|
Глава 1. Исследование, расчет и прогнозирование надежности механических систем
1.1. Методы испытаний на надежность
Ресурсные испытания подразделяют на группы [35]. Первую группу составляют испытания, связанные с созданием и доводкой новой конструкции, а также модернизацией серийных машин. К ним относят доводочные, предварительные и приемочные испытания. Вторая группа - это контрольные испытания, цель которых состоит в проверке соответствия серийной продукции требованиям технических условий, например заданному уровню надежности. Третью группу составляют исследовательские испытания, охватывающие все сферы экспериментального изучения свойств изделий и факторов, влияющих на надежность. Кроме того, некоторые исследователи полагают, что эксплуатацию изделий потребителем, являющуюся по-существу важнейшим источником информации о надежности, следует отнести к четвертой группе ресурсных испытаний.
Один из вариантов укрупненной классификации ресурсных испытаний, их объекты и виды приведены на рис. 1.1. К эксплуатационным относятся испытания объекта, проводимые в процессе его эксплуатации (ГОСТ 16504-81). Они могут быть трех видов: опытные, осуществляемые квалифицированным персоналом при регулярном контроле специалистами; подконтрольные, сопровождаемые контролем состояния каждого изделия специально подготовленным персоналом; рядовые, проводимые потребителем с возможными отклонениями от правил использования и обслуживания. К нормальным относят испытания по продолжительности проведения соответствующие эксплуатационным, к сокращенным - проводимые по сокращенной программе.
Указанные на рис, 1.1 виды повреждений должны быть дополнены разрушительными процессами, характерными для механических систем, такими, как коррозия, ползучесть, старение.
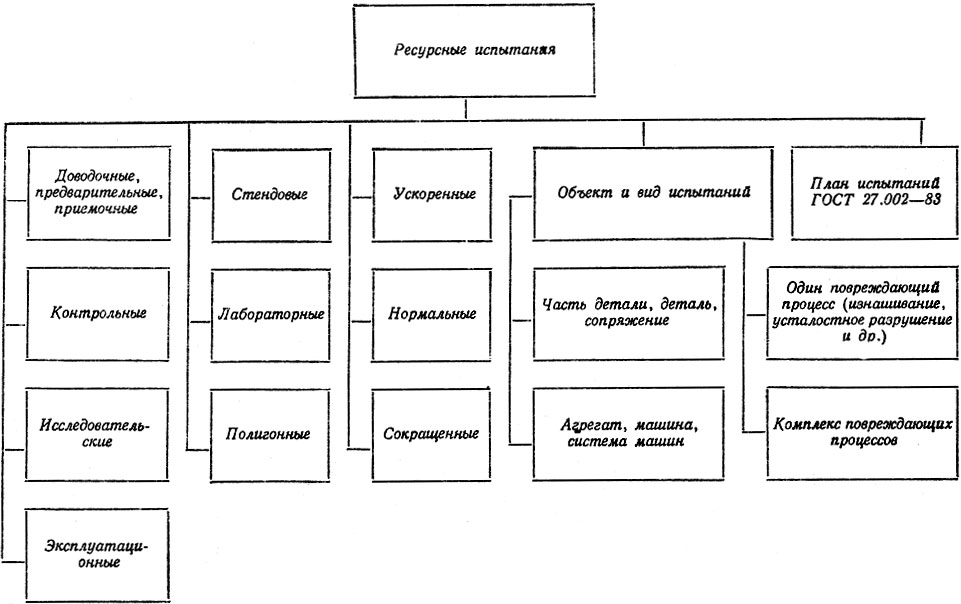 Рис. 1.1. Классификация, объекты и виды ресурсных испытаний
![Таблица 1.2. Коэффициенты ускорения стендовых ресурсных испытаний деталей н агрегатов грузовых автомобилей [35]](pic/000002.jpg) Таблица 1.2. Коэффициенты ускорения стендовых ресурсных испытаний деталей н агрегатов грузовых автомобилей [35]
Каждой группе ресурсных испытаний соответствует свой набор классификационных признаков. Например, исследовательские испытания - определение предела усталости (повреждающее воздействие) детали (объект испытаний) - обычно проводятся на стендах (способ проведения), ускоренно (темп проведения), до поломки части или всех деталей опытной партии (план испытаний).
Как правило, стендовые и полигонные испытания являются ускоренными и при их проведении необходимую информацию о надежности изделий получают в более короткие сроки, чем при нормальных испытаниях. Для оценки темпа ускоренных испытаний используют коэффициенты ускорения по наработке Ку.н = Lэ/Lи и по времени Ку.в = Тэ/Ти, где Lэ, Lи - соответственно наработки при эксплуатации и испытаниях; Тэ, Ти - соответственно календарная продолжительность работы при эксплуатации и испытаниях.
В табл. 1.1, 1.2 приведены коэффициенты ускорения при стендовых и полигонных испытаниях деталей и агрегатов грузовых автомобилей. Из них следует, что сокращение сроков доводки, повышение надежности проектируемых автомобилей невозможны без дальнейшего развития и совершенствования стендовых и полигонных испытаний. Подробно вопросы организации ресурсных испытаний изложены в работах [35, 58, 80].
