§ 5. Техническое обслуживание систем питания двигателей
В современных быстроходных автомобильных двигателях, имеющих высокие степени сжатия, времени на сгорание рабочей смеси чрезвычайно мало, вследствие чего предъявляются высокие требования к работе приборов системы питания.
Усовершенствования системы питания двигателей направлены на улучшение качества очистки топлива и воздуха, обеспечение равномерного распределения горючей смеси по цилиндрам, на изменения в конструкции насосов, карбюраторов и форсунок, обусловливающие вероятность безотказной работы систем питания, а также повышающие срок службы, мощность и экономичность двигателей
Применение для карбюраторных двигателей герметизированных, топливных насосов повышенной производительности и двухкамерных карбюраторов, а для четырехтактных дизельных двигателей топ-ливоподающей аппаратуры разделенного типа требует высококачественного выполнения всех операций по техническому обслуживанию систем питания двигателей.
Техническое обслуживание системы питания карбюраторных двигателей
Неисправности в системе питания карбюраторных двигателей в большинстве случаев приводят к нарушению состава горючей смеси и подтеканию топлива.
К нарушению состава горючей смеси следует отнести чрезмерное обеднение или обогащение ее.
Чрезмерное обогащение горючей смеси вызывается следующим: слишком высоким уровнем топлива в поплавковой камере карбюратора вследствие неправильной его регулировки и неплотного закрытия игольчатого клапана или повреждения поплавка; износом калиброванных отверстий топливных жиклеров и засорением воздушных жиклеров карбюратора; неплотным закрытием клапанов экономайзера или ускорительного насоса; неполным открытием воздушной заслонки карбюратора; засорением воздушного фильтра при нарушении действия системы балансирования поплавковой камеры карбюратора.
Чрезмерное обеднение горючей смеси может быть вызвано слишком низким уровнем топлива в поплавковой камере карбюратора из-за неправильной его регулировки, засорением топливных жиклеров, подсосом воздуха в соединения карбюратора, а также уменьшением подачи топлива к карбюратору вследствие заедания воздушного клапана пробки бака, засорением топливопроводов, фильтров и отстойников, неисправностями топливного насоса, подсосом воздуха в топливопроводах и соединениях приборов питания.
При переобеднении горючей смеси и малой скорости ее горения появляются вспышки во впускном трубопроводе, двигатель перегревается, снижаются его мощность и приемистость, увеличивается расход топлива. При переобогащении смеси и вследствие неполного ее сгорания появляются выстрелы в глушителе, отработавшие газы становятся темными, на деталях цилиндро-поршневой группы и зажигательных свечах образуется значительное отложение нагара, возникают перегрев и перебои в работе двигателя, мощность его падает, расход топлива увеличивается.
Техническое обслуживание предусматривает выполнение следующих работ по системе питания:
при ЕО - проверка герметичности системы питания, уровня топлива в баке и заправка топливом;
при ТО-1 - проверка осмотром состояния всех приборов системы, крепления и действия приводов управления дросселем и воздушной заслонкой карбюратора, промывка воздушного фильтра и смена в нем масла при работе по пыльным дорогам; выпуск отстоя из топливных фильтров;
при ТО-2- проверка крепления всех приборов, работы топливного насоса (без снятия с двигателя), уровня топлива в поплавковой камере карбюратора, промывка топливных фильтров и очистка отстойника насоса, промывка воздушного фильтра и смена в нем масла; проверка легкости пуска и работы двигателя, а при необходимости - расхода топлива; два раза в год - разборка и очистка карбюратора, регулировка в соответствии с наступающим сезоном эксплуатации подогрева горючей смеси во впускном трубопроводе, промывка и проверка ограничителя числа оборотов коленчатого вала двигателя, выпуск отстоя из топливного бака; один раз в год - проверка рабочих деталей карбюратора; при подготовке к осенне-зимнему периоду эксплуатации: разборка, очистка и проверка работы топливного насоса, промывка топливного бака.
Обслуживание карбюраторов. Надежность в работе карбюратора достигается выполнением следующих операций.
Очистка и промывка карбюратора. Карбюратор снимают с двигателя и разбирают, удаляют смолистые отложения, промывают детали с помощью волосяной кисти в ванночке с авиационным бензином или ацетоном, продувают жиклеры и каналы в корпусе сжатым воздухом. Запрещается применять для прочистки жиклеров проволоку, металлические предметы или обтирочные материалы. При работе на этилированном бензине перед очисткой деталей карбюратора их необходимо погрузить на 10 - 20 мин в керосин или другой растворитель. При сборке карбюратора следует проверить состояние всех прокладок и негодные заменить. Во избежание порчи поплавка не допускается продувка собранного карбюратора сжатым воздухом через топливоподводящий штуцер или балансировочную трубку.
