2.6. Мероприятия по повышению надежности и эффективности использования СТД
Оценка технического уровня и надежности СТД. Оценка технического уровня технологического оборудования, в том числе средств технического диагностирования, есть комплекс мероприятий, включающий в себя выбор номенклатуры показателей качества, определение их числовых значений и, как результат, определение обобщенного показателя, по которому делают вывод о техническом уровне образцов оборудования. Оценку технического уровня оборудования производят на стадиях его разработки, производства и эксплуатации.
Для получения достоверных данных о техническом уровне используют методику оценки, которая должна отличаться корректностью, необходимой гибкостью, учитывающей отличительные особенности конкретного типа оборудования, и, в то же время, быть достаточно универсальной.
В основу нижеописанной методики оценки технического уровня единиц СТД положен принцип сопоставления совокупности показателей базового и исследуемого образцов. Номенклатуру показателей устанавливают в соответствии с ГОСТ 4.112-84 и делят на основные и частные. Коэффициенты весомости этих показателей оценивают экспертным путем с привлечением специалистов различных организаций.
К числу основных показателей относят назначение, надежность, технологичность, эргономические, эстетические и патентноправовые показатели, уровень стандартизации и унификации и др.
В составе каждого из основных показателей исследуемой единицы оборудования выделяют группу частных. Их устанавливают с учетом специфики использования, конструктивных и технологических особенностей СТД.
Показатели назначения характеризуют степень соответствия оборудования его целевому назначению, отражает конструктивное исполнение и основные размеры, устойчивость к внешним механическим, тепловым и другим воздействиям и т. д. К числу частных показателей могут быть отнесены, например, длительность рабочего цикла, производительность, удельная занимаемая площадь.
Показатели надежности характеризуют степень выполнения оборудованием заданных функций в течение срока службы и в определенных условиях внешней среды с сохранением своих свойств при соблюдении правил хранения, транспортирования и эксплуатации. К числу частных показателей надежности могут быть отнесены, например, ресурс, вероятность безотказной работы, срок службы, ремонтопригодность.
Показатели технологичности характеризуют эффективность конструктивно-технических решений для обеспечения высокой производительности при изготовлении и ремонте автомобиля. К числу частных показателей технологичности относят, например удельную трудоемкость изготовления единицы СТД, коэффициент сборности, удельную материалоемкость.
Удельная трудоемкость изготовления определяется как отношение трудоемкости изготовления единицы оборудования к номинальному значению его главного параметра (например, для тормозного стенда - максимально реализуемая тормозная сила).
Коэффициент сборности Ксб (простота сборки) определяется по формуле Ксб=Е/(Е+Д), где Е - число сборных единиц в СТД, Д - число деталей, являющихся составными частями CT Д.
Удельная материалоемкость определяется как отношение массы единицы СТД к номинальному значению его главного параметра.
Уровень стандартизации и унификации оценивают коэффициентами применяемости Кпр и повторяемости Kп по формулам Кпр=(Nоб-Nо)/Nоб; Кп=NобП, где Nоб - общее число составных частей, входящих в СТД, определяемое по формуле Noб=Nст+Ny+Nо (Nст - число стандартизированных составных частей СТД; Ny - число унифицированных составных частей СТД; Nо - число оригинальных составных частей СТД; П - общее число типоразмеров составных частей единицы СТД).
Эргономические показатели определяются удобством управления и обслуживания, уровнями шума, загазованности, вибрации, надежностью сигнализации и др.
Эстетические показатели определяют рациональность и современность эстетического решения и качество отделки оборудования. К их числу относят функциональность формы (приспособленность формы к выполняемой функции, информационная наглядность), композиционная целостность формы, товарный вид.
Патентно-правовые показатели оценивают уровнем патентной защиты и патентной чистоты.
Как указывалось выше, в основу оценки технического уровня СТД заложен метод сравнения совокупности показателей качества рассматриваемого образца с соответствующими показателями базового образца. В качестве базового обычно используют образцы установившегося производства (отечественные или зарубежные), имеющие с анализируемым образом общность в конструкции, принципе действия, функциональном назначении. При этом базовый образец должен воспроизводить перспективные методы диагностирования и должен относиться к числу современных, срок выпуска которых к моменту оценки не превышает 2-3 лет с начала производства, а в ряде случаев - разработки.
Для оценки технического уровня СТД используют два метода: дифференциальный и комплексный. Дифференциальный метод основан на сравнении образцов по отдельным показателям, причем значение каждого отдельно устанавливаемого качества технического уровня рассчитывается как отношение значений показателей оцениваемого и базового образцов. Если улучшение качества обусловлено увеличением его показателя, используют формулу qi=Pi/Piб, где Pi и Рiб - соответственно значения i-гo показателя оцениваемого и базового образцов. Когда улучшение качества вызвано уменьшением его показателя, используется формула qi=Piб/Pi. Если все значения n оцениваемых показателей качества выше или равны показателям базового образца (qi≥1), то технический уровень оцениваемого СТД выше или равен техническому уровню базового образца. Если часть значений qi≥1, а другая часть qi<1, то применяют комплексный метод оценки.
Комплексный метод оценки технического уровня СТД характеризуется одним обобщающим показателем, который рассчитывается как средневзвешенный по всем единичным показателям (кроме показателей уровня унификации и стандартизации и патентно-правовых). При установлении обобщающего показателя сначала определяют относительные показатели дифференциальным методом qi, а затем проводят расчет относительных групповых показателей с учетом коэффициента весомости j-го частного показателя: Qj=∑nj=1mjqj, где mj - коэффициент весомости j-го частного показателя, n - число показателей.
