4. Автоматизация работы ковейеров
Одним из важнейших преимуществ конвейерного транспорта на внутризаводских и внешних перевозках является возможность полной автоматизации управления отдельными конвейерными линиями и конвейерными системами в целом.
За последние годы особенно широко применяется автоматизация работы подвесных толкающих и напольных тележечных конвейеров с автоматическим адресованием грузов; конвейерных систем, обслуживающих доменное и сталелитейное производство; конвейеров обогатительных фабрик, заводов строительных материалов и др.
При этом создаются как полностью автоматизированные конвейерные системы, так и конвейерные линии с автоматизацией части операций: пуска и остановки конвейеров, регулирования загрузки и скорости движения лент и т. д.
При автоматизации процессов работы конвейерного транспорта применяются различные новейшие системы дистанционного и программного управления транспортными установками: программное управление на основе запоминающих устройств играет особенно важную роль в крупном производстве с технологически взаимо-связанными машинами и движением огромного количества перемещаемых изделий, для которых необходимо автоматически определять путь их движения.
Особенно большую эффективность имеет автоматизация транспортных процессов при создании современных заводо-автоматов (машиностроительных, обогатительных фабрик, заводов строительных материалов, лесообрабатывающих предприятий и т. д.). Автоматизация работы конвейерных систем занимает одно из важных мест в создании таких заводов-автоматов и оказывает большое влияние на совершенствование основного производства.
Рассмотрим системы автоматизации конвейерного транспорта, применяемые в зарубежных странах в различных отраслях промышленности и для разных типов конвейеров.
На предприятиях строительных материалов, обогатительных фабриках, карьерах и рудниках, где для перевозки сыпучих грузов применяются ленточные конвейеры, вводится полная автоматизация работы конвейерных систем. Это иллюстрируется следующими примерами.
В США завод по выпуску гравия, щебня и заполнителей для бетона фирмы Graoel & Sand Co. производительностью 300 т/ч имеет технологическую линию из пяти станций, связанных между собой конвейерами со скоростью транспортирования 87 м/мин. технологическая линия обслуживается всего тремя рабочими.
В Канаде гравийно-щебеночный завод фирмы Acton Limistone Quarries, Ltd производственной мощностью 1000 т/ч оборудован автоматизированной конвейерной системой общей длиной 1300 м и состоящей из 21 конвейера. Управление всеми процессами, включая погрузку, ведется с центрального пульта. Максимальный темп погрузки материалов на внешний транспорт составляет 1000 т/ч . На пуск всей системы, включая технологическое оборудование, затрачивается 13 мин, на остановку 14 мин. При аварии на линии привод всех питателей, конвейеров и грохотов до аварийной точки автоматически отключается. Погрузка материала ведется в самосвалы или 100 т вагоны без остановки последних и без расцепки состава.
В Англии агломерационная фабрика фирмы Richard Thomas and Balduin, производственной мощностью 200-240 т/ч оборудована автоматизированным конвейерным комплексом дозирования и подачи сырья на технологическую линию [155]. На складе имеется 15 установленных в линию бункеров, из которых 8 предназначены для руды, поступающей из трех месторождений, 2 для кокса и 2 для отходов основного (доменного) производства и колошниковой пыли; остальные 3 бункера рециркуляционные. Каждый бункер снабжен ротационным питателем, который в сочетании с ленточным перегружателем обеспечивает дозирование сортов руды, кокса и других компонентов по заранее заданной программе. Суммарная производительность питателей составляет 650 т/ч . Дозы выдаются на магистральный конвейер, который промежуточным конвейером связан с первичной перемешивающей машиной. Распределительный желоб на входе в эту машину позволяет при необходимости переключать подачу в обход нее, направляя сырье через систему из трех конвейеров в промежуточный сдвоенный выравнивающий бункер питания вторичных перемешивающих машин (по одной на каждую технологическую линию). Здесь же размещен резервный сдвоенный бункер для кокса, используемый для усреднения состава шихты. Бункера снабжены дозаторами и уровнемерами, которые управляют процессом заполнения.