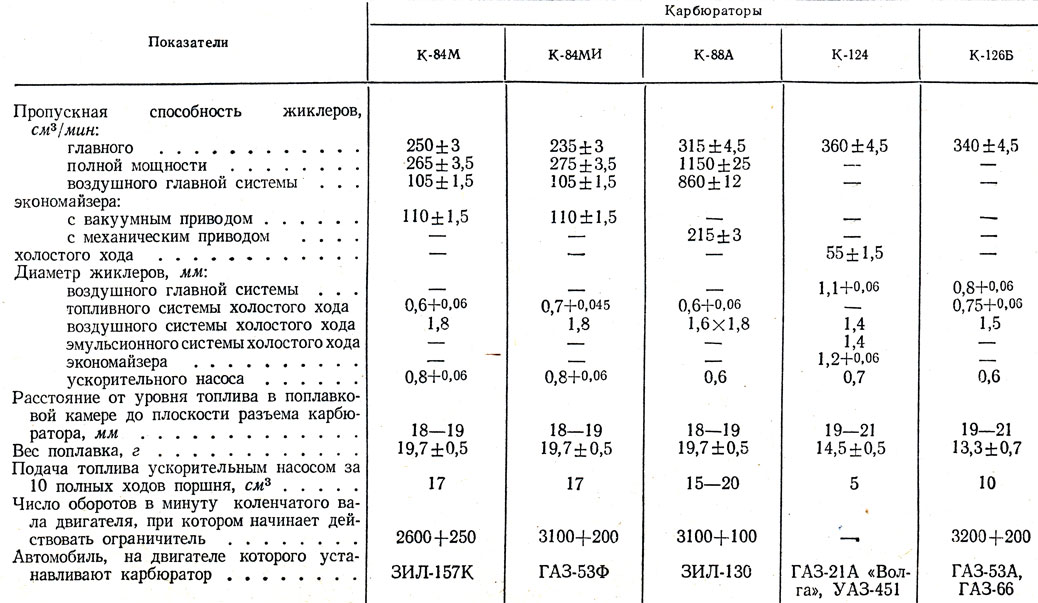 Таблица 8. Основные параметры карбюраторов
Дроссель и воздушную заслонку при разборке карбюратора не снимают. После сборки карбюратора надо убедиться в том, что они поворачиваются без заедания.
Проверка герметичности поплавка производится погружением его на 30 сек в воду, нагретую до температуры 80 - 90° С. При неисправности поплавка из него будут выходить пузырьки воздуха. Такой поплавок необходимо заменить или запаять, предварительно удалив попавшее в него топливо. После пайки проверяют вес поплавка. Если он не соответствует данным табл. 8, то необходимо удалить часть припоя.
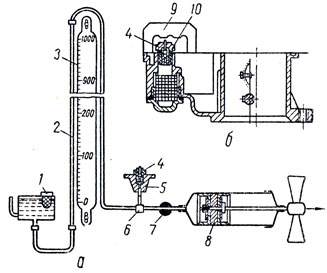 Рис. 82. Схема приспособления для проверки герметичности и правильности установки игольчатого клапана карбюратора К-88А: а - проверка герметичности; б- проверка установки
Проверка герметичности игольчатого клапана выполняется на вакуумном приборе (рис. 82, а). Бачок/ прибора заполняют дистиллированной водой, и в корпусе 5 устанавливают на прокладках испытуемый клапан в сборе с седлом 4. Затем с помощью поршня 8 насоса создают разрежение в контрольной трубке 2, подняв уровень водяного столба до 1000 мм (замеряют по шкале 3) и закрывают кран 7. Одновременно разрежение создается в тройнике 6 под испытуемым клапаном.
Герметичность клапана считается удовлетворительной, если уровень воды в контрольной трубке понизится не более, чем на 10 мм в течение 30 сек. При большем падении уровня воды клапан необходимо притереть или заменить.
В карбюраторах К-84М и К-88А установку узла запорного механизма в корпусе карбюратора проверяют шаблоном 9 (рис. 82, б) и регулируют прокладками 10.
Уровень топлива в поплавковой камере можно проверить не снимая карбюратор с двигателя или установив карбюратор на специальном приборе.
Для проверки уровня топлива используют принцип сообщающихся сосудов. С этой целью в отверстие спускной пробки (карбюраторы К-82М, К-88 и К-88А) ввертывают штуцер с трубкой, которая соединена с контрольной стеклянной трубкой. Расстояние от уровня топлива в поплавковой камере карбюратора до плоскости разъема его корпуса должно соответствовать данным таблицы 8.
В некоторых карбюраторах имеются смотровые устройства, позволяющие проверять уровень топлива в поплавковой камере во время работы двигателя на холостом ходу. Так, в карбюраторах К-124 и К-126Б уровень топлива должен находиться между рисками смотрового стекла, а в карбюраторах К-84М, К-88 и K-88A - совпадать с нижним краем контрольного отверстия (пробку из отверстия вывертывают) и не вытекать из него.
Проверка уровня топлива в поплавковой камере снятого с двигателя карбюратора и его герметичности под давлением 19613,3 н/м2 (0,2 кГ/см2 ) может быть произведена на приборе модели 355 (рис. 83). В карбюратор, закрепленный на кронштейне 7, топливо поступает из бачка 12 по трубке 3 и шлангу 2 под давлением воздуха, нагнетаемого через корпус 11 с обратным клапаном. Дазление топлива контролируют по манометру 1, а уровень топлива в поплавковой камере по трубке 6. Герметичность карбюратора проверяют по отсутствию подтеканий в его соединениях. Существует также комбинированный прибор (модель 577) для проверки карбюраторов и топливных насосов.