После расчета значений относительных групповых показателей качества Qj определяют обобщенный показатель Qi с учетом я весомости основного показателя качества: Qi=∑nj=1qimi, где mi - коэффициент весомости i-го основного единичного показателя (определяется экспертным путем), причем сумма коэффициентов весомости всех единичных показателей должна быть равна единице (∑n1mi=1). Если Qi>l, то уровень оцениваемого СТД выше уровня базового, если Qi=l - уровень оцениваемого СТД на уровне мирового, если Qi<1, то уровень оцениваемого СТД ниже уровня базового образца.
Оценка эффективности использования СТД. Особенностью современного этапа технического прогресса на АТП и СТО является интенсификация использования технологического, в том числе диагностического оборудования.
Эффективность использования СТД зависит в первую очередь от приспособленности их конструкции к контрольно-регулировочным работам на автомобиле, от метрологических показателей, степени и рациональности использования в конкретных технологических зонах и технологических процессах.
Большое влияние на эффективность использования СТД оказывает система организации работ на предприятии. Не менее важными являются факторы, определяющие надежность, ремонтопригодность и метрологическую обеспеченность СТД, наличие рациональной планово-предупредительной системы ТО и ремонта оборудования и т. д.
Эффективность использования СТД оценивают показателями, которые классифицируют на основные (оперативные и экономические), дополнительные и метрологические.
К основным показателям относят коэффициент оснащенности предприятия или его отдельной технологической зоны средствами технического диагностирования, коэффициент ис-пользования наличного оборудования, коэффициент технического использования и готовности, коэффициент экстенсивной, интенсивной и интегральной загрузки, коэффициент метрологического обеспечения. Сюда же относят средние трудоемкость и стои-мость диагностирования автомобиля данным СТД.
Коэффициент Косн оснащенности предприятия (или его отдельной технологической зоны) средствами технического диагностирования определяется как отношение фактического числа Пф единиц СТД к числу Пт единиц СТД, предусмотренных "Табелем технологического оборудования и специнструмента для СТО": Косн=Пф/Пт
Коэффициент Кн использования наличных СТД определяют по формуле Кн=Ро/Пф, где Ро - число единиц СТД, действительно используемых на предприятиях.
Коэффициент Кти технического использования для единицы СТД определяют по формуле Kти=tф/(tк-tp-toб-tпoв), где tф - фактически отработанное время на данном СТД за расчетный период наработки; tк - календарное время использования СТД; tр, tоб, tпов - время, затраченное на ремонт, обслуживание и поверку СТД.
Коэффициент Кэкс экстенсивной загрузки СТД, характеризующий степень использования оборудования во времени, определяют по формуле Кэкс=tф/tк, где tф - фактически отработанное время или число машино-заездов на данное СТД за заданный период времени; tк - календарное (или плановое) время или возможное число машинозаездов при заданном фонде рабочего времени Ф(tк=Ф/tср).
Коэффициент Кинт интенсивной загрузки единицы оборудования характеризует отношение фактического объема выполненных работ (услуг в рублях, числе проверенных автомобилей и т. д.) Qф за единицу времени к теоретическому (максимально возможному) или плановому Qвоз, подлежащему выполнению за тот же период времени: Кинт=Qф/Qвоз.
Коэффициент интегральной загрузки Кинтегр=КэксКинт и является обобщающим показателем использования СТД.
Метрологическая обеспеченность определяется коэффициентом Км метрологического обеспечения, который характеризует своевременность проведения плановых периодических поверок (аттестации) оборудования: Км=Nп/N∑ Nп - число поверенных и допущенных к эксплуатации единиц СТД, N∑ - общее число единиц СТД, подлежащих поверке.
К дополнительным критериям относят коэффициент использования полезной площади Кпп металлоемкость, энергоемкость, удобство монтажа, тип исполнения СТД, укомплектованность кадрами, среднее время обслуживания автомобиля при использовании СТД, съем услуг с одного рабочего поста и др.
На практике несколько разнотипных единиц оборудования одного назначения могут сравниваться по коэффициенту Рср: Рср=(Ти+Тэ)/Су где Ти - трудоемкость изготовления оборудования, чел-ч; Тэ - трудоемкость эксплуатации оборудования за заданный промежуток времени, чел.-ч; Су - съем услуг (производительность) с оборудования за тот же период времени. Из нескольких сравниваемых единиц оборудования наиболее эффективно то, которое имеет наименьший коэффициент Рср.
При оценке эффективности использования конкретного СТД не обязательно применять весь комплекс показателей (табл. 2.19). Выбор соответствующей номенклатуры показателей определяется типом оборудования, целью анализа, а также местом его использования в технологических процессах автопредприятия. Допустимо также расширение номенклатуры показателей.
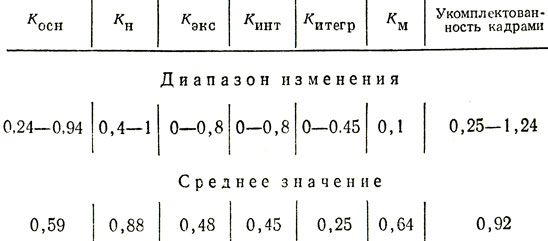 Таблица 2.19. Усредненные значения показателей эффективности использования СТД на СТО системы 'Автотехобслуживание'
На показатели экстенсивной, интенсивной и интегральной загрузки СТД существенно влияет сезонность (результаты соответствующего анализа приведены на рис. 2.57). Их значения еще более разнятся применительно к различным СТД. В целом по комплексу имеющихся на СТО средств технического диагностирования коэффициент экстенсивной загрузки меняется в диапазоне 0-0,8 при среднегодовом значении 0,48. Коэффициент интенсивной загрузки находится в диапазоне 0-0,8 при среднегодовом значении 0,45, Соответственно коэффициент интегральной загрузки находится в диапазоне 0-0,45 (рис. 2.58) при среднегодовом значении 0,25. Выше всех коэффициенты загрузки (использования) стендов для проверки и регулировки углов установки колес автомобилей (среднее значение Кинтегр равно 0,61). Несколько ниже коэффициенты загрузки мотор-тестеров и станков для балансировки колес (Кинтегр=0,24). Меньше всех коэффициенты загрузки стендов для проверки тягово-экономических показателей, тормозных стендов, средств проверки светотехнических приборов автомобилей; среднее значение Кинтегр=0,12.
