|
2. Склады для тарно-упаковочных грузов
УДК 658.78:656.073.433
Процесс совершенствования многономенклатурных складов тарно-штучных грузов предусматривает внедрение производственной тары всех необходимых типоразмеров, высотных стеллажей и систем автоматизации учета и управления. Внедрение производственной тары является необходимой и первоочередной задачей при механизации подъемно-транспортных работ. При этом тара должна быть оборотной и унифицированной, что позволяет организовать бесперевалочные перевозки грузов между производственными цехами. Следует стремится к тому, чтобы один типоразмер тары охватывал все без исключения операции, начиная от поступления на предприятие материалов и заготовок и кончая отгрузкой готовой продукции, включая производственную и складскую зоны. При этом обеспечивается единая производственно-транс-портно-складская технология, рассматривающая все объекты предприятия, в том числе и склады, как равноценные участки основного производства.
Все более увеличивается число строящихся высотных складов с высотой складирования грузов более 10 м. В ФРГ в настоящее время эксплуатируется 120 подобных складов. Целесообразность строительства таких складов обуславливается тем, что с увеличением высоты складских зданий значительно сокращается их удельная стоимость. Так, если принять строительную стоимость здания при складировании грузов автопогрузчиком на высоту 3,2 м за 100%, то при складировании кранами-шта-белерами на высоту 5,2 и 10,0 м стоимость сокращается соответственно до 80,0.2 и 75,87%. Целесообразность строительства высотных складов увеличивается еще более, если они не имеют железобетонного каркаса, а панели покрытия и стены крепятся непосредственно к стеллажам. В этих складах стеллажи используются как несущие конструкции, так как они рассчитываются на большие нагрузки, а для покрытия и стен применяются легкие и дешевые материалы. Другими преимуществами высотных складов являются возможность строительства их в стесненных городских условиях, современное внешнее архитектурное оформление и относительная несложность (по сравнению с обычными складами) автоматизации работы подъемно-транспортных машин.
Различают три степени автоматизации складов тарно-штучных грузов: полную, реачъную и частичную. Полная предусматривает комплексную автоматизацию всех работ на складе и пока осуществляется редко.
Реальная, внедренная на многих складах, предусматривает, как правило, автоматизацию работы основных погрузочно-разгрузочных и транспортных машин. Так, на участках транспортирования грузов между зонами приемки, хранения и отправления применяют напольные тележечные грузоведущие конвейеры с автоматическим адресованием. Различают два способа управления движением тележек этих конвейеров: электрическое и механическое. Электрическое основано на магнитном воздействии, создаваемого низковольтными проводниками, располагаемыми вдоль трассы передвижения под полом склада, на приводы тележек. Механический способ управления основан на сцеплении грузовых тележек с непрерывным тяговым органом (цепью), вмонтированным в специальный желоб, проложенный в полу склада.
Частичная автоматизация предусматривает автоматизацию отдельных операций (движений) подъемно-транспортных машин. Так, наиболее распространенной является автоматизация вертикального перемещения грузоподъемников кранов-штабелеров, управляемых с пола, в то время как их горизонтальное передвижение осуществляется оператором. Объясняется это необходимостью уменьшения вертикальных размеров ячеек стеллажей, что позволяет увеличить их вместимость.
Ряд усовершенствований осуществлен за последние годы на складах металла"
На складе фирмы William Rowland Steel, Ltd (Англия) в Дарлингтоне при хранении листового металла имеется оборудование для резки и правки листов, позволяющее разрезать листы шириной 2,44 м, длиной 11 м и толщиной до 12,7 мм. между установками для резки и правки находятся столы с рольгангами, облегчающими перемещение листов. Кроме того, для перемещения металла используется кран с электромагнитом грузоподъемностью о т, с помощью которого осуществляется также погрузочно-разгрузочные работы. Длина линии, которую проходят листы при резке и правке, составляет 36,6 м. Все оборудование расположено в здании склада, имеющим ширину 24,4 м. Листы длиной 11 м поступают с прокатного стана и хранятся в штабелях, уложенных на полу склада. Вес штабеля листов одного размера составляет 300 т. В 1971 г. ожидается поступление на склад листов длиной 14,6 м [96].
Склад рулонной стали фирмы W.Galloway (Англия) является одним из наиболее механизированных в стране и имеет собственный вычислительный центр. Склад рассчитан на хранение более 8 тыс. т стали в рулонах весом до 15 т, уложенных на семи специальных многоярусных стеллажах с регулируемыми фиксирующими колодками. Между стеллажами устроены проходы для движения двух самоходных погрузчиков стрелового типа грузоподъемностью 15т. По краям проходов уложены ограничительные рельсы; погрузчики снабжены боковыми направляющими роликами. Таким образом, погрузчики автоматически направляются вдоль проходов без какой-либо опасности столкновения со стеллажами и повреждения машин и складируемого материала. Это позволило уменьшить ширину проходов до минимума, лишь слегка превышающего ширину самой машины.
Компоновка склада подчинена единому технологическому потоку с подачей материала в отделение обработки, где осуществляется резка материала на листы заданного размера, полосы различной ширины и т.д. с последующей подачей заготовок на участки временного хранения и отправления заказчикам. Конвейеризованный участок размотки и рихтовки приспособлен к приему рулонов шириной до 1830 мм и весом до 15 т. Рулоны, выдаваемые из заготовительного отделения, могут весить до 10 т и иметь диаметр до 1,52 м. Загрузка трех размоточно-рихтовочных линий производится с помощью специальной тележки с регулируемыми люльками для рулонов, подаваемых на заданную высоту гидравлическими подъемниками. Для перемещения тележек применена электрогидравлическая система [97].