Для осуществления автоматического управления системами ленточных конвейеров необходимы непрерывное получение и переработка информации о загрузке конвейеров (скорости и веса материала). Для непрерывного определения скорости используются тахогенераторы или устройства, измеряющие действительную скорость движения ленты. Определение веса груза ведется по величине деформации гибкой подвески опорных роликов. На основе сигналов о загрузке конвейера осуществляется автоматическое регулирование его работы. Для этого применяются автоматические питатели и дозаторы, приборы, обеспечивающие стабильную загрузку и производительность конвейеров, а также автоматический пуск и остановку конвейеров, автоматические сбрасывающие груз тележки и т. д.
В США применяется несколько типов автоматических питателей для конвейерных систем f 156].
Ленточный питатель с электронным управлением фирмы Wellman Engineering. Co. действует по принципу замкнутой цепи с обратной связью. Датчиком является чувствительная месдоза (), поддерживающая часть конвейера, лента которого движется с определенной скоростью. Месдоза направляет сигналы в узел управления питателем, где они сравниваются с контрольным сигналом. В случае несовпадения сигналов обеспечивается соответствующее изменение степени открытия загрузного отверстия, через которое материал подается на ленту конвейера.
Весовой питатель-дозатор Feedoweight фирмы Merrick. Scale Mfg имеет в качестве чувствительного элемента роли-коопору верхней рабочей ветви конвейерной ленты. Контроль за режимом работы питателя осуществляется приводным регулятором подачи без помощи рычажного весового механизма. Неподвижная гиря поддерживает равновесие весового коромысла, когда вес груза на ленте питателя равен весу гири. Всякое отклонение немедленно регистрируется чувствительной роликоопорой, при этом нарушается равновесие коромысла. Приводной регулятор подачи, соединенный с концом коромысла, сразу же перемещает заслонку вверх или вниз. таким образом поддерживается постоянный вес груза, приходящегося на единицу длины конвейера. Магнитный суммирующий счетчик дает отсчеты в единицах веса транспортируемого материала.
Фирма West Midlands Division эксплуатирует опытные устройства для остановки автоматической конвейерной линии: при скоплении груза на передаточном пункте [157]. Устройство размещается непосредственно под лентой конвейера и представляет собой подвижную систему, состоящую из наклонной полосы, шарнира опоры, находящейся в зацеплении с переводным колесом, и переключателя. Если передаточный пункт переполнен, наклонная полоса под действием веса груза опускается, переворачиваясь вокруг шкварня. В результате переводное колесо действует на выключатель цепи управления и конвейеры останавливаются. При освобождении передаточного пункта наклонная полоса поднимается и конвейерная система автоматически включается.
В США применяются автоматизированные самоходные сбрасывающие тележки для разгрузки и распределения сыпучих и кусковых материалов с ленточных конвейеров в бункера или в открытые штабеля [158]. Фирма Kennecotl Copper Co., занимающаяся добычей и переработкой медной руды, на обогатительной фабрике в шт. Невада использует автоматизированную тележку, обслуживающую конвейер с лентой шириной 1067 мм. тележка совершает непрерывные челночные движения в обоих направлениях вдоль трассы конвейера, обеспечивая перегрузку руды в восемь бункеров общей емкостью около 14,4 тыс. т. В донной части каждого бункера предусмотрены по два разгрузочных отверстия, под которыми смонтированы валковые питатели. При непрерывном движении сбрасывающей тележки различные виды руды распределяются по всем бункерам, позволяя получить необходимую смесь.
Контроль за работой тележки осуществляется с пульта управления. Бункера оборудованы указателями уровня загрузки.