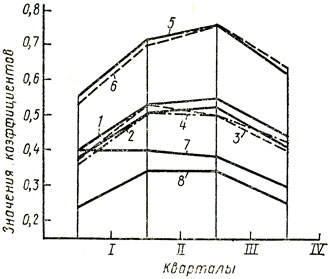 Рис. 2.57. Кривые изменения коэффициентов экстенсивной и интенсивной загрузки СТД в зависимости от квартала года: 1, 3, 5, 7 — коэффициенты экстенсивной загрузки соответственно комплекса СТД, балансировочных станков, стендов для проверки углов установки колес, стендов проверки тормозов, тяговых стендов, приборов проверки фар и т. п.; 2, 4, 6, 8 — то же для коэффициентов интенсивной загрузки
Эффективное использование средств технического диагностирования может быть лишь при условии их метрологической обеспеченности. Среднее значение коэффициента метрологического обеспечения Км СТД составляет 0,64 и варьирует по различным СТО в интервале 0-1,0, т. е, более 35 % из них не могут быть допущены к эксплуатации,
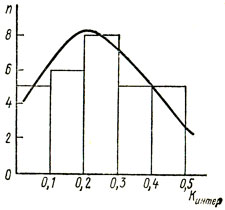 Рис. 2.58, Гистограмма распределения коэффициента интегральной загрузки К интегр комплекса СТД на посту заявочного диагностирования СТО
Система планово-предупредительных технических обслуживании, ремонтов и поверки СТД. Комплексная система планово - предупредительных технических обслуживаний, ремонтов и поверки СТД разработана филиалом НАМИ с участием ряда других организаций и узаконена документом РД-37,009.012-87, который предусматривает мероприятия по организации ТО, ремонтов и поверки СТД на разных стадиях их эксплуатации и хранения; определяет основные требования к СТД при их сдаче и приемке из капитального ремонта; определяет нормативы объемов и периодичность проведения плановых операций ТО, ремонта и поверок, а также типовые средства для выполнения основных операций. Рекомендуемые заводами-изготовителями нормативы (табл. 2.20) являются ориентировочными и предназначены для предварительного планирования сроков проведения ТО и ремонтов СТД.
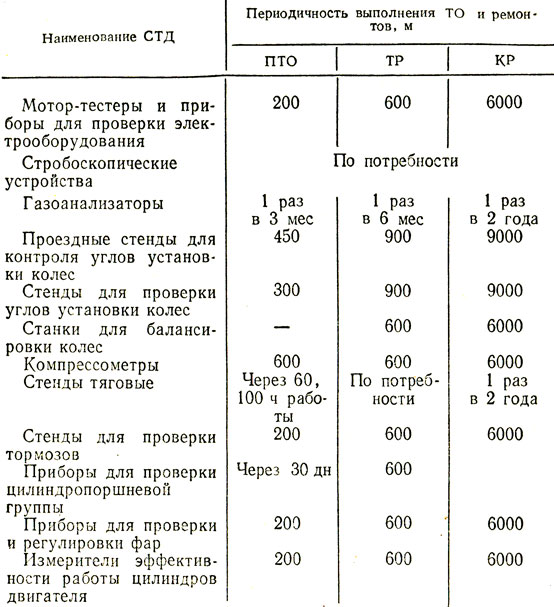 Таблица 2.20. Нормативы периодичности выполнения работ по техническому обслуживанию и ремонту СТД
()
Подсистема технических обслуживаний включает типовые работы, приведенные в соответствующей нормативно-технической документации (НТД) на конкретную модель СТД с установленной периодичностью, а также ежесменное (ежедневное) и периодическое плановое техническое обслуживание. В число типовых работ входят очистка от пыли, регулировочные работы, подтяжка крепежных соединений, смазочные работы и т. п.
При ежедневном техническом обслуживании операторы-диагносты проводят визуальный осмотр и опробование СТД в работе, выполнение несложных регулировочных работ и устранение мелких неисправностей. Ежедневное ТО не должно нарушать графика работы технологической зоны АТП или СТО, где установлено данное СТД.
При периодическом техническом обслуживании (ПТО) проводят углубленную проверку технического состояния СТД, регулировочные и калибровочные (градуировочные) работы, устранение выявленных неисправностей с последующей поверкой (при необходимости) СТД.
Для электронных средств технического диагностирования ПТО включает проверку напряжения источников питания, электрической полярности между цепью питания и корпусом, функционирования отдельных блоков, датчиков и показывающих приборов (индикаторов); калибровку измерительных каналов; выявление и устранение неисправностей и т. д.
Для механических средств технического диагностирования ПТО включает проверку функционирования; оценку герметичности пневмо- и гидроприводов; проверку исправности показывающих приборов; оценку степени изнашивания трущихся сопряжений; крепежные и смазочно-заправочные работы и т. д.
При проведении ТО допускается выполнять различные ремонтные работы, если их суммарный объем не превышает 25 % объема регламентных работ по ТО. В противном случае оформляют заявочный ремонт. Узлы СТД отработавшие регламентный срок (по наработке), заменяют на новые при соответствующем ТО. Выполняют эти работы операторы-диагносты. Для производства более сложных работ по устранению неисправностей привлекают специалистов специализированных служб. Техническое обслуживание СТД производят на местах их использования.
Подсистема ремонтов предусматривает выполнение текущих, средних и капитальных ремонтов.
