Органы управления автомобилем и подвеска
К органам управления автомобилем относятся: рулевое управление и тормоза, вернее, вся тормозная система. Они являются главными органами и обеспечивают безопасность движения автомобиля. Поэтому к конструированию и изготовлению их нужно отнестись со всей серьезностью, чтобы достигнуть надежности, присущей современному транспортному средству, двигающемуся с большой скоростью в общем потоке автомобилей.
Рулевое управление
Рулевое управление должно обеспечивать движение автомобиля в соответствии с направлением, заданным водителем. Правильность движения управляемых колес не должна нарушаться ни при изменениях положения в результате подрессоривания, ни под действием неровностей и поперечного уклона дороги, бокового ветра, вменения коэффициента сцепления и сопротивления качению на колесах одной стороны по отношению к другим. Поворот рулевого колеса в любую сторону должен быть без значительного усилия и заеданий в рулевом механизме. Рулевое управление должно обеспечивать самовозвращение рулевого колеса из положения поворота в среднее положение.
Несоответствие кинематики рулевого привода и подвески (при деформации ее упругих элементов) также может вызвать колебание управляемых колес и ухудшить управляемость автомобиля. Чтобы избежать этого, рулевой механизм размещают на подрессорной части шасси и так располагают продольную рулевую тягу от сошки до переднего колеса, чтобы при любом движении колес она подвергалась наименьшим осевым перемещениям.
B современных автомобилях управляемыми колесами в подавляющем большинстве являются передние. Если два управляемых колеса размещены на одной оси, то, чтобы обеспечить раздельное поворачивание каждого колеса вокруг своего центра поворота (ряс. 47), их необходимо устанавливать на поворотных цапфах. Поворот передних управляемых колес на разные углы α и β должен обеспечивать их качение без скольжения по своим окружностям, описанным из центра поворота автомобиля. Чем круче поворот, тем больше разница между углами, на которые поворачиваются колеса.
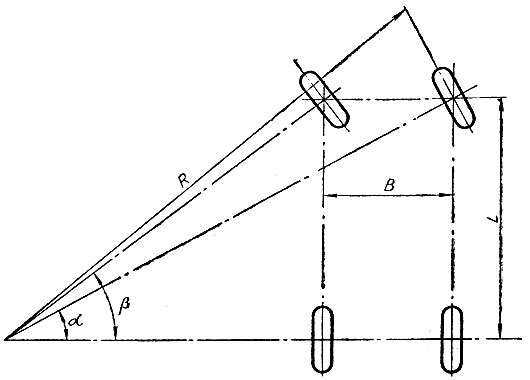 Рис. 47. Схема углов поворота управляемых колес: α - угол поворота наружного колеса; β - угол поворота внутреннего колеса; L - база автомобиля; В - расстояние между центрами поворота колес
Для обеспечения поворота управляемых колес на разные углы служит четырехзвенный механизм, называемый рулевой трапецией. У автомобилей, имеющих балку передней оси, рулевая трапеция образуется балкой передней оси, рычагами поворотных цапф и поперечной рулевой тягой. Такое рулевое управление называется нераздельным. В связи с распространенностью независимой подвески у передних управляемых колес в настоящее время применяется раздельный привод рулевого управления. Здесь рулевая трапеция образуется поперечиной кузова, рычагами поперечных тяг и составной поперечной тягой, соединенной с маятниковым рычагом.
При проектировании рулевого привода определяют размеры рычагов рулевой трапеции, углы их наклона по отношению к продольной оси автомобиля и подбирают необходимые передаточные числа рычажного привода к управляемым осям. Эти расчеты и последующую их проверку часто выполняют графически, вычерчивая в масштабе элементы рулевого управления (схематично) в плане и в виде сбоку. Чтобы проверить, выполняется ли необходимое соотношение между углами поворотов отдельных звеньев механизма, вычерчивают положение одного из элементов в нескольких позициях и связывают геометрически положение всех остальных звеньев.
Помимо выяснения правильности соотношения между углами поворота правого и левого колеса, при графической проверке следует убедиться в том, что перемещения рычагов подвески колес при наезде последних на неровности дороги не будут мешать перемещению рычагов рулевого привода и трапеции и наоборот. Поверочным графическим расчетом окончательно корректируют размеры элементов рулевой трапеции и привода, а также углов их наклона по отношению к продольной оси автомобиля.
При конструировании элементов трапеции можно воспользоваться простым, широко распространенным методом. В определенном масштабе вычерчивают прямоугольник, одна из сторон которого равна базе автомобиля L, а другая - расстоянию между осями поворотных цапф D (рис. 48). На продольной оси этого прямоугольника на расстоянии, равном 0,7 базы автомобиля, ставят точку С, которую затем соединяют прямыми линиями с точками, обозначающими оси поворотных цапф. Вдоль этих линий и располагают рулевые поворотные рычаги трапеции. Положение поперечной рулевой тяги и ее величину можно определить вначале расчетным путем, приняв отношение длины поворотных рычагов к длине поперечной рулевой тяги равным 0,12-0,14.
