Глава 3. Способы восстановления неметаллических деталей кузовов
Восстановление деревянных деталей кузовов
Деревообделочные работы проводятся при ремонте кабин грузовых автомобилей КрАЗ, деревянных платформ грузовых автомобилей и кузова-фургона, имеющего деревянный каркас.
При ремонте деревянного каркаса кузова поврежденные участки деталей чаще всего приходится восстанавливать наращиванием детали по длине и склеиванием. Негодные детали заменяют новыми. Детали каркаса по длине наращивают в том случае, если повреждение имеет место на одной части детали, а вся остальная часть остается годной к эксплуатации. При наращивании необходимо придерживаться следующих основных правил: наращивать детали силового каркаса, например продольные балки основания, нельзя; наращивать допускается в местах наименьшего изгибающего момента и наименьшей нагрузки; стыки располагать таким образом, чтобы соединение можно было при необходимости усилить дополнительным креплением к основным элементам каркаса; наращиваемая часть должна быть из той же породы дерева, из которой сделана ремонтируемая деталь.
К древесине, применяемой для ремонта и изготовления деталей кузова, предъявляются определенные требования в отношении ее сортамента и физико-механических свойств. На механические свойства древесины влияют: влажность, плотность, возраст, неоднородность строения, место произрастания и различного рода пороки.
Крепость древесины характеризуется ее временным сопротивлением (способность оказывать сопротивление сжатию, растяжению, изгибу, кручению, скалыванию).
С уменьшением влажности крепость древесины увеличивается. В результате исследований ЦНИИМОД установлено, что при влажности древесины до 30% крепость ее остается без изменения, а при дальнейшем высыхании резко повышается, достигая максимума при нулевой влажности.
Основными материалами для деревянных деталей, воспринимающих основные нагрузки в кузовах (навесные и притворные стойки, брусья основания и т;. п.), являются пиломатериалы лиственных пород (чаще всего ясень или бук). Все остальные детали кузовов, а также деревянные детали платформ грузовых автомобилей изготавливают из пиломатериалов хвойных пород (сосна, лиственница).
Первое, весьма важное требование при изготовлении деталей кузовов заключается в том, что древесина должна быть сухой. Влажность древесины, применяемой на изготовление деталей кузовов, обусловливается техническими условиями и не должна превышать 12-15%. Влажность древесины может быть определена весовым методом или при помощи электровлагомера. Электрический способ более быстрый, но менее точный и позволяет определить влажность в диапазоне от 8 до 30%.
Влажность дерева весовым методом определяется на вырезанных из доски образцах размером 2×2×3 см. Образцы взвешивают с точностью до 0,012 г, высушивают и вновь взвешивают. Влажность древесины измеряют в процентах к абсолютно сухой массе (абсолютная влажность) и определяют по формуле
где W - коэффициент абсолютной влажности; Q1 - масса дерева до высушивания; Q2 - масса дерева после высушивания до постоянной массы при температуре 95-105°С.
Высушивание предохраняет древесину от порчи и загнивания, увеличивает срок ее службы, улучшает ее физико-механические свойства, предотвращает коробление и растрескивание, а также улучшает качество склейки. Установлено, что предприятию выгоднее получать сухие доски, прирезанную и подсушенную заготовку, чем сырые доски, так как при этом на предприятии можно не иметь сушильного хозяйства и значительно менее загружать раскройный участок.
Согласно имеющимся установкам предусматривается разделение деревообрабатывающего производства на две стадии: на производство черновых, а в некоторых случаях и чистовых заготовок, деталей на лесопильных заводах и на доработку и сборку этих полуфабрикатов на предприятиях в районах, потребления. Снабжение ремонтных и сборочных предприятий в данном случае происходит в порядке кооперирования этих предприятий с предприятиями первичной обработки. Такой вид снабжения уже довольно широко применяют предприятия автомобилестроения и некоторые авторемонтные заводы. Можно уверенно сказать, что снабжение предприятий сухими и первично обработанными материалами получит преимущественное распространение. Однако, поскольку далеко не все авторемонтные заводы располагают возможностью получить сухой пиломатериал, ниже рассмотрен процесс его сушки.
Сушка древесины. Широкое распространение получила высокотемпературная сушка, основной особенностью которой является наличие избыточного давления внутри древесины, вызванного кипением влаги.
