|
3. Пневматический транспорт
УДК 621.867.8
Пневмотранспорт с успехом используется для транспортирования порошкообразных и сыпучих грузов с крупностью фракций до 50 мм при дальности перемещения до 2000 м. Имеются три категории пневмотранспортных установок, работающих при различной плотности потока. К первой относятся установки, рассчитанные на обслуживание нескольких точек ввода или вывода груза. Они работают от насосов дающих напор до 3 тыс. мм вод. ст.; плотность потока у них составляет 3 кг/кг воздуха. По принципу действия они могут быть напорными, вакуумными, или комбинированными. Ко второй категории относятся установки, у которых плотность потока 8 кг/кг воздуха, а развиваемый насосом рабочий напор -8 тыс. мм вод. ст. При транспортировании порошкообразных грузов на расстояние 35 - 235 м производительность этих установок колеблется в пределах от 5 до 12 т/ч при давлении в трубопроводе 0,4 - 0,9 ати. Установки третьей категории характеризуются плотностью потока до 1 00 кг/кг воздуха [106].
На ряде заводов электролизного алюминия французского электрометаллургического и электрохимического общества внедрены высокопроизводительные установки пневматического транспорта для разгрузки прибывающих железнодорожных цистерн с порошкообразным глиноземом, транспортирования глинозема в силосные башни, питания расходных бункеров в электролизных цехах и для подачи глинозема в электролизные ванны. Все процессы работы пневмотранспорта полностью автоматизированы, контролируются и управляются с центрального пульта.
Схема установки пневмотранспорта глинозема изображена на рис. 15, где 1 - пост разгрузки цистерны; 2 -компрессорная станция; 3 - силосные башни; 4 - шлюзовая пневмокамера; 5 - устройство для повышения давления; 6 - смесители; 7 - продукте проводы; 8 - воздухопроводы; 9 - расходные бункера; 1 0 - аэрожелоб; 11 - место загрузки кранов; 1 2 - цех электролиза.
Разгрузка цистерн емкостью 30 м3 (30 т груза) осуществляется на отдельной ветке. Прибывший состав весом 1200 т разгружается за 10 ч. Сжатый воздух давлением 2 кГ/см подается в цистерну, происходит псевдоожижение глинозема, обеспечивающее хорошую текучесть при повышенных скоростях. Компрессорная установка для этой цели состоит из компрессоров, охладителя, конденсатора, маслоуловителя и подогревателя. Мощность электродвигателей 120 квт. Разгрузка силосных башен производится при помощи сети аэрожелобов, через которые глинозем подается в шлюзовые распределительные пневмокамеры емкостью 5 м3, специально приспособленные для работы с абразивными материалами и работающие от сжатого воздуха давлением 2 кГ/см2, получаемого от группы компрессоров мощностью 100 квт. Псевдоожиженный материал подается по продуктопроводам в расходные бункера порциями по 4 т при средней подаче 25 т/ч. Расходные бункера емкостью до 1 2 т располагаются обычно на крыше. Их заполнение регулируется изотопными сигнализаторами уровня, с коммутированными с отсечной арматурой пневмокамер [107].
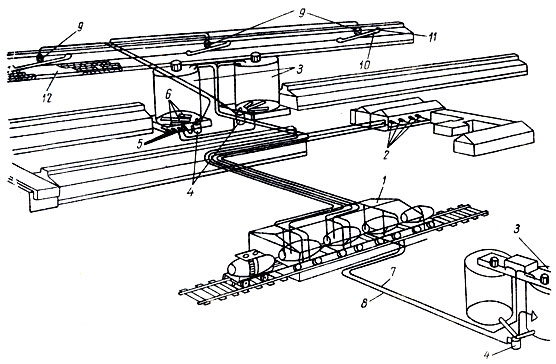 Рис 15. Установка пневмотранспорта глинозема
Пневмотранспортные установки находят широкое применение на внутризаводском транспорте в перерабатывающих отраслях промышленности Швейцарии. В частности, они используются в химической промышленности при производстве красителей и полупродуктов при транспортировании гранулированного льда различной геометрической формы и размеров. По сравнению с конвейерами они обладают рядом серьезных преимуществ. Ho как правило, характеризуются относительно большим удельным расходом мощностей (1-4 л.с. /т).
