центре г. Кэннок. Ввод информации осуществляется при помощи перфокарт. Программа Simbelt. опробована при проектировании и расчете системы конвейерного транспорта, обслуживающей две смежные шахты с суточной производительностью по 17,5 тыс. т каждая. При этом предполагалось, что при внезапном выходе из строя пришахтной углеобогатительной фабрики непрерывность выдачи ископаемого подъемником будет обеспечена за счет использования резервного вагонного парка в качестве аварийного склада на колесах [65].
Во Франции запатентовано устройство для очистки лент от приставшего к ним материала, особенно эффективное в случае перемещений конвейером вязких и сильно налипающих материалов. Обычно применяемые в этих случаях скребки и щетки забиваются и быстро выходят из строя, лента конвейера утяжеляется, что ведет к значительному износу вращающихся частей конвейера, потере расчетной производительности, увеличенному расходу электроэнергии. Устройство представляет собой ряд башмаков стреловидного профиля, прижимающихся к холостой ветви конвейера в непосредственной близости от приводного барабана. Благодаря тому, что башмаки впереди заострены и, кроме того, имеют скос, направленный к острию, они тем сильнее прижимаются к ленте конвейера, чем более прочным и более толстым является слой прилипшего к ленте материале. Башмаки располагаются а два ряда так, чтобы зоны действия их перекрывались. Они крепятся шарнирно на тягах, которые, в свою очередь, подвешены шарнирно в проушинах, укрепленных на раме конвейера. На тягах со стороны, противоположной башмакам, имеются противовесы, с помощью которых изменяется сила прижатия башмаков к конвейерной ленте. Для предотвращения опрокидывания башмаков или тяг с башмаками предусмотрены ограничительные упоры [66].
При конструировании ленточных конвейеров намечается тенденция изготавливать ленты из высокопрочных синтетических материалов - нейлона, рейона и других - с армированием металлическими тросами. Например, конвейеры с лентой шириной 1524 мм имеют рабочее натяжение до 136 т. Средняя ширина лент конвейеров колеблется от 914 до 1066 мм, хотя известны уникальные ленты шириной 3048 мм. Скорости движения ленты достигает 5 м/сек. Угол ияклона боковых роликов увеличился с 20 до 30,35 и 45 . При этом производительность конвейеров возрастает на 20-30%. Производительность конвейера с лентой шириной 3048 мм, при скорости движения 2 м/сек и угле наклона поддерживающих роликов 3 5 достигает при транспортировании песка и гравия 14 тыс. т/ч [67].
В ФРГ на ряде гидромеханизированных карьеров, в которых добываются песок и гравий, транспортирование материала от земснаряда на береговую обогатительную установку осуществляется цепочкой ленточных конвейеров, смонтированных на понтонах. Фирма Stichweh, выпускающая такие конвейерные системы, предложила ряд усовершенствований, повышающих надежность работы конвейеров. Вместо обычных прямоугольных или бочкообразных понтонов предлагается использовать круглые понтоны диаметром 2 м, глубиной погружения 0,7 м. Такие понтоны имеют высокую устойчивость, хорошую плавучесть и нечувствительны к обледенению. В системе автоматического управления приводами конвейеров использован механический (фрикционный) датчик, который реагирует на изменение крутящего момента на приводном валу в функции скорости ленты и при падении ее ниже 0,8 м/сек вызывает отключение привода данного конвейера и всех предшествующих [68]
Сенегальской компанией CSPT предложена передвижная конвейерная система, в которой используются три конвейера. Последний из них устанавливается и передвигается параллельно первому, второй монтируется стационарно, однако, загружается соответственно не по всей длине. Конвейеры поставлены фирмой Ste Stephanoinse de Construction Mecaniques. Общая протяженность трех конвейеров составила 2800 м. Увеличение производительности конвейеров достигается за счет повышения скорости движения ленты с 4,2 до 5,3 м/сек при условии изменения диаметра приводных барабанов. Ширина конвейерной ленты составляет 1600 мм. Конвейерная установка включает пять приводных станций, три из которых - концевые. Каждая станция имеет два приводных барабана диаметром 1 м, приводимых в действие от одного или двух электродвигателей мощностью по 265 квт [69].
