3. Вагонный парк промышленного транспорта
Основной тенденцией в развитии вагонного парка промышленного транспорта в зарубежных странах является стремление максимально приспособить подвижной состав к условиям перевозки различного рода грузов с целью улучшить использование грузоподъемности вагонов и резко снизить затраты на погрузочно-разгрузочные операции.
Это приводит к более узкой специализации вагонного парка и созданию новых типов промышленных вагонов большой грузоподъемности и вместимости. так, например, в Англии на металлургическом заводе фирмы John Summers используется 30 различных типов вагонов [83]. Грузоподъемность одного вагона достигает 250-300 т. В Швеции создан новый вагон для перевозки жидкого чугуна грузоподъемностью 320 т [84]; в ФРГ построен составной вагон, грузоподъемность которого достигает 400-450 т в зависимости от рода груза [85] и др.
Для обеспечения механизированной разгрузки различных грузов большое распространение получают вагоны с подвижными крышами, раскрывающимися боковыми стенами и трехстворчатыми дверьми в торцовых стенах, опрокидывающимися бункерами, устройствами для пневматической разгрузки сыпучих грузов и др.
На промышленном транспорте используются не только специальные промышленные вагоны, но и вагоны магистральных железных дорог. Парк магистральных дорог все более специализируется и приспосабливается к нуждам промышленности. При этом в ряде стран большая часть специальных вагонов принадлежит промышленным, компаниям и сдается в аренду железным дорогам. так, в США общий парк специальных вагонов, принадлежащих компаниям, достигает 300 тыс., что составляет 17% общего количества вагонов, эксплуатируемых на сети железных дорог США [86]. Б Японии 31% специальных вагонов железных дорог принадлежит частным предприятиям и лицам.
такой порядок выгоден не только железным дорогам, но и промышленным компаниям, так как он обеспечивает перевозки грузов в наиболее приспособленном подвижном составе не только на внутризаводских и подъездных путях, но и на путях магистральных железных дорог.
Рассмотрим новые типы промышленных вагонов для перевозки навалочных и сыпучих грузов.
В США для перевозки сыпучих грузов (цемента, муки, извести, крахмала и др.) используется новый хоппер грузоподъемностью 142 т и емкостью 100 м3 с пневматической системой разгрузки. Разгрузка хоппера производится в бункера или автоцистерны при подаче сжатого воздуха во внутрь хоппера [87]. Скорость разгрузки колеблется от 50 до 190 т/чв зависимости от диаметра разгрузочного шланга и мощности системы, подающей воздух в хоппер. Система разгрузки работает при давлении 1 кг/см2. Воздух обеспечивает текучесть груза.
Для перевозки битуминозного угля с шахт на электростанцию фирмой Bethlekem Steel созданы металлические полувагоны грузоподъемностью 100 т с наклонными торцовыми стенками [88]. Основные технические характеристики вагона: тара 28 576 кг, внутренняя длина 13 716 мм, высота над головкой рельса 3658 мм. Загрузка вагонор осуществляется из бункера с кнопочным управлением, под которым вагоны перемещаются со скоростью 0,10-0,15 м/сек. Подача угля в бункер производится из штабеля ленточным конвейером. Один вагон загружается за 2 мин.
Заводом South Louisville выпущены хопперы грузоподъемностью 100 т для перевозок угля. Система разгрузки хопперов позволяет освобождать кузов от угля в движении или на стоянке посредством ручного привода или автоматического управления со станционного пульта [89].
В результате тщательного прочностного анализа конструкции подобраны соответствующие марки стали для изготовления отдельных узлов. При этом вес тары хоппера составил 28,5 т, т. е. на 3,8 т меньше веса тары стандартной конструкции, выполненной из малоуглеродистой стали. Использование высокопрочных сталей дало возможность исключить из конструкции рамы вагона тяжелую хребтовую балку, которая заменена двумя облегченными продольными балками.
Все части конструкции, соприкасающиеся с грузом и подверженные интенсивной коррозии, выполнены из стали Сог-теп. Эта сталь использована для изготовления стоек боковых стен кузова.