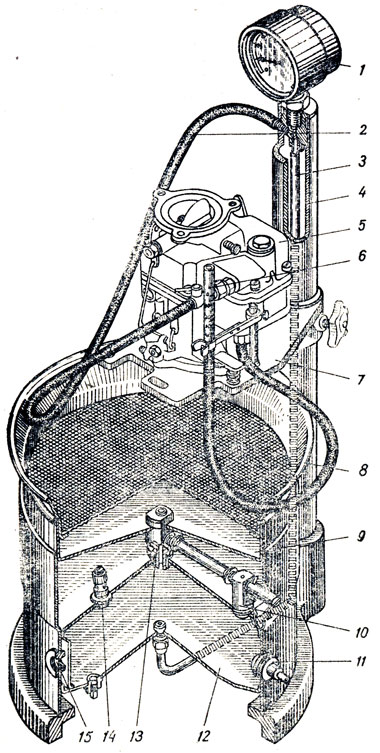 Рис. 83. Прибор для проверки карбюраторов: 1 - манометр; 2 - шланг для подачи бензина к карбюратору; 3 - трубка для подачи бензина от бачка прибора к карбюратору; 4 - колонка; 5 - испытуемый карбюратор; 6 - стеклянная трубка для проверки уровня топлива в поплавковой камере карбюратора; 7 - кронштейн для установки карбюратора; 8 - корпус с фильтрующей сеткой; 9 - ванночка для заливки бензина; 10 - кран для сообщения с атмосферой; 11 - корпус с обратным клапаном для накачки воздуха в бачок; 12 - бачок; 13 - кран для подачи бензина в ванночку; 14 - корпус предохранительного клапана; 15 - смотровое окно
Регулировка уровня топлива в карбюраторах К-84М и К-88А осуществляется изменением числа регулировочных прокладок под седлом игольчатого клапана. Если при правильной установке узла запорного механизма уровень топлива не будет доведен до нормального, то регулировку производят, подгибая вниз кронштейн поплавка при высоком уровне топлива и вверх - при низком.
В карбюраторах К-124 и К-126Б уровень топлива регулируют подгибанием язычка на рычажке поплавка.
В карбюраторе К-126Б ход поплавка должен обеспечить ход игольчатого клапана не менее 2 мм .
В карбюраторе К-124 предварительная подгонка уровня топлива производится так, чтобы при опрокинутом положении крышки карбюратора расстояние от плоскости разъема до верха поплавка составляло 40 - 41 мм ; ход игольчатого клапана устанавливают в пределах 2 - 2,5 мм . подгибая ограничитель хода поплавка.
Проверка пропускной способности жиклеров производится один раз в год в плановом порядке, а также при очередном техническом обслуживании автомобиля в случае выявления перерасхода топлива.
Пропускная способность жиклеров определяется количеством дистиллированной воды (в см3), протекающей через дозирующее отверстие жиклера за 1 мин под напором водяного столба высотой 1 ± 0,002 м при температуре воды 20 ± 1С. Проверка (тарировка) жиклеров производится на приборах, которые по принципу замера количества воды подразделяются на две группы: с абсолютным и относительным замером.
В приборе (рис. 84) с абсолютным замером пропускной способности жиклеров воду заливают в ванночку 2, откуда вода поступает в нижний бачок 1, а затем в напорный бачок 9 под давлением воздуха, нагнетаемого в бачок 1 ручным насосом через кран 14. Уровень воды в напорном бачке определяют с помощью-стеклянной трубки 10.
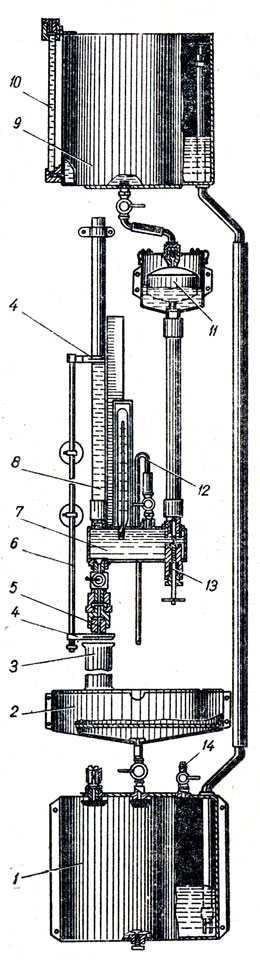 Рис. 84. Проверка пропускной способности жиклеров карбюратора на приборе с абсолютным замером расхода воды
Испытуемый жиклер 5 устанавливают под переходным бачком 7, в который поступает вода через поплавковое устройство 11 и игольчатый клапан 13. Для выхода воздуха при заполнении бачка служит трубка 12. Поплавковое устройство поддерживает постоянство напора воды над проходным отверстием, регулируемым клапаном 13. Постоянный уровень воды на высоте 1 м устанавливается в напорной трубке 8 с помощью клапана 13 при истечении воды через жиклер 5. Замер величины столба жидкости производят подвижной штангой 6, нижний указатель 4 которой устанавливают под торец испытуемого жиклера 5, а верхний - показывает уровень воды.
После регулировки величины напора воды под испытуемый жиклер устанавливают мензурку 3 и открывают кран переходного бачка 7. При этом по секундомеру или песочным часам измеряют время (t сек) истечения воды через жиклер, по мензурке определяют общий расход воды (Q см3) за время испытания и подсчитывают пропускную способность жиклера (q см3/мин):
В приборе с относительным замером пропускной способности жиклеров шкала мерного цилиндра градуирована так, что по ее делениям определяют пропускную способность жиклера (см3/мин) при напоре водяного столба высотой 1м, несмотря на то что действительный напор воды в приборе равен 600 мм .
Пропускная способность жиклера определяется как средняя величина двух-трех замеров. Направление струи воды в жиклере должно совпадать с направлением протекания топлива через жиклер в карбюраторе. Перед проверкой жиклеры следует промыть в ацетоне и продуть сжатым воздухом.
Размеры некоторых жиклеров приводятся в заводских инструкциях в миллиметрах. Для определения диаметра проходных отверстий таких жиклеров используют калибровочные (швейные) иглы.
Регулировка момента включения клапана экономайзера с механическим приводом осуществляется после разборки карбюратора. В карбюраторе К-126Б при полностью открытых дросселях вилка ускорительного насоса 3 (рис. 85, а) должна повернуться так, чтобы расстояние от верхней плоскости крышки поплавковой камеры до ролика вилки привода было равно 21,5 мм , а зазор между планкой привода ускорительного насоса и экономайзера и регулировочной гайкой штока экономайзера - 3 мм .
