|
МЕХАНИЗАЦИЯ И АВТОМАТИЗАЦИЯ ПОГРУЗОЧНО-РАЗГРУЗОЧНЫХ РАБОТ НА ПРОМЫШЛЕННОМ ТРАНСПОРТЕ. В.А. Шкурин. Г.Д. Шавкин
Глава I. Состояние и перспективы развития механизации и автоматизации погрузочно-разгрузочных работ на промышленном транспорте
УДК 621.869.002.5
В 1969 - 1971 гг. в СССР на транспорте общего пользования и промышленном транспорте значительно усилена механизация погрузочно-разгрузочных работ. Одновременно с ростом производства подъемно-транспортного оборудования научно-исследовательскими и проектно-конструкторскими организациями расширены работы по созданию новых и модернизации существующих средств механизации погрузочно-разгрузочных работ. Однако в этой области не решен еще ряд важных вопросов. Медленно разрабатываются некоторые новые высокопроизводительные комплексы с часовой выработкой до нескольких тысяч тонн, особенно необходимые для оснащения пунктов перевалки. Не решена полностью задача автоматизации застропки и отстропки контейнеров и пакетированных грузов (лесоматериалов, металла, труб). Не механизированы подготовительно-заключительные операции при выгрузке сыпучих материалов из крытого подвижного состава на эстакадах и повышенных путях.
Особое место в решении задачи комплексной механизации выгрузки насыпных грузов занимает выгрузка смерзшихся грузов, которая на большинстве предприятий производится вручную, что приводит к длительным простоям десятков тысяч вагонов и приносит народному хозяйству значительный материальный ущерб, достигающий 700 - 800 млн. руб в год.
Расчеты показали, что при увеличении производства высококачественного подъемно-транспортного оборудования примерно в 1,5 раза затраты на погрузочно-разгрузочные работы снизятся в 1,5 - 2,0 раза, уровень механизации возрастет в 1,5 раза, численность рабочих снизится на 10%, а производительность труда возрастет на 40% [1].
Обследование ряда действующих предприятий выявило диспропорцию между уровнями механизации и автоматизации основных производственных процессов и погрузочно-разгрузочных и складских работ. Низкий уровень механизации работ и наличие большого количества рабочих, занятых на них, сильно удорожает производство и вызывает необходимость внедрения новых видов высокопроизводительных транспортных средств непрерывного действия. Удельный вес заработной платы рабочих, занятых на всех транспортных, погрузочно-разгрузочных и складских операциях, в общей сумме транспортных расходов колеблется в пределах от 70 до 90%. При проектировании мероприятий по механизации транспортных и погрузочно-разгрузочных работ основная экономия получается благодаря высвобождению части рабочих и, следовательно, снижению затрат на заработную плату. В то же время возрастают амортизационные отчисления, расходы на текущий ремонт, содержание и эксплуатацию оборудования, происходит перераспределение между затратами живого и механического труда, но сумма затрат на единицу перерабатываемого груза уменьшается [2].
Анализ соотношения основных и вспомогательных работ на действующих отечественных машиностроительных заводах показывает, что основные технологические операции составляют в общем производственном цикле изготовления товарной продукции 40 - 50% и вспомогательные процессы - 50-60%. Поэтому должна производиться комплексная разработка производственных процессов, позволяющая учитывать трудоемкость вспомогательных и, в первую очередь, погрузочно-транспортных работ, определять оптимальную протяженность следования грузопотоков, производить выбор средств механизации. Основой для разработки оптимального комплексного технологического процесса должны служить технологическая классификация объектов, типовые технологические процессы и организация производства на специализированных поточных линиях [3].
Уровень механизации и автоматизации погрузочно-разгрузочных работ на автотранспорте сравнительно невысок, около 68%. В результате на погрузке и разгрузке автомобилей занято 2 млн. грузчиков, а простои подвижного состава велики. Для уменьшения простоя автомобилей под грузовыми операциями целесообразно применять автомобили, оборудованные грузоподъемными механизмами: консольными и портальными гидравлическими кранами, съемными кузовами, грузоподъемным бортом. Гидрокраны моделей 4030, 4030П грузоподъемностью 500 кг, 4033-550 кг и 4032 - 1000 кг, выпускаются Львовским заводом автопогрузчиков. Последние две модели модифицированы и получили индекс 4901 и 5912. Новая модель крана 4093 грузоподъемностью 2500 кг для автомобилей ЗИЛ-1 ЗОГ и МАЗ-500 предназначена для погрузки штучных пакетных грузов, а также контейнеров весом брутто 1,25 т. В качестве другого средства механизации погрузочно-разгрузочных работ на автомобильном транспорте, помимо оборудования автомобилей кранами .применяют автомобили-самопогрузчики опытных моделей П-28, П-39, П-40, 5911 [4].
