2. Сыпучие и навалочные грузы
УДК 621.869:656,225.073.437
Для ускорения разгрузки насыпных грузов в ряде случаев применяются вспомогательные средства, которые подразделяются на две группы, в зависимости от того, приводят они к изменению свойства сыпучего груза или нет. К первой группе относятся диспергаторы, известные также под названием "ускорители", и аэрирующие устройства. Диспергаторы представляют собой порошки чрезвычайно мелкой фракции (до 10-5 мм), которые при смешивании с сыпучим грузом предотвращают его слеживание и улучшают текучесть. Во вторую группу входят: 1) вибрационные устройства, имеющие электрический механический или пневматический привод и устанавливаемые на стенках бункера ближе к выпускной горловине; 2) устройства (подвижные и неподвижные) внутри выпускной горловины бункера 3) устройства, изменяющие форму бункера и наклон стенок его выпускной горловины; 4) пневматические устройства [46].
В 1970-71 гг. в разных странах разработан ряд устройств для ускоренной погрузки-выгрузки сыпучих грузов.
Так, в США запатентовано устройство, предназначенное для цилиндрических складов сыпучих материалов, например, силосной башни, и состоящее из центральной колонны, образованной стяжками 5 и трубчатыми секциями 4 (рис. 17).
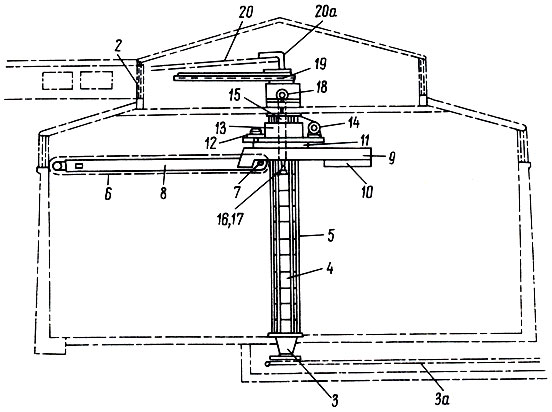 Рис. 17. Погрузочно-разгрузочное устройство для склада сыпучего материала цилиндрической формы
Сыпучий материал поступает через окно 2 и с помощью конвейера 20 перегружается через течку 2 0 а на распределительный конвейер 19, который вращается вместе с центральной колонной. Высыпаемый с этого конвейера материал образует кольцевой валик вблизи среднего диаметра склада. На колонне смонтирована каретка 13, которая может перемещаться вверх и вниз по стяжкам 5 колонны. На каретке установлен распределительный конвейер 8 со скребковой цепью 6. На каретке монтируются привод конвейера 7, противовес 10, механизм подъема и опускания каретки. Каретка поворачивается вместе с колонной, конвейер разравнивает поступающий материал, обеспечивая максимальное использование объема склада при его загрузке. Для выгрузки конвейер 8 сдвигает материал к центральной колонне. Трубчатые секции 4, образующие разгрузочную течку; могут поочередно подниматься с помощью смонтированных внутри трубы захватов 16, 17 и механизма подъема 18. В зависимости от уровня разгружаемого материала необходимое число верхних секций 4 поднимается. В образовавшуюся при этом кольцевую щель высыпается материал, подаваемый скребковым конвейером 8. В нижней части колонны материал поступает на разгрузочный конвейер 3а и убирается. При понижении уровня материала захват 16 опускается ниже и поднимает большее число секций, что обеспечивает разгрузку до заданного уровня [47].
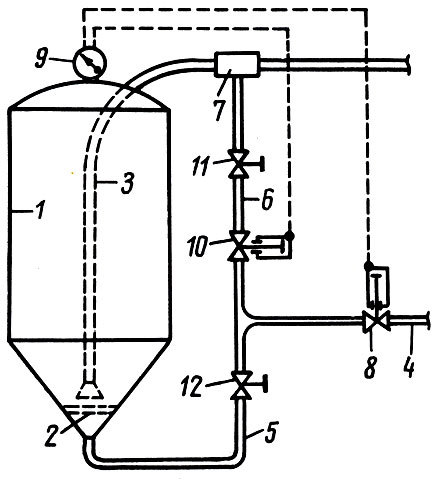 Рис. 18. Разгрузочное бункерное устройство
В Англии разработано устройство, состоящее из бункера (рис. 18) с пористым днищем 2 и разгрузочного трубопровода 3. Сжатый воздух из сети 4 по трубе 5 поступает под днище бункера и по трубе 6 в транспортный трубопровод. При повышении давления в бункере до заданного предела манометр 9 открывает клапан 10 и начинается движение сыпучего материала по трубе 3. В зависимости от колебания давления внутри бункера по комацде от манометра 9 открывается и закрывается клапан 8, что обеспечивает равномерную разгрузку в течение всего цикла [48].