В карбюраторах двигателей ЗИЛ экономайзер должен включаться при следующих значениях расстояния между кромкой дросселя и стенкой смесительной камеры: 14,6 мм для карбюратора К-82М; 11,2 мм - для К-84М, К-88А и К-89А.
В последних двух моделях карбюраторов эта регулировка достигается с помощью гайки 5 (см. рис. 85, б), а в остальных - подгибанием планки 6 иной конструкции.
Проверка и регулировка приводов дросселя и воздушной заслонки карбюратора. Приводы дросселя и воздушной заслонки должны работать без заедания и обеспечивать возможность полного открывания и плотного закрывания заслонок.
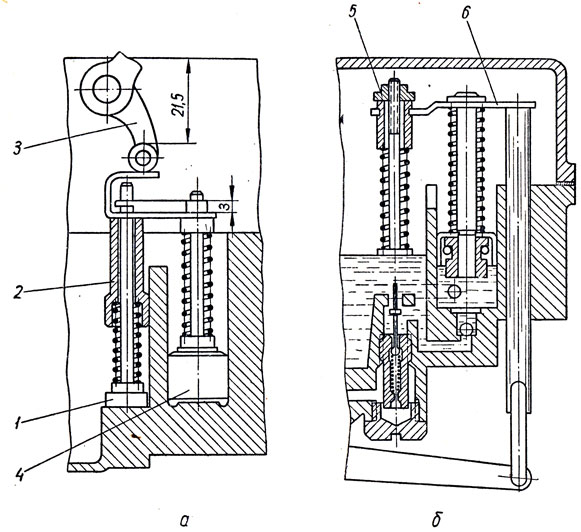 Рис. 85. Регулировка момента включения клапана экономайзера с механическим приводом: а - карбюратора К-126Б; б - карбюратора К-88А; 1 - клапан экономайзера; 2 - направляющая привода экономайзера; 3 - вилка привода; 4 - ускорительный насос; 5 - регулировочная гайка; 6 - планка
Ножной привод дросселей карбюратора К-88А регулируют с помощью резьбовых наконечников на тяге карбюратора и резьбовой тяги педали управления дросселями. При полном открытии дросселей педаль не должна доходить до пола кабины на 3 - 5 мм . Ход педали должен составлять не менее 160 мм . Кнопку ручного привода дросселей вдвигают до отказа, затем на конце троса привода укрепляют зажим так, чтобы между ним и кронштейном, укрепленным на тяге, оставался зазор 2 - 3 мм .
Кнопку привода воздушной заслонки устанавливают с зазором 2 - 3 мм до щитка приборов и при полностью открытой заслонке соединяют трос с рычагом заслонки, а затем закрепляют оболочку троса в зажиме. Аналогично регулируют приводы управления другими карбюраторами.
Шарнирные соединения деталей привода и оболочки тросов смазывают моторным маслом при ТО-2, а резиновые втулки валика привода дросселя смазывают тормозной жидкостью.
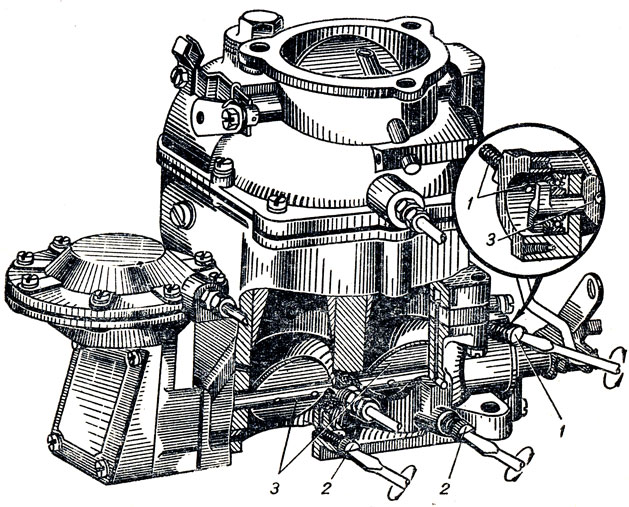 Рис. 86. Регулировка карбюратора К-88А на малые обороты холостого хода двигателя: 1 - упорный винт привода дросселей; 2 - винт регулировки количества эмульсии, поступающей в смесительную камеру; 3 - дроссели
Регулировка карбюратора на малые обороты холостого хода двигателя должна обеспечивать устойчивую работу двигателя на минимальных оборотах коленчатого вала и возможность резкого изменения режима работы двигателя. Эта регулировка производится на прогретом двигателе при правильно установленном зажигании, при нормальных зазорах между электродами свечей, контактами прерывателя и исправном состоянии приборов системы питания.
Количество подаваемой горючей смеси регулируют упорным винтом 1(рис. 86) оси привода дросселей 5. При завертывании винта количество подаваемой смеси и обороты коленчатого вала двигателя увеличиваются, при отвертывании - уменьшаются.
Качество подаваемой горючей смеси регулируют двумя (в двухкамерном карбюраторе) винтами 2. При отвертывании винтов смесь обогащается, при завертывании - обедняется.
При регулировке вначале завертывают винты 2 до упора, а затем отвертывают их на два-три оборота; запускают двигатель и винтом 1 устанавливают наименьшее устойчивое число оборотов коленчатого вала двигателя; после этого один из винтов 2 завертывают на 1/4 оборота до появления перебоев в работе двигателя, а затем отвертывают на 1/2 оборота и повторяют эти операции для второй смесительной камеры карбюратора; отвертывая винт 1, уменьшают число оборотов холостого хода, сохраняя устойчивую работу двигателя, а затем поворотом винтов 2 увеличивают их соответственно новому положению упорного винта 1.