Фирма C.Walker Sons, Ltd (Англия) открыла в г. Блэкберне первую очередь крупнейшего склада металлопроката, который к 1975 г. будет иметь годовой оборот 350 тыс. т проката. Первая очередь склада имеет размеры 300 х 120 м. Она разделена на 6 секций (A - F), каждая из которых имеет соответствующую специализацию. Например, в секции А установлено оборудование для резки листового материала. Это оборудование закуплено у фирмы Ehrhardt Sehner АС (ФРГ). Оно позволяет резать листы толщиной до 13 мм, шириной до 2000 мм и длиной от 1000 до 8000 мм. Максимальная операционная скорость на этой линии 30 м/мин. С этой линией соединена установка для разматывания рулонов, расположенная в секции В. В секции С установлены 2 автоматические линии для разматывания рулонов и разрезки их на листы. Операционные скорости на линии 15 и 30 м/мин. При этих скоростях допуски на разрезку листов составляют ±0,125 мм. Возможно увеличение операционной скорости до 150 м/мин. В этом случае погрешность на длину листов значительно возрастает. В секции D установлены ножницы гильотинного типа, способные разрезать листы толщиной до 32 мм.
Для хранения проката в этой секции предусмотрены стеллажи елочного типа. Вместимость стеллажей 100 тыс. т проката. Секция Е предназначена для хранения среднего и легкого проката. Вместимость стеллажей - 150 тыс. т. В секции F хранятся трубы различных типоразмеров. Склад обслуживается 22 мостовыми кранами-штабелерами, обеспечивающими складирование грузов и передачу их из секции в секцию. Краны снабжены специальными захватами, исключающими повреждение проката [98,99].
В Швейцарии сдан в эксплуатацию крупный склад фирмы Allga AG, предназначенный для приема, переработки и отправления потребителям алюминия свыше 1200 наименований профилей и 500 наименований листового алюминия. При проектировании склада основное внимание обращалось на достижение высоких коэффициентов использования площади пола и механизации внутрискладских работ, а также на высокую производительность основных операций. Главное хранилище размещено в каркасном здании размерами в плане 66 X 44 ми высотой 25м, к которому примыкают на длинных сторонах 2 крыла, служащих для приема грузов в склад и отправления со склада. Хранилище оборудовано тремя парами многоярусных стеллажей длиной 30 м, с возможностью увеличения длины за счет оставленного свободного пространства. Большая высота стеллажей позволяет разделить в пространстве одновременное ведение работ на склад и со склада.
Прибывающие грузы выгружаются из вагонов с откидной крышей с помощью специального крана-штабелера грузоподъемностью 6 т. Кран переваливает грузы в тележки, в которых они подаются в проезды между парами стеллажей. В проездах работают 4 мачтовых штабелера грузоподъемностью 1,1 т. Скорость штабелера 90 м/мин, скорость подъема груза 35 м/мин. Грузоподъемник снабжен двумя лебедками с регулируемым электроприводом. Грузозахват выполнен в виде выдвижных 2-сторонних вилок. На нем смонтирован также накопитель. Открытая кабина с двумя операторами перемещается вместе с грузо-за хватом.
Выдаваемые со склада грузы поступают на 10 - секционный роликовый конвейер, используемый в качестве промежуточного накопителя. В экспедиции на работах заняты вилочные погрузчики и мостовой кран, обслуживающий всю длину пролета. Оборудование склада поставлено фирмой Demag-Fordertechnik (ФРГ) [100].
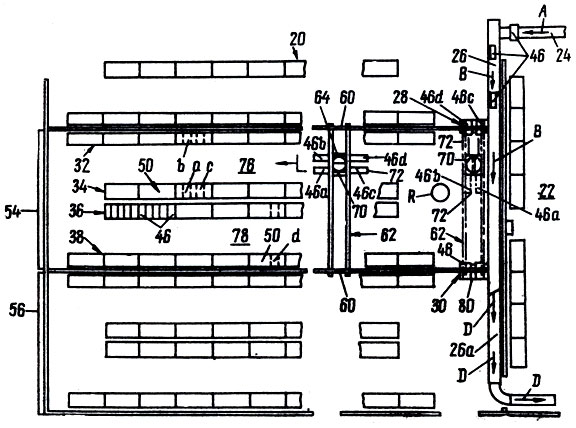 Рис. 34. Вид склада в плане
В США разработаны новый способ работы с рулонами и конструкция крана-укладчика для автоматизированного склада металла. Склад 20 (рис. 34) примыкает к производственному цеху 22 из которого по конвейеру 24 поступают упакованные рулоны 46. С конвейера 24 рулоны попадают на конвейер 26, доставляющий их к станциям перегрузки 28 или 30, с которых рулоны перемещают на стеллажи 32, 34, 36 или 38 для хранения. В каждом рулоне материал намотан на полый цилиндр 40 (рис. 35). Для выдачи рулонов со склада используются верхние элементы 84 стеллажей 80 перегрузочных станций 28 и 30, на которых ленточный конвейер передает рулоны на конвейер 26а, расположенный над конвейером 26. При подаче рулонов на склад они поступают с конвейера 26 на нижние элементы стеллажей 80. Для доставки рулонов на полки 50 стеллажей 32, 34, 36 и 38 применяется кран-укладчик, перемещающийся по несущим балкам 60, установленным над средней частью стеллажей 32 и 38. Кран имеет мостовые балки 62, по которым перемещается каретка 64 (рис. 36). К последней присоединен механизм, обеспечивающий поворот кольцевого элемента с подвешенными к нему вертикальными балками 68. На балках 68 установлено грузозахватное устройство 70 с вилками, которые могут поворачиваться на осях крепления 74 на угол до 90°. В устройстве 70 предусмотрено свободное пространство 8 2 для расположения органов управления краном и места для оператора. При необходимости перемещения рулонов краном вилки вводят в полые цилиндры 40, а затем поднимают грузозахватное устройство 70 по балкам 68. Укладываются рулоны при обратном порядке операций. Устройство 70 может перемещаться в вертикальном направлении по балкам 68, в поперечном при движении каретки 64 по балкам 62 и в продольном - при движении крана по балкам 60 [101].