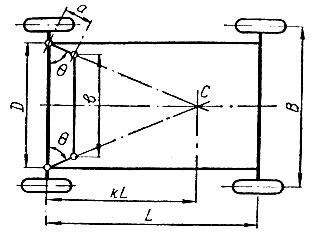 Рис. 48. Определение размеров элементов рулевой трапеции
Затем графически, вычертив несколько положений трапеции, проверяют связь между углами поворота внутреннего и внешнего колес автомобиля. Если не учитывать увода колес, то оптимальным соотношением углов поворота управляемых колес будет такое, когда оси их вращения пересекаются на продолжении задней оси (рис. 47), что соответствует качению колес без бокового скольжения. При этом должно выполняться равенство
Для того чтобы учесть увод шин, возникающий из-за их эластичности, при построении трапеции следует брать не действительный размер базы автомобиля, а увеличенный на 25%
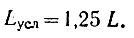
Но не только рулевая трапеция обеспечивает прямолинейное движение автомобиля при среднем расположении рулевого колеса. Во время движения на колеса действуют внешние силы, стремящиеся повернуть колеса вокруг шкворней. Если бы в сочленениях рулевого управления не было зазоров, тогда автомобиль "держал" бы дорогу, как это ему было задано рулевым колесом. Но при наличии зазоров под действием внешних сил колеса могут занять другое положение. Во избежание этого оси шкворней и сами колеса устанавливают с некоторым наклоном, чтобы при выводе колес из нейтрального положения они под действием возникающих сил сами возвращались в исходное положение. Это называется стабилизацией управляемых колес. Углы наклона колес к вертикали и горизонтали, направленной вдоль автомобиля, и углы отклонения шкворня от вертикали называются углами стабилизации передних колес автомобиля.
Угол развала колес у отечественных автомобилей находится в пределах 0° 30-1°. Сходимость колес можно принять около 3 мм, углы установки шкворней в поперечном направлении - 3-6°, в продольном - от 0° до 3°, Учитывая, что рулевое управление является важным узлом, обеспечивающим безопасность движения автомобиля, необходимо, особенно при создании четырехместных микроавтомобилей, использовать уже имеющиеся заводские конструкции и только в исключительных случаях применять самодельные рулевые управления. Это, конечно, не относится к тихоходным и небольшим по весу детским микроавтомобилям. Здесь конструктор может в полную меру приложить свои знания и, возможно, создаст оригинальное рулевое управление, не уступающее заводским конструкциям.
Во всех остальных случаях, если возникнет необходимость, рулевые управления следует делать по подобию тех, которые установлены на мотоколясках и автомобилях "Москвич" и "Запорожец", с максимальным использованием деталей от этих механизмов, особенно шарнирных сочленений рулевых тяг. Детали и узлы их можно приобрести в автомагазинах и магазинах спортивных товаров. При конструировании рулевых управлений следуй правильно подобрать передаточное отношение как рулевого механизма, так и рулевого привода. Исходить нужно из максимальных углов поворота управляемых колес, которые не должны превышать 40-45°, при этом рулевое колесо у автомобилей делает поворот на 1,5-3 оборота в каждую сторону, что соответствует угловому передаточному числу, равному 12÷25. Угловые же передаточные числа рулевых механизмов автомобилей "Москвич" и "Запорожец" равны 17, а мотоколяски - 10,5. Угловое передаточное число рулевого управления iω, представляющее отношение угла поворота рулевого колена к углу поворота управляемых колес, есть произведение передаточного числа рулевого механизма iм и рулевого привода iп
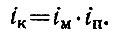
Под угловым передаточным числом рулевого механизма понимают отношение угла поворота колеса и вала сошки или соответственно угловые скорости вращения рулевого колеса и вала сошки
где dθк, dθс - элементарные углы поворота рулевого колеса и вала сошки;
ωк, ωс - соответственно их угловые скорости. Передаточное число рулевого привода iп зависит от соотношения плеч рычагов привода и может быть определено как отношение плеч рычага поворотной цапфы и рулевой сошки
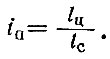
Если имеется готовый рулевой механизм, но с недостаточным угловым передаточным числом, то можно несколько повысить общее угловое передаточное число рулевого управления, подбирая соответствующие длины рычага поворотной цапфы и рулевой сошки. В случае отсутствия рулевого механизма можно самому изготовить его. Для этого нужно использовать простой механизм типа шестерни-рейки, который позволит сократить в рулевом приводе количество шаровых соединений, являющихся ответственными узлами привода, Однако этому механизму присущи некоторые недостатки. Его угловое передаточное отношение, о котором говорилось выше, редко превышает 10-12. При разработке конструкции механизмов такого типа трудно получить удовлетворительный узел компенсации неравномерного износа рейки. Он не создает у водителя ощущения движения по прямой.
В механизмах других типов передаточное отношение изменяется с изменением угла поворота рулевого колеса. Несколько изменяется также коэффициент полезного действия механизма. Это позволяет водителю, как говорят, чувствовать то положение рулевого колёса, при котором автомобиль движется прямолинейно. Этот недостаток реечного рулевого механизма можно устранить, если фиксировать среднее положение рейки, соответствующее движению колес по прямой, с помощью шарикового фиксатора.
На рис. 49 показана простейшая конструкция рулевого механизма реечного типа. Рулевой вал 1 с помощью штифтов или другого элемента соединяется с хвостовиком шестерни 11, располагаемой в картере рулевого механизма 4. Хвостовик шестерни вращается во втулке 3, зажатой между крышкой картера 2 и упорной шайбой 12. Положение шестерни вдоль ее оси изменяется с помощью регулировочного винта 8. Рейка 7 перемещается перпендикулярно оси шестерни в специальном направляющем отверстии картера рулевого механизма.
