2. Реконструкция промышленного транспорта
За последние годы во многих странах работы по реконструкции транспорта достигают больших объемов. Как уже указывалось, они производятся на действующих предприятиях как при реконструкции основного производства, так и независимо от нее.
Можно все работы по реконструкции транспортного хозяйства промышленных предприятий разделить на две группы: первая - работы, связанные с заменой одного вида транспорта другим; вторая - работы по усилению и переустройству имеющихся на предприятиях видов транспорта (например, реконструкция тяги на железнодорожном транспорте, повышение производительности конвейерных линий и др.). Работы второй группы будут рассмотрены в главах, посвященных развитию соответствующих видов транспорта. Здесь же дается характеристика работ по реконструкции, связанных с заменой одного вида транспорта другим, что за последние годы является характерным явлением для промышленного транспорта многих стран.
Изучение проводимых в зарубежных странах работ по реконструкции транспортного хозяйства промышленных предприятий показывает, что они вызываются в основном следующими причинами:
- увеличением объема перевозок в связи с ростом мощности предприятия, в результате чего требуется увеличить провозную способность имеющихся транспортных средств.
- изменившимися в результате реконструкции предприятия условиями работы (например, увеличением глубины разрабатываемых карьеров, необходимостью занятия территории расширяющимися производственными цехами, переходом на полную автоматизацию основного производства и др.);
- неэкономичностью работы имеющихся видов промышленного транспорта предприятия.
Вот наиболее характерные примеры реконструкции транспортного хозяйства предприятий.
В США на крупном месторождении медных руд фирмы Kennecott Copper Corp. разработка ведется открытым способом уступами [46]. До недавнего времени вывозка руды и вскрышных пород осуществлялась исключительно рельсовым транспортом при дальности транспортирования руды 7,2 км и вскрышных пород 12,8км. Средний уклон пути на уступах составлял 20%0.
В связи с понижением отметок дна карьера и увеличением фронта добычи общая протяженность рельсовых путей (включая вспомогательные участки) достигла 67 км, из которых около 1/3 приходится периодически перекладывать.
Поскольку развитие системы рельсового транспорта вызывало все возрастающее удорожание работ, принято решение о постепенном переходе на смешанный способ с преимущественным использованием автомобильного транспорта. Первоначально автомобильный транспорт (семь самосвалов грузоподъемностью 40 т) использовали только на вывозке вскрышных пород, а затем, поскольку он оказался экономически эффективнее рельсового, и на основных работах.
В настоящее время работа транспортной системы организована следующим образом. Первый (от дна карьера) уступ соединен с наиболее высокой точкой борта карьера скиповым подъемником (длина трассы 420 м, перепад высот в крайних точках 178,5 м). Станция загрузки скипов оборудована эстакадой с двумя бункерами. Подвозка руды и пустой породы от экскаватора с ковшом емкостью 4,5 м3 производится 40-т самосвалами.
Подъемник автоматизирован, оборудован скипами грузоподъемностью 40 т при собственном весе 34 т. Привод подъемника от двухбарабанной лебедки, работающей от двух двигателей постоянного тока мощностью по 5000 л. с. Обслуживающий персонал два человека: оператор на станции погрузки, контролирующий работу автотранспорта и загрузку скипов, и оператор на станции разгрузки. Производительность подъемника по руде и пустой породе соответственно 2000 и 1700 т/ч. По мере понижения отметок дна карьера предусмотрено доведение общей длины подъемника до 525 м с перепадом высот в крайних точках 232,5 м.
Станции разгрузки руды и пустой породы выполнены раздельными, причем первая расположена на 37,5 м ниже второй.
Для приема руды предусмотрен 1000-т бункер, из которого она с помощью двух качающихся питателей грузится в 90-т полувагоны; средний темп погрузки 3600 т/ч, что эквивалентно продолжительности загрузки одного вагона 1 мин. Груженные рудой полувагоны подаются затем на станции формирования маршрутов. На станции приема пустой породы установлен 350-т бункер, из которого ведется загрузка думпкаров, транспортирующих породу в отвал под уклон 20%0, емкость кузова полувагона 30,4 м3.