Последовательно проводя указанные операции, находят наивыгоднейшее положение винтов, обеспечивающее наименьшие устойчивые обороты коленчатого вала двигателя. Обе секции карбюратора должны быть одинаково отрегулированы. Проверку регулировки производят резким открытием дросселей и быстрым прикрытием их, при этом двигатель не должен глохнуть. Если двигатель перестает работать, надо несколько увеличить число оборотов, ввернув упорный винт, а затем снова проверить правильность регулировки.
Индивидуальная регулировка карбюратора. Топливная экономичность автомобиля может быть улучшена путем наивыгоднейшей индивидуальной регулировки карбюратора. Проверка расхода топлива производится различными методами: контрольными пробегами по определенному маршруту (протяженностью 5 - 10 км), характерному для обычных условий эксплуатации данного автомобиля; пробегом автомобиля с постоянной скоростью на коротком мерном (1 км) участке пути; на стенде с беговыми барабанами.
Первый метод является в настоящее время наиболее употребительным. Заезды должны проводиться в обе стороны. Питание двигателя во время испытания осуществляется из соединенного с топливным насосом мерного бачка со стеклянной трубкой и шкалой, показывающими расход топлива. Перед контрольным пробегом двигатель и все агрегаты автомобиля доводят до нормального теплового состояния и проверяют правильность установки опережения зажигания.
Первый контрольный пробег проводят при существующей регулировке карбюратора, а по количеству израсходованного топлива и пройденному пути (по спидометру) подсчитывают расход топлива в литрах на 100 км. Затем проводят ряд пробегов, последовательно уменьшая размер главного жиклера по производительности на 5 - 10 см3/мин, пока не будет определен жиклер, обеспечивающий наименьший расход топлива при сохранении динамических качеств автомобиля.
Мерный участок выбирают на ровной дороге с малым движением. Автомобиль разгоняют до определенной скорости (40 - 60 км/ч), на которой и проходят весь участок, определяя при этом расход топлива.
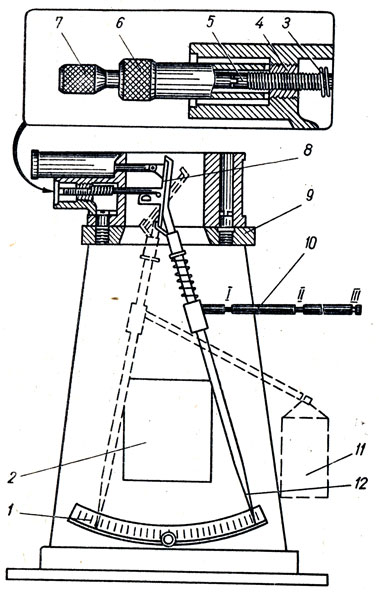 Рис. 87. Регулировка ограничителя (пневматического типа) числа максимальных оборотов коленчатого вала двигателя
Указанные методы неприемлемы для крупных автохозяйств. В последних применяют посты диагностики, оборудованные стендами с беговыми барабанами, с помощью которых можно имитировать дорожные и нагрузочные условия работы автомобиля.
Проверка и регулировка ограничителей максимальных оборотов коленчатого вала двигателя. В процессе эксплуатации автомобиля пружина ограничителя оборотов пневматического типа частично теряет упругость, вследствие чего он срабатывает раньше, и максимальная скорость автомобиля снижается. Для проверки ограничитель после промывки устанавливают на монтажной площадке 9 (рис. 87) и к заслонке 8 ограничителя крепят стрелку 12, имеющую плечо 10. Затем перемещают шкалу 1 так, чтобы конец стрелки совпадал с нулевым делением. Упругость пружины 3 ограничителя проверяют по величине отклонения стрелки 12 при подвешивании на места заточки плеча 10 груза 11 весом в 100 г. При проверке ограничителя карбюратора К-22Г груз подвешивают поочередно на заточки Ι и ΙΙΙ, а при проверке ограничителя карбюраторов К-82М и К-84М - на заточки ΙΙΙ и ΙΙ. Полученные данные сравнивают с данными таблицы 2, укрепленной на корпусе прибора. Регулировку производят изменением натяжения пружины 3 при помощи отвертки 7, вращающей винт 5 грубой регулировки, и пустотелой отвертки 6, которой поворачивают гайку 4 тонкой регулировки ограничителя.
При ТО-2 рекомендуется промыть ограничитель пневматического типа в неэтилированном бензине или ацетоне. Кроме того, в ограничителе карбюратора К-82М следует заменить в корпусе войлочный фильтр, через который вакуумный механизм ограничителя сообщается с атмосферой.
В ограничителе центробежно-вакуумного типа на специальном приборе регулируют ротор центробежного датчика. Ротор 6 (рис. 88) приводят во вращение с помощью электродвигателя 9 с плавно изменяющимся числом оборотов вала, которое измеряют тахометром. Внутренняя полость ротора через тройник соединена с вакуумным насосом и ртутным манометром 5, в корпус которого вмонтированы проводники, идущие к контрольным лампочкам 1 конца и 2 начала срабатывания ограничителя. При включении электродвигателя одновременно включается вакуумный насос. Плавно увеличивая скорость вращения ротора, по тахометру наблюдают, при каком числе оборотов ротора за счет увеличения разрежения включатся лампочки. Если ротор настроен правильно, то начало ср абатывани я огр аничител я произойдет при
(1600 - 1700 об/мин )· |
π |
рад/сек, |
|
30 |
а конец срабатывания при
(1725 - 1825 об/мин )· |
π |
рад/сек |
|
30 |
(ротор вращается в два раза медленнее коленчатого вала). Регулируют ограничитель, вращая отверткой винт 7, изменяющий натяжение пружины 12. Вращение винта по часовой стрелке увеличивает, а против часовой стрелки уменьшает число оборотов, при котором ограничитель срабатывает.