![Таблица 1.2. Средние коэффициенты ускорения полигонных испытаний грузовых автомобилей [58]](pic/000003.jpg) Таблица 1.2. Средние коэффициенты ускорения полигонных испытаний грузовых автомобилей [58]
Эксплуатационная надежность
Систематическое изучение эксплуатационной надежности автомобилей началось после создания в стране экспериментально-производственных автохозяйств (ЭПАХ), опорных автотранспортных предприятий (ОАТП) и базовых автотранспортных предприятий (БАТП) [24, 49, 52]. В указанных авто предприятиях сбор информации об эксплуатационной надежности осуществляется в результате наблюдений за подконтрольными партиями автомобилей различных лет выпуска. При этом фиксируются не только отказы и неисправности, различные виды воздействия (техническое обслуживание, текущие ремонты), но и условия эксплуатации автомобилей: перевозимые грузы, длины ездок, виды дорог, средние скорости движения и т. д.
Основными результатами исследований по оценке эксплуатационной надежности являются: определение основных показателей эксплуатационной надежности; классификация отказов деталей, узлов и агрегатов автомобиля; выявление типовых отказов элементов и установление возможных причин их возникновения; выявление деталей "критических" по надежности (или "лимитирующих" надежность); определение параметров и видов законов распределения ресурсов деталей; выявление связи эксплуатационной надежности с технико-экономическими показателями работы автомобилей.
Основные показатели эксплуатационной надежности автомобилей (без показателей, относящихся к транспортировке и хранению) приведены в табл. 1.3. Из 25 показателей 17 относятся к показателям долговечности (в соответствии с ГОСТ 27.002-83) и 2 - к безотказности (наработка на отказ). Остальные могут быть отнесены к комплексным.
Некоторые показатели могут быть определены лишь по результатам соответствующих исследований на ремонтных предприятиях (ремонтируемая или не ремонтируемая деталь, удельная стоимость капитальных ремонтов). Ряд показателей зависит от наработки автомобиля с начала эксплуатации (наработка на отказ, удельная трудоемкость и стоимость).
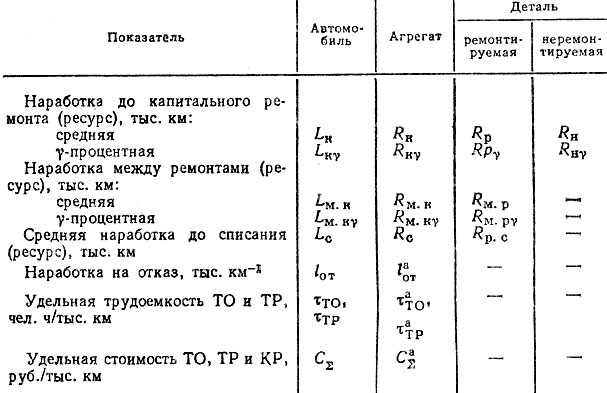 Таблица 1.3. Основные показатели эксплуатационной надежности автомобилей
Анализ табл. 1.3 позволяет сделать следующие выводы: при проектировании число показателей долговечности и безотказности деталей, агрегатов и автомобиля целесообразно ограничить основными показателями эксплуатационной надежности;
поскольку периодичность, трудоемкость и стоимость ТО определяются по результатам опытной эксплуатации серийных машин, то при проектировании они могут быть выбраны по аналогии с существующими моделями или определены с учетом прогнозных оценок с последующей корректировкой;
затраты на запасные части, на текущий и капитальный ремонт также принимаются по аналогии с существующими конструкциями на основании прейскурантов, ценников, нормативных материалов или с использованием методов прогнозирования.
При рассмотрении вопросов оценки надежности большое внимание уделяется классификации отказов [34]. Не останавливаясь подробно на всех аспектах классификации, отметим, что по внешним признакам проявления отказов для грузового автомобиля грузоподъемностью 8 т на пробеге 100 тыс. км износы составляют 40%, пластические деформации и разрушения - 20%, усталостные разрушения - 18%, температурные разрушения - 12% [37 L Аналогичные соотношения наблюдаются и для автобуса среднего класса" Распределение отказов деталей автомобиля грузоподъемностью 4 т следующее [33]: износ - 53%, разрушение (трещины, поломки, обрывы) - 19%, деформации (растяжение, скручивание, изгиб) - 10%, другие виды дефектов - 18% [33]. Обобщение ряда исследований показало, что в среднем по автомобилю отказы, связанные с износом, составляют около 50%, различные виды усталостных и прочностных разрушений (деформаций) - 35 %, на отказы, вызванные коррозией, кавитаций, прогоранием, закоксовыванием, короблением и др. причинами, приходится 15%. Таким образом, из большого числа разрушающих процессов, приводящих к отказу деталей, главное внимание необходимо уделить развитию вероятностных методов оценки ресурса, связанных с износом, усталостью и статической прочностью.