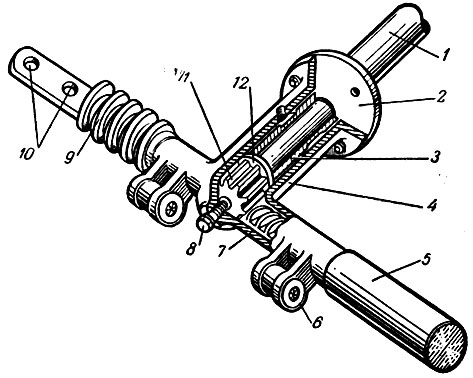 Рис. 49. Рулевой механизм реечного типа: 1 - рулевой вал; 2 - крышка картера; 3 - эксцентриковая втулка; 4 - картер рулевого механизма; 5 - чехол рейки; 6 - проушины для крепления рулевого механизма; 7 - рейка; 8 - упорный регулировочный винт; 9 - гофрированный чехол рейки; 10 - отверстия для установки шаровых сочленений; 11 - шестерня; 12 - упорная шайба
Рейка с одного конца закрыта глухим резиновым чехлом 5, а с другого защищена от попадания грязи и влаги в механизм гофрированным резиновым чехлом 9. Выступающий из гофрированного чехла конец рейки имеет два конических отверстия, в которые укрепляют шаровые пальцы шарниров поперечных тяг, так как этот механизм предназначен для независимой подвески передних управляемых колес. Он может применяться и для управляемых колес с неразрезной балкой и зависимой подвеской, тогда будет вполне достаточно одного отверстия. На литом картере имеются две проушины 6 для крепления рулевого механизма к балке передней подвески. При самостоятельном изготовлении рулевого механизма картер можно выполнить сварным из выточенных на токарном станке деталей. От проворачивания во время работы механизма рейка удерживается шпонкой, помещенной в нижней части картера. Шпонка крепится на винтах, и под нее ставят прокладки. Изменяя толщину прокладки под шпонкой, можно устранить зазор между шестерней и рейкой. Расстояние между шестерней и рейкой можно изменить и за счет поворота эксцентриковой втулки.
Те, кто знаком с расчетом деталей на прочность, могут не только подобрать узлы и элементы рулевого управления, но и произвести проверочные расчеты всех рычагов и тяг. Нагрузки на детали рулевого управления подсчитывают, когда известно усилие, приложенное к рулевому и управляемым колесам.
В первом случае считается, что водитель на окружности рулевого колеса может приложить касательную окружную силу, равную 40 кгс. Тогда нетрудно подсчитать момент, соответствующий этой силе, который будет приложен к валу рулевого колеса,
Затем нетрудно определить нагрузки во всех звеньях рулевого управления, рассматривая последовательно кинематическую связь его отдельных элементов. Коэффициент полезного действия рулевых механизмов колеблется в пределах от 0,5 (червячных) до 0,8 (механизмов реечного типа). Общий к. п. д. рулевого управления для автомобилей с одной передней управляемой осью составляет 0,5-0,7.
Во втором случае за расчетный принимается момент сопротивления повороту колес на месте. Для расчетов можно воспользоваться полуэмпирической формулой, которая дает результаты, достаточно близкие к действительным,
где Gк - нагрузка на колесо;
φ - коэффициент сцепления;
Р - давление воздуха в шине.
После чего можно рассчитать силу на рулевом колесе
где lс - плечо рулевой сошки;
lп.р. - плечо поворотного рычага;
Rк - радиус рулевого колеса;
iп - передаточное число рулевого механизма;
ηр.у. - к. п. д. рулевого управления.
Так как рулевой механизм в самодельных микроавтомобилях берется из готовых, изготовляемых заводами на его расчете останавливаться нет надобности. Чаще всего приходится либо изготавливать, либо подгонять из существующих вал рулевого управления. Рассчитывав вал рулевого управления на прочность, следует определить возникающие в нем напряжения от кручения по формуле
где Мв - момент на валу, кгм;
D - наружный диаметр полого вала, м;
α - отношение внутреннего диаметра вала к наружному
Полученное напряжение при сдвиге сравнивают с допускаемым напряжением, которое следует брать по пределу текучести, принимая запас прочности n в пределах 2,5-3,5.
где σт - предел текучести для данного материала, кгс/м2. Если вал длинный, тогда необходимо произвести расчет на жесткость, определяя угол закручивания по формуле
где lв - длина вала, м;
Мк - максимальный крутящий момент на валу, кгс/м2;
G - модуль сдвига, который в расчете стальных деталей следует принимать равным 78-80 кгс/м2;
J - полярный момент инерции сечения, м4.
Полярный момент инерции вала сплошного сечения подсчитывается так
а для полого вала при известном отношении
Рычаги, работающие на изгиб и кручение (сошка, рычаги, передаточные рычаги поворотных цапф), рассчитываются на сложные напряжения изгиба и кручения по известным формулам сопротивления материала. Продольная, поперечная межосевые тяги привода рассчитаются на сжатие и продольный изгиб. Растяжение вызывает меньше опасений. Сжатие тяг может привести к потере их продольной устойчивости. Поэтому следует произвести расчет на определение критического напряжения, при котором появляется опасность потери устойчивости. Это можно сделать по формуле
где l - длина тяги;
F - площадь поперечного сечения тяги, м2;
Е - модуль упругости первого рода, кгс/м2;*
* ()
I - экваториальный момент инерции сечения, который для круглого сечения подсчитывается по формуле
После чего рассчитывается напряжение сжатия по формуле
где Рт - продольное усилие, кгс.