При ТО-2 необходимо смазать втулку ротора центробежного датчика моторным маслом, залив в масленку несколько капель.
 Рис. 88. Регулировка ограничителя (цен-тробежно-вакуумного типа) числа максимальных оборотов коленчатого вала двигателя: 1 - контрольная лампочка конца срабатывания; 2 - контрольная лампочка начала срабатывания; 3 - ртутный манометр; 4 - кран; 5 - корпус прибора; 6 - ротор; 7 -регулировочный винт; 8 - валик привода ротора; 9 - электродвигатель; 10 - седло клапана; 11 - клапан датчика; пружина
Обслуживание топливных насосов. Надежная подача топлива к карбюратору на различных режимах работы двигателя может быть нарушена вследствие повреждения диафрагмы топливного насоса, потери упругости ее пружины, осмоления и залипания клапанов, загрязнений фильтрующей сетки и потери герметичности насоса.
В насосах, имеющих стакан-отстойник, возможно подтекание топлива через прокладку между корпусом и стаканом-отстойником. Если течь не прекратится после более плотной затяжки барашка крепления, необходимо сменить прокладку.
Подтекание топлива наружу из отверстия корпуса насоса или при отвертывании контрольной пробки в корпусе у герметизированных насосов указывает на порчу диафрагмы, которую следует заменить.
Наиболее простой способ проверки работы насоса без снятия его с двигателя - с помощью ручной подкачки. Исправный насос должен бесперебойно подавать сильную пульсирующую струю топлива без пены из штуцера насоса, отсоединенного от топливопровода, идущего к карбюратору. Наличие пены свидетельствует о подсосе воздуха в магистрали.
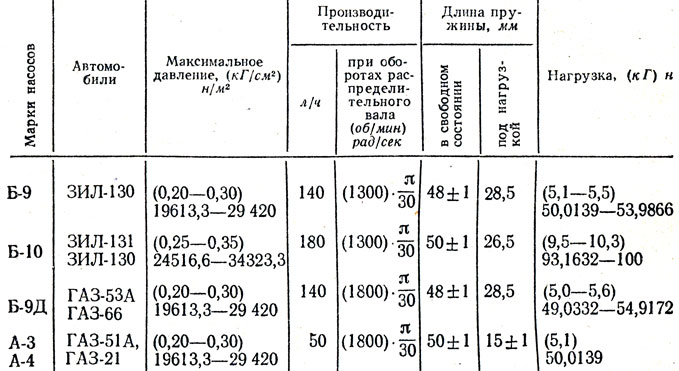 Таблица 9. Некоторые данные по топливным насосам
Более точный способ проверки - с помощью манометра, который непосредственно соединяют с топливопроводом, отсоединенным от карбюратора, или присоединяют к насосу с помощью тройника. Исправный насос при работе прогретого двигателя на малых оборотах должен развивать установленное давление (табл. 9).
После проверки давления можно проверить герметичность насоса. Для этого, выключив двигатель, следят по манометру за падением давления. При исправных клапанах насоса падение давления за 30 сек не должно превышать (0,1 кГ/см2 ) 9806,65 н/м2.
Очистка насоса А-3 заключается в снятии стакана-отстойника и сетчатого фильтра и промывке их в неэтилированном бензине. В насосах Б-9 и Б-10 для промывки сетчатого фильтра необходима частичная разборка насоса; так, в насосе Б-10 требуется снять с корпуса головку.
При значительном износе конца рычага привода нососа уменьшается ход диафрагмы и снижаются производительность насоса и создаваемое им давление. Поэтому один раз в год необходимо проверить на стенде давление впрыска, производительность и герметичность насоса.
Насос 5 (рис. 89) крепят к панели прибора (модель 374), соединяют шлангами 3 и 4 с трубками 15 и 16, приводят его в действие, вращая вручную кулачковый вал 17 до появления струи бензина в мерном цилиндре 6, затем перекрывают кран 9, направляя бензин по каналу 12 к манометру 11. После того как давление будет доведено до максимальной величины, вращение кулачкового вала прекращают и по секундомеру фиксируют падение давления за 30 сек при отжатом рычаге насоса. При этом падение давления должно быть не более (0,1 кГ/см2 ) 9806,65 н/м2.
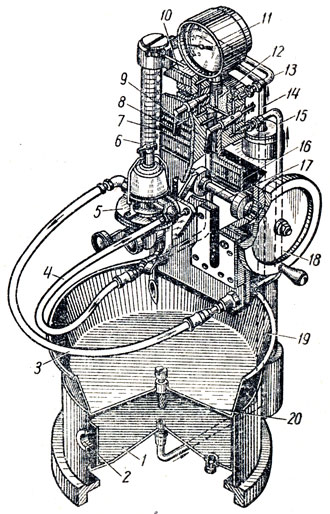 Рис. 89. Прибор для проверки топливных насосов: 1 - бачок; 2 - смотровое окно; 3 и 4 - шланги; 5 - испытуемый насос; 6 - мерный цилиндр; 7 - таблица положения кранов при различных замерах; 8 - кран впускной магистрали; 9 - кран нагнетательной магистрали; 10 - канал для сообщения с атмосферой; 11 - манометр; 12 - канал для подачи бензина к манометру; 13 - трубка для подачи бензина к мерному цилиндру; 14 - трубка для подачи бензина из ванночки к блоку кранов; 15 - трубка для подачи бензина от насоса; 16 - трубка для подачи бензина к насосу; 17 - кулачковый вал; 18 - маховичок; 19 - ванночка для заливки бензина; 20 - фильтр
Для проверки производительности насоса соединяют через кран 9 трубку 15 с мерным цилиндром 6, затем, вращая кулачковый вал со скоростью (1 об/сек) · 2π рад/сек через 10 оборотов прекращают вращение и определяют объем бензина в мерном цилиндре.