В Англии в железорудном разрезе Scunthorfe для снижения транспортных затрат железнодорожный транспорт заменен автомобильным [47]. транспортирование руды теперь осуществляется в двухосных автосамосвалах Enebid грузоподъемностью 15 и 30 т. В разрезе Roxby используются четыре самосвала грузоподъемностью 15 т, которые еженедельно вывозят до 10 тыс. т руды из разреза к специально сооруженной погрузочной станции, где руда перегружается в железнодорожные вагоны для перевозки на расстояние 6,4 км к рудодробильному заводу. При помощи четырех 30-т самосвалов из разреза Crosby Uhrren вывозится до 15 тыс. т железной руды в неделю, а из разреза Jarborough, где действуют пять таких самосвалов, еженедельно доставляется 40 тыс. т руды. В последнем случае работа организована по двухсменной системе, что позволяет более эффективно использовать оборудование. Для движения автотранспорта сооружены дороги с уплотненным шлаковым покрытием. Отгрузочные станции имеют подпорные шпунтовые стенки, подсыпанные шлаком и покрытые сверху бетоном. такой метод сооружения значительно дешевле, чем из монолитного бетона. Применение автотранспорта для перевозки руды дало возможность сократить численность персонала с 353 до 293 человек.
В Италии на цементном заводе Colleferro в связи с увеличением мощности предприятия и вводом в эксплуатацию нового карьера известняка принято решение о демонтаже имеющейся подвесной канатной дороги и замене ее ленточной конвейерной системой [48]. Канатная дорога имела длину 2400 м и производительность 100 т/ч. Новая конвейерная система фирмы Fredenhagen (ФРГ) имеет производительность 400 т/ч. Система состоит из шести конвейеров, оборудованных лентой шириной 800 мм и имеющих скорость движения 2,09 м/сек. На доставку сырья из карьера на завод затрачивается 30 мин.
При строительстве линии искусственные сооружения (мосты, эстакады) возводились на трассе лишь в местах резкого перепада высот и на пересечениях с автомобильными дорогами. В остальных местах несущие конструкции конвейеров установлены на грунте с использованием под стойки небольших бетонных фундаментов, предотвращающих размыв оснований в периоды интенсивного выпадения осадков. Сверху конвейеры защищены навесом из рифленого материала этернита, а сбоку - экранами из листового материала.
С технико-экономической точки зрения реконструкция обеспечила большую эффективность транспорта завода.
В Швеции на сталеплавильном заводе в Геллефорсе произвели замену внутреннего узкоколейного железнодорожного пути безрельсовыми дорогами и внутризаводского транспорта- автовозами (портальными автопогрузчиками).
В программу регулярных внутризаводских перевозок завода входят семь основных групп грузов: слитки при температуре 900° весом каждый по 2 и 3 т партиями по 16-18 т; два 6-т ковша с расплавленной сталью; 24 погрузочных кюбеля по 1 т; бухты проволоки или рулоны ленты по 250 кг партиями общим весом 22,5 т; 24 стандартных контейнера по 1 т; балки и заготовки большой длины; короткие заготовки длиной до 2 м [49].
Замена железнодорожного транспорта автовозами была закончена в августе 1962 г. Были приобретены три автовоза грузоподъемностью по 22,5 т, из которых два включены в постоянную трехсменную работу, один резервный. Размер портала автовоза: ширина 1,8 м, высота 2,15 м.
В результате реорганизации высвобождено три локомотива, 150 вагонов и разобрано 11 км железнодорожных путей. Эксплуатационные расходы железнодорожного транспорта в 1951 - 1958 гг. составляли 9,7 кроны на 1 т стали в слитках. После ликвидации железнодорожных путей эксплуатационные расходы сократились до 3,5 кроны на 1 т стальных слитков. Кроме того, после разборки железнодорожных путей высвобождено 50 000 м2 площади.
