Глава III. Вопросы экономической эффективности механизации и автоматизации погрузочно-разгрузочных работ на промышленном транспорте
Важнейшим из общих вопросов механизации и автоматизации погрузочно-разгрузочных работ на промышленном транспорте является повышение экономической эффективности этих процессов.
Получение наибольшей экономической эффективности погрузочно-разгрузочных машин и механизмов во многом зависит от правильного определения сфер рационального применения тех или иных машин. Например, выполненные ВНИИПтМаш работы [43] для определения сферы наиболее рационального применения отдельных погрузочно-разгрузочных машин на машиностроительных заводах показали, что электропогрузчики являются одним из наиболее универсальных средств механизации погрузочно-разгрузочных и транспортных работ на складах и в цехах.
При высоте складов не более 4-5 м применение электропогрузчиков более эффективно, чем кранов-штабелеров.
На внутрицеховых и межцеховых перевозках, на расстоянии до 150-300 м и грузообороте до 30-70 тыс. т в год применять электропогрузчики более целесообразно, чем подвесные толкающие конвейеры и автотягачи.
Краны-штабелеры являются эффективным средством механизации подъемно-транспортных работ на складах. Оборудование складов кранами-штабелерами целесообразно при стесненности территории завода.
Применение таких кранов вместо электропогрузчиков позволяет увеличить примерно в 2 раза высоту склада, уменьшить на 30% проезды и тем самым сократить площадь склада в 2-2,3 раза.
В результате проведенного исследования выявлены наиболее перспективные типы машин для машиностроительных заводов:
- электропогрузчики грузоподъемностью 0,5-1,0; 2,0; 3,2 и 5 т, высота подъема груза 1,8; 2,8 - 4,5 м;
- краны-штабелеры грузоподъемностью 0,2; 0,3; 0,5; 0,8; 1,25; 2,0; 3,2 и 5 т.
Варианты применения тех или иных машин сравнивались путем сопоставления удельных капитальных затрат и эксплуатационных расходов при нормативном сроке окупаемости дополнительных затрат в 4 года.
Исследования, проведенные некоторыми фирмами в ФРГ [44], показали, что применение погрузчиков наиболее эффективно, когда примерно 70% времени они затрачивают на погрузочно-разгрузочные работы и 30% на транспортировку при дальности 100-200 м.
Критерием при выборе типа погрузчика применяется себестоимость, отнесенная к единице времени или тонне переработанного груза.
Установлено, что себестоимость, отнесенная к единице времени, составляет при односменной работе для дизельного погрузчика 2,95 ед., для аккумуляторного 2,73 ед.; для бензинного погрузчика 3,71 ед.
Стоимость одного погрузчика грузоподъемностью до 3,5 т примерно соответствует расходам на содержание одного рабочего. При принятых сроках службы 8-10 лет погрузчик многократно себя оправдывает, высвобождая 8-10 человек.
Важным для повышения экономичности является также вопрос правильного определения параметров погрузочно-разгрузочных машин [45].
Интересные исследования в этом отношении произведены в ЧССР [46], где утверждены следующие основные параметры типового оборудования механизации промышленного транспорта и складов.