При проектировании установок среднюю крупность фракций льда, исходя из накопленного опыта, принимают равной 20 - 30 мм, для других сыпучих грузов диаметр в свету трубопровода рекомендуется принимать 5 - 10-кратным от средней крупности фракций. Вторым исходным параметром при проектировании является средняя скорость взвешивания частиц в воздушном потоке. Для льда ее берут равной 10 м/сек. На этой основе определяют скорость воздушного потока, которая должна быть не меньше чем удвоенная скорость взвешивания. Третьим исходным параметром служит "консистенция" смеси "воздух - продукт" т.е. отношение расхода по весу в трубопроводе за единицу времени по твердому и по газу. Для рассматриваемого груза его принимают равным 10 - 15. С увеличением дальности транспортирования абсолютное значение этой величины уменьшается.
Поскольку зависимость между расходом мощности и производительностью носит почти линейный характер, целесообразно проектировать установки с большими верти - кальными и малыми горизонтальными участками. При расчете воздухопроизводительности на холостых режимах и, соответственно, потребных мощностей радиусы закруглений трубопровода следует принимать не менее 1,0 -1,5 м, а при расчете потерь напора в них по известным формулам длину трубопровода - удваивать против фактической и во всяком случае принимать не менее 1,5-кратной [108] ,
На одном из предприятий химической промышленности Испании внедрена пневмотранспортная установка с автоматизированным циклом. Она используется для подачи смеси порошкообразных компонентов, из которой изготовляется поливинилхлоридная пленка. В проектном задании, выданном фирме System-Technik, предусматривалось: груз с температурой до +100 С, дальность транспортирования до 35 м, превышение отметки в конечной точке пути 4 м, минимальная производительность 600 кг/ч, управление установкой с рабочего места оператора.
У смесителя установлен шлюзовой аппарат в виде усеченного конуса с диаметром патрубка (на нижнем конце) 250 мм, перекрываемого автоматическим затвором. Корпус аппарата выполнен из ванадиевой стали и изнутри полирован для предупреждения налипания частиц транспорт тируемого материала. Пневмопривод изготовлен из стальных труб диаметром в свету 36 мм, с полированными внутренними стенками. Соединение фланцев труб произведено специальным клеем для предотвращения деформаций, обычно наблюдающихся при соединении фланцев методом сварки. Установка работает при минимальном давлении 6 кГ/см2. Предусмотрены средства автоматического отключения при падении давления [109].
Для эффективного использования пневмосистем в целях транспортирования гигроскопичных сыпучих материалов, а также трудных для пневмотранспорта материалов (уголь, гравий, зерно, рыхлый тальк и др.) создано специальное устройство. Нагнетающие и дозирующие устройства, обычно применяемые в пневмотранспортных системах, оборудуются бункерными вибраторами и другими приспособлениями, которые, однако, недостаточно эффективно предотвращают зависание, налипание или слеживание материала. Предлагаемое устройство, изготовленное в виде полукруглого сверху цилиндрического сосуда, не имеет практически никаких движущихся рабочих органов, кроме регулирующих клапанов и задвижек с соленоидным или ручным управлением. В процессе работы сосуд поочередно автоматически подсоединяется к вакуум - насосу и компрессору для принудительного забора и последующего нагнетания сухого сыпучего материала. Криволинейные внутренние поверхности корпуса сосуда выполнены гиперболическими асимметричными, что обеспечивает беспрепятственное скольжение транспортируемого материала без опасности его накопления в какой-либо точке поверхности.