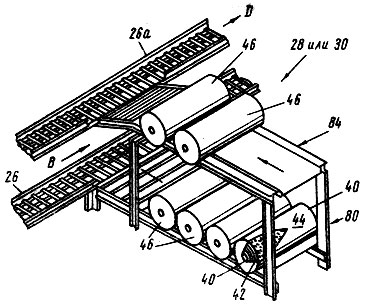 Рис. 35. Полые цилиндры
В организации работы крупных складов тарно-штучных грузов отмечается стремление к четкой специализации участков по видам выполняемых в них работ и применяемым механизмам. Так" в зоне хранения грузов, отличающейся, как правило, большой строительной высотой, применение электропогрузчиков становится неэффективным вследствие относительно небольшой высоты складирования грузов. Нецелесообразным становится использование погрузчиков и на транспортных грузопотоках в этих складах вследствие их малой производительности. Таким образомэ в крупных складах погрузчик - это не универсальная, как было ранее, а специализированная машина. Применение его целесообразно только в зонах прибытия и отправления грузов. В этих условиях в зоне хранения появляется необходимость в применении других подъемно-транспортных средств, специализированных по участкам складов. Такими средствами являются краны-штабелеры в зонах хранения и напольные тележечные конвейеры, соединяющие зоны хранения, приема и отправления грузов, Тележечный конвейер состоит из следующих, основных узлов: привода, ходовой части, натяжного устройства, опорной металлоконструкции и устройств для разветвления ходовых путей. Грузоподъем-ность тележечного конвейера достигает 4000. кг, скорость передвижения 40 м/мкн, преодолеваемый уклон до 15, общая длина трассы до 2 км и более, а срок службы 20 - 30 лет. Другим важным преимуществом тележечного конвейера является удобное сочетание с основными погрузочно-разгрузочными машина ми, применяемыми на складах: погрузчиками, кранами-штабелерами и мостовыми кранами. По способу восприятия тягового усилия привода тележечные конвейеры делятся на цепные - с бесконечным замкнутым тяговым органом и бесцепные, движение которых обеспечивается индивидуальными приводами.
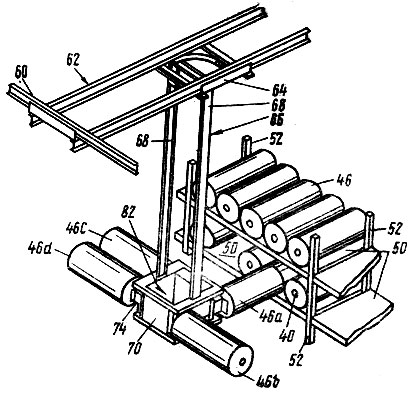 Рис. 36. Мостовые балки с кареткой
Применяются оптическое, электрическое и механическое управление передвижением тележек. Оптическое управление основано на фотоэлектрическом эффекте, который осуществляется путем установки на самоходных тележках фотоэлементов, реагирующих на изменение цвета контрастной полосы, наносимой на трассу передвижения. Электрическое управление основано на действии магнитного поля, создаваемого низковольтными проводниками, располагаемыми под полом склада вдоль трассы передвижения, на индукционные катушки тележек. При движении тележки по заданному маршруту напряжение в каждой катушке остается одинаковым. В случае же отклонения ее от заданного маршрута одна из катушек приближается к проводу, напряжение индуктированного в ней тока повышается и приводит в действие мотор рулевого управления. Механический способ управления осгован на сцеплении грузовых тележек с непрерывным тяговым органом (цепью), вмонтированным в специальный желоб, проложенный в полу склада.
Управление напольными тележечными конвейерами может быть автоматизировано в зависимости от характера трассы и величины грузопотока. В простейшем случае тележки подключаются к цепи и отключаются от нее вручную. При сложных трассах управление конвейерами может быть полностью автоматизировано, включая сортировку и адресование грузов, вывод их на кольцевые или тупиковые ответвления, перегрузку грузов и т.д. [102].
Фирмой GGMS (Франция) внедрена система складирования блоков телефонных станций. Система состоит из стеллажей, на которых хранятся блоки, и кран-штабелера Т-150. Кран может работать в автоматическом режиме (по командам, считываемым с перфокарт), в полуавтоматическом режиме (под контролем оператора) и в режиме ручного управления. Средняя продолжительность рабочего цикла 3 мин. Этой же фирмой выпускается кран-штабелер TG-1000 с высотой подъема груза 17,5 м. Краны-штабелеры фирмы Demag (ФРГ) имеют грузоподъемность 150 и 300 кг, высоту подъема груза 10м. Скорость подъема груза 12 м/мин, перемещения 100 м/мин. Краны-штабелеры фирмыFenwick (Франция) выпускаются грузоподъемностью 0,5 т. Рама крана опирается на два рельса, уложенных сверху стеллажей. Особенностью этих кранов является возможность автоматического выбора уровня передвижения грузозахватного устройства и рабочей площадки. Для кранов разработана система автоматического управления, элементами которой являются вычислительная машина и перфокарты.
Фирма Metalarc (Франция) поставляет краны-штабелеры грузоподъемностью 0,5 т, с высотой подъема груза 5 м, скорость перемещения 63 м/мин для работы в стеллажных проходах шириной 0,9 м. Эти краны имеют специальную тележку, позволяющую выполнять операции в нескольких проходах. Скорость перемещения тележки между проходами 28 м/мин. Разработаны фирмой Feralco роликовые дорожки с фрикционными толкателями для перемещения грузов, пакетированных на поддонах [103].