На обогатительной фабрике в шт. Юта сооружена бункерная установка с двумя автоматизированными сбрасывающими тележками, осуществляющими перегрузку измельченной руды с двух конвейеров с лентами шириной 864 мм в один общий бункер длиной 173,7 м, шириной 6,25 м и высотой 7,0 м. Каждая из тележек обслуживает половину этого бункера. Надбункерные конвейеры получают материал с двух питающих конвейеров с лентами шириной 914 мм, примыкающих к центральной части бункера. тележки разгружают материал через два направляющих желоба.
Внутри бункер разделен перегородками на 97 отсеков. Руда должна загружаться по центру отсеков. Под бункером размещено 13 пар пластинчатых питателей с лентой шириной 1525 мм, которые выдают руду из бункера для последующей технологической обработки.
Система управления движением сбрасывающих тележек обеспечивает последовательную загрузку всех отсеков бункера. Управление тележками независимое, любая из них может работать при выключенной другой тележке.
Во Франции фирмой СУВЕRМЕСА Со. создан промышленный образец электромеханического прибора для непрерывного контроля скорости ленточного конвейера в зависимости от меняющейся нагрузки на ленту, что позволяет получить стабильную производительность независимо от колебаний в работе загрузочных устройств [159]. Основной частью прибора является дифференциал, к обмоткам которого подключен тахогенератор. Сердечник дифференциала связан с упругоподвешенными роликами, вертикальное перемещение которых зависит от изменений нагрузки на ленту. Происходящее в результате этого смещение сердечника вызывает изменение магнитного поля в обмотках дифференциала, вследствие чего в его цепи возникает сигнал, сила которого зависит от отклонения фактической производительности от заданной. На основе этого получают корректирующий сигнал, подаваемый в цепь управления двигателем.
В последнее время в США, Франции, Бельгии и др. ленточные конвейеры стали применяться как средство автоматизации подачи шихты в доменные и мартеновские печи.
Во Франции автоматическая загрузка доменных печей ленточными конвейерами осуществлена на заводе Louvreil компании Usinor при реконструкции завода со строительством новых доменных печей большого объема [160]. Схема автоматической загрузочной установки с конической дозировочной башней и автоматическими ленточными конвейерами показана на рис. 12.
Применение конической дозировочной башни, распределяющей и взвешивающей сырьевые компоненты в одном пункте, свело к минимуму количество конвейеров.
Кокс подается в бункера конвейером т. Руда прибывает в поездах и по двум путям подается к бункерным ячейкам. Из бункеров вибропитатели подают кокс и руду на главный конвейер В1 передающий материал в дозировочную башню.
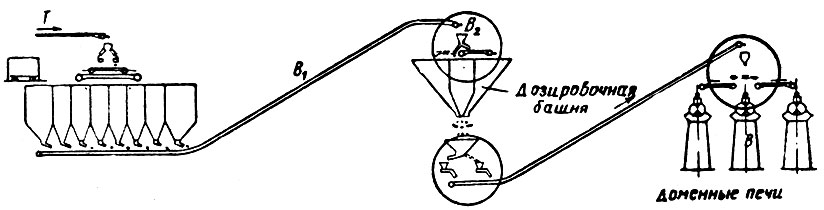 Рис. 12. Схема автоматической загрузочной установки доменных печей металлургического завода
В башне автоматическая установка останавливает вращающийся конвейер В2 над порожним силосом. Конвейер поворачивается в течение 2 мин. В этой установке использованы гамма-лучи, определяющие уровень загрузки силосов.
У колошника средней печи установлен реверсивный конвейер, направляющий материал к первой или третьей печи по передвижному конвейеру или непосредственно к средней печи В.
От колошника материал идет на малый и большой конус каждой печи. Управление подачей сырья сосредоточено в дозировочной башне. В помещении командного пункта перед диспетчером имеются табло с индикаторами загруженности материалами печей, четыре телевизионных экрана, визуально показывающие работу основных узлов, планшеты, где фиксируется вес загруженного в печи материала. Здесь же находится аппаратура для программирования автоматического действия загрузки печей.
