|
1.3. Построение алгоритма диагностирования
При организации технологического процесса диагностирования ставится задача рациональной минимизации числа контрольно-измерительных операций, повышения точности измерения диагностических параметров и соответственно достоверности постановки диагноза. При этом должно соблюдаться общее условие минимизации издержек на эксплуатацию, обслуживание и ремонт диагностируемого объекта с сохранением на должном уровне коэффициента готовности автомобильного парка.
Как указывалось выше, техническое диагностирование направлено на решение трех основных задач: определение работоспособности объекта, выявление и локализацию отказа и неисправности, определение остаточного ресурса. Каждому из трех случаев соответствует определенный методический подход, обеспечивающий построение своего оптимального алгоритма диагностирования.
Построению алгоритма диагностирования предшествует анализ статистических данных на наиболее часто повторяющиеся неисправности и отказы. На основе данных анализа разрабатывают блок-схемы структурно-следственных связей по цепи: диагностируемый объект (автомобиль) - агрегат - система, механизм, узел - элемент - структурный параметр - неисправность - внешний признак (симптом) - диагностический параметр. Число звеньев в цепи в каждом конкретном случае (применительно к различным системам и агрегатам) может меняться. Каждое звено определяет задаваемый уровень поиска или технологического шага, направленного на установление неисправности. Например, в приведенной на рис. 1.4 цепи их девять:
первый (высший) уровень поиска предусматривает определение общего технического состояния автомобиля;
второй уровень поиска включает в себя контроль основных агрегатов и систем автомобиля (двигателя, ходовой части, тормозной системы, системы рулевого управления и др.);
на третьем уровне осуществляют поиск неисправностей по узлам, механизмам и системам отдельных агрегатов (на примере двигателя - это кривошипно-шатунный механизм, цилиндропоршневая группа, системы смазывания, питания и др.);
четвертый уровень соответствует контролю основных узлов, из которых состоит диагностируемый механизм (в отдельных случаях агрегат) или система. Применительно к системе зажигания - это аккумуляторная батарея, реле-регулятор, распределитель зажигания, катушка зажигания, свечи зажигания и др.;
на пятом уровне контролируют сопряжения и элементы узлов и агрегатов, по которым в процессе эксплуатации наблюдается наибольшее число отказов и неисправностей;
шестому уровню соответствует контроль структурных параметров, определяемых на основе анализа статистических данных и с учетом критериев эксплуатационной надежности;
на седьмом уровне контролируют возможные неисправности изделий и сопряжений;
на восьмом уровне устанавливают перечень внешних признаков, проявлением которых определяется каждая конкретная неисправность;
на девятом уровне определяют предварительный перечень всех возможных диагностических параметров, из которых выбирают наиболее информативные и технологичные в измерении.
Взаимосвязь структурных и диагностических параметров автомобиля в общем виде может быть представлена блок-схемой (рис. 1.5), где все системы и агрегаты автомобиля разделены на две группы (возможны и другие классификации). Первая группа состоит из систем, обеспечивающих безопасность движения (ОБД), а вторая - содержит остальные функциональные системы (ФС). Каждая группа включает в себя определенно число ρ агрегатов и систем из общей их совокупности R. Техническое состояние каждого агрегата (системы) характеризуется каким-то набором n≤N диагностических параметров, где N - общее число диагностических параметров, характеризующих состояние автомобиля, его отдельных агрегатов и систем. Каждый из j-x диагностических параметров зависит от значений соответствующих им j-x структурных параметров m≤М, где М - общее число структурных параметров, характеризующих состояние автомобиля, его отдельных агрегатов и систем.