Пиломатериалы сушат при высокотемпературных режимах в среде перегретого пара. При этом температура среды по мокрому термометру при атмосферном давлении равна 100, а по сухому - выше 100°С. В начальный период сушки в камеру поступает насыщенный пар, который прогревает древесину, вытесняет из камеры воздух и одновременно циркулируется вентиляторами через калориферы, где он перегревается. После этого пар испаряет влагу из древесины и смешивается с этими испарениями. Подача пара в камеру прекращается. Смесь циркулируется вентиляторами через калориферы, где повышается степень ее перегрева, затем проходит через штабель и т. д. Излишек пара удаляется через пароотводящую трубу в атмосферу или же в теплообменные установки, в которых исключаются потери тепла.
При сушке древесины с температурой выше 100°С физическая сущность процесса продвижения влаги изменяется. Наряду с потоком влаги, идущим под влиянием градиента влажности, в этом случае большое значение имеет поток влаги, образующийся из-за повышенного давления паровоздушной смеси в древесине, вследствие которого влага из внутренних слоев сортимента интенсивно перемещается на его поверхность. Градиент влажности и перепад давления являются движущей силой для перемещения влаги, но при значительной величине они могут быть причиной появления напряжений и растрескивания материала в процессе сушки.
При сушке пиломатериалов высокотемпературными режимами древесина приобретает повышенную пластичность, поэтому напряжения, вызванные перепадом влажности и давления в древесине при сушке, падают и материал не разрушается. Усушка древесины при высокотемпературных режимах из-за понижения предела гигроскопичности, как правило, меньше, чем при сушке той же древесины при низких температурах в пределах 20°С. При высокой температуре вязкость влаги уменьшается, что облегчает ее продвижение по мельчайшим отверстиям соединительных пор и микрокапилляров.
При применении высокотемпературной сушки древесины должно учитываться требование к ее качеству, которое в значительной степени зависит от применяемого оборудования и режима сушки.
Для высокотемпературной сушки наиболее пригодны камеры, имеющие достаточную герметизацию всех конструктивных элементов, обеспечивающих поддержание высоких температур по смоченному термометру в пределах 100°С. Наиболее герметичны цельнометаллические камеры с двойными стенками. В них пространство между стенками заполняют теплоизоляционным материалом (шлаковата, стекловата), По данным института лесохозяйственных проблем Латвийской ССР сооружение металлических камер, включая их монтаж при одном и том же объеме загружаемых в камеру пиломатериалов, обходится на 20-30% дешевле кирпичных.
Высокотемпературная лесосушильная камера СПВ-62 (рис. 71) конструкции Гипродревпрома - одноштабельная, конвективная, периодического действия, состоит из четырех одинаковых секций, снабженных вентиляторами 2 с индивидуальным приводом 1 и циркуляцией сушильного агента через штабель 5 в поперечном направлении.
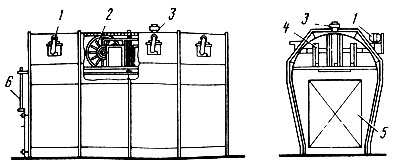 Рис. 71. Высокотемпературная лесосушильная камера СПВ-2
Для притока свежего воздуха и удаления горячей смеси во время охлаждения пиломатериалов после сушки на одной из секций установлены две приточно-вытяжные трубы 3 с дроссельными заслонками. В конструкцию камеры входят также система пароснабжения, тепловое оборудование, система контроля, регулирования и управления процессами сушки.
Для повышения стойкости против тепловых, влажностных и электрических воздействий ответственные части ограждений камер выполняют из технически чистого алюминия, а основное обрудование - из нержавеющей стали. Секция образуется каркасом, герметично обшитым внутри алюминиевыми листами, а снаружи - листовой сталью. Между обшивками укладывают теплоизоляционные маты толщиной 100 мм из стекловолокна. Передняя секция имеет одностворчатую дверь 6, обшитую алюминиевыми листами с обеих сторон. По всему периметру дверь герметизируется прокладкой из термостойкой резины. Для герметизации двери в нижней части рельсы делают откидными.
Конструкция камеры СПВ-62 обеспечивает аэродинамические и тепловые условия для качественной скоростной сушки пиломатериалов в среде перегретого пара или любыми из рекомендуемых руководящими материалами режимами сушки. Корпус камеры в зоне высушиваемого материала трапециевидной формы. Верхняя часть камеры закруглена.
Осевые вентиляторы на поперечных валах, установленные вверху камеры, создают мощную побудительную циркуляцию агента сушки, который, проходя через ряд пластинчатых калориферов 4, обогревается и направляется в штабель. В камере установлено 16 пластинчатых калориферов типа СТД-3009-Б5 с поверхностью нагрева 327 м2.