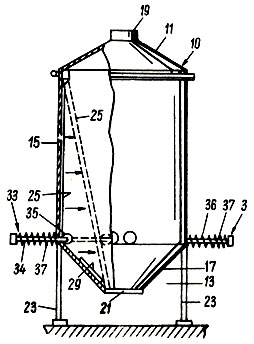 Рис. 19. Бункер
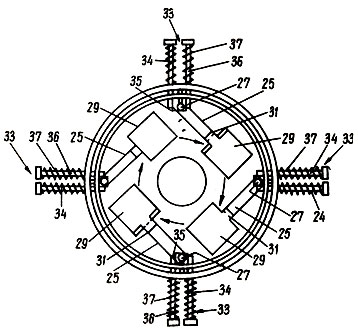 Рис. 20. Плоские сопла
В США предложена конструкция устройства для создания потока порошкообразного материала, проходящего для хранения через бункер. Бункер 10 (рис. 19) состоит из верхней 11 и нижней 1 3 конических частей цилиндрической части 15. Груз поступает в бункер через горловину 19 и удаляется через горловину 21. В бункере 10 установлены воздушные рукава 25 с плоскими соплами 29 (рис. 20) на концах. Эти рукава соединены устройствами 27 (рис. 21) с воздухопроводом. Рукава 25 могут быть прижаты к стенке 15 роликами 35, в результате чего подача воздуха в сопла 29 прекращается. Ролики прижимают рукава 25 к стенке 1 5 под действием пружин 37. При нажатии на болты 34 рукав 25 освобождается роликом 35 и воздух проходит к соплам 2 9. Вытекая из этих сопел, поток воздуха создает поток материала, направленный таким образом, что происходит его удаление из бункера [49].
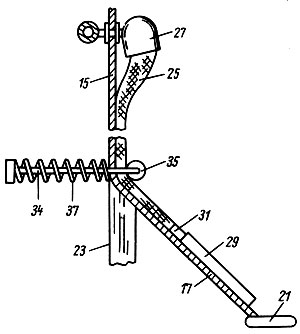 Рис.21. Соединение рукавов с воздуховодами
В СССР запатентовано устройство для загрузки подвижного состава сыпучим материалом. Устройство имеет бункер с затвором и расположенную под выпускным отверстием бункера телескопическую насадку. Размер верхней части насадки соответствует размеру выпускного отверстия бункера, а размер нижней части обеспечивает равномерное наполнение загружаемых платформ. Нижняя часть телескопической насадки оборудована контактирующим с загружаемой платформой подвижным в вертикальной плоскости фартуком. Фартук фиксирован выдвижными фиксаторами на насадке, помешенными в вертикальные пазы фартука, причем длина пазов соответствует просадке рессор. Это позволяет дозировать загружаемый материал путем учета просадки рессор подвижного состава [50]
Для борьбы со слеживанием сыпучих материалов при бестарном хранении и перевозках и обеспечения их устойчивого выпуска из емкостей применяются с хорошими результатами пневмоаэрация (периодическое или непрерывное расширение слоя материала воздухом или другим газом) и аэрожелоба. В процессе исследования получены соответствующие аэродинамические характеристики и установлены их изменения в зависимости от диаметра аппарата, высоты слоя, отношения диаметра аппарата к высоте слоя, материала ограждающих поверхностей, избыточного статического давления и др.
Применение пневмоаэрации для выпуска сухих товарных дрожжей из бункеров, транспортирование их аэрожелобами и тем более разрыхление для предотвращения слеживания неэффективны [51].
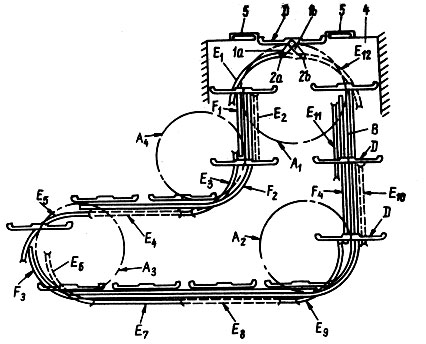 Рис. 22. Подземный конвейер
В Японии запатентован конвейер, расположенный под землей, который предназначен для приемки, хранения и выдачи сыпучих грузов на поддонах или в контейнерах. Конвейер (рис. 22) имеет полки D, укрепленные осями на несущих тросах В. Тросы проходят через направляющие ролики А1 - А4. Одна пара направляющих роликов является ведущей. Вдоль следования полок конвейера по стенкам помещения, в котором размещен накопительный конвейер, имеются пазы Е и Ф. По пазам F следуют подшипники, расположенные на концах осей полок D, a по пазам Е - подшипники 2а и 2b, которые находятся на рычагах 1а и 1b.Последние укреплены на двух сторонах осей полок D. Пазы F и подшипники осей полок D предназначены для направления движения полок по траектории движения несущих тросов В, а пазы Е с подшипниками 2а и 2b и рычагами 1а и 1b для поддержания полок D с погруженными на них поддонами или конвейерами всегда в горизонтальном положении [52].
Гипрохим совместно с Винницким химкомбинатом и Коростеньским опытным заводом треста Укрхимремонт создали опытный образец стационарной скребковой машины производительностью 120 т/ч. Машину обслуживает 1 человек. Выгрузка 1 т апатита с помощью указанной машины почти в 4 раза дешевле выгрузки его механическими лопатами.
Наиболее рациональным и надежным способом транспортирования апатитового концентрата является перевозка его в специальных саморазгружающихся хопперах. Созданы условия для широкого внедрения перевозки флотоконцентратов и фосфоритной муки в железнодорожных цистернах с пневматической загрузкой и разгрузкой [53].