При проверке необходимого количества ходов рычага для подъема бензина на высоту 400 мм входной штуцер насоса с помощью крана 8 через канал 10 соединяют с атмосферой и вращают кулачковый вал, пока весь бензин из насоса не поступит в мерный цилиндр. Далее, соединив с помощью крана 8 входной штуцер насоса с бачком 1, перекачивают из бачка бензин по трубке 15, пока не появится струя бензина в мерном цилиндре. Количество оборотов кулачкового вала при этом должно быть не более 25.
Для заполнения бачка 1 прибора бензин заливают в ванночку 19. Емкость бачка 4 л. Уровень бензина проверяют через смотровое окно 2.
После разборки насоса все детали промывают в бензине, удаляя смолистые отложения.
Упругость пружины диафрагмы проверяют на приборе (модель 357, рис. 90) замером ее длины в свободном состоянии и под нагрузкой. Длина пружины должна соответствовать данным табл. 9. Неисправные диафрагмы, клапаны и прокладки заменяют новыми. При смене диафрагмы закреплять ее между частями корпуса следует при крайнем нижнем положении диафрагмы, в противном случае она в процессе работы будет вытягиваться больше, чем положено, и раньше срока выйдет из строя.
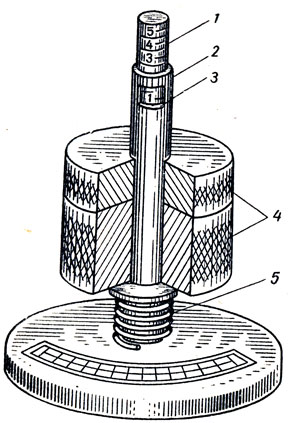 Рис. 90. Проверка упругости пру жины диафрагмы насоса: 1 - шток со шкалой; 2 - измерительная втулка; 3 - смотровое окно втулки; 4 - контрольный груз; 5 - пружина диафрагмы
Уход за воздушным фильтром. Периодичность ухода за воздушным фильтром зависит от условий эксплуатации. Уход заключается в промывке фильтра и смене масла. В обычных условиях эксплуатации эту операцию проводят при ТО-2, в тяжелых дорожных условиях - при ТО-1, а в условиях сильной запыленности воздуха - через день. Для промывки воздушный фильтр снимают с двигателя, сливают загрязненное масло из его ванны, промывают детали фильтра в керосине или бензине, затем протирают их, а фильтрующий элемент просушивают сжатым воздухом. Фильтрующий элемент смачивают маслом, применяемым для двигателя, а в корпус заливают масло до установленного уровня.
В воздушных фильтрах, соединенных с системой вентиляции картера двигателя, одновремено с очисткой системы вентиляции необходимо также очистить и воздушную полость фильтра от смолистых отложений, а металлический фильтрующий элемент погрузить на 20 - 30 мин в ацетон, после чего продуть его сжатым воздухом. При работе в условиях низкой температуры (от -20° до -40°) в фильтр надо заливать масло АУ, обладающее низкой температурой застывания. При температуре ниже -40° в условиях бесснежной зимы к маслу, заливаемому в фильтр, следует добавлять до 20% керосина.
После сборки фильтра не следует запускать двигатель в течение 10 - 15 мин для того, чтобы излишнее масло стекло с фильтрующего элемента.
Уход за топливными фильтрами. Уход за фильтром-отстойником заключается в проверке его герметичности, выпуске отстоя и промывке.
Для выпуска отстоя надо, предварительно перекрыв кран от топливного бака и ослабив стяжной болт, отвернуть пробку. После выпуска отстоя открывают кран бака на время, достаточное для ополаскивания корпуса фильтра чистым бензином.
Для промывки фильтра-отстойника снимают корпус и фильтрующий элемент, промывают их в неэтилированном бензине и просушивают. Во избежание порчи фильтрующих пластин при их очистке не следует пользоваться щетками, скребками, а также сжатым воздухом высокого давления. При сборке проверяют состояние прокладок. Герметичность собранного фильтра-отстойника проверяют под давлением (2 кГ/см2 ) 196 133 н/м2.
В фильтре тонкой очистки топлива снимают стакан-отстойник и керамический или капроновый фильтрующий элемент и тщательно промывают их в бензине.
Уход за топливным баком и топливопроводами. Герметичность топливопроводов на участке от бака до топливного насоса следует проверять при неработающем двигателе, а на участке от насоса до карбюратора - при работающем двигателе, когда в топливопроводе создается давление. Обнаруженную утечку топлива устраняют путем подтягивания гаек соединений или заменой неисправных гаек, штуцеров и топливопроводов.
При ТО-2 следует подтянуть крепления бака, проверить плотность затяжки штуцеров топливопроводов, крепление пробки бака и работу ее клапанов, прочистить вентиляционные отверстия в пробке, чтобы предотвратить возникновение разрежения в баке.
