Глава VII. Содержание и ремонт погрузочно-разгрузочных машин и устройств
Повышение уровня механизации погрузочно-разгрузочных работ, снижение затрат на эти работы во многом зависит от качества содержания и ремонта погрузочно-разгрузочных машин, улучшения организации ремонта и проведения соответствующих мер по увеличению сроков службы машин.
За последние годы в СССР [118] все более широко внедряется агрегатный метод ремонта машин, когда восстановление работоспособности машин осуществляется путем замены в процессе ремонта изношенных узлов. Это относится главным образом к машинам, собираемым из унифицированных узлов (редукторы, муфты, блоки и пр.).
В настоящее время начал применяться более прогрессивный метод ремонта машин, получивший название планово-предупредительной замены узлов (ППЗУ). Этот способ ремонта наиболее эффективен в тех случаях, когда используется большое число однотипных машин.
Сущность ремонта по системе ППЗУ состоит в периодическом обновлении некоторых агрегатов машины в процессе эксплуатации без длительных ее остановок. Обновление производится за счет централизованного снабжения или изготовления на местах новых узлов и запасных частей, а также в результате реставрации узлов, ранее снятых с машин.
Замена каждого из узлов производится по срокам такого износа этого узла, когда его дальнейшее использование становится экономически и технически нецелесообразным.
Опыт показал возможность и эффективность применения планово-предупредительной замены узлов при ремонте погрузочно-разгрузочных машин, в частности, козловых кранов. Конструкция козловых кранов имеет пять независимо действующих агрегатов: тельфер, две ведущие и две ведомые тележки механизма передвижения.
Важнейшим вопросом организации ремонта является правильное и своевременное комплектование оборотного фонда агрегатов и узлов.
Организация планово-предупредительного ремонта подъемно-транспортных машин применяется и в других странах.
На одном из крупных предприятий химической промышленности ГДР (119] на внутризаводском транспорте работают 300 кранов, 100 подъемников, 160 электротельферов, 100 электролебедок, 100 вилочных погрузчиков и 1000 простых механизмов. Для производства всех видов ремонта, включая капитальный, создана центральная мастерская, в которой работают 14 инженеров и мастеров-бригадиров и 100 рабочих. Персонал разбит примерно поровну на три группы. Две группы работают непосредственно на производственных участках, причем каждая из них состоит из бригад электриков и слесарей. третья группа работает на территории мастерских; в нее входят электрики, слесари, станочники, сварщики и другие рабочие.
Предусматриваются два вида технического осмотра: простейший, при котором проверяются только важные части и узлы, а остальные подвергаются поверхностному осмотру, и средний, при котором проверке подвергаются все части и узлы. Обнаруженные дефекты и неисправности по каждой машине и механизму заносятся в дефектную ведомость с указанием исполнителей (по категориям) и трудозатрат в часах. Эти данные используются для подсчета выработки и оплаты по повременно премиальной системе.
Неодинаковость коэффициента использования различных машин и механизмов по времени, конструктивные и эксплуатационные особенности и ряд других специфических факторов чрезвычайно затрудняют разработку научно обоснованной нормативной документации. Все машины и механизмы разбиты на шесть групп в зависимости от выполняемого объема работ и их заменяемости. Основой при составлении графика ремонтных работ являются карты планирования, составляемые с разбивкой по бригадам и группам родственных машин и механизмов.
Карта планирования состоит из двух частей: на одной записываются паспортные и другие данные, включая установленную периодичность технических осмотров, а на второй оформляется годичный график.
С 1960 г. в ремонтных мастерских ведется картотека трудозатрат, в том числе по каждой машине и механизму с разбивкой на слесарные и электротехнические работы. Предусмотрена следующая рубрикация: плановый ремонт; плановый осмотр, проверка и опробование узлов; устранение повреждений с указанием причин. Данные этой картотеки используются при начислении премиальных доплат рабочим по ремонту, а также для ежемесячного определения стоимости ремонта и обслуживания, т. е. определения того момента, когда дальнейшая эксплуатация данной машины или механизма становится экономически невыгодной.
Кроме картотеки трудозатрат, ведется картотека, в которой отражаются все фактически выполненные работы за срок службы машин и механизмов; она используется для анализа износостойкости отдельных частей и узлов.