Джезказганским горно-металлургическим комбинатом и институтом НИПИГормаш проведены промышленные испытания погрузочно-транспортной машины ПДН-ЗД. Машина представляет собой пневмоколесное шасси с колесной формулой 4 х 4. Кузов емкостью 6 м разгружается опрокидыванием на любую из боковых сторон. Погрузочный орган-ковш емкостью 1,5 м3. Машина имеет дизельный двигатель ЯМЗ-238 А мощностью 215 л.с. с системой очистки выхлопных газов, гидромеханическую коробку перемены передач НАМИ-0126, двойную стенку тормозов (пневмогидравлический - рабочий на все 4 колеса и механический - стояночный), двухпозиционную кабину управления. Испытаниями установлено, что машина удовлетворяет требованиям погрузки и транспортирования крупнокусковой горной массы в подземных горных условиях при проходке подготовительных выработок сечением свыше 14 м2 и применении камерных систем с безлюковым выпуском руды и высоте камер - 3,5 - 6 м.
При расстояниях транспортирования 150 - 300 м использование машины ПДН-ЗД позволяет снизить стоимость по-грузочно-доставочных работ и поднять производительность труда [54].
Фирмой McDowell - Wallmann Engineering (США) создана новая машина Stakrate, которая представляет собой передвижной скребковый конвейер с изменяющимся от 0 до 30 углом наклона. Отсыпка груза в штабель происходит при поднятом конвейере по его верхней ветви. При заборе груза конвейер опускается и с помошью скребков нижней ветви материал подгребается к забойному конвейеру, расположенному параллельно штабелю [55].
Фирма General Electric Co. (Англия) применила на ряде своих обогатительных фабрик смесительную установку типа Robins - Messiter. В настоящее время построено свыше 100 таких установок. Сырье подается распределительным конвейером и, с помощью передвижного штабелера, укладывается послойно в треугольный штабель. Таких слоев в штабеле может быть до 100, что обеспечивает более однородную смесь. Забор материала из штабеля производится передвижным скребковым конвейером, который разгружается на тоннельном конвейере. Производительность первых установок была до 500 т/ч. Одна из последних смесительных установок содержит роторный ковшовый питатель для забора материалов из штабеля. Роторные питатели монтируются на передвижных мостках с пролетом от 12 до 60 м. Производительность таких установок от 10 тыс. до 1 5 тыс. т/ч [56]
Как известно, в ряде случаев перевозка сыпучих грузов осуществляется в мешках. Фирма Howe Richerdson Scabe (США) применила электронную систему контроля веса продукта при дозировании объема его и компенсации изменений насыпного веса в процессе затаривания. Заполнение мешков с клапанами может производиться тремя способами: шнековым устройством, которое обеспечивает максимальную производительность 6 мешков в 1 мин; импульсным методом, когда порошок предварительно сжимается и через подающую трубу, вводимую в клапан, заполняет мешок со скоростью загрузки 6-7 мешков в 1 мин; с использованием псевдоожиженного слоя, благодаря вводимому в продукт сжатому воздуху низкого давления. В последнем случае воздух подается через специальные форсунки. Сыпучий продукт приобретает свойства жидкости и легко заполйяет мешок.
Фирма H.L.Stoker (США) разработала машину с использованием указанного принципа. Эта машина обеспечивает заполнение до 1 2 мешков в 1 мин. Затем открытые мешки зашивают или склеивают. В ряде случаев зашивание не обеспечивает требуемой герметизации; тогда швы проклеивают лентой. В США в основном применяют закрытые мешки с клапанами или открытые, свариваемые по шву. Фирма St. Regis Paper поставляет машину, выполняющую операции по автоматической термосварке мешков.
Специальный вариант этой машины производит одновременную сварку внутренних швов и склеивание наружных для многослойных мешков из различных материалов [571,
В мае 1969 г. на цементном заводе "Победа Октября" установлена погрузочная машина, состоящая из трех последовательно расположенных ленточных конвейеров лентой шириной 650 мм, которая доставляет мешки с цементом непосредственно к месту погрузки в вагоны. Первая лента установлена на раме, передвигающейся перпендикулярно оси вагона по рельсам вторая закреплена на консоли рамы первой ленты и может поворачиваться в обе стороны третья закреплена на консоли второй и поворачивается в горизонтальной плоскости в обе стороны. Кроме того, она передвигается в вертикальной плоскости, что позволяет регулировать высоту разгрузочного столика в пределах 900 - 1100 мм, считая от пола вагона. Благодаря наличию телескопического приспособления длина может изменяться в пределах 800 мм. Управление электроприводами расположено с обеих сторон на конце выдвижной части третьего конвейера. Все механизмы (за исключением ленточных конвейеров) приводятся в действие нажатием кнопки. Третий разгрузочный конвейер легко поворачивается вручную. Не представляет трудности и ввод машины внутрь вагона. Эта операция осуществляется путем движения станины первого конвейера в сторону вагона с одновременным поворачиванием вдоль его оси третьего и второго конвейеров. Система управления проста и быстро осваивается. Машина облегчила труд грузчиков. Численность обслуживающей бригады сокращена на 1/3. Теперь при помощи укладчика загрузку 4-осного вагона выполняет бригада из 2 человек [58]°
В США разработано устройство для загрузки мешков в автотранспорт. Устройство смонтировано на погрузочной платформе, к которой подается полуприцеп с открытой задней дверью. На платформе расположена стойка с продольными направляющими, по которым перемешается каретка. Ручная тележка с мешками подъезжает к каретке, и пакет мешков переталкивается с направляющих роликов тележки на ролики каретки. Толкатель стойки перемещает каретку сначала по своим направляющим^ затем по состыкованным с ними направляющим на боковых стенках полуприцепа. В конце хода дополнительный толкатель сдвигает мешки в кузов, а каретка возвращается за следующим грузом [59]
В течение последних лет в горнорудной промышленности находят широкое применение тракторные ковшовые погрузчики для погрузки руды и породы. Обычно грузоподъемность их до 10 т, а емкость ковша до 4,59 м3.