Если взять "средний" грузовой автомобиль, то относительное распределение общего числа отказов на пробеге до первого капитального ремонта будет следующим: двигатель - 25%* трансмиссия - 23%, подвеска - 10%, тормозная система - 13%, электрооборудование - 10%, рулевой механизм -5%, передний мост -3%, прочие узлы и агрегаты - 11%, Следует отметить, что для различных моделей автомобилей относительное распределение отказов по одинаковым агрегатам различно, что косвенно указывает на определяющую роль условий эксплуатации.
Анализ данных эксплуатационной надежности автомобилей показывает, что у каждой модели в определенных условиях эксплуатации при фиксированной наработке имеется ограниченное число деталей, которые чаще других выходят из строя, что определяет материальные и трудовые затраты на поддержание автомобиля в работоспособном состоянии. Такие детали получили название "лимитирующих" надежность, или "критических" по надежности [751. В работе [65] указывается, что из 15-18 тыс. деталей, из которых состоит автомобиль среднего класса, 3-4 тыс. имеют сроки службы меньше, чем автомобиль, но только 400 деталей являются критическими по надежности.
Выявление деталей, лимитирующих надежность, имеет принципиальное значение с точки зрения совершенствования методов расчета надежности, так как это позволяет сократить объем вычислений при проектировании примерно в 10 раз.
В настоящее время отсутствует общепринятая методика определения деталей, лимитирующих надежность (ДЛН). Так, в работе [25] для этих целей используется метод комплексного анализа безотказности, долговечности и ремонтопригодности (табл. 1.4). В этой же таблице приведены результаты расчетов по методике, согласно которой ДЛН определяются в виде единого стоимостного критерия, включающего стоимость детали, затраты на ремонт и другие затраты [491.?
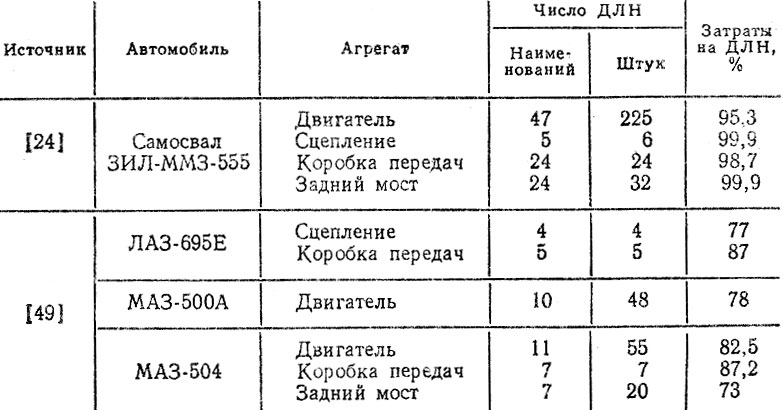 Таблица 1.4. Сравнительная оценка методик определения ДЛН
Обработка данных об отказах и неисправностях автомобилей представляющих собой случайные величины, производится статистическими методами [8-10, 12, 14]. Наиболее часто для описания наработок (ресурсов) деталей и агрегатов автомобиля используются законы распределения: Вейбулла, логарифмически нормальный, экспоненциальный, Рэлея Так, по данным [24] наработки деталей до отказа в 60% случаев подчинились закону Вейбулла, в 35% случаев - нормальному. В общем случае для аналитического описания наработок (ресурсов) деталей и агрегатов должны использоваться законы распределения для положительных случайных величин [12, 77]. Систематизированные данные о параметрах наработок (ресурсов) могут быть использованы для прогнозирования ресурсов или проектирования и для сравнения с результатами расчетов,
Обработка результатов наблюдений за эксплуатационной надежностью автомобилей как в ЭПАХ, ОАТП, так и в рядовых АТП показала, что в зависимости от пробега с начала эксплуатации увеличивается не только число отказов, но и трудовые затраты и затраты, связанные с поддержанием автомобилей в работоспособном состоянии; одновременно происходит уменьшение коэффициентов технической готовности и выпуска, снижаются годовые пробеги и производительность (рис. 1.2). Очевидно, выявленные эмпирические закономерности влияния надежности на эффективность использования автомобиля требуют соответствующего теоретического обоснования и разработки комплекса методик, позволяющих производить расчеты показателей надежности при проектировании.
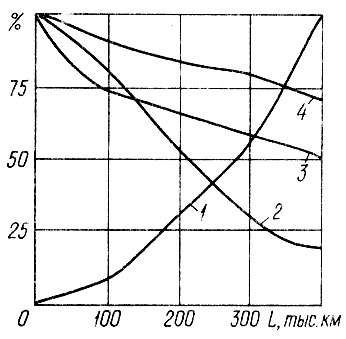 Рис. 1.2. Зависимости накопленных затрат на запасные части (1), наработки на отказ (2), среднегодового пробега (3) и коэффициента технической готовности (4) от пробега с начала эксплуатации грузового автомобиля
Опыт ресурсных испытаний, исследования эксплуатационной надежности и полученные результаты можно рассматривать как основу для совершенствования методов расчета надежности автомобилей при проектировании.
|
|