Бесприводные транспортные средства
Грузоподъемность, кг 80-160-320-400-630-800-1000-1250-1600-2000-2500-3200-4000-6300;
Ручные тележки
Максимальная грузоподъемность, кг 160-320-630-1250
Длина, мм 900-1300-1800
Ширина, мм 700-900-1300
Погрузочная площадь, м2 0,63; 1,17; 2,34
Прицепные тележки
Грузоподъемность, кг 630-1250-2500-6300
Длина,мм 1300-1800-2700
Ширина, мм 900-1300-1800
Погрузочная площадь, м2 1,17-2,34-4,86
Ручные вилочные погрузчики
Грузоподъемность, кг 320-630-1250
Длина вилочного захвата, мм 550-1600
Высота подъема, мм 120-1600
Вес, кг 50-70-100-110-150
Автопогрузчики
Грузоподъемность, кг 400-630-800-1000-1250-1600-2500-3200-4000-6300
Длина вилочного захвата, мм 800-1100
Высота-подъема, мм 140-1600-2500-3200 мм
Скорость-подъема, (м/сек) 0,16, 0,20, 0,26, 0,35
Скорость движения км/ч
без - груза 5-10-15-25
с грузом 4-9-15-25
Собственный вес, кг 600-650-750-800-850-1450-1700-2000-2450-2500-2800-4000-4500-5500-6000-7500-8000
Краны-штабелеры
Грузоподъемность, кг 1250-2500-4000
Скорость подъема, м/сек 0,20-0,26, 0,35
Скорость движения, км/ч 15
Вес, кг 4500
Скорость применяемых тягачей, км/ч
без груза 12-25
с грузом 10-25
В 1966 г. в ЧССР начнется производство усовершенствованного автопогрузчика грузоподъемностью 5000 кг с высотой подъема вилочного захвата 3500-4200 мм и скоростью 25 км/ч. В перспективе намечается выпуск автопогрузчиков грузоподъемностью 12 000 кг [47].
При выборе внутрискладского штабелера [48] следует учитывать такие факторы, как преодолеваемое расстояние, род груза, высота потолка, ширина проезжей части и возможная высота штабелирования. Особое внимание уделяется способности маневрирования машин в узких проходах. Как показал опыт некоторых английских фирм, при весе груза более 1 т эффективность использования штабелера снижается независимо от дальности рейсов. Штабелеры могут иметь различные виды сменного рабочего оборудования, в том числе безблочную крановую стрелу, захват с прижимом, подъемную грузовую платформу вместо обычного захвата, поворотную грузовую каретку и другие. Фирма Andredson Atlas, Ltd (Англия) выпускает 15 моделей стандартных погрузчиков-штабелеров грузоподъемностью от 300 до 1150 кг при удалении центра тяжести груза от спинки захвата на расстояние 38-66 см. Высота подъема груза 2-5,4 м. Одна из моделей имеет подъемный механизм с электрогидравлическим приводом, питаемым от сети переменного тока. В приводе применен электродвигатель в пламезащитном исполнении. Другая модель, оборудованная высокопрочными пневматическими шинами и телескопическим грузоподъемником, предназначается для использования на открытых складах с неровным покрытием.
Штабелер модели Dumbo, выпущенный фирмой A. L. Marshall Carlson, Ltd имеет грузоподъемность 100 или 200 кг. Предельная высота подъема соответственно 5,6 и 4,2 м.
На основании анализа опытных данных в ПНР выработаны рекомендации по выбору вилочных тележек и штабелеров конструкции со следующими основными техническими данными [49] (табл. 2).
Аналогичные исследования экономических параметров машин ведутся и в других странах. В США, например, [50] разработаны рекомендации по соотношению параметров экскаваторов и обслуживающих их автомобилей. Рекомендуется емкость кузова автомобилей принимать равной 4-5-кратной емкости ковша экскаватора. Практически считается приемлемым коэффициент использования по времени 0,8. Для исключения простоев экскаваторов вследствие выхода из строя транспортных машин необходимо предусматривать резервный парк последних. Экономические расчеты показывают, что численность этого парка должна составлять 20-25% общего количества автомобилей.
При выборе наиболее экономичного способа переработки материалов на складах необходимо учитывать сроки хранения и ассортимента грузов.