Фирма Fromme Forderanlager (ФРГ) выпускает напольный, замкнутый в горизонтальной плоскости конвейер Fransi Тrеad предназначенный для транспортирования штучных грузов по любому криволинейному маршруту. Изгибание грузонесущего органа в виде членистой ленты может происходить по любому контуру с достаточно малыми радиусами сопряжений. Лента образована пластинами-сегментами серповидной формы, заходящими одна на другую. Сверху на сегменты напылен слой пластмассы с фрикционными свойствами. Снизу пластины сочленены одна с другой посредством шарнирных тяг, снабженных направляющими роликами с вертикальной осью вращения, которые движутся в направляющем канале по оси конвейера, задающем профиль движения. По бокам пластины опираются на горизонтальные ролики из износостойкого материала, оборудованные специальной шумоподавляющей рубашкой. Несущая конструкция конвейера монтируется на опорных стойках регулируемой высоты в пределах 0,28 - 0,37 м. Привод членистой ленты осуществляется от цепи с толкающими кулачками, взаимодействующими непосредственно с пластинами членистой ленты. При общей длине конвейера до 50 м достаточна одна приводная станция, которая устанавливается сбоку конвейера и обеспечивает скорость движения 0,4 м/сек [70].
Фирма A.Stotz AG (ФРГ) выпускает несколько типов конвейеров с замыканием грузонесущего органа в горизонтальной или вертикальной плоскости. Тяговым органом в них служит одинарная или сдвоенная цепь. В зависимости от особенностей груза членистая лента выполняется обычной или с уплотнениями включая такие, которые допускают бестарное транспортирование сыпучих грузов. Опора для верхней ветви конвейеров - ролики либо линейки из антифрикционных материалов, включая полиамидные пластмассы. Конвейеры находят применение в различных отраслях промышленности в том числе в качестве сборочных для изделий относительно небольшого веса и габаритов [71].
В СССР запатентован самоходный изгибающийся конвейер, содержащий: раму, состоящую из шарнирно соединенных между собой концевых и средних секций с ходовыми колесамид снабженными приводными механизмами и механизмами поворота секций в горизонтальной плоскости; гибкую грузовую ленту; механизм привода и натяжения ленты и механизм управления. Для обеспечения движения всех секций по одной траектории конвейер снабжается корректирующим устройством выполненным в виде бесконечной цепи, Цепь содержит звенья Т-образного сечения, индуктивно взаимодействующие своими вертикальными пластинами с датчиками. Последние жестко устанавливаются на осях ходовых колес , воздействуя на механизмы поворота секций [72].
Днепропетровский горный институт разработал конструкцию пластинчатых конвейерных поездов для железорудных карьеров. Эти поезда представляют собой систему шарнирно соединенных между собой желобов, лотков, пластин или вагонеток, движущихся по замкнутой кривой, загружаемых или разгружаемых автоматически. Транспортные системы на основе конвейерных поездов сочетают в себе принципы действия пластинчатых конвейеров и рельсовой откатки. Конвейерный поезд опирается роликами на специальные направляющие пути и приводится в движение промежуточными гусеничными приводами. Применение конвейерных поездов позволяет повысить производительность труда при транспортировании в 1,6 - 3,9 раза по сравнению с колесными видами транспорта, а в целом по карьеру в 1,3 - 1,9 раза за счет снижения трудоемкости ремонта и передвижки путей, упразднения службы тяги и контактной сети. Расчетные затраты на 1 т сырой руды уменьшаются на 2 - 16% по сравнению с ж.-д. и автомобильным транспортом [73].
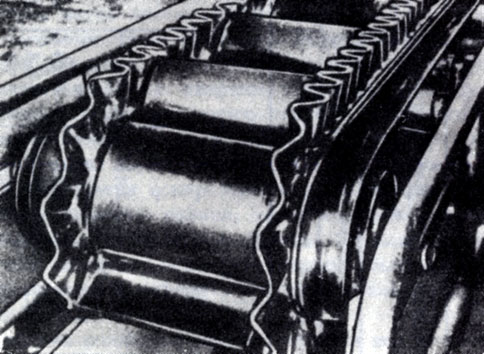 Рис. 10. Лента с гофрированными бортами
За рубежом широкое применение в горизонтальных и наклонных конвейерах находят ленты с гофрированными бортами (рис. 10). Сравнение желобчатых лент обычного типа и лент с гофрированными бортами в горизонтальных конвейерах показывает, что производительность последних при сравнимой ширине лент гораздо выше, что видно из таблицы. При составлении таблицы принято горизонтальное перемещение груза, скодюсть ленты 1 м/сек и угол откоса насыпного груза 15°.