Анализ показывает, что при уровне механизации погрузочно-разгрузочных и складских работ на металлобазах близком к 1 00% удельный вес рабочих-немеханизаторов в общей численности рабочих составляет 54 - 82%. Такое положение вызывается несовершенством учета уровня механизации погрузочно-разгрузочных операций. Поэтому необходима перестройка системы учета уровня механизации [5].
Анализ расходов по складированию материалов показал, что от 40 до 93% всех производственных расходов приходится прямо или косвенно на перемещение материалов. Причинами чрезмерно больших расходов на перемещение часто являются нерациональное использование средств механизации, выполнение ненужных операций, неудачная упаковка, отсутствие необходимых технических средств, неправильные и неточные конструкции. Для достижения наибольшего эффекта необходимо, чтобы средства механизации соответствовали определенному виду транспортируемых материалов. С помощью различных вспомогательных приспособлений можно повысить производительность различных машин и расширить сферу их применения. Следует, где это только возможно, использовать для перемещения материалов ускорение силы тяжести и инерции. При возможности нужно укрупнять отдельные грузовые единицы, что позволит сократить объем грузовых операций [6].
Развитие средств обслуживания стеллажей, таких как краны-штабелеры, напольные транспортные средства и другие механизмы, позволяет лучше использовать высоту складского помещения. Применение поддонов, контейнеров, стандартной многооборотной тары требует использования механизированных и автоматизированных вспомогательных средств на складе. Экономичность складов зависит от параметров потока материалов. Следует стремиться не только к сокращению ручных операций, но также к размещению большего количества материалов на меньшей площади, к автоматизации управления потоками [7].
В США ежегодно выпускается подъемно-транспортного оборудования на 2 млрд .долл., затраты на транспортные, складские и погрузочно-разгрузочные работы составляют 30% всех прямых трудовых затрат [8].
На Ганноверской выставке 1969 г. 40 фирм представили образцы машин напольного безрельсового транспорта, большинство из которых в 1970 г., признаны устаревшими. Поэтому выбор типов машин напольного безрельсового транспорта, и прежде всего погрузчиков, следует производить с учетом основных показателей, определяющих их оптимальность как в настоящее время, так и в перспективе. Естественно важнейшими показателями эффективности погрузчиков являются эксплуатационные затраты (постоянные и переменные) и основные технические параметры машин. Стоимостными показателями являются затраты на амортизацию, ремонт, заработную плату, топливо или электроэнергию, техническими скорости подъема и передвижения, радиусы поворотов, устойчивость, собственный вес, мощность привода и др.
Анализ этих факторов с учетом конкретных условий применения позволяет правильно выбрать типоразмер погрузчика.
При выборе погрузчиков, кроме указанных выше параметров, необходимо учитывать величину ускорения и замедления их движения. Погрузчик при движении вынужден часто изменять скорость передвижения при прохождении участков поворота, узких проездов, неравномерно освещенных площадок при перевозках на короткие расстояния и т.п. Поэтому определяющим фактором является не только скорость передвижения погрузчиков, но и величина их ускорений и замедлений.
Скорость подъема и опускания груза также должны учитываться при выборе погрузчиков в зависимости от потребной высоты складирования.
Удобство работы водителя является также одним из основных требований к погрузчикам. Место установки педалей и рычагов управления, величины прикладываемых усилий, размещения сидения и другие факторы, характеризующие этот показатель, влияют на производительность погрузчика в пределах до ±20%. Габаритные размеры погрузчиков, особенно их ширина и радиусы поворота, так же влияют на выбор типов погрузчиков. Необходимо, кроме того, учитывать собственный вес погрузчиков, особенно малой грузоподъемности, так как он определяет условия их применения в многоэтажных складах, вагонах и автомобилях [9].