Во Франции разработан комплекс быстросборных складских конструкций, предназначенный в основном для хранения автомобильных частей и деталей (система Codi - Fix). Этот комплекс включает сотни различных элементов для полного оснащения складов. Элементы делятся на две большие группы: лотки четырех типов из металлических листов или пластмассы, имеющие на лицевой стороне держатель для этикеток или перфокарт; несущий каркас из рам трех размеров и регулируемых на длине 5 см стоек и распорок. Собранные в одну жесткую конструкцию, стеллажи отвечают необходимым требованиям для хранения, приема и выдачи деталей. Все элементы соединяются между собой при помощи пазов и зажимов. Установки из элементов Codi-Fex могут иметь любые размеры - от одного отсека до нескольких сотен - располагаясь на одном, двух или трех этажах. Для громоздких частей устанавливают рамы высотой 217 см, глубиной 80 см, распорки 68 см. Для мелких деталей применяют рамы высотой 217 см и глубиной 37, 70 и 80 см, Для продолговатых изделий (осей, прутков, тяг и т.п.) устанавливают решетчатые или перфорированные стенки внутри или снаружи рам, иногда у стены склада, которые скрепляют скобами. Изделия опираются на 2 - 3 точки [104].
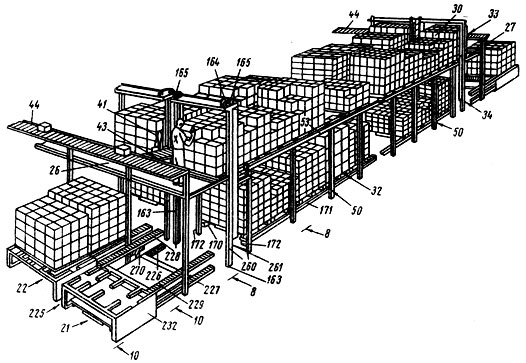 Рис. 37. Линии хранения склада
В США запатентованы транспортные устройства для перемещения тарно-штучных грузов в системе складского хозяйства, состоящей из линий хранения 21, 22 и т.д. (рис. 37), Составители заказов находятся на платформах 26 и 27. На каждой линии имеются верхняя конвейерная система 30 и нижняя 32, доставляющие поддоны с грузом соответственно к составителю заказов и к подъемнику, расположенному рядом со станцией составления заказов. Информация о содержании заказов проектируется на экранах устройств 41. Составитель наклеивает на упаковку требуемого груза ярлык и по рольгангам 43 и 44 отправляет их в зону сортировки. Верхняя и нижняя конвейерные системы 30 включают два швеллера 52 и 53 (рис, 38), установленных параллельно и неподвижно на поперечных балках 50 В закрепленных на вертикальных балках 50 А. Параллельно швеллерам 52 и 53 расположены также неподвижно закрепленные уголки 54. Эти швеллеры и уголки являются опорами для вращающихся роликов 55, на которые опираются продольные элементы профилей 60 и соединенные поперечной балкой 83. Груженые и порожние поддоны опираются на среднюю часть профилей 60. Полки профилей 60 используются, как направляющие и находятся в контакте с роликами 66, установленными на полках швеллеров 53 и 55. К балкам 83 приварены V-образные элементы 68. На одном из концов верхней конвейерной системы расположен толкающий механизм с тяговыми цепями 76 и 77 (рис. 39), одетыми на холостые звездочки 79, установленные на валу 80 с помощью подшипникового узла 81. Тяговые звездочки 83 находятся на валу 84, соединенном с гидродвигателем 86. На цепях 76 и 77 расположены толкающие ролики 87, соединенные со специальными звеньями 89 этих цепей. На звеньях 89 на пальцах 90 установлены пары вращающихся внутренних роликов 91 и пары вращающихся внешних роликов 92. Верхние части цепей опираются внешними роликами 92 на элементы 93 и 94, закрепленные на балках 50 В. Нижние части цепей поддерживаются скользящими элементами звеньев на направляющих 96, также закрепленных на поперечных балках 50В, Упорный узел 100 смонтирован на поперечном уголке 101, проходящем за элементами 93. Упорный узел состоит из фиксированной части 103 и подвешенного к ней на валу рычага 104, упирающегося в балку 63. Рычаг 104 удерживается в нужном положении пружиной 107, закрепленной также на фиксированной части 103. Рычаг 104 может отводиться от балки 63 пневмоцилиндром 108. Когда платформа подъемника находится на станции составления заказов, цепи 76 и 77 приводятся в движение и перемещают поперечные балки 63 и профили 60 до тех пор, пока первая из них не будет остановлена упорным узлом 100. После этого ролики 91 воздействуют на 11 -образные элементы 68 балок 63, несколько приподнимают их и проходят под ними, После освобождения первой балки упорным узлом 100 она перемещается на платформу 109 подъемника, на которой имеются роликовые устройства, аналогичные взаимодействующим с профилями 60 и рас положенным на балках рамы 50. Такое же устройство роликового пути предусмотрено для нижней конвейерной системы. Различия заключаются лишь в конструкции упорных узлов. Упорный узел на платформе 109 выполняет не только функции останавливающего механизма, но и амортизатора для плавной остановки поддона с грузом, находящегося на профилях 60. Перемещение балок 63 левой части нижней конвейерной системы осуществляется гидроцилиндром двойного действия, а этих же балок правой части - толкающими цепями, аналогичными рассмотренным цепям. Правая часть верхней конвейерной системы работает с гидроцилиндром двойного действия и полностью идентична левой части нижней конвейерной системы. Подача грузов на поддонах и их замена производятся с помощью механизма 225 (см. рис. 37), имеющего рольганги 226 и 227, установленные на уровне нижнего положения платформы 109, и рольганги 228 и 229 находящиеся на несколько более высоком уровне. Внутри рамы механизма 225 установлено устройство для подъема поддонов. Для остановки поддонов использовано устройство 270 взаимодействующее с подвижными поперечными балками 63. Для вертикального перемещения платформы 109 в качестве направляющих применены вертикальные стойки 163, выполненные из швеллеров. Платформу 109 передвигают цепи 165, приводимые в движение гидродвигателями 164. Для управления и взаимоблокирования отдельных перемещений поддонов с вертикальным движением платформы 169 использована электрическая система, в которую входят конечные выключатели, датчики положения, фотоэлементы, реле и контакторы. Управление работой оборудования осуществляют составители заказов [ 105].