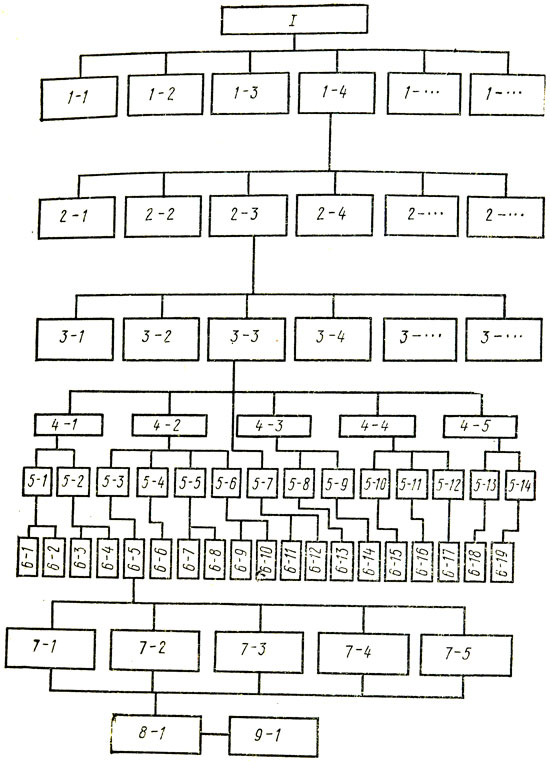 Рис. 1.4. Блок-схема структурно-следственных связей: 1 - автомобиль; 1-1 - ходовая часть, 1-2 - коробка передач, 1-3 - тормозная система, 1-4 - двигатель, 1-2-1 - кривошипно-шатунный механизм, 2-2 - цилиндро-поршневая группа, 2-3 - система зажигания, 3-3 - распределитель зажигания, 3-4 - высоковольтные провода, 3 - ..., 4-1 - распределитель, 4-2 - прерыватель, 4-3 - центробежный регулятор, 4-4 - вакуумный регулятор, 4-5 - октан-корректор, 5-1 - крышка распределителя - уголек, 5-2 - ротор - пружина уголька, 5-3 - подвижный контакт - неподвижный контакт, 5-4 - регулировочный экспентрик - пластина неподвижного контакта с винтом крепления, 5-5 - пятка рычага подвижного контакта - втулка с кулачком и пластиной в сборе, 5-6 - рычаг подвижного контакта-пружина, 5-7 - приводной валик - втулка приводного валика, 5-8 - грузики в сборе-пружины центробежного автомата, 5-9 - штифт поворота - грузики в сборе, 5-10 - регулировочная шайба - пружина, 5-11 - шайба диафрагмы - диафрагма, 5-12 - тяга с пластиной прерывателя - шарикоподшипник, 5-13 - эксцентрик - пружина эксцентрика, 5-14 - эксцентрик - ось эксцентрика, 6-1 - сопротивление уголька, 6-2 - полное сопротивление изоляции крышки, 6-3 - полное сопротивление изоляции ротора, 6-4 - упругость пружины под номинальной нагрузкой, 6-5 - геометрическая форма и чистота поверхности контакта, 6-6 - зазор между контактами, 6-7 - геометрическая форма пятки, 6-8 - геометрическая форма кулачка, 6-9 - зазор в сопряжении ось - рычаг, 6-10 - упругость пружины, сила прижатия контактов, 6-11 - лифт приводного валика, 6-12 - угол поворота распределителя относительно нормального положения, 6-13 - упругость и длина пружины, 6-14 - зазор между осью грузовиков и пластиной регулятора, 6-15 - упругость пружины, длина пружины при номинальной нагрузке, 6-16 - герметичность регулятора, 6-17 - люфт, 6-18 - упру, гость пружины, 6-19 - зазор в сопряжении ось - эксцентрик, 7-1 - износ контактов, 7-2 - эрозия контактов, 7-3 - подгорание контактов, 7-4 - окисление контактов, 7-5 - замасливание контактов, 8-1 - измерение сопротивления контактов, 9-1 - падение напряжения на контактах
Алгоритм диагностирования строится таким образом, чтобы по выбранному перечню параметров и последовательности их измерения определить работоспособность объекта и локализовать выявленные при этом неисправности. Глубина локализации неисправности определяется в каждом конкретном случае своим уровнем: заменой детали, заменой или ремонтом узла или агрегата, проведением каких-то регулировочных работ. Этот уровень определяется эксплуатационными и экономическими факторами, нормируемыми показателями надежности, требованиями обеспечения безопасности дорожного движения, сохранения экологических характеристик и т. д.
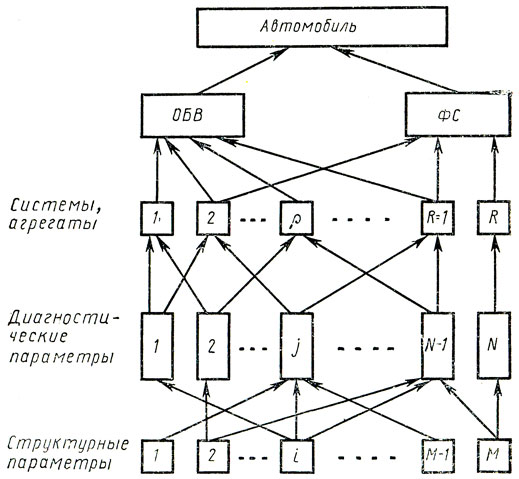 Рис. 1.5. Взаимосвязь структурных и диагностических параметров
Заключительными этапами построения алгоритма диагностирования является разработка базовой и комплексной маршрутных технологий. В основу построения алгоритма закладываются задачи статистического моделирования и в первую очередь условие альтернатив. На рис. 1.6 показан пример построения алгоритма диагностирования и процедуры (частично) принятия решения.
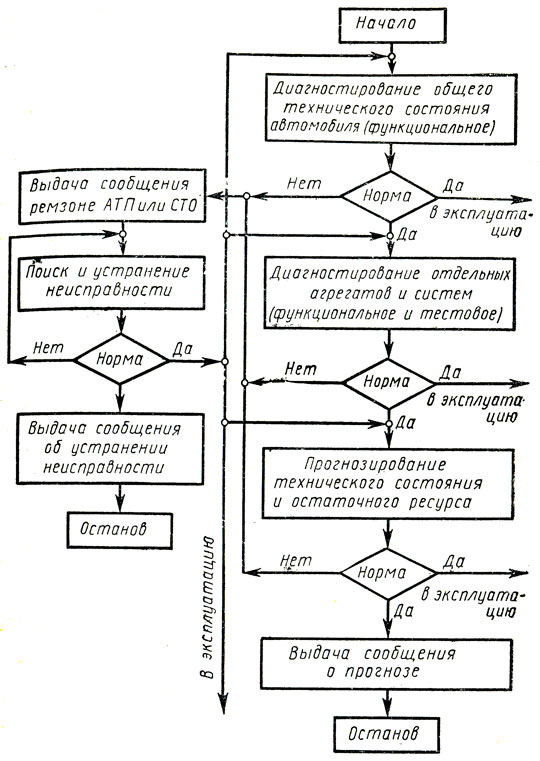 Рис. 1.6. Модельный пример алгоритма диагностирования
|
|