Зная критическое напряжение и напряжение сжатия, можно определить запас устойчивости, который представляет собой отношение критического напряжения к напряжению сжатия
Запас устойчивости следует принимать равным 1,25-2,5. При изготовлении рулевого механизма для шестерни следует брать цементуемую сталь 12ХНЗА. Рейку можно изготавливать из углеродистой стали 45 с последующей термообработкой (закалкой и отпуском). Для рулевых валов и рулевых тяг применяются бесшовные трубы из стали 30, 35 и 40. Рычаги поворотных цапф и сошек рекомендуется делать из стали 40, 40Х и 40ХН.
Тормозная система
Другой системой, от которой также зависит безопасность движения, является тормозная система. Состоит она из тормозов, которые располагаются обычно на колесах, и тормозного привода, передающего усилие от рычага или педали к тормозным механизмам.
По существующим в Советском Союзе нормативам тормозной путь легковых автомобилей при торможении на горизонтальном участке дороги со скорости 30 км/час должен быть не больше 7,2 м, а максимальное замедление при этом не менее 5,8 м/сек2.
Если рассматривать процесс торможения, то за все время тормозного пути действительное торможение с полным тормозным моментом на колесах происходит только за определенную часть этого пути. Какое-то, хотя и небольшое, время необходимо для реакции водителя и срабатывания тормозного привода, куда относятся выбор зазора в приводе и механизме тормозов и нарастание тормозного усилия. Учитывая последнее, можно сразу сказать, что гидравлический привод в тормозных системах предпочтительней, так как время срабатывания у него является наименьшим. Но все же в самодельных микроавтомобилях, а также в мотоциклах применяется большей частью механический привод как наиболее простой в изготовлении.
Для безопасности и безотказности действия тормозов на автомобилях устанавливают две или даже три тормозные системы. В микролитражных машинах в основном две системы тормозов: рабочий и стояночный тормоз. У автомобилей с весом не выше 600 кг допускается установка рабочих тормозов только на задние колеса, в то время как на автомобилях с большим весом тормоза должны быть на всех колесах.
Если на микроавтомобиле вы решили использовать гидравлическую систему привода тормозов, то, конечно, ее лучше всего взять от автомобиля "Запорожец" или от мотоколяски СЗАМ, для чего на колесах нужно установить тормозные диски и тормозные барабаны вместе с внутренними механизмами. Эти системы подробно описаны в специальной технической литературе.
Все же большее распространение на самодельных микроавтомобилях, как уже отмечалось выше, получают тормоза с механическим приводом. Они более просты в устройстве и эксплуатации, несмотря на то, что время срабатывания привода несколько больше и сложнее их регулировка. На рис. 50 показано устройство механического привода тормозов, которое может быть применено на микролитражных автомобилях. Тормозная педаль 5, укрепленная на валике 9, с помощью рычагов и тросов воздействует на рычаги разжимного кулака 7 и через них на тормозные колодки. На этом же валу находится привод ручного тормоза, связанный с рычагом 4, который при действии ножного тормоза остается на месте.
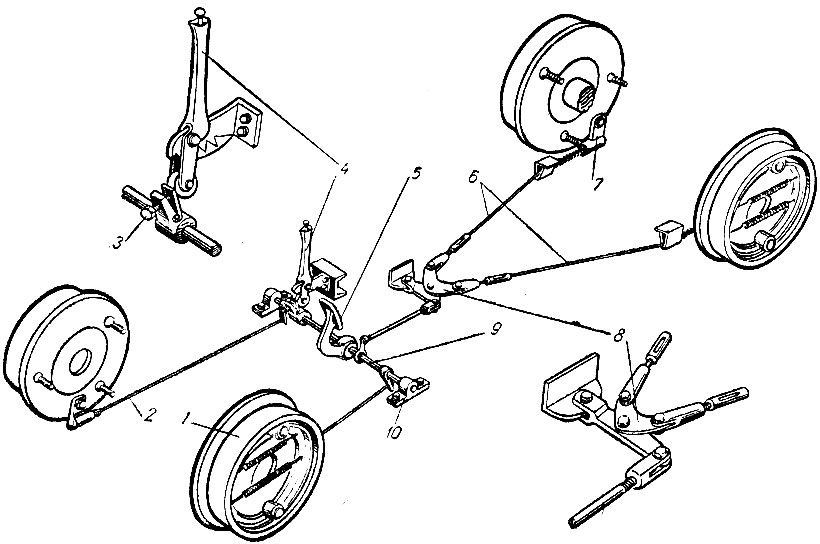 Рис. 50. Схема устройства механической системы привода тормозов: 1 - тормоз; 2 - тяга переднего тормоза; 3 - регулировочный винт ручного тормоза; 4 - рычаг привода ручного тормоза; 5 - педаль привода ножного тормоза; 6 - тяги к задним тормозам; 7 - рычаг разжимного кулака тормозного механизма; 8 - коромысло уравнения тормозных усилий на задних колесах; 9 - поперечный тормозной валик; 10 - подшипник тормозного валика
Если происходит затормаживание ручным тормозом, педаль не изменяет своего положения, так как свободно сидит на валу и поворачивает последний, действуя на специальный упор. Таким образом, в данной конструкции рабочие тормоза всех четырех колес являются стояночными. Привод ручного тормоза можно сделать только на два задних колеса. Рычаг привода ручного тормоза должен обязательно иметь фиксирующее устройство, для того чтобы его можно было оставлять в заторможенном состоянии. Обычно это устройство выполняется в виде храпового механизма, Чтобы обеспечить одинаковые усилия в приводе на каждое из задних колес, в механизм привода включается уравнительное устройство. За счет различной длины рычагов привода, насаженных на вал, можно изменять тормозные усилия передних и задних колес. В механизме привода тормозов обязательно должны быть предусмотрены регулирующие устройства натяжения тросов для регулировки свободного хода педали и рычага стояночного тормоза. Проектируя привод, следует тщательно продумать все узлы, чтобы исключить возможность заеданий механизма в процессе эксплуатации.