Фирма Clark Equipment Co. (США) провела сравнение ковшовых погрузчиков последнего типа Michigan 475 со стандартным экскаватором при использовании на открытых карьерах. Для сравнения был выбран стандартный экскаватор с емкостью ковша 4,59 м3 а ковшовый погрузчик с емкостью ковша 9,18 м , так как их производительность примерно одинакова. Вызывает некоторую трудность сравнение первоначальных затрат на покупку оборудования, так как обычно к экскаватору поставляется различное сменное оборудование. Однако в среднем экскаватор стоит 385 тыс. долл., а ковшовый погрузчик той же производительности 148 тыс. долл. Срок службы экскаватора 20 лет, а ковшового погрузчика 6 лет. Следовательно, ковшовые погрузчики можно чаще заменять более совершенными машинами. Производительность экскаватора в карьере была 789 т/ч, а ковшового погрузчика 890 т/ч. Часовая стоимость эксплутации экскватора 43,28 долл., а ковшового погрузчика 37,27 долл. Стоимость погрузки 1 т руды экскаватором составляет 5,5 центов а ковшовым погрузчиком 42 цента. В карьере дважды в неделю производятся взрывные работы. Ковшовый погрузчик более маневренен. Скорость его передвижения 34,24 км/ч. На перестановку экскаватора из карьера и возврат его к месту работы затрачивается около 40 мин.За счет этого недельная производительность экскаватора снижается на 1260т, а часовая производительность - с 789 до 758 т/ч. От потери производительности возрастает стоимость переработки 1 т руды на 0,2 цента. После работы экскаватора требуется зачистка бульдозером. В этом случае эксплуатационные расходы составляют 15 долл. в 1 ч. Стоимость погрузки 1 т возрастает на 2 цента. Следовательно, общая стоимость переработки 1 т экскаватором составит 7,7 цента, а тракторным погрузчиком 4,2 цента. Недельная экономия при использовании тракторного погрузчика составит 1060 долл., а годовая экономия 53 тыс. долл. Кроме того, ковшовые погрузчики обладают рядом других преимуществ: большей маневренностью, лучшей видимостью при производстве работ, более легким запуском и т.п. Поэтому ковшовые колесные погрузчики находят все более широкое применение на небольших карьерах в качестве основных погрузочных средств. На средних и больших карьерах для основных работ применяются большие экскаваторы, а для вспомогательных - ковшовые погрузчики [60].
В ФРГ разработана машина для погрузки сыпучих ма-териалов на складах древесины, а также на целлюлозных и бумажных фабриках. Машина устроена по принципу экскаватора с гидравлическим приводом. Ее рабочий орган перемещается в различных направлениях.
База машины - серийно выпускаемый экскаватор Liebherr A 921. Кабина водителя может быть расположена на высоте до 4240 мм, что обеспечивает хорошую обзорность при погрузке в вагоны. Машина снабжена 4-цилиндровым дизельным двигателем с воздушным охлаждением мощностью 67 л.с. Гидравлический привод колес обеспечивает скорость движения по дорогам высокого класса до 19,75 км/ч. Опрокидывание ковша производится также при помощи гидропривода. Машина может,не перемещаясь, обслуживать рабочюю площадку радиусом 14 м, обеспечивая до 4 рабочих циклов в 1 мин [61].
На целлюлозном заводе Columbia Cellulose Co. (отделение CelgarPulp, Канада) введена в действие новая высокоэффективная система выгрузки древесной щепы из вагонов, которая дает возможность за 20 мин (включая время на подачу и установку вагона) разгрузить 70т щепы из вагона. Это в 5 раз быстрее, чем до применения этой системы. В зимнее время, когда щепа смерзается, экономия времени еще больше. В состав новой системы входят: 1) пневмоколесный тракторный погрузчик с ковшом емкостью 6,1 м3, ширина которого несколько уменьшена для свободного движения машины внутри разгружаемого вагона с открывающимися торцовыми стенками; 2) подрельсовый бункер емкостью 15,3 м3, над которым располагается открытая торцовая часть разгружаемого вагона; 3) пневматическая трубопроводная сеть, позволяющая перемещать щепу в различные точки, удаленные на расстояние до 320 м. Погрузчик подается к разгружаемому вагону с помощью вспомогательной четырехосной платформы. Колесные тележки платформы могут поворачиваться до 90 (боковое движение) для установки ее перед разгружаемым вагоном до поднятия его торцовой стенки. На платформе установлен тракторный погрузчик, который начинает работу с прямолинейного въезда в разгружаемый вагон.
Выгружаемая из вагона щепа сбрасывается на скребковый конвейер, установленный в донной части подрельсового бункера. Конвейер в свою очередь подает щепу в систему пневмотранспорта, с помощью которого щепа может быть подана к любому из пяти открытых штабелей - хранилищ, предназначенных для временного хранения различных видов древесины, либо непосредственно на технологическое оборудование предприятия [62].
Серьезное внимание в СССР и за рубежом уделяется вопросам организации быстрой выгрузки в зимнее время сыпучих и навалочных грузов, подверженных смерзанию.