В области строительства напольных транспортных средств в ФРГ можно отметить три основных тенденции: расширение применения электронного импульсного управления в агрегатах с электроприводом, разработка новых моделей для сугубо специального назначения и создание особо мощных агрегатов. Применение электронного импульсного управления, базирующегося на использовании тиристоров, позволяет, кроме прочих преимуществ, экономить в процессе эксплуатации в среднем около 20% энергии батарей; при самых низких скоростях экономия электроэнергии достигает 80%. Погрузчики с импульсной системой управления целесообразно применять при коротких пробегах и многочисленных маневрах.
Особое внимание в новых конструкциях уделено комфорту водителя и легкости управления. В стандартном исполнении электропогрузчики грузоподъемностью 2,8 -3,6 т имеют максимальную скорость с грузом 12 км/ч, без груза - 15,5 км/ч, преодолеваемый подъем составляет 28%, скорость подъема груза при оснащении скоростным механизмом подъема 0,36 м/сек. Погрузчики новой серии грузоподъемностью 1,0, 1,25 и 1,6 т оснащаются электронным импульсным управлением.
Для работы в узких проходах предназначается электропогрузчик с. выдвижной грузовой мачтой, ширина которого составляет 832 - 1015 мм, грузоподъемность -800 - 1000 кг. Погрузчик может работать в проходах шириной 1830 - 2230 мм. Высота подъема груза равна 4 м.
Для обслуживания высотных стеллажей разработан электропогрузчик, который отличается от обычных погрузчиков телескопическим грузозахватным органом, выдвигающимся в обоих поперечных направлениях, благодаря чему исключается необходимость маневров внутри проходов. Во время передвижения по проходу рулевое управление погрузчика блокируется, а надежное продвижение погрузчика обеспечивается с помощью боковых направляющих полос. Таким образом, внимание водителя концентрируется лишь на операциях по загрузке и разгрузке стеллажей. Приборная доска погрузчика снабжается указателем высоты подъема груза, который может быть дополнен автоматическим устройством для выбора необходимой высоты.
Среди агрегатов, предназначенных только для горизонтального транспортирования, получают, широкое применение электротележки и электротягачи, оснащенные индукционным автоматическим управлением. В противоположность ранее применявшимся подобным агрегатам, обеспечивающим автоматическое управление передвижением только в одну сторону (вперед), новые конструкции автоматически управляют передвижением вперед и назад.
Кроме указанных агрегатов, находят распространение толкающие транспортные устройства с дистанционным автоматическим управлением, которые подъезжают лод грузовую тележку и толкают ее к месту назначения.
Для транспортирования тяжеловесных и длинномерных грузов предназначаются преимущественно погрузчики с боковым выдвижением грузоподъемного органа грузоподъемностью 3 - 13 т. Разработаны также погрузчики специально для перегрузки крупнотоннажных контейнеров. Разрабатываются фронтальные вилочные погрузчики грузоподъемностью 7 - 1 1 ,5 т.
В последние годы для транспортирования тяжеловесных грузов находят применение портальные погрузчики, грузоподъемностью 5 - 30 т, с шириной портала (в свету) 1,0 - 3,6 м и высотой 1,7 - 3,0 м [10].
В США намечается тенденция к широкому использованию в складах вилочных погрузчиков с боковым выдвижением грузоподъемника вместо обычных кранов-штабелеров. Такие погрузчики имеют меньшую стоимость, более маневренны и требуют небольших проездов между стеллажами. Электропогрузчики фирмы Raymond имеют грузоподъемность 1814 - 4536 кг, высоту складирования 6 - 9 м, скорость передвижения до 11,2 км/ч и подъема до 24 м/мин. Ширина проездов составляет 1,5-1,8 м. Автопогрузчики типа Lancer имеют грузоподъемность До 45 т и скорость передвижения до 40 км/ч. Необходимая ширина проездов 2,3 м [11].