Текущий ремонт (TP) выполняют для обеспечения или восстановления работоспособности СТД с заменой или восстановлением работоспособности отдельных его элементов и узлов. TP целесообразно совмещать с плановым техническим обслуживанием.
При среднем ремонте выполняют замену или восстановление составных частей ограниченной номенклатуры. Объем работ среднего ремонта составляет 0,3-0,6 объема капитального ремонта.
При капитальном ремонте (KP) заменяют или восстанавливают любые части СТД, включая и базовые. Ресурс капитально отремонтированного СТД должен быть не менее 0,8 ресурса нового.
Текущий ремонт СТД в зависимости от его сложности производят силами ремонтной специализированной службы или специалистами, эксплуатирующими данное СТД, как на местах, так и в специализированных мастерских. Средний и капитальный ремонты СТД производят силами специализированной ремонтноповерочной службы с высоким уровнем организации ремонтных работ в специализированных ремонтных мастерских.
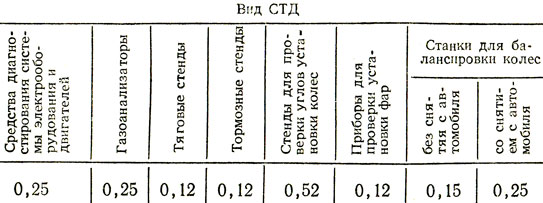 Таблица 2.21. Усредненные среднестатические значения К интегр для предприятий системы «Автотехобслуживание»
Наработку СТД для планирования сроков проведения технических обслуживаний и ремонтов рекомендуется определять по формуле T=NtКcмКинтегр, где N - число рабочих дней в году, t - продолжительность рабочей смены, ч, Ксм - коэффициент сменности использования СТД, Кинтегр - интегральный коэффициент использования СТД. Значение Кинтегр для конкретных условий применения СТД определяют статистическим путем. Усредненные среднестатистические значения Кинтегр (табл. 2.21) в первом приближении применимы и для автотранспортных предприятий. Вместо коэффициента Кинтегр можно использовать коэффициент экстенсивного использования СТД по времени Кэкс. Нормативы трудоемкости и периодичности выполнения ТО и ремонтов применительно к основным СТД приведены в табл. 2.22.
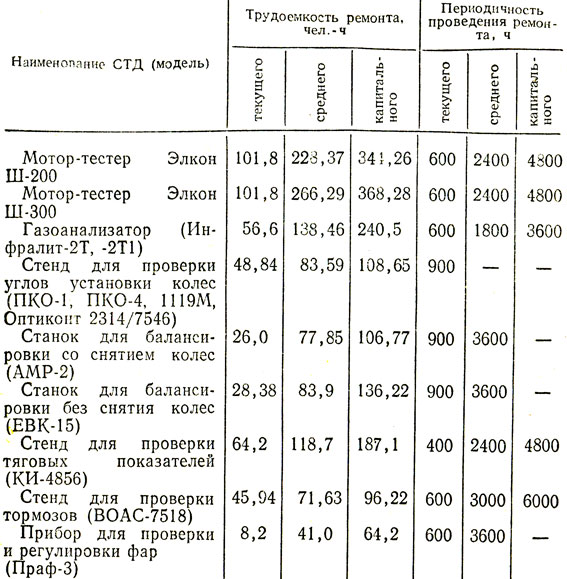 Таблица 2.22. Трудоемкость и периодичность выполнения работ по ремонту основных СТД
Подсистема метрологического обеспечения представляет собой комплекс организационно-технических мероприятий и соответствующей нормативно-технической документации, направленной на повышение эффективности использования СТД, обеспечение требуемой точности и достоверности измерений диагностических параметров и т. д. Составной частью метрологического обеспечения является поверка, которую подразделяют на пять видов:
1. Первичную, осуществляемую при выпуске из производства и при вводе и эксплуатацию у потребителя (по назначению соответствует метрологической аттестации);
2. Периодическую, выполняемую у потребителя согласно графику периодической поверки СТД, утвержденному в установленном порядке и согласованному территориальным органом Госстандарта СССР;
3. Внеочередную, производимую после длительного хранения, при повреждении поверительного клейма и утере документа о поверке и в других случаях;
4. Экспертную, предназначенную для решения спорных вопросов по исправности СТД, пригодности его к применению;
5. Инспекционную, осуществляемую в порядке госнадзора и ведомственного метрологического контроля за состоянием СТД.
Периодичность поверки СТД на предприятиях Минавтопрома определяют с учетом требований РД 37.665.002-85 и рекомендаций действующих" методик поверки на отдельные виды СТД. Нормативы трудоемкости и периодичности поверок СТД приведены в табл. 2.23.
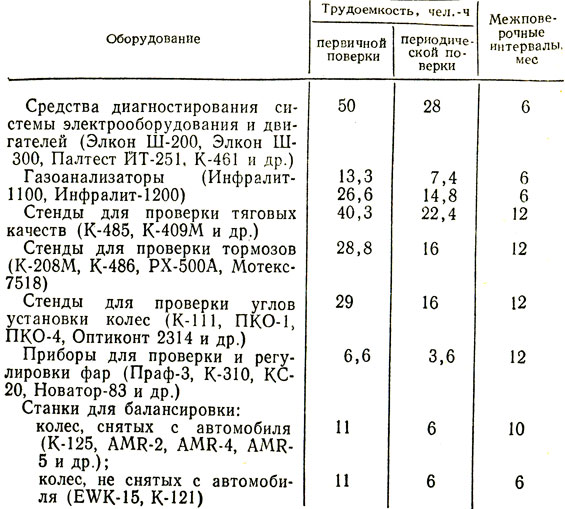 Таблица 2.23. Нормативы трудоемкости и периодичности поверки СТД
Подсистема метрологического обеспечения СТД в условиях их эксплуатации предусматривает наличие ведомственной поверочной службы с соответствующим оборудованием и НТД; планирование работ по метрологическому обслуживанию эксплуатирующихся СТД; подготовку производственного персонала к выполнению технических измерений, поверки, ремонта и наладки СТД; организацию и проведение ведомственного метрологического контроля за состоянием и применением СТД; организацию и проведение метрологической аттестации и поверок СТД; организацию оперативного учета, хранения и ремонта СТД.