Предусмотрены указатели уровня загрузки сырья в доменных печах, дающие указания системе по объему загрузки той или иной печи. Эти сведения автоматически передаются и записываются на магнитную ленту установки по загрузке, откуда подается команда на дозировочную башню по отгрузке определенных весовых порций сырья. Отгрузка и взвешивание осуществляются автоматически с применением специальных электронных приборов и фотоэлектрических аппаратов. Возможное отклонение веса от заданного значения 20 кг на отвес порции в 20 т. Пишущая электрическая машинка отмечает время выдачи порции сырья, последовательный номер отгруженного материала и его наименование, условный позывной номер зонда доменной печи, гранулометрический состав сырья и его вес.
Загрузка сырья в дозировочную башню ведется автоматически посредством конвейера Вь Башня имеет девять силосов на ее периферии для руды классифицированной и три силоса центральных для двух гранулометрических классов просеянного кокса.
В установке имеются органы программирования, в которые вводятся необходимая информация, общая задача и последовательность работ, что записывается на магнитную ленту; последняя после записи вводится в аппаратуру исполнения.
Специальная аппаратура контролирует правильность кодирования, электрической памяти, световых сигналов и пр.
Движение конвейерной ленты связано со скоростью магнитной ленты управляющей установки.
Основным органом этой установки являются элементы логического течения процесса. Логические элементы получают информацию от всех установок и частей механизмов и в свою очередь выдают на ее основе приказы, поддерживая заданную последовательность операций о начале или приостановке загрузки, выключении или приведении в движение конвейеров и т. д.
В США на заводе фирмы И. S. Steel Corp. в Дукейне осуществлено автоматическое регулирование поступления шихтовых материалов в доменную печь. Автоматически регулируются взвешивание, сортировка и грохочение сырья [161]. Электронные регулирующие приборы обеспечивают подачу ленточными конвейерами требуемого количества материалов в заданной последовательности от бункеров их хранения к весовым воронкам. Вес материала, поступающего в воронку, дважды контролируется электронными весами. Для постоянного контроля за работой механизмов в систему автоматического регулирования введены регистрирующие устройства, записывающие на ленте точный вес каждой партии загружаемых в весовую воронку материалов. Если весы показывают неполноту взвешивания, то система запоминает ошибку, которую компенсирует на следующей ступени загрузки. Система автоматического регулирования загрузки фирмы General Electric включает пять функциональных секций. Первая состоит из секции программирования, включающей программное управляющее устройство (задание, в которое вводится с помощью перфокарты), и селектора вспомогательной программы. Секция определяет программную информацию о типе и последовательности загрузки. Данные из этой секции поступают в запоминающее устройство (вторая секция) в соответствии с требованием управляющего устройства системы загрузки (третья секция). Четвертая (основная) секция координирует поток сигналов для выполнения операций нужного количества по подготовке для завалки в доменную печь. Пятая секция управляет механизмами привода скипового подъемника, приводов механизмов на рудном дворе и т. д.
Наряду с автоматизацией работы ленточных конвейеров при транспортировании сыпучих грузов в ряде стран разработаны и применяются системы автоматического адресования транспортируемых ленточным конвейером штучных грузов.
В США эта система осуществлена путем применения конвейерной ленты с магнитным слоем [162, 163].
Для этого между слоями конвейерной ленты закладывается магнитный материал, который позволяет записывать любую информацию. Это обеспечивает создание автоматической распределительной конвейерной системы, когда оператор на сортировочной станции при нажатии соответствующей кнопки включает нанесение соответствующей команды на магнитный слой конвейерной ленты под очередным грузом.