Тормозные устройства колес для системы с механическим приводом необходимо брать готовые, заводские, которые устанавливаются на мотоциклах, мотороллерах и мотоколясках.
При выборе тормозных устройств необходимо обратить внимание на те, которые будут наиболее эффективными для автомобиля данного веса, т. е. они должны развивать на колесах требуемые тормозные усилия. Если тормоза недостаточно мощные, возрастет тормозной путь автомобиля. Если же тормозной момент у выбранного тормоза больше, чем требуется, будет происходить частая блокировка колес при торможении. Это приводит к повышенному износу шин и к возрастанию тормозного пути. Исследования показали, что тормозной путь автомобиля с заблокированными колесами на 15-20% больше, чем при торможении, когда колеса находятся на грани блокировки.
Тормозные усилия на колесах и тормозной момент, которые потребуются автомобилю, можно подсчитать после завершения компоновки, когда ориентировочно будет известен полный сухой вес автомобиля. Нужно узнать вес автомобиля с пассажирами и снаряжением. Зная процентное распределение веса по осям, можно подсчитать нагрузку на каждое колесо.
При этом следует учитывать перераспределение нагрузок по колесам в процессе торможения. Нагрузка на передние колеса возрастет, а на задние - уменьшится. Когда известны статические нагрузки на колеса Gп и Gз, высота центра тяжести h, расстояние центра тяжести по горизонтали от передней оси а, можно подсчитать возникающие реакции на колесах передней и задней оси.
Для колес передней оси
Для колес задней оси
Если положение центра тяжести автомобиля неизвестно, тогда ориентировочно можно определить перераспределение нагрузки по осям, умножая статические нагрузки на коэффициенты перераспределения, которые для передней оси можно взять в пределах m1=1,7, а для задней оси m2=0,6 (значения средние). Тогда
Зная нагрузки, приходящиеся на каждое колесо, можно подсчитать тормозное усилие, которое необходимо приложить к колесу, чтобы полностью использовать его сцепной вес на дороге с твердым покрытием. Для этого в расчете принимаем коэффициент сцепления 0,8 (значение для обычных асфальтовых дорог). Перемножив вес, приходящийся на колесо, на этот коэффициент, получим максимально возможное тормозное усилие, которое допустимо по сцеплению колеса с дорогой
Если теперь это тормозное усилие умножить на радиус качения колеса, получим максимальный тормозной момент, который можно допустить на колесе при полном использовании сцепного веса. Тормозной момент больше этого расчетного приведет к блокировке колес со всеми нежелательными явлениями, о которых говорилось выше.
Когда тормозные механизмы на всех колесах будут одинаковыми, их следует подбирать по наиболее нагруженному колесу (максимальному тормозному моменту). Зная конструкцию тормоза, можно определить значение тормозного момента аналитически - расчетным путем. Расчет тормозных механизмов различных типов приведен в специальной литературе*.
* (
Н. А. Бухарин, В. С. Прозоров, М. М. Щукин. Автомобили. Теория рабочих процессов, теория прочности агрегатов и систем автомобиля (под ред. Н. А. Бухарина). М., "Машиностроение", 1965.)
Подобрать тормозные механизмы можно другим методом, не производя расчета. Известно, что тормоза мотоциклов, мотороллеров и мотоколясок обеспечивают при установленной нагрузке необходимую эффективность торможения. Следовательно, если определить нагрузку на колеса и принять условия, аналогичные вышерассмотренным (когда коэффициент сцепления 0,8), нетрудно подсчитать тормозное усилие и тормозной момент.
Наконец, имея собранный тормозной механизм, можно чисто экспериментальным путем определить тормозной момент следующим образом. Закрепить колесный тормоз за опорный диск (рис. 51). На тормозной барабан установить рычаг, длина которого должна быть несколько больше 1 м, чтобы затем на нем, на расстоянии 1 м от центра оси тормозного барабана, можно было сделать отметку или треугольный запил. При заторможенных колодках на расстоянии 1 м на рычаг навесить гири или навески, пока барабан не провернется. Вес гирь укажет в данном случае тот тормозной момент, который могут дать испытываемые тормоза. При этом необходимо, чтобы усилие на рычаге тормозного кулачка, разжимающего колодки, было такое же, какое возникает в результате нажатия на педаль с силой 50 кг. Определить это усилие можно тогда, когда в тормозном приводе известны плечи всех рычагов привода и выбрана педаль. Конечно, лучше всего определять требуемый тормозной момент, укрепляя тормозные механизмы с рычагом на ступицах колес собранного шасси с готовым тормозным приводом.