В рассматриваемой системе проведения ремонтных работ роль поверки СТД расширяется до функций, подтверждающих необходимость постановки СТД на тот или иной вид ремонта или продления его эксплуатации. Применительно к механическим узлам и некоторым электронным блокам, не влияющим на метрологические характеристики СТД, необходимость проведения ремонтных работ определяют внешним осмотром и проверкой на функционирование (аварийные внезапные отказы чаще всего сюда не относятся), а необходимость ремонта систем, блоков и СТД в целом, техническое состояние которых влияет на метрологические характеристики СТД, обосновывают внешним осмотром, проверкой на функционирование и поверкой.
В результате периодических осмотров (внешний осмотр, проверка на функционирование, поверка) принимают решение о необходимости проведения конкретного вида ремонта (TP, CP, KP) или продления эксплуатации СТД. СТД, прошедшие ремонт и признанные ОТК годными к эксплуатации, поверяют и затем вводят в эксплуатацию. СТД, не относящиеся к средствам измерений или испытательному оборудованию, поверке не подвергают. По результатам осмотра может быть принято решение о необходимости списания СТД.
На ремонты, выполняемые специализированной службой, подают заявку с указанием вида ремонта, вида отказа и внешних признаков его проявления, а также места (технологической зоны) расположения СТД, даты и времени подачи заявки на ремонт. Выполнение ТО и всех видов ремонта оформляют актом или регистрируют в паспорте СТД.
Текущий, средний или капитальный ремонты СТД целесообразно осуществлять в стационарных условиях в специализированных лабораториях (мастерских). В этих лабораториях проводят также послеремонтную поверку СТД после регистрации их в местном органе Госстандарта СССР. Для регистрации лаборатории необходимо иметь соответствующее помещение для работы, оборудованное аттестованными образцовыми мерами, образцовыми и другими приборами; соответствующую нормативно-техническую документацию и штат сотрудников необходимой квалификации.
Регистрация в местном органе Госстандарта СССР осуществляется при наличии следующих документов: письма-отношения предприятия; заявления по форме Госстандарта СССР; приказов по предприятию о создании ведомственной метрологической службы и о назначении ответственного лица за единство мер и измерений по предприятию; положения о метрологической службе; полного перечня мер и приборов по видам проводимых измерений; графика проверки, плана внедрения новой техники, журнала проверяемых средств; схемы передач значений единиц измерений от образцовых до рабочих и измерительных приборов.
Особенностью эксплуатации СТД является необходимость поверки их непосредственно на рабочих местах на АТП и СТО. При этом в ряде случаев совмещают поверку с ремонтными и регулировочными работами. Для этого филиалом НАМИ совместно с другими организациями разработан типоразмерный ряд передвижных поверочных лабораторий на базе легковых и малотоннажных грузовых автомобилей. К ним относят ППЛ-1 и ППЛ-4 II (на базе автомобиля ЕрАЗ-762а), ППЛ-2 (на базе автомобилей ВАЗ-2102 и ВАЗ-2104), ППЛ-3 (на базе автомобиля ИЖ-2715), ПС-4 (на базе автомобиля Авиа-21Ф). Эти лаборатории рассчитаны на передвижение по дорогам 1-4 категорий, имеющим усовершенствованные капитальные или облегченные (гладкие) покрытия. Как правило, лаборатории оснащают исходными образцовыми измерительными приборами (табл. 2.24) и приспособлениями, комплектом запасных частей, инструментов и принадлежностей (ЗИП), материалами для проведения поверок, наладки, а в ряде случаев для выполнения технического обслуживания и ремонта СТД. Лаборатории, осуществляющие ремонт СТД, дополнительно оснащают ремонтной аппаратурой и специальным рабочим местом.
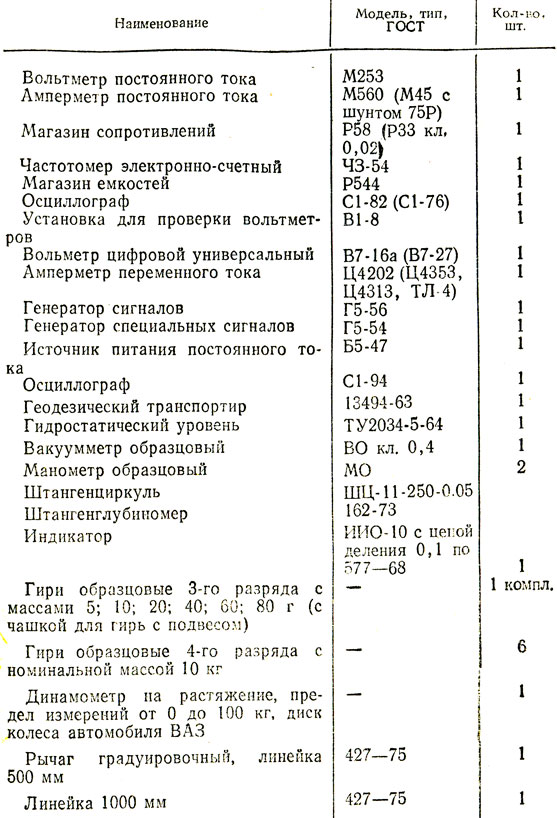 Таблица 2.24. Средства измерений для оснащения передвижных поверочных лабораторий
()
Кузов автомобиля-лаборатории ППЛ-3 (рис. 2.59) дополнительно утеплен и снабжен отопителем и системой вентиляции. Образцовые средства поверки, приспособления и инструмент размещены и закреплены на специальном выдвижном контейнере, перемещающемся по двум направляющим, которые жестко крепятся к полу кузова автомобиля.