В мае 1971 г. на выставке подъемно-транспортного оборудования в Филадельфии (США) демонстрировались погрузчики, у которых грузозахватные вилки расположены перпендикулярно к продольной оси, а также погрузчики с поворотной рамой грузоподъемника. Они обеспечивают установку длинномерных грузов на стеллажи без разворота погрузчика и работу в более узких проездах. Грузоподъемность погрузчиков 2721, 3175 и 3628 кг. Ширина проездов 1,8 м. Малогабаритные погрузчики с боковым выдвижением грузоподъемника обеспечивают складирование до высоты 7,2 м. Применение дистанционного управления на погрузчиках и вилочных тележках обеспечивает уменьшение их габаритов и работу в более узких проездах [12].
Фирма Raymound Corp. (США) выпустила новый вилочный электропогрузчик, позволяющий уменьшить ширину проходов между стеллажами в складе. Мачта нового погрузчика может выдвигаться вперед. Вилочный захват по конструкции напоминает ножницы. Новый погрузчик может брать со стеллажей два груза, расположенных один перед другим, или укладывать два груза на стеллажи. Операции по выемке и укладке грузов осуществляется при движении вилочного захвата в направлении, перпендикулярном направлению движения погрузчика, причем вилочный захват может перемещаться только в одну сторону от погрузчика. Он может поднимать грузы весом до 90 кг на высоту 10м. Аккумуляторная батарея погрузчика имеет емкость, достаточную для непрерывной работы на протяжении всей рабочей смены [13].
Сконструирован погрузчик с крестообразным движением, объединяющий в себе свойства погрузчика фронтального и бокового действия. При его эксплуатации ширина проездов, по сравнению с использованием погрузчиков фронтального действия, сокращается на 30%. Погрузчик с крестообразным движением представляет собой погрузчик фронтального действия с выдвижной подъемной мачтой, колеса которого могут поворачиваться на 90.
Одной из шведских фирм выпущены такие автопогрузчики грузоподъемностью 2000 кг при расстоянии от центра тяжести до нижней кромки вилок 400 мм, а также грузоподъемностью 1500 кг с расстоянием между указанными точками 610 мм.
Вилки погрузчиков можно поворачивать вручную и с помощью гидравлического поворотного устройства [14].
Применение автопогрузчиков с двигателями внутреннего сгорания для погрузочно-разгрузочиых работ в складских помещениях вызывает сильное загрязнение воздуха окисью углерода и другими продуктами, содержащимися в выхлопных газах. Компания Armstrong Rubber применяет в своем трехэтажном складе готовой продукции шинного завода (1,5 млн.шин) 15 автопогрузчиков для внутрискладского перемещения поддонов? вмещающих 36 шин (4 вертикальных обоймы по 9 шин, уложенные горизонтально). Для очистки воздуха применены катализаторные аппараты, выпускаемые фирмой Engelhard Minerals and Chemicals Corp. Устанавливаемые на автопогрузчик аппараты работают удовлетворительно. На радиотелевизионном предприятии фирмы Lenith Radio Corp, (США) 42 автопогрузчика и тягача с двигателями внутреннего сгорания снабжены вместо обычных глушителей катализаторными воздухоочистителями фирмы Catalyst Corp., поглощающими из выхлопных газов окись углерода и другие вредные компоненты [15].
В малогабаритных производственных и складских зданиях в ряде случаев нецелесообразно устраивать стационарные погрузочно-разгрузочные площадки, обеспечивающие погрузку и выгрузку грузов вилочными погрузчиками. В этих случаях рекомендуется убирающаяся погрузочно-разгрузочная площадка.
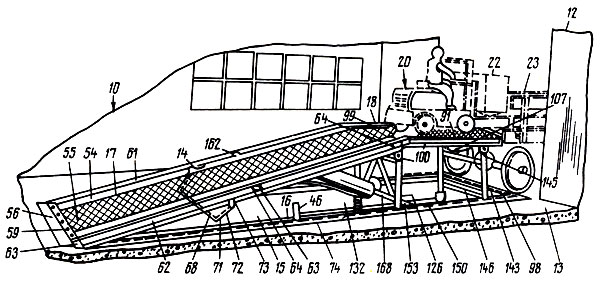 Рис. 16. Убирающаяся погрузочно-разгрузочная площадка
Она состоит (рис.16) из подъемного стола 18 и аппарели 17, шарнирно соединенных между собой, Уклон аппарели в поднятом положении 20%. Подъем и опускание погрузочной площадки осуществляются с помощью гидродомкрата 162. Погрузчик 20 везжает по аппарели и устанавливает груз 22 в подвижной состав 23. Высота подъемного стола может изменяться в зависимости уровня пола подвижного состава. Когда погрузочно-разгрузочная площадка опускается в углубление в полу здания верхняя поверхность аппарели и подъемного стола совпадает с уровнем пола [16].