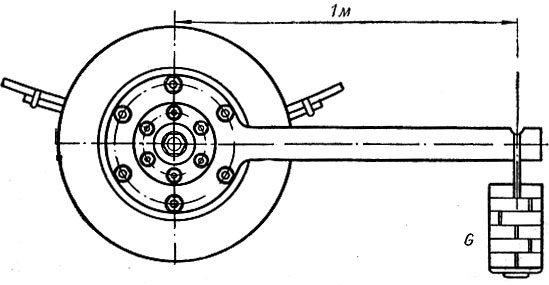 Рис. 51. Схема определения тормозного момента на колесе автомобиля
При длительном торможении тормозные колодки нагреваются, и в результате снижения коэффициента трения между поверхностями тормозных накладок и барабаном начинает снижаться эффективность торможения. Поэтому, конструируя тормозные механизмы, необходимо произвести расчет нагрева тормозов. Учитывая сложность и недостаточную точность такого расчета, эффективность действия тормозов при длительном торможении часто определяют отношением веса автомобиля к общей площади тормозных накладок
В легковых автомобилях, у которых тормоза находятся в худших условиях для охлаждения, так как колеса располагаются под крылом кузова и эффективность торможения выше ввиду высоких скоростей и больших замедлений, рекомендуется брать это отношение в пределах 1,3÷4,0 кгс/см2.
Ручной стояночный тормоз, предназначенный для удержания автомобиля на наибольшем подъеме, должен быть достаточно эффективным. Наиболее неблагоприятными условиями для автомобиля, имеющего привод от стояночного тормоза только на задние колеса, будут такие, когда он не затормаживается на уклоне. В этом случае для удержания его потребуются тормоза, способные развивать тормозной момент, равный:
где α - величина уклона в градусах;
L - база автомобиля, м;
h - высота центра тяжести, м;
а - расстояние по горизонтали от передней оси до центра тяжести, м;
rк - радиус качения колеса, м;
Ga - полный вес (масса) автомобиля, кг.
При затормаживании автомобиля на подъеме с величиной угла подъема α на задних его колесах должен быть приложен несколько больший момент, чем рассчитанный по вышеприведенному уравнению. В этом случае необходимо, чтобы тормоза развивали тормозной момент, равный
Описанное выше относится к приводу стояночного тормоза только на задние колеса. Когда же стояночный тормоз при затормаживании автомобиля действует на все колеса, то общий тормозной момент должен быть равен
При известных значениях тормозных моментов на колесах, используя вышеприведенные уравнения, можно решить обратную задачу по определению максимального угла наклона, на котором эти тормоза еще будут способны удерживать автомобиль.
Рычаг привода стояночного тормоза должен быть так связан с остальными деталями тормозных механизмов, чтобы водитель, затормаживая автомобиль, перемещал его по направлению к себе.
Ходовая часть
Конструируя ходовую часть шасси, соединять раму или кузов с мостами (колесами) автомобиля следует элементами подвески, в которую входят упругие элементы, направляющие устройства и амортизаторы.
Первые смягчают динамические нагрузки, действующие от колес на раму, и обеспечивают требуемую плавность хода.
Направляющие устройства передают на раму действующие со стороны Дороги и колеса силы и моменты, а амортизаторы предназначены для гашения возникающих колебаний.
В качестве упругих элементов подвески применяются листовые рессоры, спиральные пружины, торсионы, резиновые и телескопические гидравлические элементы. Пневматические элементы, получающие в последнее время распространение в автостроении, при создании самодельных автомобилей пока не используются.
Колебания подвески гасятся большей частью гидравлическими амортизаторами одностороннего и двустороннего действия, которые выпускаются промышленностью, а иногда за счет трения в упругом элементе и направляющем устройстве или за счет специально сконструированных амортизаторов механического трения.
В самодельных микроавтомобилях могут применяться как зависимые подвески, когда перемещение одного колеса в поперечной плоскости передается другому колесу, так и независимые, при которых непосредственная связь одного колеса с другим отсутствует. В зависимых подвесках правое и левое колеса одной оси связываются жесткой балкой, которая через подвеску связана с рамой или кузовом автомобиля. В независимых подвесках каждое колесо связывается с рамой или кузовом одним или двумя рычагами, перемещающимися независимо друг от друга.
На рис. 52 приведены основные типы независимых подвесок, которые могут быть использованы для самодельных микролитражных автомобилей. Первые две схемы (а и б) дают представление об однорычажной и двухрычажной подвесках с перемещением колес в поперечной плоскости. Две другие схемы (в и г) показывают, как можно выполнить однорычажную и двухрычажную подвески колес, качающихся в продольной плоскости. Если ось крепления рычага разместить под углом к продольной оси автомобиля, то можно получить подвеску с перемещением колес одновременно в продольной и поперечной плоскостях (рис. 52, д). Наконец, встречается вариант свечной подвески (рис. 52, е), когда колесо при наезде на препятствие поднимается вертикально вверх, не изменяя углов установки.