Длина хоппера по концевым балкам рамы 15 700 мм, база вагона 11 700 мм, внутренняя длина кузова 15 200 мм, внутренняя ширина 3000 мм, высота от уровня головок рельсов 4050 мм, полный объем кузова при заполнении до верхних обвязок 102 м3, при заполнении с 250-мм шапкой 113 м3.
Электрический привод обеспечивает надежное и плотное запирание разгрузочных люков, а также открывание их за 6,4 сек, освобождение кузова без использования средств разгрузки и разрыхления за 12 сек, закрывание и замыкание люков за 7,4 сек. Питание к электродвигателю подводится по междувагонному соединению или через розетку на боковой стене. Для открывания и закрывания 16 люков хоппера применяется трехфазный электродвигатель мощностью 10 л. с, напряжение тока 440 в, частота 60 гц. Двигатель смонтирован на раме в 1330 мм от оси шкворневой балки на одном конце вагона.
В ФРГ фирма Krupp изготовляет четырех- и восьмиосные думпкары (для колеи 1435 мм) емкостью 90 м3 и грузоподъемностью 160-200 т; причем емкость можно увеличить да 135 мг, грузоподъемность до 260 т [90].
Подобный вид саморазгружающихся вагонов имеет ряд, модификаций. У вагона с односторонним опрокидыванием, после освобождения запорного устройства процесс гравитационного опорожнения кузова осуществляется за короткий промежуток времени. такой вагон используется главным образом для перевозки влажных и липких материалов. Восьмиосный вагон этого типа имеет емкость кузова 100 м3, грузоподъемность 200 т, собственный вес 60 т. Приведение опрокинутого кузова в нормальное положение осуществляется автоматически после опорожнения. такие вагоны в большинстве случаев используются на определенных участках, например, между экскаватором и бункерной или дробильной установкой, имея постоянное место разгрузки с устройством для принудительного опрокидывания.
Во Франции для внутризаводского транспорта выпускаются вагоны-бункеры с двусторонней боковой разгрузкой [91]. Вагон состоит из четырехколесного шасси с базой 10 м (рис. 6). На раме при помощи листовых рессор установлеа открытый бункер емкостью 40 м3 или закрытый емкостью. 38 м3. Боковые стенки бункера наклонены под углом 43-50°. Длина бункера 8 м, ширина отверстия открытого бункера 1,95 м, закрытого 1,2 м. В нижней части бункера с обеих сторон имеются отверстия размером 1500 X 420 для разгрузки. Грузоподъемность бункеров 28-29 т.
В ГДР на вагоностроительном заводе в Бауцене в 1963 г. начато серийное производство четырехосного вагона для вывозки золы с тепловых электростанций, а также для обслуживания крупных предприятий горной и химической промышленности [92]. Вагон оборудован тремя самоопрокидывающимися цельносварными бункерами емкостью по 11,1 м3. Опрокидывание на угол 50° осуществляется четырехступенчатыми телескопическими гидроподъемниками, работающими: от шестеренчатых насосов с расходом 16 л/мин, которые развивают давление до 160 атм. Управление работой гидросистем производится при помощи командного выключателя, расположенного на раме вагона. В случае выхода из строя привода насосов гидросистема может работать от ручного насоса.
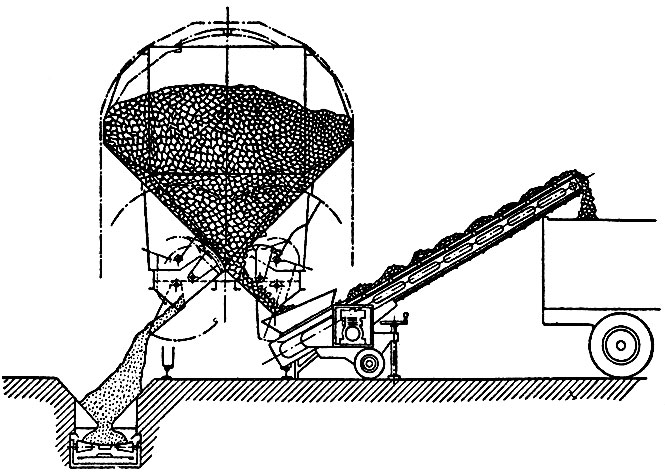 Рис. 6. Вагон-бункер с боковой разгрузкой (Франция)
Большое количество специализированных вагонов используется на металлургических заводах для транспортирования так называемых «горячих грузов».