Важным показателем экономичности вилочных погрузчиков является величина расходов на 1 т переработанного материала. Для ее определения необходимо знать часовые производственные расходы и производительность погрузчика. Производственные расходы состоят из постоянных и переменных. Первые складываются из амортизационных отчислений и сумм для возмещения инвестиционного капитала. Они зависят от первоначальной стоимости, срока слуюбы и процентной ставки на капитал, В СССР капитальные вложения, приходящиеся на определенное время работы машины исчисляются исходя из нормативного срока их окупаемости. Переменные расходы включают зарплату водителя, стоимость горючесмазочных материалов, обслуживания и ремонта. Часовая производительность погрузчика зависит от количества рабочих циклов за 1 ч, производительности за цикл и соответственно от грузоподъемности или объема поднимаемого груза. Производительность погрузчика является функцией продолжительности фаз рабочего цикла - ускорения и замедления, скоростей движения, подъема и опускания захвата. Для сравнительной оценки погрузчиков по производительности введен фактор преимущества V, который показывает относительное время для выполнения одной и той же работы. Так, при V = 1,36 погрузчик менее производителен по сравнению с эталонным, для которого V = 1. Знание этого фактора позволяет подсчитать экономию от внедрения более прогрессивной конструкции. Обозначив: ka - часовые производственные расходы для погрузчика A; Кb - то же для погрузчика В;kav - расходы для погрузчика А при выполнении равной с погрузчиком В работы; Eh - часовую экономию от погрузчика В, получим kaV = kav; kav - kb = εh Фактор преимущества разбивается на факторы по вертикальным операциям, ускорениям и максимальной скорости движения. Для подсчета часовых производственных затрат необходимо определить срок службы погрузчиков. Приведенная формула, включающая действительные сроки службы погрузчиков и фактор преимущества V, позволяет подсчитать условный срок службы в зависимости от производительности погрузчика [17].
Выбор типов погрузчиков производится также на основе сравнения их первоначальной стоимости и стоимости машино-часа. Однако при этом, как правило, не учитывается долговечность и надежность машин, что иногда приводит к неправильным выводам. Так, при одинаковой суточной производительности погрузчиков и разнице в стоимости машино-часа между первым и вторым погрузчиком, равной 0,17 денежных единиц, экономическая целесообразность первого погрузчика не доказана. В случае, если срок службы первого погрузчика меньше, чем второго, то и его выработка на весь срок эксплуатации также будет меньше, и, следовательно, раньше (по сравнению с другим погрузчиком) потребуется приобретение нового погрузчика. Необходимые дополнительные капитальные затраты на приобретение нового погрузчика взамен менее долговечного следует учитывать при сравнении погрузчиков. Стоимостной показатель долговечности рекомендуется определять отношением первоначальной стоимости погрузчика (числитель) к сроку службы его в годах, умноженному на годовой фонд времени в часах (знаменатель).
При различной мощности и первоначальной стоимости погрузчиков необходимо также учитывать и продолжительность их простоя в ремонтах (показатель надежности), так как в это время для обслуживания производства привлекают другие типы аналогичных погрузчиков. Анализ структуры стоимости машино-часа различных погрузчиков позволяет определить основные его составляющие [18].
Англия является одним из основных мировых экспортеров подъемно-транспортной техники. Экспонаты, представленные на 12-й Международной выставке подъемно-транспортного оборудования в Лондоне, свидетельствуют о тенденции к созданию универсального оборудования, легко приспосабливаемого меняющимся производственным условиям.
Интересен универсальный вилочный погрузчик с горизонтально выдвигающимся грузоподъемником, который без разворота корпуса перемещается в любом направлении. Благодаря наличию шасси возможны установка и снятие грузов без маневрирования машины. Применение этого погрузчика дает экономию рабочего времени и позволяет полнее использовать емкость складских помещений.