При прохождении груза мимо отклоняющего приспособления, считывающая головка которого настроена на соответствующий сигнал, груз переводится на боковой конвейер. Специальные дублирующие станции позволяют переносить сигнал при переходе груза на другую ленту. Система является очень гибкой, может использовать до 1000 разных команд, не требует установки на грузе различных командных устройств. Ее стоимость и эксплуатационные расходы не выше, чем у других аналогичных систем.
В машиностроении, химии и других отраслях промышленности широко применяются подвесные толкающие конвейеры. В ряде стран (СССР, США, ФРГ, Франция) осуществлена разработка подвесных толкающих конвейеров с автоматическим адресованием грузов.
Для автоматизации подвесных конвейеров в США применяются различные системы автоматического адресования грузов [164].
При автоматическом управлении перемещаемые изделия должны получать информацию, определяющую путь их движения. В качестве носителя информации обычно применяются откидные кулачковые выключатели или контактные пластинки, устанавливаемые непосредственно на грузозахватных подвесках конвейеров. Более надежны в тяжелых условиях работы бесконтактные магнитные системы маркировки, допускающие большие зазоры (до 15 мм) между носителем информации и генератором, сигнал которого зависит только от степени намагничивания. При этом скорость движения транспортного устройства не влияет на передачу сигналов. В качестве носителя информации применяются намагничиваемые металлические пластины, расположенные на грузовых подвесках. При движении подвесок мимо станции записи пластины воспринимают ту или иную информацию на нескольких магнитных дорожках. При большом объеме информации отдельные признаки подвески зашифровываются, чтобы общее число магнитных дорожек было минимальным.
В некоторых случаях, когда изделия должны получить адреса в промежуточных пунктах транспортной цепи, на грузовых подвесках устанавливаются магнитные многопозиционные переключатели, настраиваемые на определенный адрес вручную.
Для подачи команд управления применяется магнитное запоминающее устройство, в котором носителем информации служат намагничиваемые металлические ленты, укрепленные по окружности специального барабана. Число лент зависит от количества адресов. Над магнитными лентами помещаются записывающие, опросные и стирающие головки. Для точной установки этих головок по отношению к магнитным лентам применяются специальные салазки, гарантирующие зазор 0,1 мм.
На одном часовом заводе транспортирование полуфабрикатов в ящиках производится при помощи замкнутых конвейерных систем. На каждой подвеске конвейера имеется датчик с двумя рядами чисел. Рабочий, производящий загрузку подвесок, одновременно устанавливает на датчике номер пункта разгрузки. При подходе груженой подвески к этому пункту датчик дает соответствующие электрические импульсы, после чего производится автоматическая разгрузка.
Во Франции система автоматического адресования грузов по пунктам их назначения основана на применении дисков и фотоэлектрических реле, позволяющих предусмотреть 999 различных адресов. Устройство съемное и может сниматься вместе с грузом или оставаться на конвейере. Посредством фотоэлектрических реле читается ход адреса и приводятся в действие необходимые механические устройства {165].
На конвейерах типа Carrous для транспортирования ящиков кодирование адресов производится с помощью клавиатуры из двух групп по 8 клавишей. Достаточно набрать на клавиатуре две цифры, соответствующие коду станции выгрузки, чтобы контейнер с грузом был автоматически выгружен в требуемом месте.
В ФРГ фирмы Stohr и Siemens производят конвейеры с автоматическим адресованием транспортируемых грузов и приборы управления к ним [166]. При адресовании грузов, осуществляются автоматическая загрузка конвейерной линии, снятие грузов с нее, доставка грузов на определенные участки и другие подобные операции. Различают конвейеры с электромеханическим и с магнитным управлением.
В подвесном конвейере с электромеханическим адресованием на каждой подвеске имеется штанга, устанавливаемая на один из обозначенных на ней номеров от 1 до 10 в соответствии с нумерацией упаковочного стола.
Подвески конвейера выполнены таким образом, что при установке штанги, например на № 1, подъемный стол упаковочного участка № 1 автоматически приподнимается, после чего подвеска разгружается.