В ФРГ для перевозки жидкого металла и шлака используются вагоны с ковшами, установленными на раме [90]. Ковши своими цапфами подвешиваются на двух опорах, что уменьшает воздействие высокой температуры на ходовые части вагона. Четырехосный вагон имеет ковш емкостью 11 м3. Ковши с внутренней стороны футерованы шамотным кирпичом. Если ковш изготовлен из гематитового чугуна, футеровка не требуется. Опрокидывание ковша для выгрузки металла производится на любую сторону от ручного или электрического привода через червячную передачу на зубчатый венец, надетый на цапфы ковша. При опрокидывании происходит смещение ковша в сторону опрокидывания, чем предотвращается попадание расплавленного металла или шлака на железнодорожный путь.
Второй вагон такого же типа грузоподъемностью 230 т имеет котел внешним диаметром 3175 мм. Вес вагона 170 т, количество осей 12, длина 23 500 мм.
Вагоны аналогичного типа выпускаются в США компанией Treedwell.
На внутризаводском транспорте металлургических заводов в ФРГ эксплуатируются вагоны специальных типов: для перевозки руды грузоподъемностью 100 т с боковыми люками; кокса - с кузовом повышенных размеров вместимостью 70 м3 и грузоподъемностью 36 т; горячей окалины с температурой до 150° - с кузовом, выполненным из стали, имеющим вместимость 52 м3, грузоподъемностью 70 т и собственным весом 25 т; «горячих» грузов - с кузовом, представляющим собой съемную ванну с внутренней изоляцией огнеупорными материалами и др.
За последнее время в целях снижения веса тары в США начали строить полувагоны и хопперы с алюминиевыми кузовами.
так, фирма Pullman-Standard в 1960-1961 гг. поставила 750 таких полувагонов грузоподъемностью 90 т, фирма Major - 515 хопперов, в том числе 455 крытых и 60 с кузовами цилиндрической формы и т. д.
Эксплуатационные преимущества этих вагонов характеризуются тем, что 100-т вагон-хоппер из алюминия вмещает 76,3 м3 цемента и 102 м3 угля, а из стали соответственно 65 и 77,9 м3.
Алюминиевый крытый полувагон, построенный фирмой Harway Aluminium на базе рамы платформы длиной 25 900 мм, имеет кузов из алюминия емкостью 97,4 м3, длиной 24 480 мм, шириной 2510 мм и высотой 1500 мм. торцовые стенки кузова усилены балками двутаврового сечения и соединены с боковыми стенками и рамой стальными заклепками. Все соединения алюминиевых частей кузова между собой предварительно промазаны специальной пастой.
Вес алюминиевого кузова 4,54 т, что примерно в три раза меньше веса аналогичного стального кузова. Общий вес вагона 34,4 т при грузоподъемности 59 т, что на 8 т больше грузоподъемности стального вагона.
Одной из отличительных особенностей вагона является наличие съемной крыши, выполненной также из алюминия. Крыша состоит из четырех секций длиной по 6096 мм. Ее снятие и постановка осуществляются краном за 10-15 мин. Закрепление крыши производится при помощи установленных на боковых стенках кузова скоб с защелками [93].
В СССР за 1958-1965 гг. общий парк вагонов на промышленном транспорте возрос на 8-10%. При этом, в связи с увеличением выпуска вагонов повышенной грузоподъемности парк четырех-и шестиосных вагонов увеличился с 47 до 64%, а средняя грузоподъемность одного вагона с 33 до 42 т.
За это время заводы освоили серийный выпуск ряда новых специальных вагонов для промышленного транспорта.
Если до 1958 г. для открытых горных разработок в основном выпускались четырехосные думпкары грузоподъемностью 50 т, то в последние годы выпускаются четырех-и шестиосные думпкары и полувагоны грузоподъемностью 60-100 т.
Для внутризаводского транспорта металлургических заводов в настоящее время серийно выпускаются: четырехосный хоппер грузоподъемностью 50 т для перевозки горячего агломерата, четырехосная платформа грузоподъемностью 90 т для перевозки горячих грузов (чушкового чугуна и др.).
В процессе освоения находится восьмиосный саморазгружающийся вагон грузоподъемностью 115 т для перевозки горячего агломерата.