Широко были представлены на выставке также специальные самоходные подъемные тележки для отбора грузов со складских стеллажей, достигающих значительной высоты.
В состав комплексного оборудования для складов входит большое количество разнообразных устройств, в том числе: пневматические и электронные управляющие устройства, автоматические контрольные аппараты, счетчики и взвешивающие механизмы непрерывного действия. Объединение указанных элементов в единой системе позволяет получить полностью автоматизированные транспортные системы и склады. Примером могут служить центральный склад автомобильных деталей фирмы ВМС в Бирмингене и склад CWS. На этих складах ЭВМ ведут непрерывный учет наличия товара по всей номенклатуре, сигнализируют о снижении запасов до минимального уровня, сообщают об экономически целесообразных запасах и т.д. [19].
По своей конструкции и назначению электроштабелеры занимают промежуточное место между самоходными тележками с низким подъемом вилок и универсальными электропогрузчиками.
Основное преимущество этой группы машин по сравнению с погрузчиками заключается в сравнительно меньших размерах, что позволяет использовать малогабаритные машины в стесненных условиях и узких проездах внутри цехов, складов, вагонов и автомобилей, а также дает возможность многоярусного складирования.
Конструктивно электроштабелеры оформляются как 3-х или 4-х колесные самоходные тележки с приводом от аккумуляторных электродвигателей. В передней части машины монтируется грузоподъемная мачта с гидравлическим подъемом вилочной каретки или платформы. Управление осуществляется рабочим, идущим или стоящим рядом с машиной, или со специальной площадки, расположенной в торцовой части машины. Все электроштабелеры можно разделить на 2 группы. К 1-й относятся штабелеры с выносными балочными опорами, у которых центр тяжести поднимаемого груза лежит в пределах опорной поверхности штабелера, ко 2-й - построенные по той же схеме, но с противовесом. Центр тяжести перемещаемого груза у них лежит вне опорной площади штабелера. Наиболее универсальной и перспективной машиной являются высокоманевренные, малогабаритные электроштабелеры с продольным выдвижением грузоподъемника и поворотными вилками [20].
В Западной Европе произведена стандартизация мостовых кранов с жесткой подвеской, в целях сокращения их стоимости. Стандартизированная серия включает в себя краны грузоподъемностью от 800 до 5000 кг, при ширине колеи от 4 до 5 м. Высота мостовой балки варьируется от 2 1 0 до 800 мм, максимальная стрела прогиба под нагрузкой составляет 1/750 ширины проема. Вес мостовой балки значительно снижен благодаря применению специальных профилей из стали марки А 60.
Боковые габариты также доведены по минимума и составляют 400 - 705 мм для кранов грузоподъемностью 800 кг и 590 - 1035 мм для крана грузоподъемностью 5000 кг. Грузоподъемность электроталей составляет ряд 800 - 1000 - 1600 - 2000 - 3200 - 5000 кг. Скорость подъема варьируется от 4 до 12 м/мин. Подъем, передвижение и доставка груза краном производятся при помощи подвесного пульта управления [21].
К числу универсальных погрузочно-разгрузочных устройств относятся электротали, которые имеют компактную конструкцию, малый собственный вес, просты в управлении. Для их передвижения устанавливаются пути несложной конструкции. Поэтому они широко используются в народном хозяйстве как самостоятельные подъемно-транспортные машины и применяются в комплексе подъемно-транспортных устройств для решения самых разнообразных проблем механизации. В 1 967 г. завод "Подъем" (НРБ) приступил к изготовлению новой конструкции - типа Т. Это компактный электротельфер с минимальными весом и габаритными размерами, дающий возможность монтировать и демонтировать отдельные узлы (редуктор, корпус с барабаном, электродвигатель) независимо один от другого. Тельфер приспособлен для работы на открытом воздухе. Канатные электротали управляются безопасным канатным напряжением, так как на них поставлен трансформатор, питающий цепь управления. Кроме главной скорости подъема, электродвигателем можно создать и микроскорость, которая является очень удобной для разных монтажных операций. Соотношение микроскорости к главной около 1:8. Основные параметры канатных электроталей соответствуют рекомендациям СЭВ: грузоподъемность 250, 500, 1000, 2000, 3200, 5000, 8000 и 12500 кг; высота подъема 6, 9, 12, 18, 24 и 36 м; скорость подъема в соотношении 1:8, .1:6; скорость горизонтального перемещения тележки 20-32 м/мин. Тележка может быть с тормозом и без него;, для скорости 32 м/мин - только с тормозом. Параллельно с развитием канатных электроталей в НРБ созданы конструкции цепных электроталей грузоподъемностью 125-1000 кг [22].