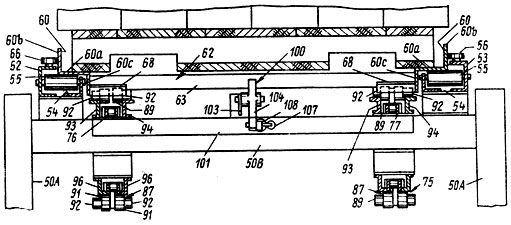 Рис. 38. Швеллеры с поперечными балками конвейера
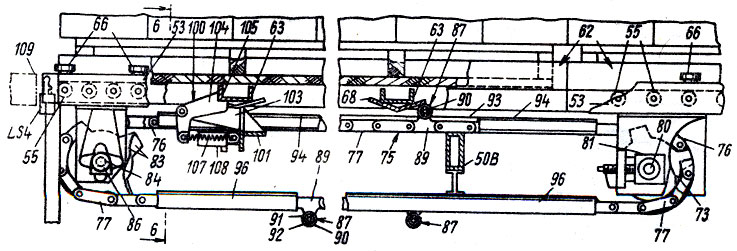 Рис. 39. Толкающий механизм с тяговыми усилиями
В ФРГ выполнено исследование для определения показателей эффективности работы складов. Установлено, что такими показателями являются коэффициент использования их объема запас материалов и численность обслуживающего персонала. Исходной базой для определения величины показателей является транспортно-технологическая схема организации и механизации внутрискладских работ, устанавливающая перечень всех технологических, подъемно-транспортных, контрольных, учетных и других операций, в их последовательности и взаимодействии, которым подвергаются материалы (полуфабрикаты, изделия) с момента поступления их на склад до отправления потребителю.
В зависимости от специализации и назначения склада его транспортно-технологическая схема включает следующие основные операции или только некоторые из них: выгрузка поступающих грузов8 количественный и качественный анализ и оформление документов о приеме грузов, подача к местам хранения, загрузка стеллажей (укладка штабелей), хранение, разгрузка стеллажей (штабелей), подача в экспедицию, комплектование заказов, упаковка, погрузка на транспорт вывоза, учет поступления, выдачи и остатков грузов, информация о состоянии складских запасов. На складах преимущественное распространение получают поддоны 800 x 1200 и 1200 x 1200 мм грузоподъемностью до 1200 кг. Загрузка этих поддонов должна производиться в зоне отправления. Это одно из основных требований к правильной организации работы складов, обеспечивающее транзитное (бесперегрузочное) прохождение груза по всему складу. При этом основным средством перемещения этих поддонов по складу являются приводные роликовые или тележечные конвейеры. В зоне хранения применяются краны-штабелеры мостовые опорные на стеллажи или колонны, и стеллажные, опорные и подвесные. При этом в зависимости от технологии работы этой зоны, комплектование заказов может производиться либо в кабине крана-штабелера (мелких отправок), либо в экспедиции, куда доставляются груженые поддоны. Экономически целесообразно строительство высотных складов с применением стеллажных кранов-штабелеров с высотой складирования до 30 м. Однако при этом целесообразно проверять их на динамическую устойчивость [106].
Вновь построенный склад металлоизделий фирмы Moremont (США) предназначен для хранения выхлопных труб и глушителей автомобилей. Для достижения высокой эффективности работы склада при его проектировании были заложены следующие принципы организации работы: стеллажное хранение изделий; использование ЭВМ для оперативного планирования и обработки информации; применение разветвленной сети теле- и радиосвязи; транспортирование грузов непрерывным транспортом; выполнение погрузочно-разгрузочных операций вилочными погрузчиками с боковым захватом. Применение перечисленных принципов дает возможность одновременно хранить на складе 1,6 млн. глушителей и их частей 600 различных наименований и 250 тыс. выхлопных труб и деталей 1800 наименований, отправлять -30 тыс. глушителей и выхлопных труб в смену, выполнять 90% заказов на другой день после их поступления. Склад имеет высоту 7,9 м, что дало возможность смонтировать в нем стеллажи высотой 7,5 м. Треть площади склада специализирована для хранения глушителей, а остальная для труб [107].
На заводе John Deere Tractors Works введены новые средства механизации на складе, позволившие автоматизировать процесс складирования и выдачи изделий со склада на производственные линии. Средства механизации включают автоматически управляемые краны-штабелеры, передающие тележки, серию гравитационных и приводных роликовых и ленточных конвейеров, а также поворотных столов весовых устройств и пакетоформирующих машин. Предлагаемые средства механизации позволили высвободить 22 рабочих, 3 вилочных погрузчика и сэкономить 3716 м2 складских площадей [108].
Складское и транспортное хозяйство предприятия фирмы Lye Steel (Англия) отличается использованием самых современных средств складирования и механизации. Предприятие поставляет заказчикам высококачественные стальные заготовки. Новый метод складирования рулонов листовой стали обеспечивает высокую степень использования емкости склада и облегчает нахождение нужного материала. Рулоны весом до 15 т складируются на многоярусных стеллажах, где они навешиваются на горизонтальные штыри. Внутрискладское транспортирование рулонного материала осуществляется с помощью оригинального подвесного крана-штабелера, полный вес которого превышает 42 т. Кран способен передвигаться в четырех внутрискладских проходах вдоль стеллажей. Оператор крана находится в закрытой кабине, перемещающейся вместе с вертикальной рамой. С помощью системы промышленного телевидения оператор легко обнаруживает необходимую ячейку стеллажа. Вертикальная рама может поворачиваться вокруг своей длинной оси в пределах 270. Величина пролета, в пределах которого указанная рама вместе с кабиной оператора и захватным рабочим органом может перемещаться вдоль горизонтальной мостовой фермы, равна 24,4 м. Длина мостовой фермы 26,5 м. Кран используется для укладки материала на стеллажи, а также для подачи его к технологическому оборудованию для резки, шлицевания и т.д. Предприятие, включая склад и технологическое отделение, занимает площадь 4180 м2 [109].