Для разгрузки смерзшихся углей на Губахинском коксохимическом заводе используется бурорыхлительная машина типа БРМ - 56 М. Она представляет собой портал, внутри которого на общей подвижной раме смонтированы 4 бура, приводимых в движение двумя электродвигателями мощностью 28 квт каждый. Низ бура оснащен резцами из материала ВК-8. Рама с вращающимися бурами опускается при свободном тросе лебедки под тяжестью собственного веса в вагон на мерзлый уголь, который пробуривается до дна вагона. Затем, при поднятых бурах вагон продвигается на определенное расстояние и производится следующее пробуривание монолита. Для разгрузки вагона требуется 5 - 6 таких операций. На угле - приемных ямах пробуривание можно осуществлять при открытых люках вагонов, а уголь высыпать через решетку в углеприемный бункер. Зачистку вагонов производят вручную. Вес машины 12 т, производительность одного агрегата 200 т/ч. При установке сдвоенных агрегатов производительность машины 300 т/ч. Установку обслуживает один оператор. Капитальные вложения на один агрегат 22 тыс. руб. Недостаток конструкции - бурение только в вертикальной плоскости. Затруднительны разборка, сборка и смазка буров. После доработки отдельных узлов бурорыхлительная машина может найти широкое применение при разгрузке смерзшихся грузов [63].
Для облегчения разгрузки смерзшегося в вагонах угля предложен метод объемного оттаивания у потребителя путем нагнетания конденсирующихся или неконденсирующихся теплоносителей. Создан простой и надежный снаряд для быстрой проходки в мерзлом угле шпуров под трубы - инъекторы. Снаряд состоит из паровой иглы и электродвигателя-вибратора. Нагнетаемый через трубы-инъекторы водяной пар или горячий воздух свободно проникает в поры смерзшегося угля. Время оттаивания одного насквозь промороженного вагона угля при нагревании пара под давлением 4 - 5 ат через 23 - 24 инъектора не превышает 40 - 60 мин. С учетом проходки шпуров продолжительность оттаивания не превышает 1,5 ч, что укладывается в нормы простоя вагона под погрузочно-разгрузочными операциями. Рассмотренный способ, по-видимому, более эффективен на теплоэлектроцентралях, а также вблизи крупных котельных установок. В зависимости от степени промораживания вагонов, и исходной влажности отгружаемого угля, затраты на размораживание составляют 15 - 27 коп. на 1 т угля. Рыхление смерзшегося угля в вагоне другими известными способами обходится в 3 - 5 раз дороже [64].
В США запатентована система обогрева грузовых вагонов для ускорения разгрузки смерзшейся железной руды. Система состоит из постоянно включенных обогревателей, расположенных под вагонами. Оттаивание грузов происходит за счет нагрева вагонов при медленном движении состава по рельсам. Для предохранения резиновых межвагонных соединений (тормозных шлангов, электропроводки и т.д.) от нагрева (и следовательно порчи) предусмотрено их охлаждение [65].
Запатентован также способ обогрева вагонов, обеспечивающий оттаивание смерзшихся кусковых, сыпучих или порошкообразных грузов. Вагоны и другие транспортные средства, обогревают направленным потоком нагретого воздуха, подаваемого непосредственно к кузову вагона. Направленная подача нагретого воздуха под давлением осуществляется специально разработанной для этой цели установкой (рис. 23), обеспечивающей равномерный нагрев кузова вагона при поступлении его на участок разгрузки.
Установка состоит из опорных рам со стойками 11, оборудованных с двух сторон пути 12, на которых смонтированы подвижные каретки, составляющие одно целое с воздушным коллектором 18, связанным с воздуховодами 17, имеющими форсунки 10.
Конструктивный вариант узлов крепления подвижной каретки к воздушному коллектору 18 приведен на рис. 24. Узлы крепления 22 воздуховодов 17с поддерживающими тросами 26, перекинутыми через блок, связаны с помощью двух тяг 27с корпусом воздушного коллектора 18. Воздуховоды 1 7 крепятся к воздушному коллектору при помощи болтов 19, проходящих через отверстия 20 во фланцах 21, укрепленных на торцах воздуховодов 17. Отверстия 20 во фланцах имеют форму эллипса, благодаря чему обеспечивается поворот воздуховодов 17 относительно продольной оси воздушного коллектора 18 и соответствующее регулирование направления потока воздуха из сопел 10.