Для контроля за выполнением планово-предупредительного ремонта создана специальная картотека на основе карт планирования. На каждую машину и механизм предусмотрены две карточки: рабочая и контрольная (при раздельном выполнении слесарных и электротехнических работ количество карточек удваивается). Оба вида карточек отражают основные сведеция по данной машине или механизму, включая номер группы по объему выполняемых работ, а также график со сроками их выполнения. Картотека классифицирована по бригадам, срокам работ и заводским заданиям. Перед выполнением работ рабочая карточка изымается бригадиром из картотеки и используется в качестве наряд-задания.
Выполненные работы отмечаются на карточке, и она сдается обратно. Учетчик переносит с нее данные на контрольную, после чего обе карточки перекладываются на новое место в соответствии со сроком следующего ремонта.
Фирма Goodyears Turc Rubber Co. (США) применяет четыре отчетные формы, в которых регистрируются и подробно освещаются результаты осмотров и все виды ремонтов конвейеров [120].
Критический анализ таких форм позволяет выявить случаи повторных повреждений и определить необходимый объем и периодичность ремонтных работ. Этот метод использован фирмой для планирования и проведения большинства ремонтных работ и дал экономию в стоимости и времени. так, на один из видов ремонта требовалось 30 дней, а после введения этого метода всего 12.
Мастера по предупредительному ремонту вместе с мастером линии составляют подробный технологический график в рабочих часах для каждого вида работы. Предупредительные ремонты планируются. Каждый конвейер осматривается не реже одного раза в месяц. Доклад о техническом состоянии конвейера и замеченных неисправностях служит основанием для выписывания нарядов как на текущие, так и на специальные ремонтные работы.
Важнейшее значение в организации содержания и ремонта погрузочно-разгрузочных машин имеет совершенствование системы обучения и подготовки кадров, обслуживающих эти машины.
На некоторых предприятиях ГДР внедряется новая система подготовки персонала, обслуживающего грузоподъемные машины и механизмы (121]. Система складывается из нескольких этапов. Первый - получение предварительных практических навыков и ознакомление с машинами. Для этого каждый будущий крановщик или механик должен определенное время работать транспортным рабочим, такелажником, сигнальщиком, смазчиком, ремонтником, помощником у опытного крановщика и т. д. Минимальный срок предварительной подготовки для крановщиков 14 дней, для механиков 12 месяцев.
Второй этап - теоретическое обучение, проводимое по установленной программе. Продолжительность обучения по основной программе 30 ч, по дополнительной 20 ч, по специальной 60 ч.
По окончании теоретического курса учащемуся выдается паспорт машиниста подъемных механизмов, включающий свидетельство о прохождении курса обучения для механиков подъемных механизмов; отметки органов технического надзора; заключения о врачебных освидетельствованиях, проводимых не реже одного раза в 2 года; отметки о служебной деятельности (время и место работы).
Получение паспорта и свидетельства о прохождении курса обучения еще не дает права на управление и обслуживание подъемных механизмов. Специальное удостоверение обучающийся получает после третьего этапа обучения.
По окончании обучения предусмотрена стажировка по управлению и обслуживанию определенной подъемной машины под руководством опытного рабочего. По окончании стажировки руководителем предприятия выдается удостоверение на право управления и обслуживания подъемных машин определенных типов. Удостоверение имеет силу только в пределах данного предприятия.
На двух предприятиях и складах фирмы Garingtons, Ltd. (Англия) применяется поощрительная система организации и оплаты труда водителей вилочных погрузчиков (122).
Все 48 водителей находятся в распоряжении транспортного отдела предприятий. В цехах они подчиняются мастеру и бригадирам. За каждым водителем закреплена определенная машина, которую никто, кроме гаражного механика и бригадира, не имеет права использовать. Разработанная система планово-предупредительного ремонта предусматривает регулярное техобслуживание машины один раз в две недели. Для повышения персональной ответственности водителей на каждом погрузчике закреплена табличка с именем водителя.
Премиально-поощрительная система оплаты труда заключается в следующем. В начале каждых двух недель работы водителю записываются 200 исходных баллов, соответствующих 100%-ной эффективности его работы. Для получения наиболее высокой заработной платы водителю необходимо сохранить не менее 182 баллов. Все 200 баллов распределяются следующим образом (табл. 3).