Периодическое (каждый час) автоматическое переключение направления вращения вентиляторов реверсирует агент сушки, а наклонные стенки камеры обеспечивают равномерное его распределение по высоте штабеля. Вентилятор типа У12 № 10 приводится в действие электродвигателем А02-41-4.
Техническая характеристика камеры СПВ-62
Таблица 5
Режимы высокотемпературной сушки
Режимы сушки. При выборе режима сушки следует руководствоваться следующим. Чем толще сортимент, выше его влажность, строже требования к качеству сушки и т. п., тем мягче должен быть режим сушки, т. е. ниже температура и меньше психрометрическая разность в сушильной камере. На основании исследований МЛТИ, ЦНИИМОДа и других институтов разработаны новые режимы для высокотемпературной сушки пиломатериалов.
Режимы высокотемпературного процесса в камерах периодического действия приведены в табл. 5. Режим, применяемый для сушки пиломатериалов конкретной породы и размера, определяется его номером (от I до VII).
Регламентируемые режимы сушки предусматривают двухступенчатое изменение параметров сушильного агента. С первой ступени режима на вторую переходят при достижении древесиной переходной влажности 20%.
Для пиломатериалов с высокой начальной влажностью (более 60%) допускается в целях сокращения продолжительности процесса повышения переходной влажности до 25%, если контрольными опытными сушками установлено, что при этом обеспечивается сохранение целостности древесины.
Для всех высокотемпературных режимов устанавливают стабильную температуру по мокрому термометру 100°С. Допускается снижение температуры мокрого термометра до 96°С. В этом случае соответственно снижается температура сушильного агента по сухому термометру с сохранением заданной психрометрической Разности.
Режимы сушки пиломатериалов, рекомендуемые ЛатНИИЛХПом, приводятся в табл. 6.
Таблица 6
Режимы сушки различных пород
Штабеля закатывают в камеру и плотно закрывают двери. Затем через пропарочную трубу пускают насыщенный пар из котла. вентилятор в это время работает. Пар пускают в количестве, обеспечивающем повышение температуры с разницей показаний по сухому и мокрому термометрам в 1-2°С. В этот период древесина прогревается. Достижение температуры 100°С должно быть обеспечено исходя из расчета 0,5 на 1 см толщины пиломатериалов. Затем пар подают только в калориферы и постепенно устанавливают необходимую температуру сушки. Продолжительность повышения температуры определяют в зависимости от высушиваемого материала.
При сушке по 1, II, III режимах промежуточная пропарка не требуется. При других режимах ее выполняют при достижении материалом влажности 35%, понижая температуру агента сушки до 100°Си, если необходимо, пуская пар непосредственно в камеру (через пропарочную трубу).
Во время пропарки необходимо следить за тем, чтобы показания температуры по сухому и мокрому термометрам были одинаковыми и приблизительно равнялись 100°С. Продолжительность пропарки устанавливают из расчета 1-1,5 ч на 1 см толщины материала с момента снижения температуры в камере до 100°C. По окончании сушки понижают температуру в камере и выдерживают материал при этой температуре.
Продолжительность конечной обработки пиломатериалов также устанавливают из расчета 1-1,5 ч на 1 см толщины материала с момента снижения температуры в камере до необходимого предела. Древесину охлаждают до 50°С. Во время охлаждения вентиляторная установка продолжает работать и выключается только перед раскрытием дверей камеры для разгрузки.
Склеивание. Для склеивания древесины в ремонтной практике применяют главным образом фенолоформальдегидные клеи и клеющие композиции из резорциновых и фенолорезорциновых смол. Технологический процесс склеивания древесных материалов складывается из следующих основных операций: подготовки материалов к склеиванию; нанесения клея; сборки и запрессовки деталей.
Большое влияние на прочность клеевых соединений оказывает влажность древесины. Это влияние обусловливается двумя факторами: деформацией древесины при изменении ее влажности и ослаблением клеящей способности синтетических смол при нанесении их на влажную древесину. Во всех случаях влажность склеиваемых материалов не должена быть более 18%. В помещениях, где склеивают детали из древесины, необходимо поддерживать влажность воздуха 40-60%. Температура воздуха и заготовок древесных материалов при склеивании синтетическими клеями без нагревания должна быть не ниже 16°С, при склеивании с подогревом температура в помещении должна быть не ниже 8°С.