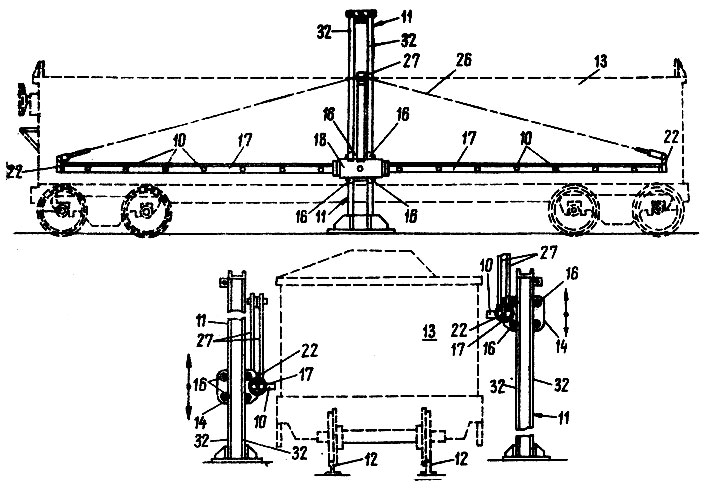 Рис. 23. Установка для подачи нагретого воздуха
Такой простой способ крепления делает возможной быструю сборку установки с учетом использования воздуховодов разной длины для обеспечения обогрева различных по длине транспортных средств. Устройство крепления воздуховодов, обеспечивающее их перемещение по вертикали" определяет равномерное прогревание вагонов по высоте. На рис. 25 показано сечение воздушного коллектора с подсоединенным к нему участком воз духовода, где размещен патрубок 23, предназначенный для присоедине-нения шланга, связывающего коллектор с источником нагретого воздуха. Между наружными и внутренними стенками коллектора прокладывается слой теплоизоляции. Присоединяемый к воздушному коллектору воздуховод представляет собой систему труб 28, проложенных в слое изоляции 25, с отводами к форсункам 10с напорными соплами. Поперечное сечение воздуховода по линии 77 показано на рис. 26. Предлагаемое устройство форсунки предусматривает использованиеряда насадок 29, раслоложенных по убывающему размеру диаметра сопел, и обеспечивает эффективность нагрева с помощью отражателя 30, направляющего струю нагретого воздуха.
 Рис. 24. Узел крепления подвижной каретки, к воздушному коллектору
Непрерывная длительная подача нагретого воздуха под давлением может производиться с помощью компрессора или другим способом, обеспечивающим подачу воздуха с температурой 200 - 250 С при давлении 7,03 кг/см2. Использование данной установки в специальном тоннеле создает предпосылки для автоматизации ряда процессов (подачи вагонов, воздуха и пр.).
В системе могут быть использованы любые типы сопел для разных режимов нагрева разнородных грузов, а также применены различные способы для направления воздушного потока непосредственно в толщу материала. В этом случае воздуховоды с форсунками могут быть оборудованы над вагонами. Дальнейшее развитие данный способ может получить при рассмотрении вопроса использования механической энергии струи сжатого воздуха для разрыхления груза, облегчающего разгрузку [66].
Некоторые фирмы пытаются решить проблему разгрузки смерзшихся или слежавшихся грузов из бункеров с помощью взрывных зарядов, однако это часто приводит к повреждению стенок и затворов бункера, а также ухудшает условия труда. Фирма Long-Airdox (США) разработала две системы, обеспечивающие эффективность и безопасность выгрузки смерзшихся и слежавшихся грузов.
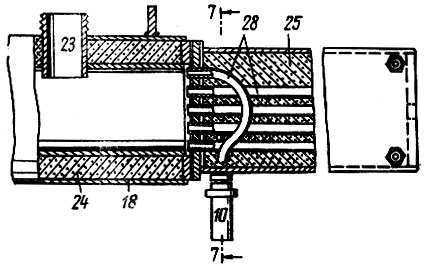 Рис. 25. Разрез воздушного коллектора
Первая из них - Airdox - основана на использовании сжатого воздуха под высоким давлением. Основой системы является шестиступенчатый компрессор, создающий давление 847 кг/см2. От компрессора воздух подводится по системе стальных и медных труб, оборудованных клапанами, к патрону с отверстиями, изготовленному из высокопрочных сплавов. Сжатый воздух выпускается через отверстия патрона циклично с помощью поршня, автоматически с установленной частотой перекрывающего выпускные отверстия. Создаваемое при этом разрушающее усилие 250 - 420 кг/см2 достаточно для дробления большинства слежавшихся и смерзшихся грузов и вместе с тем не приводит к повреждению металлоконструкции бункера.
Второе устройство - Cardox - состоит из высокопрочного патрона, заполненного жидким углекислым газом и химическим агентом. С помощью электрического тока происходит воспламенение агента, при этом выделяется тепловая энергия, достаточная для испарения углекислого газа. Создаваемое при этом давление порядка 700 - 1300 кг/см2 вырывает заглушку патрона и разрушает материал. Это устройство используется, главным образом, для дробления груза в штабелях [67].
Для выгрузки сыпучих и навалочных грузов на металлургических заводах, электростанциях и некоторых других предприятиях все шире применяются вагоноопрокидыватели.
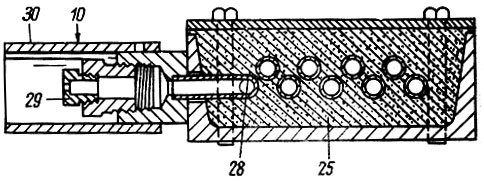 Рис. 26. Поперечный разрез воздуховода
В США запатентована конструкция механизма с противовесами для закрепления вагона в вагоноопрокидыва-теле при его повороте. Вагоноопрокидыватель (рис. 27, 28 и 29) имеет опорные кольцевые элементы 22 и 24. По периферии элементов 22 и 24 на цилиндрической поверхности предусмотрен выступ 25, опирающийся на вращающиеся колеса 26. Ось вращения элементов 22 и 24 совпадает с осью 28 автосцепок с поворотными головками, которыми оборудованы вагоны 34, устанавливаемые на путь 32, уложенный на U-образной раме 30. Эта рама жестко соединена с элементами 22 и 24. Для приведения вагоноопрокидывателя в действие использован реверсивный электродвигатель М, вращающийся с помощью валов 41 и шестерни 44, передающих вращение зубчатым колесам 46, соединенными с барабанами лебедок 48. Концы тросов 50, намотанных на барабаны 52, закреплены на элементах 22 и 24 натяжными болтами 54. Поворот вагоноопрокидывателя ограничивается упорами, до которых могут доходить ролики 56, закрепленные на элементах 22 и 24.