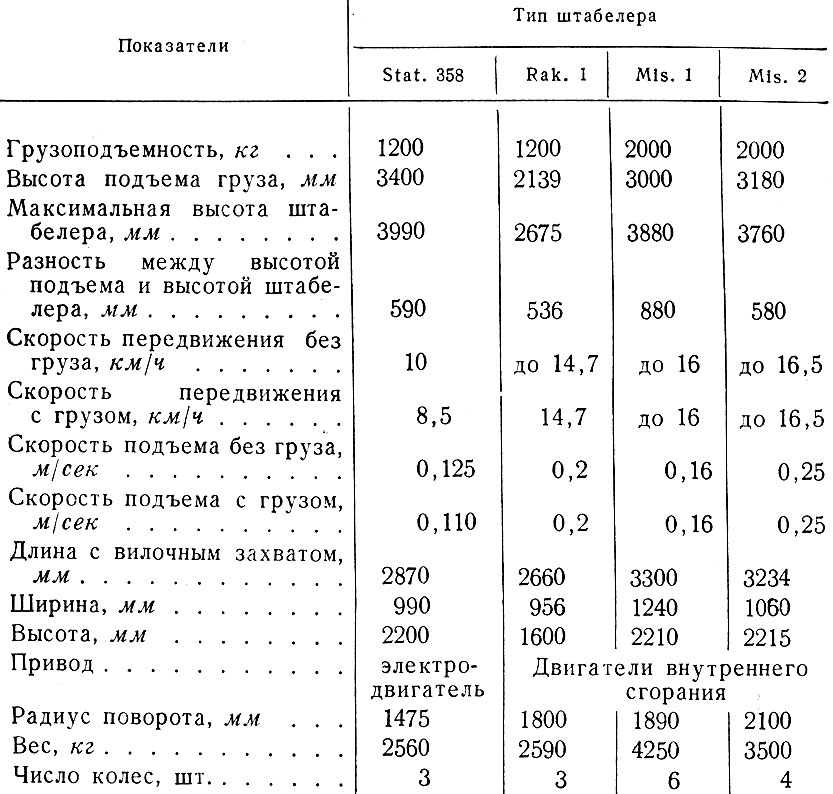 таблица 2
В ФРГ [51] на складах металлургических предприятий в виду большого ассортимента и краткосрочности хранения широко используются мостовые погружатели с пролетом 60 м в комплексе с ленточными конвейерами. Обычная высота штабелей 10 м. Загрузка конвейеров ведется через бункер, укрепленный на одной из опор моста.
В угольных складах тепловых электростанций срабатывание штабелей производится портальными роторно-ковшовыми погрузчиками с поворотной стрелой вылетом 28 м. Погрузчик перемещается по рельсовому пути, проложенному по продольной оси склада. Два штабеля шириной у основания 34 м каждый располагаются по обе стороны рельсового пути.
Когда срабатывание штабелей производится с большими интервалами, используются фронтальные ковшовые погрузчики на пневмоколесном ходу в комплексе с передвижными бункерами на внешней стороне обоих штабелей для загрузки конвейеров. С точки зрения капитальных затрат это наиболее выгодная схема. Определение экономичности того или иного варианта рекомендуется производить простым сравнением соответствующих показателей для мостового погружателя, роторно-ковшового и фронтально ковшового погрузчика.
При среднем темпе работы 45 циклов в 1 ч производительность перегружателя 450 т/ч . Удельный расход мощности на 1 т груза составит 0,5 квт х ч, срок службы 30 лет при односменной и 20 лет при трехсменной работе.
Производительность роторного погрузчика 530 т/ч , остальные показатели те же.
У фронтально-ковшового погрузчика темп 60 циклов, емкость ковша 2 м3, производительность 300 т/ч , стоимость погрузчика списывается за 12 тыс. ч (4 года при односменной и 2 года - при трехсменной работе.)
Как показывает опыт, эффективность применения того или иного способа выполнения погрузочно-разгрузочных работ зависит не только от параметров, механизмов, но, в первую очередь, от объема работы. По исследованиям, опубликованным в ПНР [52], применение экскаватора более эффективно при объеме работы > 60 тыс. м3 в год, а использование погрузчика эффективно при объемах работы 40 тыс. м3.
Во Франции предложена специальная формула для подсчета объема автоматизированных складов, учитывающая основные факторы объема и условий работы склада [53].