Поверхность древесины, предназначенная для склеивания, должна быть обработана так, чтобы склеиваемые детали плотно прилегали друг к другу и обеспечивалось получение равномерной по толщине клеевой пленки. В большинстве случаев склеиваемые поверхности простругивают на рейсмусовом станке или прифуговывают вручную.
В зависимости от типа клея и условий склеивания клей нанося на одну или на обе склеиваемые поверхности. Так, фенолоформальдегидные клеи, легко впитывающиеся в древесину, обычно наносят на обе поверхности (исключение составляют ясень и дуб). Клей наносят с помощью щетинных и лубяных кистей с длиной ворса 1,5-2,5 см. Ширина кистей должна соответствовать ширине склеиваемых деталей. Кисть должна двигаться только в одну сторону. После нанесения клея дается открытая выдержка, продолжительность которой для фенольных клеев типа ВИАМ Б-3 составляет 4-15 мин. Продолжительность открытой выдержки зависит от температуры воздуха в помещении: чем выше температура, тем выдержка должна быть короче. По окончании открытой выдержки собирают детали и выдерживают под давлением в течение определенного времени при нормальной или повышенной температуре в зависимости от типа клея. Продолжительность выдержки склеиваемых деталей под давлением зависит от скорости отверждения клея, температуры воздуха и склеиваемых деталей, а также от породы соединяемых материалов. Минимальная продолжительность выдержки плоских деталей из древесных материалов под давлением при склеивании фенолоформальдегидными клеями типа ВИАМ Б-3 без нагревания составляет: при 16-20°С - 5 ч, при 21-25°С - 4 ч, при 26-30°С - 3 ч. После окончания склеивания осуществляется свободная выдержка при температуре не ниже 16°С.
При склеивании фенольными клеями деталей из древесины хвойных пород давление должно составлять 2-3 кгс/см2, из древесины лиственных пород (ясень, дуб и др.) - 3-4 кгс/см2. Давление создается с помощью различных переносных зажимных приспособлений и прессов с винтовыми или клиновыми зажимами. К числу стационарных относятся пневматические и гидравлические прессы.
Для ускорения процесса склеивания древесины обычно применяют нагревание. При использовании фенолоформальдегидных клеев температура склеивания должна быть 50-60°С. Повышение температуры должно происходить постепенно.
Детали при склеивании нагревают различными способами. На авторемонтных заводах применяют нагревание при помощи инфракрасных лучей. Основными преимуществами этого способа являются: экономичность; высокая скорость; малая инерционность (при включении установки прогрев начинается практически мгновенно); простота регулирования температуры нагревания, в частности, путем регулирования напряжения в электросети; простота и невысокая стоимость оборудования; малая площадь для размещения нагревательных установок; простота эксплуатации и невысокие эксплуатационные расходы.
Изготовление ремонтных деталей. Технологический процесс изготовления деревянных деталей кузова состоит из ряда последовательных этапов, включая механическую обработку.
Механическая обработка древесных материалов на станках обычно начинается с раскроя, т. е. разрезания досок, брусков на отрезки определенных размеров. Такие заготовки называют черновыми. Процесс дальнейшей механической обработки имеет две характерные стадии. Первая стадия заключается в остругивании черновых заготовок с четырех сторон и отторцовке для придания им правильной геометрической формы и точных размеров. Полученные таким образом заготовки в отличие от черновых называют чистовыми. Вторая стадия механической обработки заключается в превращении чистой заготовки в готовую деталь, заданную чертежами изделия, в нарезании на чистовых заготовках шипов и проушин, в сверлении отверстий, выборке гнезд и т. д. Для деталей клеевых (склеенных из нескольких пластин) в процессе превращения черновой заготовки в деталь прибавится еще одна стадия - склеивание.
До постановки на кузов или до крепления металлической облицовки деревянные детали каркаса, как и металлические, должны быть прогрунтованы.
Преобладающим видом механической обработки на авторемонтных заводах является резание со снятием стружки способами пиления, строгания, фрезерования, долбления, сверления. Силу резания определяют по формуле
где k - удельное сопротивление резания (определяется опытным путем и составляет для древесины от 0,5 до 10-15 кгс/см2);
b и h - соответственно ширина и толщина стружки, мм.
При резании вращающимися резцами среднюю окружную силу резания Рср находят из зависимости
Выражение представляет собой объем материала, снятого в течение секунды, где s - скорость подачи, м/мин (в данном случае скорость подачи равна скорости резания); v - скорость резания, м/с. Частота вращения инструментов определяется возможностями станка и видов обработки.
|