Однако выпускаемые промышленные вагоны ни по числу типов, ни по своим характеристикам не удовлетворяют потребности важнейших отраслей промышленности в специальном подвижном составе. так, металлургическая промышленность испытывает недостаток в специальных платформах для перевозки горячих грузов; для открытых горных разработок необходимы думпкары большей грузоподъемности и вместимости; учитывая зарубежный опыт, необходимо применение для вагоностроения более прочных материалов и др.
На основе научных исследований, проведенных в Промтрансниипроекте, ЦНИИ МПС, ВНИИВ и в ряде отраслевых институтов, разработаны типы основных промышленных вагонов, в соответствии с которым вагоностроительные заводы нашей страны в ближайшие годы должны освоить серийный выпуск следующих типов вагонов.
Хопперы: четырехосные для перевозки кокса грузоподъемностью 45 т с нагрузкой на ось 21 т; крытый хоппер для апатитового концентрата и фосфоритной муки грузоподъемностью 63 т; четырехосный хоппер для руды, доломита и других шихтовых грузов грузоподъемностью 90 т с нагрузкой на ось 30 т.
Полувагоны: шестиосные угольные грузоподъемностью по 90 т с седлообразным полом и люками в полу, грузоподъемностью 140 т с седлообразным полом для перевозки шихтовых грузов; с глухим полом грузоподъемностью 135 т для перевозки металлической шихты, скрапа и лома.
Платформы восьмиосные: грузоподъемностью 130 т для перевозки горячего чушкового чугуна и слитков; безбортная грузоподъемностью 180 т для горячих грузов; платформа-термос грузоподъемностью 170 т и др.
Особенно большая потребность в более совершенных промышленных вагонах возникает на открытых горных разработках в связи с большим ростом железнодорожных перевозок в угольных и рудных карьерах. Если в предстоящем пятилетии 1966-1970 гг. общий объем перевозок в целом на железнодорожном транспорте возрастает на 25%, то на открытых разработках он увеличивается в 1,5 раза.
Для обеспечения этих перевозок всего будет выпускаться 10 типов четырех-, шести- и восьмиосных думпкаров грузоподъемностью от 50-60 до 180 т с односторонней и двухсторонней разгрузкой как с откидными, так и с подъемными бортами.
В их числе будет освоено производство шестиосного думпкара грузоподъемностью 100 т с обмоторенными осями.
В качестве разгрузочных устройств в хопперах, полувагонах и думпкарах предусматривается использование механических, пневматических и электрогидравлических систем с применением дистанционного управления разгрузкой.
Представляет интерес электрогидравлическая система разгрузки, имеющая большие преимущества по сравнению с другими системами. На Калининградском вагоностроительном заводе сооружается поезд, состоящий из пяти шестиосных думпкаров грузоподъемностью 105 т каждый [94]. Система состоит из мотор-насосной установки на локомотиве и гидросистемы.
Рабочая жидкость от насоса нагнетается в разгрузочные цилиндры, установленные на раме каждого думпкара, по два с каждой стороны. Цилиндры осуществляют поворот кузова думпкара на 45е (опрокидывание). Мотор-насосная установка на локомотиве состоит из двигателя постоянного тока, поршневого насоса, масляного бака и гидропроводки.
Управление разгрузкой производится дистанционно из кабины локомотива при помощи электрической системы. Продолжительность разгрузки одного думпкара 80 сек, максимальное давление 160 атм. Думпкарным поездом может управлять один человек.
Электрогидравлическая система имеет преимущество по сравнению с пневматической: она снижает вес тары, увеличивает устойчивость думпкаров при разгрузке за счет сближения осей поворота кузова.
При сооружении новых типов промышленных вагонов должен быть учтен опыт зарубежных стран, особенно в области применения материалов высокой прочности и приспособления подвижного состава для механизации и автоматизации погрузочно-разгрузочных работ.
Кроме того, необходимо учесть опыт создания за рубежом промышленных вагонов с корытообразным кузовом для перевозки тестообразных грузов, вагона с раздвигающейся крышей для перевозки моторов, оборудования, думпкара с вибрационной установкой для разгрузки смерзшихся грузов и другие типы вагонов.
|