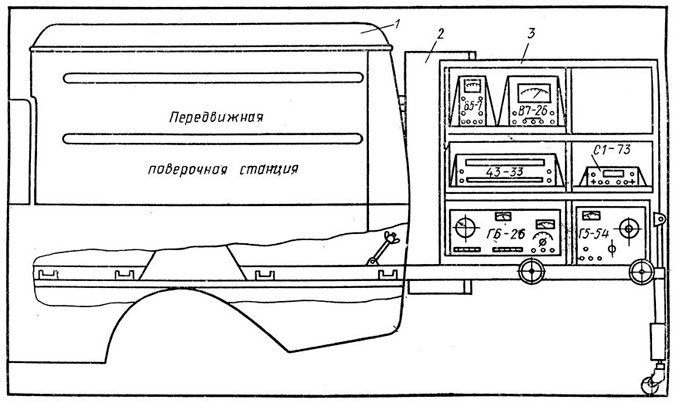 Рис. 2.59. Передвижная лаборатория ППЛ-3: 1 - грузовое отделение, 2 - дверь, 3 - контейнер
В левой стороне контейнера расположены приборы, в правой - отсек с ящиками для инструмента и ЗИП. Контейнер выполнен из стальных труб прямоугольного сечения, разделен на три яруса. В выдвинутом положении контейнер опирается на откидную подставку, регулируемую по высоте. Специальное запорное устройство предохраняет контейнер от самопроизвольного перемещения.
Приборы установлены на специальные амортизаторы, обеспечивающие снижение допустимых нагрузок до 1 g, Длиномерные предметы при транспортировании укладывают на пол кузова и крепят скобами; место укладки оклеено резиной.
Электрооборудование ППЛ-3 состоит из кабеля ввода, электрощита и системы освещения. На лицевую панель электрощита выведены сигнальная лампа, общий выключатель, выключатель освещения рабочего места, розетки для подключения приборов и паяльника, колодка штепсельного разъема, через которую подводится питание от сети 220 В/50 Гц. Длина кабеля для подключения лаборатории к сети освещения СТО имеет длину 30 м.
Наибольшая скорость передвижения ППЛ-3 до 70 км/ч; скорость передвижения при радиусе поворота около 9 м 20-25 км/ч. Рациональный радиус передвижения лаборатории не более 300 км. Время развертывания лаборатории в рабочее положение не превышает 10 мин (без учета времени на прогревание приборов). Габаритные размеры лаборатории в развернутом (рабочем) состоянии 5200X1790X1600 мм, полная масса 1400 кг, масса оборудования 300 кг, Лаборатория обслуживается двумя специалистами.
В комплект лаборатории ППЛ-1 входят серийно выпускаемые приборы, приспособления и их эксплуатационная документация, инструмент, материалы и инвентарь, а также нестандартное оборудование; верстак, стеллаж, подвеска для приборов, ящик-сиденье, подставка для котировочной штанги, электрощит. Базовый автомобиль дополнительно утеплен, снабжен подогревательным устройством и системой вентиляции.
Повышение технологичности ППЛ-1 обеспечивается применением специальной поворачивающейся выносной подвески для установки приборов (рис. 2.60). Она состоит из стойки, крепящейся к полу, консолей с кронштейнами и захватов. Устанавливаемые в захваты приборы (например, частотомер и генератор сигналов) имеют дополнительные амортизаторы.
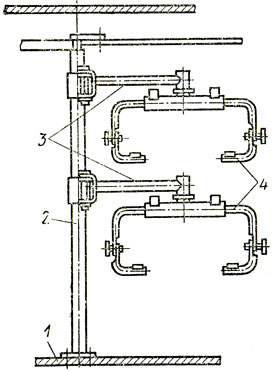 Рис. 2.60. Выносная подвеска для приборов: 1 — пол салона автомобиля, 2 - стойка, 3 — консоли, 4 — захваты для приборов
Питание ППЛ-1 во время проведения поверочных и других работ от наружной сети 220 В, 50 Гц через специально предусмотренный выходной кабель. Естественное освещение в салоне обеспечивается через боковые окна, искусственное - за счет трех потолочных и боковых плафонов и светильника служебного освещения.
Передвижная лаборатория ПС-4 может эксплуатироваться в климатических условиях УХЛ4 по ГОСТ 15150-69. Обслуживают ее два человека (включая водителя).
В кузове автомобиля по левому борту размещена стойка приборов, отопитель и ящик-сиденье, по правому - между проемом боковой двери и задним бортом - шкаф и верстак.
Стойка приборов представляет собой металлическую конструкцию, состоящую из основания, прикрепленного к полу кузова стремянками, и стеллажа для приборов, шарнирно соединенного с основанием четырьмя стойками для изменения положения стеллажа с приборами на верхнее - при транспортировании и работе с обслуживаемыми средствами диагностирования внутри станции и нижнее (опущенное) - при работе с ним вне станции. В последнем случае стеллаж с поверочными приборами перемещают к проему открытой боковой двери.
Для облегчения подъема стеллажа в исходное верхнее положение предусмотрены две пружины, а для исключения его самопроизвольного перемещнеия из верхнего положения в нижнее стойка жестко фиксируется двумя гайками-барашками,
При замене приборов, монтируемых на стеллаже, на аналогичные, но других габаритных размеров, используют кронштейны, которые перемещаются по трубам стеллажа и жестко фиксируются в заданных положениях. Приборы крепятся к кронштейнам через резинометаллические амортизаторы, которые уменьшают амплитуду вибраций до значений, меньших 1 g.