Взамен старой системы хранения длинномерных материалов в ящиках на полу склада целесообразно располагать их на стеллаже, что обеспечивает хорошую обзорность склада и оптимальное использование его пространства. Для этого в ФРГ применяют стеллажи сварной конструкции, состоящие из несущих элементов двутаврового и швеллерного сечения, которые изготавливаются из высококачественной стали. Конструкция отличается большой грузоподъемностью и не требует специального закрепления в складском помещении. Необходимо лишь обеспечить достаточную прочность фундамента. Преимущества стеллажного складирования могут быть показаны на следующем примере. Складирование в отдельных ящиках длиной 6 м, шириной 50 см, высотой 60 см при расстоянии между ящиками 1 м позволяет при весе ящика 1 тыс. кг разместить на складской площади 20 м и шириной 8 м, 20 тыс. кг груза. При ярусном расположении затрудняется доступ к нижним ящикам. Однако при этом на той же поверхности пола могут быть размещены 6 двусторонних и два односторонних 5-этажных стеллажа длиной 3 м и шириной 0,5 м при расстоянии между стеллажами 1,3 м. В этом случае вес размещаемого груза может быть увеличен до 70 тыс. кг, т.е. в 3,5 раза. Система допускает использование складской техники [110].
В США запатентован стеллаж, который может быть составлен из элементов, устанавливаемых один на другой. Элемент стеллажа состоит из рамы, образованной продольными и поперечными элементами. По углам рамы имеются вертикальные стойки. Сварная рама выполнена из швеллеров, соединенных так, что они получают коробчатое поперечное сечение. Стойки соединены между собой с помощью швеллеров и опорных плит. При этом нагрузка от груза и от рамы передается нижней частью стоек плитам и опорной поверхности пола складского помещения. Стойки будут передавать нагрузку только от следующего, установленного на них элемента. В верхней части стоек имеются направляющие, облегчающие установку элементов стеллажа один на другой с помощью вилочного погрузчика. Стеллаж такой конструкции позволяет ускорить выполнение складских операций [111].
Передвижные стеллажи, используемые на складах и позволяющие увеличить полезную площадь складских помещений, имеют в определенных условиях ряд преимуществ по сравнению со стационарными. В Англии на некоторых складах применяется дистанционное управление такими стеллажами по радио или с помощью других средств. В качестве меры безопасности при передвижении стеллажей возможно использование фотоэлектрических датчиков инфракрасных лучей [112].
В Англии разработаны две конструкции стеллажей, предназначенных для использования на автоматизированных складах. Одна из конструкций представляет собой два стеллажа 1 (рис. 40), между которыми в проходе 4 расположен механизм выемки и установки поддонов или желобов 3. На стойках стеллажей имеются роликовые опоры 2, по которым могут скользить поддоны 3. Для выемки и установки поддонов 3 используется рама 5, находящаяся в проходе между стеллажами 1 и опирающаяся на вертикальные валы 6 с винтовой нарезкой, установленные по углам стеллажей на опорах 7 с подшипниковыми узлами. Для перемещения рамы 5 в вертикальном направлении используется реверсивный электродвигатель 8, вращающий через редукторы 9 и валы 10 гайки валов 6, установленные в корпусах 11, закрепленных на раме 5. По раме 5 может перемещаться поперечная балка 12, движение которой осуществляется при вращении валов 13 с винтовой нарезкой от реверсивного электродвигателя 14 через редуктор 15 и вал 16. На поперечной балке 12 расположено двухстороннее захватное устройство 17, которое может соединяться с поддоном при подходе к нему балки 12. При обратном движении балки 12 это устройство обеспечивает перемещение поддона по раме 5. Когда поддон полностью окажется на раме 5, он может быть удален краном или вилочным погрузчиком. При постановке поддонов на стеллаж порядок операций обратный. Управление работой электродвигателей и захватным устройством ведется с пульта 18.
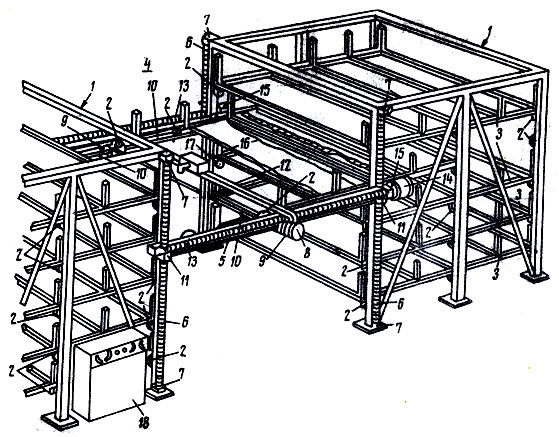 Рис. 40. Стеллажи автоматизированного склада
Вторая конструкция представляет собой стеллаж, разделенный на секции 1 (рис. 41). На стойках секций стеллажа имеются ролики 2, по которым могут скользить поддоны 3. Для выемки и установки поддонов на стеллаж используется рама 5, опирающаяся на вертикальную раму 19 и перемещающуюся относительно этой рамы в вертикальном направлении с помощью вертикальных валов 6 с винтовой нарезкой, реверсивного электродвигателя 8, редуктора 9 и валов 10. Вертикальные валы 6 закреплены в раме 19 подшипниковыми опорами 7. По раме 5 перемещается балка 12с двухсторонним захватом 17. Для движения балки используется реверсивный электродвигатель 14, редуктор 15, валы 16 и гайки в корпусах 22, перемещающиеся при вращении по валам 13с винтовой нарезкой. Как и в первой конструкции выемка и установка поддонов осуществляется захватом 17 при движении балки 12. Перед выемкой или установкой поддона раму 19 устанавливают у требуемой секции стеллажа, перемещая ее по рельсам 20. Затем раму 5 подводят к соответствующей полке стеллажа и только после этого подгоняют к поддону балку 12. Перемещение рамы 19 вдоль стеллажа может осуществляться не только обычным, но и линейным электродвигателем. Управление всем этим оборудованием ведется с пульта 18, установленного на платформе 23, укрепленной на раме 19 [113].