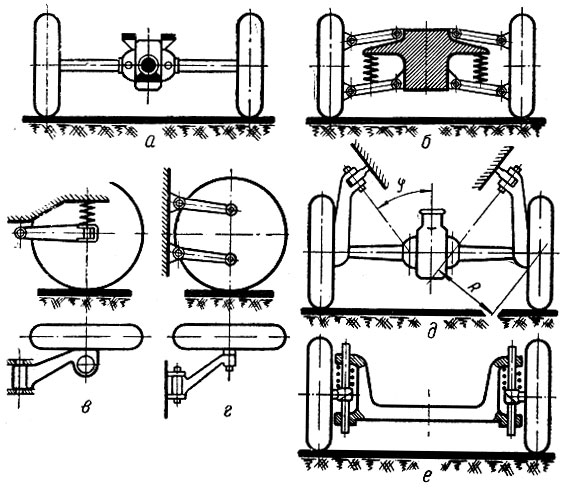 Рис. 52. Основные типы независимых подвесок: а - с разрезными осями с перемещением колес в поперечной плоскости; б - на двух рычагах с качением колес в поперечной плоскости; в - на одном рычаге с перемещением колес в продольной плоскости; г - на двух рычагах с перемещением колес в продольной плоскости; д - на одном рычаге с перемещением колес в продольной и поперечной плоскостях; е - свечная подвеска
Для зависимых подвесок наиболее простой является подвеска на полуэллиптических рессорах (рис. 53). Такие рессоры, например, применены в автомобилях "Юный сибиряк" и "ХАДИ-2". Рессора является не только упругим элементом, но и составляющей частью направляющего устройства. За счет трения между рессорными листами происходит частичное гашение возникающих колебаний. Но все же и при этой подвеске для обеспечения комфортабельности часто необходимо ставить амортизирующие устройства. Вместо рессор в качестве упругого элемента в зависимых подвесках могут употребляться винтовые пружины с расположенным внутри или снаружи их резиновым буфером. Подвеска на пружинных упругих элементах обязательно требует направляющего устройства для передачи продольной силы и ее моментов. Пружинные упругие элементы, так же как и торсионные, не обладают способностью гасить возникающие колебания, а поэтому при применении их обязательно наличие амортизирующих устройств.
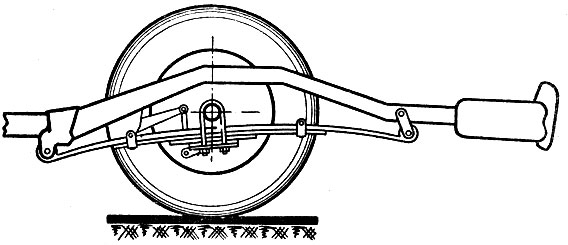 Рис. 53. Рессорная подвеска заднего колеса
На рис. 54 показан один из возможных вариантов зависимой подвески с упругими элементами в виде спиральных пружин. Применять зависимую подвеску обычно рекомендуется для неуправляемых колес. А на микролитражных автомобилях из-за расположения силового агрегата в задней части автомобиля, даже для задних неуправляемых колес, применяют большей частью независимую подвеску. Это позволяет более компактно разместить силовой агрегат и главную передачу, а также снизить общую высоту автомобиля. Примером такой конструкции может служить независимая подвеска ведущих колес автомобиля БМВ-700, относящаяся к типу однорычажных с качением колеса в продольной плоскости. Направляющим элементом здесь является рычаг, прикрепленный к раме шарнирно в двух точках.
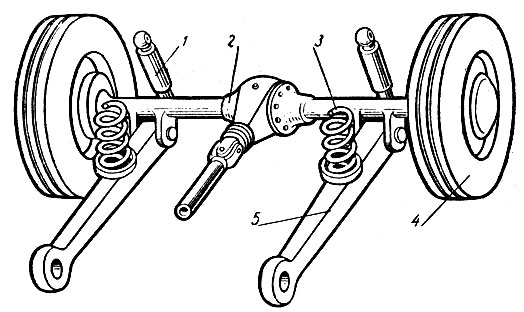 Рис. 54. Зависимая подвеска заднего моста с пружинными упругими элементами: 1 - амортизатор; 2 - задний мост; 3 - пружина подвески; 4 - колесо; 5 - направляющий элемент подвески
На следующем рис. 55 изображена однорычажная независимая подвеска колеса, где в качестве упругого элемента применен пластинчатый торсион, заключенный в трубчатый чехол, который одновременно является поперечиной рамы. Такая подвеска проста в изготовлении и может с успехом применяться в конструкции самодельных автомобилей. Рычажные подвески с качением в продольной плоскости, помимо простоты, обеспечивают при колебании колес постоянство колеи.
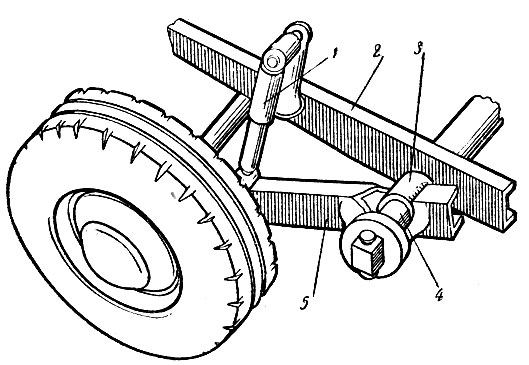 Рис. 55. Независимая однорычажная подвеска с торсионом: 1 - амортизатор; 2 - рама автомобиля; 3 - трубчатая поперечина; 4 - пластинчатый торсион; 5 - качающийся рычаг
Недостатками однорычажных подвесок с продольным расположением рычагов являются значительный наклон шин при повороте и трудность в обеспечении необходимой жесткости рычага при действии боковых сил и моментов.