На стеллаже установлены приборы для поверки и наладки практически всех электронных блоков современных средств технического диагностирования автомобилей, а также геодезический транспортир, брусковый и гидростатический уровни, образцовые манометры вакуумметры, штангенциркуль и штангенглубиномер, индикатор часового типа, линейки, эталонные гири, отвес, комплекты инструмента, емкости для смазочных материалов и т. д.
Металлический верстак имеет ящики для хранения документации, малогабаритных контрольно-измерительных и эталонных приборов, инструмента, запасных частей, материалов и др. Чтобы предотвратить самопроизвольное перемещение ящиков во время движения автомобиля, в их днище сделана выштамповка и увеличена высота задних стенок. С правой стороны верстака закреплены тиски, с левой - осциллограф (С 1-82 или С1-76); на верстаке предусмотрено рабочее место для паяльных и ремонтных работ.
На станке перед верстаком установлен перфорированный металлический лист с инструментами, а также панель с розетками для включения осциллографа, паяльника, вентилятора и др. В ящике-сиденье можно хранить крупногабаритное оборудование, материалы, емкости, а в шкафу - одежду и мелкие предметы.
Температура в салоне ПС-4 должна быть не ниже +12 °С при относительной влажности (65±15)%, поэтому стены и потолок кузова дополнительно утеплены плиточным полистирольным пенопластом и отделаны декоративным пластиком; пол покрыт войлоком и резиновым ковриком. Для поддержания рабочей температуры 20-25 °С в салоне рядом с ящиком-сиденьем размещен жидкостный отопитель, аналогичный установленному на легковом автомобиле ВАЗ. Теплоносителем в нем является жидкость из системы охлаждения двигателя. Температурно-влажностный режим в салоне станции регулируется термометром и психрометром, которые прикреплены на борту кузова.
Питание приборов осуществляется от внешней сети напряжением 220 В. Для этого в нижней части основания стойки приборов расположены барабан для сматывания кабеля и распределительный щит, на котором смонтированы понижающий трансформатор 220/12 В, сигнальная лампа включения станции, автомат защиты сети, четыре предохранителя-выключателя и розетки на 12 В. Сверху над распределительным щитом закреплен универсальный стабилизатор напряжения.
Для освещения салона станции предусмотрены три светильника дневного света мощностью по 80 Вт и два светильника, питающихся от бортовой сети автомобиля.
Во время работы заземляющую шину станции подсоединяют к заземляющему контуру СТО или АТП.
После длительного нахождения на открытом воздухе при пониженной температуре станцию необходимо поместить в теплый гараж не менее чем на 12 ч или включить отопитель.
В процессе эксплуатации станция ПС-4 подлежит первичной аттестации а входящие в ее состав приборы - периодической поверке или аттестации.
Специализированные приборы, приведенные в табл. 2.24, совмещают в себе функции имитаторов систем зажигания автомобилей, источников эталонных сигналов и образцовых средств измерений.
Из числа приведенных в таблице приборов наибольший интерес представляет ПП-3, отличающийся расширенными функциональными возможностями и высокими метрологическими характеристиками.
Прибор ПП-3 (рис. 2.61) рассчитан на работу в диапазоне температур +5÷+40 °С и относительной влажности до 80% при температуре +20°С; конструктивно состоит из двух блоков (ПП-3-1 и ПП-3-2).
 Рис. 2.61. Прибор ПП-3 для проверки мотор-тестеров: 1 — измерительный блок, 2 — блок высокого напряжения
Так как рабочие частоты прибора небольшие, то для сокращения времени и повышения точности измерения определяется не частота, а обратная ей величина - период следования импульсов. Для этого в приборе применен не частотомер, а измеритель временных интервалов.
Прибор вырабатывает тактовые импульсы в интервале 3-400 Гц, разбитом на четыре диапазона. Для выбора нужного диапазона и регулирования задаваемой частоты в выбранном диапазоне в приборе предусмотрены три ручки: "Период", "Средне", "Точно".
Прибор имеет два импульсных частотных выхода: меандр с амплитудой 12-13 В и выходным сопротивлением не более 220 Ом; токовый с параметрами, обеспечивающими надежный запуск индукционных датчиков опорного цилиндра.
Скважность импульсов устанавливается с помощью переключателя соответственно значениям угла замкнутого состояния контактов 90, 60, 45, 30 и 0° по шкале 0-90°.
Для проверки вольтметров прибор имеет выход регулируемого постоянного стабилизированного напряжения положительной полярности с выходным сопротивлением не более 1 кОм. Верхняя граница диапазона с помощью переключателя устанавливается равной 20+0,5 или 1+0,1 В; плавное регулирование выходного напряжения осуществляется двумя ручками "Uрег" и "Точно" (рис. 2.62).
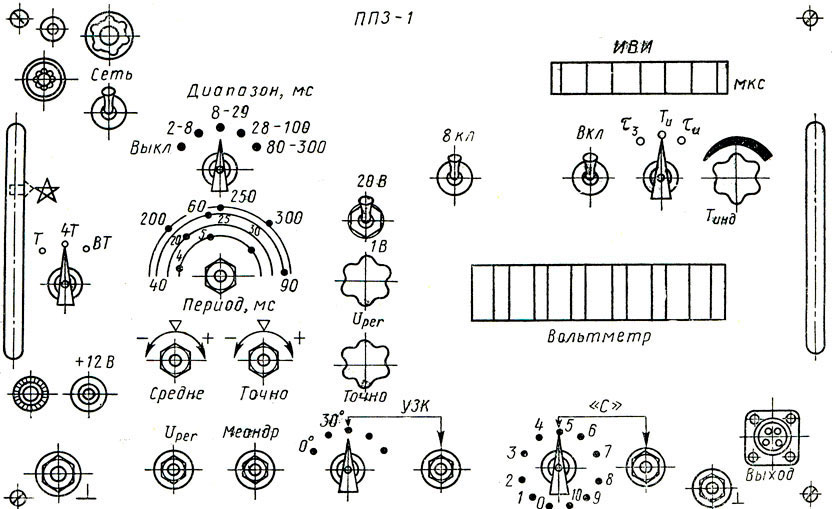 Рис. 2.62. Лицевая панель блока ПП-3-1
Прибор имеет калибровочный конденсатор емкостью 0,22 мкФ для поверки блока измерения емкости конденсатора. Измерение напряжения в приборе осуществляется встроенным 4-разрядным цифровым вольтметром с верхним пределом измерения 20 В и классом точности не ниже 0,5. Относительная приведенная погрешность измерителя Беременных интервалов также не ниже 0,5.