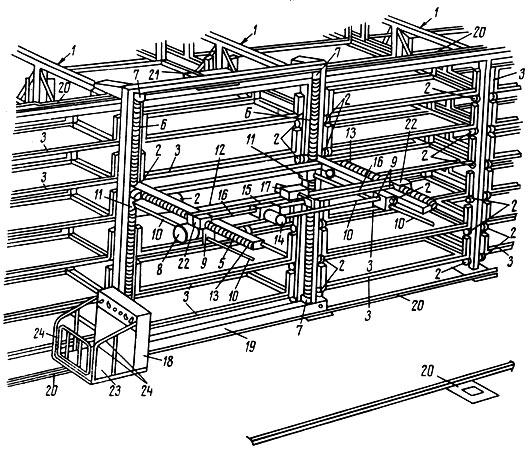 Рис. 41. Секционный стеллаж
В ФРГ применены высотные стеллажи с основанием 800 - 1200 мм, которые снабжены ходовыми роликами и с помощью звеньев соединяются в бесконечный поезд. Этот поезд движется по направляющим, которые состоят из двух прямолинейных участков и двух закруглений по концам. Цепь приводится в движение зубчатыми колесами, расположенными на этих закруглениях. Каждое зубчатое колесо снабжено приводным двигателем. Если товары необходимо снять с определенной полки стеллажа, то его номер устанавливается на приборе управления. Нажатием кнопки цепь приводится в движение до тех пор, пока требуемая полка стеллажа не окажется перед заборным пунктом и не сработает концевой выключатель установки. Механическое или электронное устройство управления может выбрать кратчайший путь (вперед или назад) движения нужного стеллажа до заборного пункта. Применяя программное управляющее устройство, можно сократить до минимума время ожидания каждого стеллажа на заборном пункте. Внедрение такой установки на складе площадью 2200 м3 дало улучшение использования его емкости на 75%. [114].
В ГДР запроектированы два стеллажных цеха на складе машиностроительного завода. Цеха размещены на первом (надцокольном) этаже заводского корпуса с допустимой удельной несущей способностью межэтажных перекрытий 2 т/м2. Оба цеха узкоспециализированы по номенклатуре готовых изделий и, из-за невозможности построения графиков снабжения деталями и полуфабрикатами, нуждались в организации промежуточных складов. Исходя из длительности полного производственного цикла, потребная емкость склада определена эквивалентной пяти рабочим дням. Учитывая множественность номенклатуры деталей и полуфабрикатов, поставляемых на склад, а также отсутствие единого носителя исходной информации для проектирования, из почти 1000 наименований выбрано 178, типичных по переработке в системе внутрицехового транспорта, и по ним произведены все основные расчеты. Поскольку на предприятии использовалось значительное количество (до 90%) нестандартных контейнеров 8 типоразмеров, решено сохранить их, но с условием эксплуатации на износ с последующей заменой контейнерами трех типоразмеров по стандарту TGL9392.
Расчет потребности в контейнерах произведен по числу рабочих мест, при коэффициенте запаса 1,3. С учетом переработки части грузов на плоских поддонах средний вес грузоедикицы принят равным 300 кг. При высоте этажа 3,2 м для переработки грузов запланировано использование вилочных электропогрузчиков EFG 631. Стеллажные блоки типа Badersleben 5 и 7 выбраны высотой 2,3 и 3,3 м в зависимости от того, используются ли поддоны или контейнеры с заходами для вилок погрузчика. Полезная высота контейнеров в последнем случае принята равной 750 мм. Предусмотрено использование плоских поддонов размерами 1200 х 800 мм, контейнеров размерного класса 0 (1240 х 840 х 540 мм) и ящечных поддонов - 1240 х840 х970 мм. Для облегчения адресования грузов все рабочие места снабжен крупноформатными индексами, хорошо видимыми с маршрута движения погрузчиков [115].
Фирма United Biscuit (США) построила склад площадью 7,4 тыс. м и высотой 12,2 м. Современные средства механизации, складирования и учета позволяют на этой относительно небольшой площади складировать 10150 поддонов с грузами 600 наименований. Ежедневный грузооборот склада составляет 1000 грузовых отправок, максимальная продолжительность хранения отдельных грузов - 2 недели. Учет грузов на складе осуществляется с помощью системы счетно-решающих устройств IBM 1130, которые обслуживаются одним оператором. Система имеет два массива информации: первый содержит данные о местонахождении каждого поддона на складе, второй - о спецификации грузов. Сведения о поступающих на склад грузах передаются до прибытия автомобилей, доставляющих грузы с предприятий. Полученная информация обрабатывается на IBM 1130, и выдается команда, устанавливающая номер погрузочно-разгрузочной платформы для разгрузки автомобиля и место размещения груза на стеллажах. Составляются 2 копии команды: одна для центрального пульта, где расположена система IBM 1130, а другая для передачи по пневмопочте на склад.