где - производительность, выраженная в среднегодовом количестве предметов каждого типа;
К - вес каждой складируемой единицы, кг;
δ - плотность каждой складируемой единицы;
W - число недель складирования;
D - динамичный фактор, учитывающий неравномерность производительности - находится в пределах 1,09 до 2,8;
G - коэффициент, учитывающий мертвое пространство, занимаемое стенами и другими объектами - от 1,08 до 2,8;
и - объем применяемых на складе подъемно-транспортных машин;
faфактор, учитывающий "и" в функции от применяемых методов работы;
с - число, показывающее используемую часть недельного ресурса времени;
о - часовая производительность подъемно-транспортных машин;
fi - факторы, учитывающие основные условия складирования;
f1 - фактор формы складируемой единицы - от 1 до 40;
f2 - фактор упаковки- от 1,07 до 10;
f3 - фактор контейнеризации - 1,07 до 3,2;
f4 - факторы разворотов - 1,15-3,2;
f5 - фактор выхода из разворота 1,12-3,4;
f6 - фактор величины разворота - 1,1;
f7 - фактор, учитывающий остальные условия -1,1.
Имеются и другие методики определения эффективности использования погрузочно-разгрузочных машин [54].
Институтом транспортной техники ГДР разработана методика сравнительного анализа внутризаводского транспорта, позволяющая определить относительные затраты ручного труда и на этой основе разработать планы механизации наиболее тяжелых и трудоемких работ.
В основу анализа положен показатель степени механизации внутризаводского транспорта, называемый коэффициентом механизации, который представляет собой количество рабочих часов, выработанных на внутризаводском транспорте с применением машин, к общему количеству рабочих часов на этом транспорте.
При этом учитывается выработка не только персонала транспортно-складских систем, но и основного и вспомогательного персонала, занятого на выполнении всевозможных погрузочно-разгрузочных и транспортных операций.
Подсчитанные затраты времени показываются не в абсолютных цифрах, а в виде условного числа рабочих единиц при полной занятости исходя из нормативного задания 1920 рабочих часов за год, или 160 рабочих часов за месяц.
Для сопоставимости коэффициентов механизации необходимо, чтобы в них учитывалась неодинаковость затрат ручного труда (различие в трудоемкости) при эксплуатации различных машин. Исходя из этого произведена разбивка транспортного персонала на шесть групп по степени затрат ручного труда и его тяжести и для каждой группы определен свой коэффициент механизации.
Всесоюзным научно-исследовательским и проектно-конст-рукторским институтом подъемно-транспортного машиностроения (ВНИИПтМаш) предложена единая методика определения состояния и эффективности механизации погрузочно-разгрузочных и подъемно-транспортных работ [55].
Важность этой работы определяется тем, что трудоемкость погрузочно-транспортных работ достигает в машиностроении до 40% общей трудоемкости, а затраты на транспортирование материалов в отдельных отраслях промышленности составляют 25-40% всех издержек производства.
В методике дается единая терминология в области ПтР и устанавливается система показателей, отражающих процесс внедрения комплексной механизации.
Предусматриваются три простейших показателя: 1) уровень механизации; 2) степень механизации и 3) расчетная выработка.
Предлагается для анализа действующих схем механизации система коэффициентов, в том числе коэффициент механизации, коэффициент переработки грузов в пределах схемы, показатель сложности механизации, коэффициент использования машин.
Вводятся показатели экономической эффективности механизации, в том числе себестоимость переработки грузов, удельные капитальные затраты, срок окупаемости, рост производительности труда, удельная производительность.
Предлагаемая методика может служить основой для разработки:
1) направления развития отрасли подъемно-транспортного машиностроения и выявления потребности в оборудовании;
2) типовых решений механизации грузопотоков;
3) единой системы показателей учета состояния механизации;
4) отраслевых методик определения состояния механизации.
Стремление улучшить использование погрузочно-разгрузочных машин, ликвидировать их непроизводительные простои приводит к созданию в ряде стран новых форм эксплуатации машин, в частности, концентрация их в прокатных организациях.
В Англии [56], например, существует несколько видов проката транспортного оборудования: краткосрочный, долгосрочный или контрактная сдача (с полным обслуживанием или без обслуживания).
Для этого используются различные погрузчики подъемной силой от 0,9 до 8 т с высотой подъема до 6,5 м.
Краткосрочный прокат используется в основном предприятиями, имеющими собственные средства для ликвидации временных перегрузок последних.
Система эксплуатации погрузочно-разгрузочных машин путем сосредоточения их в специализированных прокатных организациях является одним из методов повышения экономичности механизации погрузочно-разгрузочных работ.
|