В приборе имеется два генератора (основной и вспомогательный) высокого напряжения, выходные сигналы которых аналогичны импульсам во вторичной цепи системы зажигания автомобиля. Эти генераторы размещены в отдельном корпусе.
Для питания поверяемых переносных приборов, например, СВД-2, ПАС-2, Элкон Ш-320, в ПП-3 имеется выход постоянного напряжения 12-13 В положительной полярности. Напряжение питания прибора 220 В±10 % частотой 50 Гц.
Блок-схема ПП-3-1 (рис. 2.63) состоит из ряда узлов, каждый из которых создает нормированное воздействие, требуемое для поверки того или иного блока мотор-тестера.
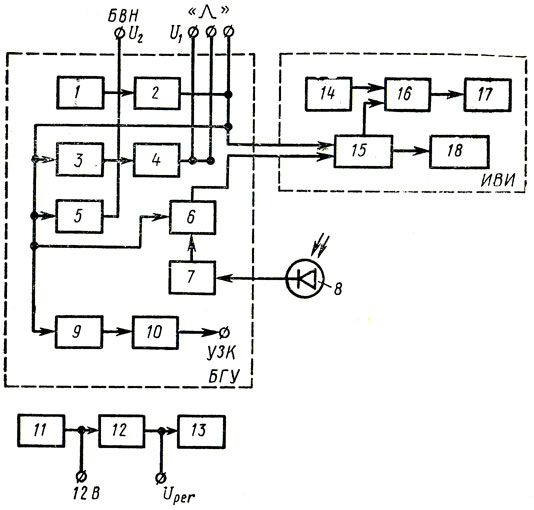 Рис. 2.63. Блок-схема прибора ПП-3-1: 1 — задающий генератор, 2, 3 — делители частоты, 4, 5, 10 — усилители-формирователи. 5 —блок формирования импульсов угла опережения зажигания, 7 — усилитель амплитудного дискриминатора, 8 — светодиод, 9 — блок формирования импульсов угла замкнутого состояния контактов прерывателя, 11 — блок питания, 12 — формирователь регулируемого напряжения, 13 — цифровой вольтметр, 14 — кварцевый генератор, 15—коммутатор рода работ, 16 — счетчик-дешчфратор 17 — индикатор, 18 — блок автоматики, БВН — блок высокого напряжения, БГУ — блок генераторов-усилителей, ИВИ — измеритель временных интервалов
Задающий генератор 1 вырабатывает прямоугольные импульсы с. частотой следования до 800 Гц; частота следования импульсов регулируется в широких пределах ручками: "Период, мс"; "Средне"; "Точно". Сигналы с задающего генератора поступают на делитель частоты, включающий несколько ступеней деления. Первая ступень 2 вырабатывает тактовые импульсы с частотой 117-420 Гц. Выход первой ступени делителя частоты соединен параллельно с входами делителя частоты 3, усилителя-формирователя 5, формирователя импульсов угла замкнутого состояния контактов 9, формирователя угла опережения зажигания 6, коммутатора 15 рода работ и выходом "Меандр". Следующие ступени деления обеспечивает делитель 3 в диапазонах частот: 34-122, 10-36, 3-11 Гц. После прохождения делителей частот импульсы усиливаются и формируются усилителем-формирователем 4 сигнала запуска опорного цилиндра, а затем подаются на выходное гнездо для запуска датчика опорного цилиндра поверяемого мотор-тестера.
На выходе второго блока усиления и формирования формируются импульсы тактовой серии с амплитудой 12 В и длительностью 50 мкс, которые поступают на второй прибор ПП-3-2 - блок высокого напряжения БВН.
Блок 9 формирования импульсов угла замкнутого состояния контактов прерывателя формирует импульсы, скважность которых соответствует углам замкнутого состояния контактов 0; 30; 45; 60; 90°. Выбор угла осуществляется переключателем УЗК, с выхода которого импульсы поступают на усилитель-формирователь и далее на гнездо прибора УЗК.
На второй вход блока 5, формирующего импульсы, длительность которых соответствует углу опережения зажигания, поступают стоп-импульсы с усилителя амплитудного дискриминатора фотоприемника стробоскопа (вынесен на лицевую панель прибора).
Импульсы с выхода делителя частоты 2 и блока 6 формирования импульсов опережения зажигания поступают на коммутатор 15 измерителя временных интервалов ИВИ, который с помощью переключателя рода работы τз, Tи, τи выбирает либо режим длительности τи, либо режим периода Tи импульса; в положении переключателя τи производится самоконтроль схемы. Результаты измерений выдаются на шестиразрядном цифровом индикаторе.
В состав ИВИ входят также кварцевый генератор 14, шестиразрядный счетчик-дешифратор 16 и блок автоматики 18, осуществляющий запуск счетчика, его останов, задание времени индикации и сброс регистра.
Блок питания 11 обеспечивает стабилизированным напряжением (+9, +12, +20 В) схему прибора. Напряжение +20 В подается на формирователь 12 регулируемого напряжения, встроенный цифровой вольтметр 13 и к гнезду Uрег на лицевой панели прибора.
|