Вагон удерживается на рельсах зажимами 60 и 62, которые приводятся в действие автоматически за счет перемещения противовеса после включения электродвигателя М и начала поворота вагоноопрокидывателя в направлении, указанном стрелкой 64. На элементах рамы 30 закреплены стойки 74 и балки 76 и 78. На стойках 84 укреплена плита 86, на которую опирается боковая стенка вагона во время его опрокидывания. Зажимы 60 и 62 перемещаются в поперечном по отношению к вагону направлении противовесами 110, 104 и 102, соединенными с этими зажимами с помощью рычажной системы.
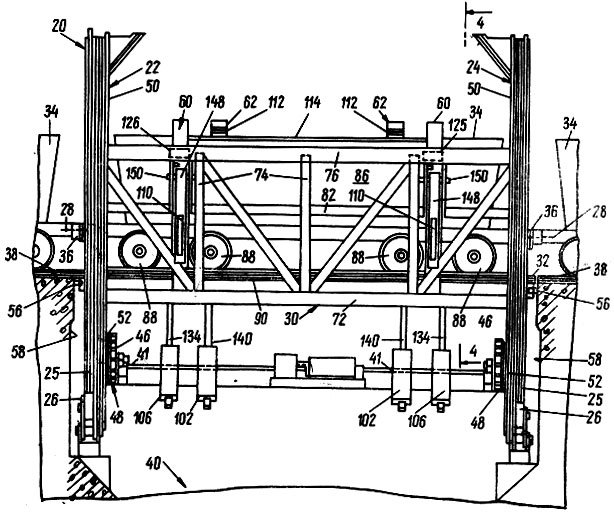 Рис. 27. Общий вид вагоноопрокидывателя
Нижние части зажимов 60 и 62 шарнирно соединены рычажной системой с противовесом 102, который обеспечивает вертикальное перемещение зажимов по отношению к боковым стенам вагона. Для отграничения перемещения противовесов применены упоры, установленные на элементах рамы 30 [68].
Известные способы предотвращения налипания и примерзания сыпучих материалов к поверхностям транспортных средств и сосудов путем нанесения на них покрытия недостаточно надежны и способствуют образованию коррозии на металлоконструкциях. Рекомендован способ, обеспечивающий надежное предотвращение примерзания и прилипания материала и уменьшение коррозирующего действия покрытий. На поверхность наносят аммонизированный водный конденсат или кислые воды, образующиеся при каталитическом окислении до кислот парафиновых углеводородов кислородом воздуха и представляющие собой водный раствор, в основном, низкомолекулярных кислот (муравьиной, уксусной и масляной) и частично альдегидов, кетонов, лактонов, дикарбоновых кислот, спиртов и т.п. Затем поверхность обрабатывают мелкодисперсными материалами, модифицированными поверхностно-активными веществами, например, образующимся при нейтрализации кислых сточных вод производства синтетических жирных кислот известью или жирными кислотами, спиртами либо другими углеводородными продуктами мелкодисперсными инертными материалами (например, сепарированным мелом). Обработка стенок производится в следующем порядке. Вначале на поверхность наносят аммонизированный водный раствор для пропитки деревянных металлических поверхностей, затем производят напыление мелкодисперсных материалов модифицированных поверхностно-активными веществами. При этом на поверхности создается пленка толщиной до 1 мм. Пленку удаляют струей холодной воды под давлением до 2 ат [69].
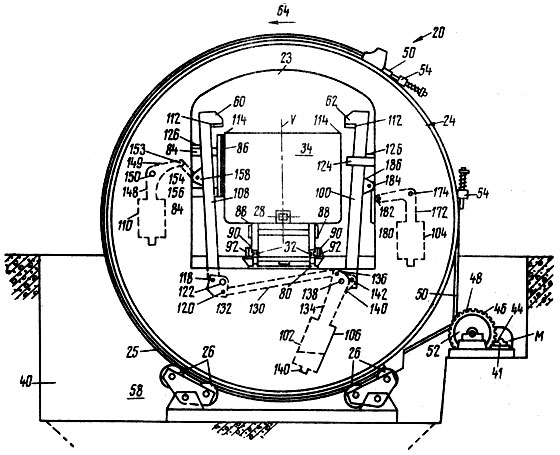 Рис. 28. Поперечный разрез вагоноопрокидывателя
В Англии запатентована конструкция подъемного устройства, смонтированного на козловом кране и предназначенного для грузовых операций с углем и железной рудой.
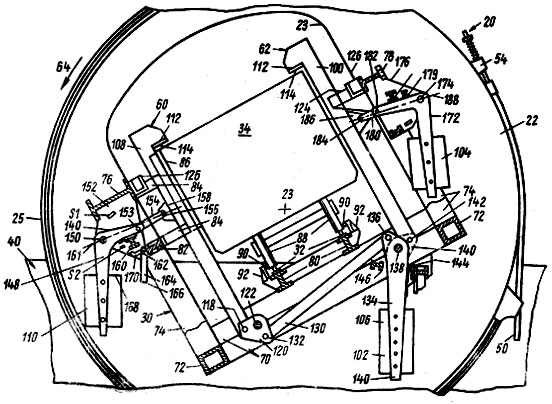 Рис. 29. Вагоноопрокидыватель в наклонном положении.