Учитывая, что поперечное сечение материала по бортовой ленте больше, чем на обычной желобчатой той же ширины, можно для одинаковой производительности конвейерной установки применять бортовую ленту меньшей ширины. Кроме того, дорогостоящие многороликовые желобчатые опоры грузовой ветви ленты, требующие специального обслуживания, заменяются плоскими роликоопорами.
Одной из важных причин, вызвавших ускорение разработки лент с гофрированными бортами, явилось то, что применяемые до сих пор обычные лотковые ленты имели непродолжительный срок службы из-за чрезвычайно высоких нагрузок, возникающих в зонах перегиба ленты. К тому же лотковые ленты требуют переходного участка длиной свыше 1,5 м между концевым барабаном и первой желобчатой роликоопорой, необходимого для обеспечения допустимой границы растяжения бортов ленты, равной максимально 0,8%.
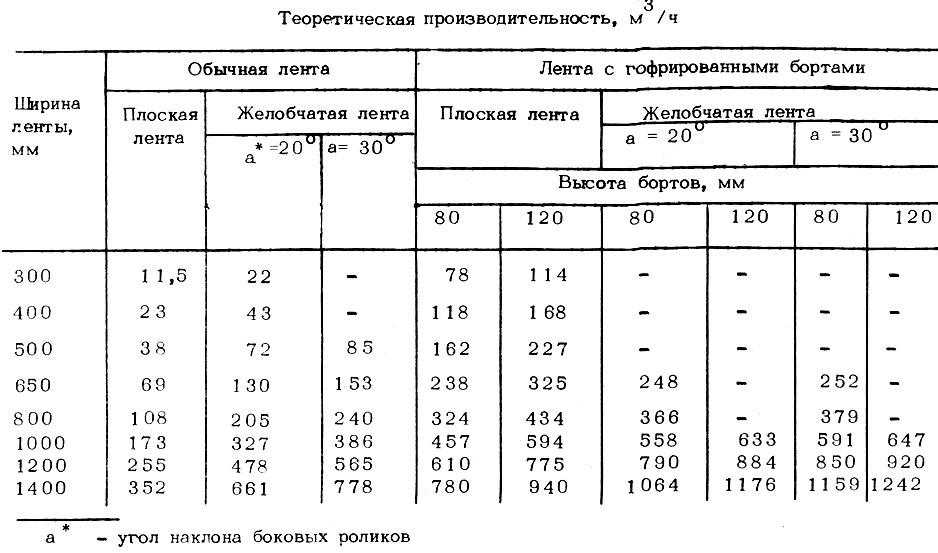 Таблица. Теоретическая производительность
Плоские ленты с гофрированными бортами не требуют никаких специальных условий. По данным фирмы Conrad Scholz AG (ФРГ) минимально допустимый диаметр барабана для этих лент составляет 160 мм при высоте бортов 80 мм и 215 мм при бортах 120 мм.
Холостая ветвь ленты может опираться на ролики двумя способами. Если жесткость гофрированных бортов достаточна для того, чтобы рассматривать их как несущий элемент, возможно опирание ленты бортами на плоский ролик. Применение этого способа ограничивается расстоянием между бортами ленты. Для широких лент, оснащенных лишь двумя бортами, в качестве несущего органа холостой ветви используются преимущественно так называемые дисковые ролики, диски которых изготовляются из резины или металла. Кроме этих двух распространенных способов, можно применять обычные плоские роликоопоры холостой ветви, располагаемые между бортами.
При лентах с гофрированными бортами исключается необходимость в оборудовании мест загрузки конвейера боковыми лотками, которые вызывают дополнительное истирание ленты и требуют специального обслуживания. Эти ленты также хорошо зарекомендовали себя при работе в качестве питающих конвейеров под бункерами.
Для наклонных конвейеров изготовляются специальные профилированные ленты с гофрированными бортами, обеспечивающие повышенный коэффициент трения. Ленты с гофрированными бортами оснащаются сплошными перегородками, заключенными между бортами так что образуются закрытые ячейки. Перегородки могут применять как прямые, так и наклонные Т-образного типа. Высота перегородок зависит от высоты бортов ленты, например при высоте бортов 80 мм высота перегородок должны быть 75 мм, при высоте 120 мм соответственно - 110 мм.
При использовании таких лент обеспечивается нормальное транспортирование сыпучих грузов при угле подъема до 75, а при особых условиях -90°.
Для практических расчетов производительность конвейера должна понижаться по сравнению с теоретической на 20 - 40%, в зависимости от характера транспортной установки транспортируемых грузов и способа загрузки ленты [74].
|
|