Дефектоскопия кузовов
Дефектоскопия кузовов является важной частью технологического процесса ремонта. После удаления старой краски кузов подвергается тщательному контролю с целью отбраковки негодных деталей, подбора годных, определения вида и объема ремонтных работ. Дефектоскопия кузова и его узлов проводится в соответствии с техническими условиями на его ремонт, разработанными для каждого типа автомобилей. От принятого способа дефектации и тщательности ее выполнения в значительной степени зависит качество ремонта.
Дефектоскопия кузова и его деталей организуется на участках общей разборки кузова и на участках его ремонта. Для обнаружения дефектов в корпусе кузова, а также для контроля вновь изготовленных деталей, сварных швов применяют способы неразрушающего метода контроля.
Техническое состояние кузова на авторемонтных заводах обычно проверяют наружным осмотром поверхности деталей невооруженным глазом или с помощью простейших луп многократного увеличения. Обычно для этой цели применяют четырех- или девятикратные бинокулярные лупы. Этот метод позволяет обнаружить поверхностные трещины, коррозионные разъедания, деформации и др. Измерение специальными измерительными инструментами, приспособлениями и шаблонами позволяет обнаружить отклонение геометрических размеров деталей от первоначальных (перекосы, прогибы и др.).
Для выявления трещин и определения плотности посадки сочлененных деталей применяется также метод простукивания деталей, который основан на определении тональности звука при простукивании деталей молотком. По изменению тональности звука можно определить трещины и ослабленные соединения (заклепками, болтами, точечной сваркой и т. п.). Эффективность этого способа зависит от опытности исполнителя.
Однако внешним осмотром можно установить только крупные, заметные на глаз повреждения, например вмятины, нарушенные формы, участки коррозии поверхности, трещины и др. В некоторых местах несущих элементов кузова в результате накопления усталости и значительного упрочнения металла вследствие наклепа, появившегося в процессе повторных ремонтов панелей, появляются волосяные трещины, которые могут быть выявлены специальными способами.
Способы, основанные на молекулярных свойствах жидкости, получили название капиллярные методы (методы проникающих жидкостей), основанные на капиллярном проникновении индикаторных жидкостей в полости поверхностных дефектов и регистрации индикаторного рисунка. Наибольшее распространение получили мелокеросиновый цветной и люминесцентный методы. Керосин, обладая хорошей смачиваемостью и поверхностным натяжением, легко проникает в неплотности.
Сущность этого метода состоит в том, что обследуемое место смачивают керосином и насухо протирают или просушивают струей воздуха. Затем это место покрывают водным раствором мела. При минусовой температуре в раствор добавляют незамерзающий растворитель (0,5 л этилового спирта на 1 л воды). Вследствие впитывания мелом керосина на меловой поверхности появляется жировой след, по которому судят о величине трещины.
При цветном контроле обследуемое место тщательно очищают и обезжиривают бензином, а затем покрывают раствором проникающей красной краски. После выдержки в течение 5-10 мин раствор удаляют с поверхности водой либо с помощью растворителя (в зависимости от применяемых дефектоскопических материалов).
После очистки Поверхности детали на нее путем напыления или мягкой кисточкой наносят слои белой проявляющей смеси. Через 15-20 мин на белом фоне в местах расположения дефектов появляются характерные яркие полоски или пятна. Трещины обнаруживаются в виде тонких линий, степень яркости которых зависит от глубины трещин. Поры проявляются в виде точек различной величины, а межкристаллитная коррозия - в виде тонкой сетки. Очень мелкие дефекты можно наблюдать через лупу или бинокулярный микроскоп. По окончании контроля проявляющую смесь удаляют с поверхности, протирая деталь ветошью, смоченной в растворителе. Деталь просушивают.
Дефектоскопические материалы применяют комплектно. В комплект входят: очищающий состав, индикаторная (проникающая) краска "Д"-М, проявляющая "Д"-В. Они могут находиться в обычной посуде, а также в аэрозольных флаконах.
Проникающие составы могут быть изготовлены из осветительного керосина - 70-80 г, бензина Б-70 - 20-30 г, анилинового красителя или Судана IV - 1-3 г, а проявляющие из (в процентах по массе) белой нитроэмали НЦ-25 - 70 г, разжижителя РДВ - 20 г, цинковых густотертых белил - 10 г.
Методом красок можно выявить трещины шириной от 0,005 мм и глубиной до 0,4 мм. При подогреве детали до 50-80° С можно обнаружить более мелкие трещины.
Поскольку кузова автомобилей, как правило, изготовляются из тонколистовой стали, во избежание выбора неправильного метода ремонта (оставить ли прокоррозированный участок, предварительно удалив с его поверхности продукты коррозии с последующим нанесением антикоррозионного покрытия, или заменить поврежденный участок новым) при дефектоскопии кузова следует определить глубину коррозионного разрушения. Для этой цели лучше всего применять неразрушающие способы дефектоскопии, например с помощью гамма-толщиномера (рис. 34). Этим прибором измеряют толщину листовой стали облицовки кузова, когда доступ к измеряемому объекту имеется лишь с одной стороны. Особых требований к чистоте поверхности при измерении прибором не предъявляется.
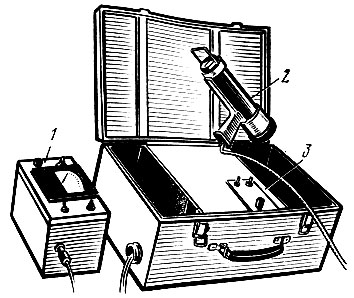 Рис. 34. Гамма-толщиномер: 1 - измерительный блок; 2 - пистолет-датчик; 3 - блок питания
Работа прибора основана на измерении интенсивности гамма- лучей (источником которых является кобальт-60), рассеянных при прохождении в обратном направлении в толще металла. Детектором в приборе служит счетчик с кристаллом йодистого натрия. Импульсы с детектора поступают в усилитель и далее на одноканальный амплитудный анализатор импульсов, к выходу которого подключена интегрирующая схема. Показания отсчитываются на приборе, шкала которого градуирована в миллиметрах.
Прибор позволяет измерять листы толщиной от 0 до 16 мм. Время, необходимое для проведения одного замера, не превышает 30 с. Прибор получает питание от сети переменного тока напряжением 220 В.
Для определения глубины коррозионного разрушения можно использовать также некоторые магнитные измерители толщины немагнитных покрытий на ферромагнитных основах (приборы МИП-10, ВИП-2 и др.).
|