В ФРГ на машиностроительном заводе «Олимпия» для транспортирования материалов был введен вместо ручных тележек парк машин, включающий тягачи с усилием на крюке 3000 кг, вилочные погрузчики грузоподъемностью 1200 и 1500 кг и прицепные тележки [50]. В результате по сравнению с прежним способом работы число рабочих, занятых на транспортировании материалов, сократилось в четыре раза. Экономия на заработной плате составила 274 тыс. зап.-герм. марок в год и средства, затраченные на приобретение транспортного оборудования, окупаются за 1,1 года.
В ГДР на один из химических заводов с рудника, находящегося на расстоянии 3,5 км, ежедневно поступает 2200 т калийных солей [51].
При выборе средств улучшения работы транспорта были исследованы два варианта: а) постройка заглубленного приемного бункера с применением для перевозки солей думпкаров; б) введение гидромеханического транспорта.
Поскольку соль гироскопична, то в сырую погоду в заглубленном бункере неизбежно ее прилипание к стенкам. Для устранения этого требуются отопительные и другие устройства. Для погрузки и выгрузки думпкаров необходимы затраты рабочей силы; кроме того, требуются расходы на содержание пути. Большой недостаток данного варианта - прерывность транспортирования в вагонах. В связи с этим был принят вариант гидромеханического транспортирования.
технологический процесс гидромеханического транспорта следующий: калийная соль выходит из дробильной мельницы с максимальной величиной зерен 14 мми подается ленточным конвейером длиной 10 м в смеситель; здесь ее смешивают с щелочным раствором и во взвешенном состоянии при концентрации пульпы 1 : 1,7 подводят к двум последовательно расположенным центробежным насосам. Продукт по трубопроводу длиной 3,3 км поступает непосредственно на завод для просеивания и вторичного измельчения, после чего соль направляется на технологические операции.
При гидравлическом транспортировании производительность по сравнению с железнодорожным транспортом возрастает на 156%. Себестоимость транспорта при перевозке соли в вагонах составляет 4,9 марки на 1 т продукта. При внедрении думпкаров себестоимость уменьшается до 3,4 марки, а при гидромеханическом способе она составляет только 2,5 марки.
В ПНР, ЧССР и ГДР, имеющих крупные открытые разработки бурого угля, ведется большая работа по реконструкции транспорта и внедрению непрерывных видов транспорта, в первую очередь конвейерного. Опыт ГДР показывает, что при конвейерном транспорте на открытых горных разработках угля себестоимость транспортирования и производительность рабочих значительно выше, чем при железнодорожном транспорте [52]. В разрезе Welzow Sud, который в 1962-1963 гг. был оборудован конвейерной системой с лентами шириной 1600 м и скоростью движения ленты 5,24 м/сек, выработка на одного рабочего в два раза выше, чем в других разрезах с использованием железнодорожного транспорта.
В этих странах замена железнодорожного транспорта на открытых разработках конвейерным вызывается не только снижением транспортных издержек. В ЧССР в разрезах Северо-Чешского угольного бассейна выявляется все более очевидный разрыв между непрерывным рабочим процессом применяемых в карьерах мощных экскаваторов и отвалооб-разователей и циклическим прерывистым процессом работы железнодорожного состава [23]. Чем выше производительность отвалообразователя, тем длиннее должны быть составы поезда и короче интервалы между поездами. В условиях Северо-Чешского бассейна даже при полном использовании путей можно достигнуть максимальной производительности 1600 м3/ч, что при современном технологическом оборудовании недостаточно. В связи с этим намечается реконструкция транспорта в бассейне и внедрение конвейерных систем производительностью до 4000 м3/ч.
В СССР внедрение новых видов промышленного транспорта (конвейерного, безрельсового колесного, гидротранспорта, пневмотранспорта, подвесных канатных дорог и т. д.) идет главным образом на вновь строящихся предприятиях, а также на предприятиях, где основное производство подвергается серьезной реконструкции и расширению.
При этом замена вида транспорта на действующих предприятиях, так же как и новое строительство, производится на основе подробных технико-экономических расчетов с учетом сроков окупаемости капитальных затрат.