Ферма 1 (рис. 30) козлового крана установлена на опорах 2, перемещающихся с помощью колес 3 по рельсам 4. По рельсам 6, уложенным по верху фермы 1, перемещается тележка 5 (рис. 31) крана, имеющая раму сварной конструкции. К оборудованию, установленному на тележке 5, подвешен грейферный захват 7, состоящий из ковшей 8, которые установлены на несущих элементах 9.
Натяжение тросов 10 вызывает поворот ковшей 8 и закрытие грейферного захвата. При ослабленных тросах 1 0 ковши 8 под действием собственного веса занимают такое положение, при котором грейферный захват остается открытым. Тросы 11 воспринимают вес захвата с грузом и являются поддерживающими. Тросы 10 наматываются на барабан 12 лебедки, приводимый в действие электродвигателем 13, а тросы 11 - на барабан 15, приводимый в действие электродвигателем 16. Барабан 1 2, редуктор и электродвигатель 13 установлены на промежуточной раме 14, закрепленной на раме тележки 5, а барабан 15, редуктор и электродвигатель 16 - на промежуточной раме 17.
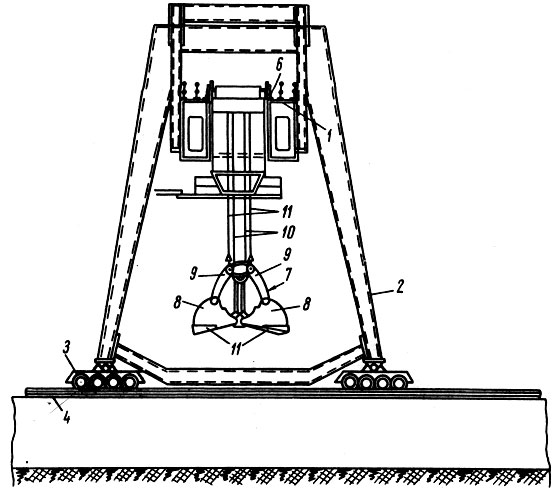 Рис. 30. Общий вид козлового крана
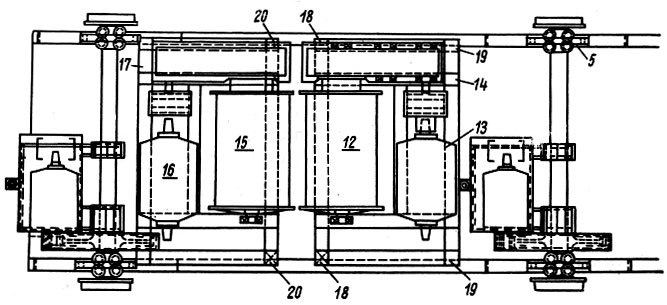 Рис. 31. Тележка козлового крана
Для предотвращения перегрузки грузоподъемного устройства в системе приведения в движение ковшей грейфера применены защитные устройства, представляющие собой весоизмерительные элементы 18, установленные между промежуточной рамой 14 и рамой тележки 5.Эти устройства отключают электродвигатель 13 при превышении определенного веса груза. Аналогичные весоизмерительные устройства защищают от повреждения тросы 11. Элементы 20 этих устройств установлены между промежуточной рамой 17 и рамой тележки 5 и воздействуют на устройства электродвигателя 16 [70].
В настоящее время почти 60% грузов, перевозимых автотранспортом, составляют навалочные грузы, большинство которых перевозится автомобилями-самосвалами. Однако около 1,0 млрд. тонн в год перевозятся бортовыми автомобилями, которые эффективнее самосвалов при расстоянии перевозки более 18 км. Выгодно применять в пунктах с небольшим и неустойчивым грузооборотом навалочных грузов различные самоходные разгрузчики, монтируемые на колесах и гусеничном шасси. Разгрузчики-опрокидыватели, работающие на принципе наклона автомобиля на боковую сторону, моделей А-101, А-107 и А-108, разработаны ЦКБ Министерства автомобильного транспорта РСФСР по принципиальным схемам и техническим требованиям, составленным НИИАТ. Разгрузчики базируются на серийно выпускаемых вилочных погрузчиках Львовского завода автопогрузчиков. Их грузоподъемность 5 т. Целесообразно создание разгрузчика на базе гусеничного трактора для работы в условиях плохих дорог. Экономический эффект от применения передвижных разгрузчиков для выгрузки из бортовых автомобилей и прицепов получается за счет снижения стоимости выгрузки груза и повышения производительности подвижного состава. Эффективно применены передвижные разгрузки модели А-101 в Ташкенте, где общий экономический эффект от использования двух разгрузчиков составил около 160 тыс.руб. в год при уровне механизации погрузочных работ с навалочными грузами 95% [71].
При транспортировании автосамосвалами рыхлые и песчано-глинистые породы вскрыши, а также руды влажностью 15 - 25% сильно прилипают к кузовам автосамосвалов, что значительно уменьшает их емкость. В СССР на одном из рудников применены очищающие устройства, навешиваемые на отвалы бульдозеров, работающих на приемке и планировке породы на автомобильных отвалах. Очистка одного кузова не превышает 3 - 4 мин, навешивание устройства занимает 1,5 - 2 мин, снятие 15 - 20 сек [72].
|