Быстрый запуск двигателей внутреннего сгорания на кранах в холодный период года дает возможность устранить непроизводительные простои машин и увеличить срок службы двигателей, так как запуск двигателя с застывшей смазкой увеличивает износ трущихся деталей. Особенно важно обеспечить быстрый запуск двигателей кранов на гусеничном ходу, которые не могут быть заведены путем их оазгона с помощью других машин.
Для запуска двигателей кранов существуют два основных типа обогревательных устройств: электрические и работающие на жидком топливе. Электрические обогреватели являются обычно более дешевыми, однако их использование возможно лишь там, где имеются источники тока. Применяются три способа предварительного разогрева двигателя электрическими обогревателями. Первый основан на подогреве воды в системе охлаждения путем установки дополнительного бака с подогревом, соединяемого во время запуска с основной системой охлаждения блоков цилиндров. Второй способ - подогрев топлива в топливном баке. Потребляемая мощность при этих способах подогрева - от 300 до 2500 вт и дополнительно 150-700 вт для разогрева смазки. Третий способ - подогрев аккумуляторных батарей путем накрывания их электрической грелкой или установки на специальное основание, в которое вмонтированы нагревательные элементы. Потребляемая мощность 40-70 вт.
Нагревательные элементы на жидком топливе обычно работают на том же виде топлива что и двигатель крана. Выделяемое при сжигании топлива тепло используется для подогрева воды или антифриза в дополнительном баке, соединенном с водяной системой охлаждения двигателя. Нагревательные устройства снабжаются аппаратурой контроля и регулирования, позволяющей регулировать температуру нагреваемой жидкости и обеспечивать безопасность работы установки. При работе нагревательной установки выделяется тепло 18900 - 25200 ккал. Устройства обогрева используются также для прогрева гидроприводов гидравлических кранов. При этом происходит нагревание поверхности гидравлических резервуаров путем установки на них электрических нагревательных элементов. Необходимая мощность установки 2 вт на 1 см2 поверхности резервуара, или 500 вт на резервуар емкостью 115 л [23].
В подъемно-транспортных машинах большее распространение получил гидравлический привод. Его основные преимущества - надежность, относительно небольшая стоимость, возможность бесступенчатого регулирования скорости и увеличения производительности машин за счет сокращения времени цикла их работы на 20 - 35%, однако этот привод требует высокой точности в изготовлении и монтаже [24].
Эмпирическим путем установлено, что увеличение емкости кузова траншейных средств способствует повышению производительности погрузчика. Расходы, связанные с процессами погрузки и транспортирования, также находятся в тесной взаимосвязи. В связи с этим возникает задача выбора наиболее рационального с экономической точки зрения, соотношение параметров погрузочного устройства и транспортных средств. Увеличение времени, затрачиваемого на погрузку, снижает производительность парка транспортных средств и ведет к повышению транспортных расходов. Если расходы, связанные с погрузкой и транспортированием, рассматривать как единое целое, то нетрудно определить для каждого погрузочного устройства экономически выгодную емкость кузова работающего в комплексе с ним транспортного средства. Изучение указанных взаимосвязей необходимо не только при создании новых машин, но и при выборе уже применяемых погрузочных и транспортных средств [25].
Фирмой Liade AG (ФРГ) разработан и внедрен ряд тестов для испытаний погрузчиком, на автодроме" При этом учитывалось, что дальность транспортирования груза погрузчикомт как правило, не превышает 60 м. Для проведения испытаний на автодроме выделен участок размерами 2,5 м и шириной проезжей части 2,5 м по периметру с 3-ярусным стеллажем высотой 3 м [26].
Эффективное использование капитальных вложений в механизацию погрузочно-разгрузочных операций зависит не только от замены ручного труда машинным, что значительно повышает производительность труда, но и от максимального снижения затрат на транспортирование единицы продукции [27].
|
|