Это можно устранить, если ось качения рычагов однорычажной подвески расположить под углом к продольной оси автомобиля, т. е. изготовить подвеску по схеме, изображенной на рис. 52, д. Тогда колеса смогут перемещаться как в продольной, так и в поперечной плоскостях. Подобное направляющее устройство в виде вильчатого качающегося рычага с резиновыми втулками в качестве шарниров применено в задней подвеске автомобиля "Запорожец".
Описание других типов подвески колес существующих микролитражных автомобилей можно найти в специальной литературе.
В самодельных микроавтомобилях очень широко используется подвеска от мотоколясок Серпуховского завода. Передний мост этих колясок имеет независимую торсионную подвеску. Подвеска задних колес независимая с цилиндрическими пружинами. В качестве упругих элементов внутри пружины вставлен резиновый буфер, ограничивающий сжатие витков.
Фрикционный амортизатор задней подвески мотоколясок (рис. 56) состоит из двух внутренних 3 и двух наружных 7 пластин, двух фрикционных шайб 4, выпуклой стальной шайбы 5, пружинной шайбы 2, стяжного болта 6 с гайкой 1 и стопорного кольца 9. Внутренние и наружные пластины одним концом своим насажены на стальную втулку и соединены с ней сваркой. Другие концы внутренних и наружных пластин через фрикционные шайбы соединены между собой посредством стяжного болта, выпуклой шайбы и гайки. Это дает возможность внутренним и наружным пластинам проворачиваться относительно друг друга. Изменять жесткость амортизатора можно, завертывая или ослабляя гайку стяжного болта.
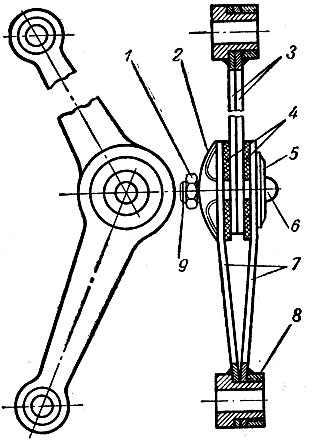 Рис. 56. Фрикционный амортизатор: 1 - гайка; 2 - пружинная шайба; 3 - внутренние пластины; 4 - фрикционные шайбы; 5 - выпуклая шайба; 6 - стяжной болт; 7 - наружные пластины; 8 - втулка крепления амортизатора; 9 - стопорное кольцо
В качестве независимой подвески задних колес можно использовать маятниковую вилку мотоциклов Ижевского завода вместе с амортизирующими устройствами, которые одновременно являются и упругими элементами подвески. Для маленьких двухместных машин следует брать подвеску легких мотоциклов, а для больших - подвеску тяжелых мотоциклов. Можно использовать отдельные элементы торсионной подвески коляски мотоциклов М-61 и М-62.
На небольших автомобилях с приводом на одно колесо можно установить подвеску заднего колеса мотороллера ВП-150, у которого силовой агрегат размещен на качающемся рычаге подвески. Заднюю подвеску мотороллера Т-200 можно применить при изготовлении однорычажной независимой подвески с качением рычага в продольной плоскости. Здесь в качестве направляющего устройства будет служить качающаяся вилка, а пружинно-гидравлический амортизатор является одновременно и упругим элементом и узлом, гасящим возникающие колебания.
В автомобилях, у которых вес на заднюю ось будет не более 300 кг, можно ставить подвеску задних колес грузовых мотороллеров МГ-150 и ТГ-200. Упругим элементом подвески мотороллера МГ-150 служат торсионные валы, а возникающие колебания гасятся фрикционными амортизаторами. Независимая же подвеска задних колес мотороллера ТГ-200 пружинного типа состоит из трапециевидных рычагов и спиральных пружин с резиновыми буферами. С каждого конца пружины установлены металлические чашки, служащие для соединения концов пружин с полуосью и рамой.
Расчет подвески автомобиля представляет собой трудную инженерную задачу, которая зачастую решается с помощью электронно-вычислительных машин. Тем не менее в практике выработались некоторые критерии, по которым можно судить в какой-то мере о подвеске построенного автомобиля. По опыту изготовленных конструкций можно сказать, что удовлетворительная плавность хода легковых автомобилей может быть получена, если эффективный прогиб подвески под действием статической нагрузки будет лежать в пределах 150-300 мм при независимой подвеске колес и 80-140 мм при зависимой подвеске колес. Причем, по данным испытаний, у лучших по плавности хода автомобилей передняя подвеска обычно мягче задней.
Самодельные автомобили для малышей, имеющие небольшие скорости движения, можно делать без упругих элементов подвески, так как эластичность шин вполне достаточна для создания необходимой комфортабельности езды на таком автомобиле. Тем более, что используются они в основном на дорожках парка или двора, где поверхность обычно гладкая.
|