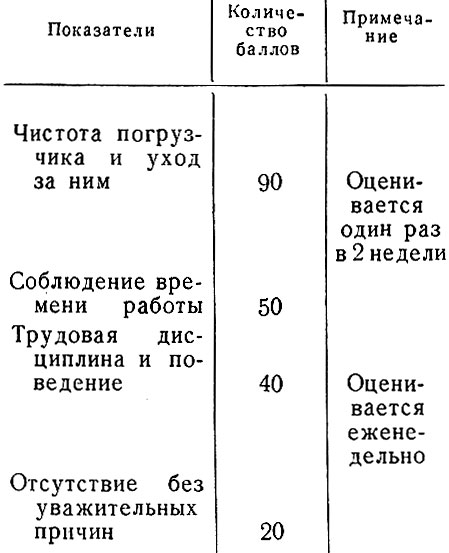 таблица 3
Оценку по первому пункту производят гаражный механик и сотрудник транспортного отдела во время регулярной двухнедельной проверки всех машин. Баллы снимаются за наличие царапин, грязи, повреждений. Снятие баллов можно опротестовать перед начальником транспортной службы.
По второму пункту учет ведется при помощи номограммы. Здесь принимается во внимание общее количество и время опозданий. При снятии 19-26 баллов выплачиваются 2/3 премиальных, при потере 27-48 баллов 1/3 премиальных, а при потере 49 баллов премиальные вовсе невыплачиваются. По истечении 12 недель водителю, сохранившему наибольшую сумму баллов, выплачивается дополнительная надбавка к зарплате.
По данным фирмы описанная система оплаты позволила повысить эффективность использования парка вилочных погрузчиков и улучшить их техническое состояние при небольших дополнительных затратах.
Увеличение парка погрузочно-разгрузочных машин делает особенно актуальной задачу повышения межремонтных сроков и сроков службы машин.
На заводах ФРГ (123), изготовляющих подъемно-транспортное оборудование, осуществляется нанесение недолговечных антикоррозионных покрытий на поверхности стальных деталей. Покрытия обеспечивают защиту от атмосферных воздействий на период сборки машины. Иногда покрытия наносятся после монтажа, но, так как они недолговечны, то при транспортировании машины сильно повреждаются.
Покрытие Hafgrund, содержащее соли хромовой кислоты, и фосфорную кислоту, наносится тонким слоем и имеет малую механическую прочность. В качестве покрытия применяют также свинцовый сурик V40, содержащий на 100 весовых частей готового состава и 40 весовых частей измельченного тяжелого шпата (барита). По эффекту пассивирования покрытие V40 не уступает чистому свинцовому сурику. В качестве связующего средства используется олифа.
Основным вопросом при конструировании ленточных конвейеров является увеличение срока службы конвейерной тенты которая подвергается наибольшему износу в период ее загрузки (124). Для этого на одном из предприятии Англии на погрузочной станции роликоопоры рабочей ветви делаются из сборных резиновых роликов. такой ролик имеет металлический вал, на котором собирается комплект из резиновых колец, образующих тело ролика. Подобная конструкция роликоопоры смягчает ударные нагрузки, возникающие вследствие падения кусков материала на ленту.
Имеются конструкции, в которых ролики представляют собой резиновые баллоны, заполненные воздухом. Один из способов, применяемых с целью сокращения износа ленты в период ее загрузки, состоит в том, что на ленте перед местом погрузки создается «подушка» из такого же материала, который с очень малой скоростью подается на ленту. В этом случае материал, подаваемый основным питателем, попадает на «подушку» и не причиняет ленте механических повреждений Большое значение имеет также очистка ленты. Используемые для этого статические механические скребки, щетки вращающиеся скребками, не производят полной очистки и кроме того, могут вызывать износ ленты. Хорошие показатели дает механо-динамическое очистное устройство состоящее из вращающегося ребристого барабанчика с четырьмя или пятью ребрами. При вращении ребро с легким ударом приподнимает ленту, а затем проскальзывает по ней, счищая грязь.
Своевременное удаление очищенной грязи, а также устранение просыпания материалов с ленты способствуют уменьшению загрязнения ленты. Натяжение ленты также сказывается на ее долговечность. Создание лент с нейлоновым кордом увеличит долговечность лент. Чтобы увеличить долговечность службы погрузочно-разгрузочных машин, важно также не допускать повреждения их в процессе эксплуатации. В Италии (125) разработаны приборы для предотвращения столкновения кранов, перемещающихся по одному подкрановому пути. Созданы специальные приборы, которые подразделяются по принципу действия на механические, электрические, световые и акустические.
Одни приборы реагируют на приближение кранов друг к другу, а другие не допускают въезда крана на определенный отрезок кранового пути. Последние применяются, когда крановый путь разделен на участки в соответствии с выполняемой кранами работой.
В Англии (126) запатентована система сигнализации для безопасной работы крана с установкой на одном из них источника света, фотоэлемента и усилительного устройства, а на другом - отражателя или дополнительного источника света.
|