После установки подвесного конвейера с автоматическим адресованием потребность в обслуживающем персонале на складе уменьшилась на 30%.
Другой способ автоматического адресования грузов осуществляется с использованием небольших магнитных пластинок, управляемых посредством электронной системы. Путем импульсного намагничивания пластинкам сообщают двойной код. Каждому рабочему месту (пункту назначения) соответствует определенная полоса на магнитной ленте, а каждой полосе - специальная головка для записи и для. считывания кода.
При движении все контейнеры удерживаются на подвесках специальными державками, которые в месте адресования груза автоматически раскрываются. Счетчик беспрерывно регистрирует количество находящихся на конвейере контейнеров. На световом табло отражается степень обеспечения всех рабочих мест обрабатываемыми деталями. Установку можно реверсировать с двумя скоростями в обоих направлениях.
Применяется автоматическое адресование грузов также для напольных тележечных конвейеров.
В США на центральном распределительном товарном складе фирмы General Electrie Co. действует развитая система автоматизированных напольных тележечных конвейеров с дистанционым диспетчерским управлением [167]. При помощи непрерывно движущихся встроенных в пол тяговых цепей осуществляется передвижение отдельных четырехколесных грузовых тележек, которые при необходимости легко отделяются от тяговых линий.
На тележках установлены электронные селекторные устройства, посредством которых программируется маршрут следования до соответствующего участка хранилища или отгрузочной платформы.
транспортной системой управляет один оператор с дистанционного пульта. Кроме основного магистрального конвейера, в систему входят 69 ответвлений и две вспомогательные замкнутые линии.
Протяженность замкнутого магистрального конвейера 549 м. трасса его проходит по внутреннему периметру склада. Скорость движения тяговой линии 0,46 м/сек. Две вспомогательные тяговые линии служат для временного отвода порожних и загрузочных тележек в случае занятости магистрального конвейера.
Отвод тележек с магистрального конвейера на соответствующие ответвления осуществляется посредством переводных механизмов, управляемых электронными установками с запоминающим устройством.
В ФРГ в текстильной промышленности широкое распространение получили тележечные конвейеры с автоматическим адресованием [168]. тяговым органом этих конвейеров является цепь. Она монтируется в специальной траншее в полу склада, что позволяет сократить строительную высоту зданий и исключить загрязнения в цехах. Последнее особенно важно для текстильных предприятий.
тележки конвейеров оборудуются автоматическими адресующими устройствами, принцип работы которых заключается в изменении величины магнитного поля стрелочных переводов или пунктов погрузки-разгрузки при наезде на них тележек. Пункт назначения устанавливается производственным рабочим после окончания погрузочно-разгрузочных операций. Контроль за работой конвейера осуществляется с центрального пульта управления.
В СССР автоматизация конвейерного транспорта идет по линии создания автоматических систем ленточных конвейеров на предприятиях строительных материалов, в карьерах, на обогатительных фабриках и др. и внедрения подвесных толкающих конвейеров с автоматическим адресованием грузов на предприятиях машиностроения, химической промышленности и т. д.
ВНИИПтМАШем совместно с предприятиями созданы конструкции отечественных подвесных толкающих конвейеров с автоматическим адресованием грузов. Испытания показали, что эти устройства по техническим данным находятся на уровне лучших зарубежных образцов, а в отдельных случаях превосходят их. В настоящее время изготовлена первая серия этих устройств в количестве 26 тыс. м грузонесущих конвейеров [169].
Сконструированы автоматические ленточные конвейерные линии для дробильно-обогатительного предприятия, для лесообрабатывающих заводов и др.
Однако необходимо отметить, что внедрение автоматизации конвейерного транспорта идет еще медленно. В связи с тем, что в ближайшее время предстоит выполнить большой объем работ по автоматизации конвейерного транспорта, опыт зарубежных стран в этой области заслуживает тщательного изучения.
|