Пневмонагнетатель работает циклично. После сброса внутреннего давления до уровня атмосферного начинается период заполнения материалом рабочей камеры сосуда при закрытом разгрузочном отверстии. В этот период работает вакуум-насос. При подаче в камеру необходимого количества материала механические сигнализаторы уровня через систему злектроуправления обеспечивают действие соответствующих клапанов, в результате чего в сосуд начинает поступать сжатый воздух от компрессора. Когда давление в камере сосуда достигнет нужного уровня, разгрузочное отверстие открывается, и материал под воздействием сжатого воздуха выдается в пневмотранспортную магистраль Затем изложенный цикл повторяется. Благодаря чередованию интенсивного всасывания с нагнетанием устройство можно использовать для высокопроизводительной перегрузки минеральных удобрений из сосудов, барж, ж.-д. вагонов и складских хранилищ [110].
Для пневматического транспортирования горячих раздробленных материалов с температурой выше 150 С в ПНР создан камерный питатель, выполненный в виде бака с пневматической разгрузкой. В питателе используэтся эффект "псевдоожижения" гранулированного материала под воздействием струй воздуха. В нижней части бака оборудовано устройство для "ожижения" горячего сыпучего гранулированного материала и предусмотрено выходное отверстие с фланцем для подачи материала в систему пневматического транспортирования. Устройство для "ожижения" материала снабжено входным патрубком для подачи сжатого воздуха в распределительную камеру. Входной патрубок имеет боковой отвод для подачи части сжатого воздуха в камеру выходного отверстия питателя. В верхней части бака находится патрубок с фланцем и крышкой для засыпки горячего материала в питатель. Внутри в нижней части бака расположена разделенная на 2 части аэрирующая сетчатая поверхность, состоящая из двух металлических перфорированных сеток с мелкими отверстиями. Между сетками насыпан мелкий кварцевый песок, внутри бака аэрирующая сетчатая поверхность также занимает наклонное положение с уклоном в сторону выходного отверстия из питателя. Работа питателя начинается с открытия крышки верхнего отверстия и засыпки горячего гранулированного материала. Затем крышка закрьюается, и материал под воздействием "сжижающего" устройства начинает перемещаться в сторону выходного отверстия. В камере выходного отверстия материал подхватывается струей воздуха и поступает в систему пневмотранспорта [111].
При транспортировании абразивных кусковых материалов по трубам часто применяется базальтовая футеровка. Для обеспечения ее соосного расположения между ней и кожухом трубы устанавливают прокладки из поливинил - хлорида или дерева. Остающиеся зазоры заполняются цементной массой под давлением 3 - 5 ати. Для изготовления футеровки базальтовые камни дробят до 20 - 50 мм и обжигают при температуре 1250 С. Расплавленная базальтовая масса подается в песчаные формы или кокили, внутри которых имеются стержни, состоящие из формовочной смеси и обеспечивающие получение отверстия. Применяют также центробежное литье во вращающихся кокилях с окружной скоростью 7 м/сек. Полученная базальтовая масса обладает следующими свойствами: плотность 2,8-2,9 г/см3, твердость по Виккерсу 720, прочность на сжатие 450 кг/см2, жесткость на изгиб 390 кг/см , удельная теплоемкость 0,2 ккал/кгтрад., удельная теплопроводность - 0,86 - 1,0 ккал/м х ч.град., температурная стойкость до 350 С. Коэффициент трения шлифованного базальта в состоянии покоя равен 0,2 - 0,4, в движении 0,1 - 0,2 [112].
Фирмой Edgar Kost (ФРГ) предложена модернизированная конструкция радиусной части ("колена") пневмо-трубопровода, транспортирующего материалы под давлением, большим атмосферного. Внешний радиус колена, подвергающийся наибольшему абразивному износу, по длине выполнен из ряда почти прямолинейных вставок на фланцевых соединениях. Каждая вставка изнутри снабжена вкладышем из упругодеформируемого материала, например резины, который за счет тугой посадки удерживается в П-образном выеме вставки. Во вкладыше имеется осевой канал, совпадающий с проходным поперечником трубопровода. Основное преимущество такого решения заключается в простоте монтажа и демонтажа вставок и вкладышей и устранении случайного выбивания футеровки [113].
|
|