На складе на груз наносится маркировка, включающая номер прохода, номер ряда вдоль прохода и номер яруса, где должны размещаться грузы. С разгрузочной платформы грузы, согласно маркировке, передаются 28 рольгангами (длиной по 4,9 м) к стеллажам типа Speed lock. Каждый стеллаж имеет длину 80,2 ми высоту 1 1,7 м с полками на уровне 0,46; 2,67; 4,88; 7,09; 9,30 м. Все стеллажи разбиты на 4 зоны, каждая из которых обслуживается одним вилочным погрузчиком Ameise ETX грузоподъемностью 770 кг с четырехкратно выдвижной мачтой, обеспечивающей высоту подъема груза до 9,6 м. На погрузочно-разгрузочных платформах склада работают погрузчики Hestair Sherpa Pegs грузоподъемностью 950 кг с высотой подъема груза 3,3 м. Эти погрузчики чрезвычайно маневренны и свободно работают внутри большегрузных контейнеров. Отобранные со стеллажей грузы погрузчиками ЕТХ передаются на пластинчатые конвейеры, которые доставляют их к погрузочно-раз 12 это устройство обеспечивает перемещение поддона грузочным платформам. Все 8 платформ имеют гидравлический привод, обеспечивающий установку платформы на уровне пола. Стеллажи новых типов разработаны в ФРГ. Стеллажи пола подвижного состава [116].
Стеллажи Optaur предназначены для складирования поддонов и тяжеловесных грузов. Горизонтальные несущие балки стеллажей скрепляются с вертикальными рамами штекерным соединением и могут быть в любой момент переставлены выше или ниже с шагом 75 мм. Конструкция штекерного узла такова, что с увеличением нагрузки увеличивается его жесткость. Выбор несущих балок зависит от ожидаемых нагрузок. Максимально допустимая нагрузка на две балки составляет 5,6 т. Обслуживание стеллажей осуществляется вилочным электропогрузчиком с выдвижной стрелой Стеллажи Multirack состоят из двух элементов - вертикальных опор и продольных связей. Соединение их осуществляется без винтов и других соединительных деталей. Опоры стеллажей свариваются в виде лестницы из поперечных и диагональных элементов U-образного профиля, в нижней части к ним привариваются опорные плиты так, что нагрузка на пол не превышает допустимых норм.
Предусмотрена перестановка полок через 100 мм. У стеллажей Hubertus вертикальные стойки каркасной конструкции сварены из Т-образного стального профиля, устойчивого против скручивания; допустимая нагрузка на одну стойку 12 т. Безвинтовое соединение позволяет легко переставлять горизонтальные полки по высоте через 100 мм. Фиксирующие шпильки исключают снятие полок вилочным погрузчиком. Одноместные и многоместные стеллажи, предназначенные для поддонов размерами 800х 1200 мм и 1000 х 1200 мм, составляют из элементов при помощи шлицевых соединений, обеспечивающих большую жесткость конструкции. Вертикальные несущие рамы из коробчатого сечения стеллажей Kombifix при весе 25 - 40 кг обеспечивают нагрузку 14 т при двойном запасе прочности. Безвинтовое соединение позволяет быстро собирать, разбирать и переставлять стеллажи через 60 мм [117].
На трубном заводе фирмы Detroit Tube Products (США) создан склад готовой продукции, в котором используются стеллажи, оборудованные специальными пневмокамерами, способными создать некоторый воздушный зазор между полом и опорной поверхностью стеллажа, что допускает его легкое перемещение. Система разработана фирмой Palmer-Shile. На новом складе полностью отпадает необходимость во внутрискладских проходах, благодаря чему резко возрастает коэффициент использования емкости хранилища. В стационарном положении стеллаж опирается своей жесткой нижней плоскостью на пол складского помещения. При подаче сжатого воздуха в надувные пневмокамеры, расположенные под опорной поверхностью стеллажа, последний (порожний или с грузом) несколько приподнимается над полом.
В надувных пневмокамерах предусмотрены мельчайшие отверстия, и по мере увеличения давления нагнетаемого воздуха он начинает выходить через указанные отверстия, чему способствует наличие мелких канавок в поверхности пола. В конечном счете под пневмокамерами создается тонкая воздушная прослойка или воздушная пленка, ликвидирующая жесткий контакт между опорой поверхностью стеллажа и полом. Такой стеллаж легко перемещается в любом направлении при приложении сравнительно небольшого горизонтального усилия. Упругие пневмокамеры способны изменять свою форму в соответствии с неровностями поверхности пола, при этом воздушная пленка под ними сохраняется. Величина усилия, необходимого для перемещения груза, зависит от веса груза, степени неровности поверхности пола и требуемой скорости перемещения груза. Для трогания груза с места необходимо большее усилие, чем при его последующем перемещении. Если усилия одного человека недостаточно и привлечение дополнительного персонала нежелательно, процесс перемещения можно механизировать [118].
Фирма Fagel в Женеве построила за 1968 - 1969 гг. механизированный склад общей площадью 4000 м2 для обработки и хранения 4000 наименований фармацевтической продукции. Склад состоит из административного корпуса и складских помещений площадью 2800 м2, где размещены упаковочный, экспедиционный и складской участки. На складском участке размером 44 x 20 х 17 м и площадью 880 м^ установлены 5 двухсторонних стеллажей башенного типа шириной 1,4 м высотой 17 м. Каждая башня имеет 11 полок и по 38 ячеек на каждой стороне полки. Все 5 башен вмещают 4180 поддонов. Размер поддонов 800 х 1200 х 1300 мм, грузоподъемность 800 кг, суточный грузооборот склада 30 т в сутки.
При поступлении поддонов на склад фотоэлемент контролирует их размер. Нестандартные поддоны автоматически направляются на запасной ленточный конвейер. Каждой ячейке башни соответствует пластмассовая адресная перфокарта, которую оператор вводит в считывающее устройство ЭВМ. По команде ЭВМ срабатывают исполнительные механизмы телескопического вилочного захвата и штабелирующего крана, которые укладывают поддоны в любую свободную ячейку. На складе заняты 1 оператор, 9 укладчиков, 12 упаковщиков и 3 агента. На складе эксплуатируется автоматическая противопожарная система, оснащенная детектором дыма, кнопками сигналов тревоги и огнетушителями, которые управляются дистанционной городской пожарной службой [119].
|
|