В качестве примера можно привести Магнитогорский металлургический комбинат [45]. В связи с расширением комбината и внедрением на нем комплексной механизации и автоматизации производства была рассмотрена целесообразность замены железнодорожного транспорта для перевозки некоторых грузов.
На основе произведенных расчетов признано целесообразным заменить железнодорожный транспорт другими видами транспорта для перевозки огнеупоров, скрапов, металлолома, колошниковой пыли, ферросплавов и т. п. 60-т тягачами с прицепами и полуприцепами; коксовой мелочи из доменного цеха на аглофабрику и дробленой руды в сталеплавильные цехи - конвейерным транспортом; уборку шлаков от доменных цехов на шлакоперерабатывающие предприятия, промпродукта с углемойки на тЭЦ, шлаков от копровых цехов сталеплавильных цехов на отвал - трубопроводным транспортом.
Замена железнодорожного транспорта на этих перевозках другими видами транспорта позволит сократить число рабочих, занятых на этих работах, примерно на 900 человек, уменьшить эксплуатационные расходы на 1,3 млн. руб в год, сократить существующую сеть железнодорожных путей на 64,5 км.
В результате осуществления этих мероприятий удельный вес перевозок по видам транспорта на комбинате изменится следующим образом (табл. 6).
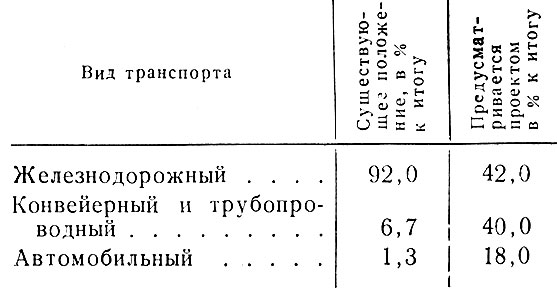 таблица 6
На Глуховецком комбинате была произведена замена экскаваторной разработки глины с перевозкой ее железнодорожным транспортом на гидравлический способ разработки с транспортированием глины по гидропроводу. Это позволило сократить количество обслуживающего персонала в три раза и получить годовую экономию 200 тыс. руб.
Замена автомобильного транспорта конвейерным на Ахан-Гаранском цементном заводе обеспечила увеличение производительности труда в 3,5 раза и снижение себестоимости перевозки более чем на 30%. Применение канатно-подвесных дорог на некоторых цементных заводах в стране (Ново-Здосбуновском, Каспи и др.) также обеспечивает снижение себестоимости транспортирования сырья по сравнению с автомобильным транспортом в 5-9 раз и т. д.
Приведенные примеры высокой эффективности работ по реконструкции транспортного хозяйства на промышленных предприятиях с применением в результате реконструкции наиболее экономичных видов промышленного транспорта свидетельствуют о необходимости изучения опыта зарубежных стран с целью более широкого развертывания таких работ в нашей стране.
Одной из основных причин незначительного удельного веса непрерывных видов транспорта в общем объеме перевозок на промышленном транспорте в нашей стране (1965 г.- 12%) является недостаточный выпуск нашей промышленностью подъемно-транспортного машиностроения средств непрерывного транспорта. Потребность промышленности в оборудовании для непрерывных видов транспорта удовлетворяется всего на 50-60%. В результате большая часть его идет на вновь строящиеся предприятия и только незначительная часть - на реконструкцию транспорта действующих предприятий. В зарубежных странах производство транспортного оборудования занимает в машиностроительной промышленности большой удельный вес: в ФРГ 30%, Англии 37%, ПНР 32% и т. д. Удельный вес производства конвейеров в общем объеме продукции подъемно-транспортного машиностроения составляет в США 26-27%, в Англии и ФРГ - 21-25%.
Следовательно, важнейшей задачей в области внедрения экономичных и, в первую очередь, непрерывных видов транспорта в нашей стране является расширение производства на заводах подъемно-транспортного машиностроения производительного и надежного оборудования для этих видов транспорта.
|