Два раза в год надо удалять отстой из бака, проверять исправность и чистоту его сетчатого фильтра, отсоединять топливопроводы, промывать их и продувать сжатым воздухом.
При подготовке автомобиля к осенне-зимней эксплуатации для удаления смолистых отложений и грязи бак надо снять и промыть. Бак промывают горячей водой или паром низкого давления, неэтилированным бензином, керосицом, растворителями (авиационным бензином Б-70, уайт-спиритом). Наличие ржавчины в отстое свидетельствует о повреждении внутреннего покрытия бака. В этом случае необходимо залить в снятый бак 10 - 15 л нагретого до 105° обезвоженного масла, применяемого для двигателя, затем плавно несколько раз повернуть так, чтобы тонкий слой масла покрыл все стенки бака. Остатки масла из бака выливают.
Одновременно с промывкой бака следует промыть фильтр топ-ливоприемной трубки.
Диагностика системы питания путем замера расхода топлива на холостом ходу, при постоянных режимах движения и при разгоне производится на одной из станций диагностики с помощью электронного прибора, схема которого показана на рис. 91. Прибор состоит из электронного усилителя 7, расходомерной колбы 2 с поплавком 5, трехходового крана 14, осветителей 7, датчиков с фотосопротивлениями 4, спидометра 6 с электроприводом, датчиков 12, электросекундомера 9 и суммарного счетчика пути 10.
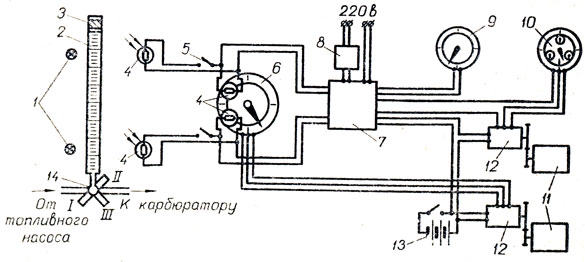 Рис. 91. Схема прибора для замера расхода топлива, пути и времени разгона и наката: 1 - осветители; 2 - расходомерная колба; 3 - поплавок; 4 - фотосопротивления; 5 - тумблер; 6 - спидометр; 7 - электронный усилитель; 8 - источник питания; 9 - электросекундомер; 10 - суммарный счетчик оборотов; 11 - беговые барабаны; 12 - датчик оборотов; 13 - источник питания датчиков; 14 - трехходовой кран
Трехходовой кран подключают в разъем трубки от топливного насоса к фильтру тонкой очистки. При замере расхода топлива на холостом ходу кран поворачивают в положение ΙΙ (топливо поступает к карбюратору и в расходомер), устанавливают постоянные обороты холостого хода двигателя и переводят кран в положение ΙΙΙ (топливо поступает из расходомера в карбюратор). Объем израсходованного топлива определяют по шкале расходомера; а время - по электросекундомеру 9, который включается и выключается электронным усилителем 7 при пересечении поплавком 3 лучей, идущих от осветителей 1 на фотодатчики 4. Отсекаемый объем топлива может быть изменен в пределах от 20 до 125 см3 перемещением верхнего датчика с фотосопротивлением.
Аналогично замеряется расход топлива при движении автомобиля по барабанам стенда с постоянной скоростью и при разгоне в диапазоне скоростей от 20 до 60 км/ч. В этих случаях с помощью суммарного счетчика 10 дополнительно фиксируется пройденный путь.
Техническое обслуживание системы питания четырехтактных дизельных двигателей
Надежная и экономичная работа дизеля в значительной степени зависит от состояния системы питания. Неисправности топливной аппаратуры вызывают снижение мощности и экономичности двигателя, затруднения в запуске, перебои в работе, повышают дымность выпуска отработавших газов.
Затруднения в запуске двигателя вызываются недостаточной подачей топлива в цилиндры вследствие подсасывания воздуха в системе питания, неисправности топливоподкачивающего насоса, износа плунжерных пар и нагнетательных клапанов насоса высокого давления, заедания его рейки, пониженного давления начала подъема иглы форсунок, а также вследствие засорения фильтрующих элементов топливных фильтров.
Снижение мощности двигателя может произойти вследствие неостаточной подачи топлива в цилиндры, неправильной регулировки начала подачи топлива и заедания в механизме управления подачей топлива.
Неравномерная работа двигателя возникает при подсасывании оздуха в систему питания, ослаблении крепления или разрыве топ-ивопровода высокого давления, при нарушении равномерности одачи топлива секциями насоса и зависании или негерметичности нагнетательного клапана, при неудовлетворительной работе отдельных форсунок.
Двигатель идет "в разнос" или не останавливается при прекращении подачи топлива вследствие поломки пружины регулятора исла оборотов, а также заедания рейки топливного насоса высокого давления. Последняя неисправность может быть вызвана погнутостью рейки, наличием грязи или заусенцев на ее зубьях и заеданием плунжера во втулке.
Двигатель сильно дымит (черный дым) при большой подаче топлива в цилиндры, позднем угле опережения впрыска топлива и низком давлении впрыска топлива у форсунок. Двигатель дымит при некачественном распылении топлива форсунками (синий дым) и пропуске вспышек в цилиндре двигателя вследствие отсутствия впрыска у одной из форсунок (белый дым).
Системой технического обслуживания предусмотрено выполнение следующих работ:
при ЕО - проверка при работающем двигателе герметичности соединений топливопроводов, проверка уровня и при необходимости доливка масла в топливный насос высокого давления и регулятор, слив отстоя из топливных фильтров, заправка топливного бака;
ТО-1-проверка крепления приборов топливной аппаратуры и топливопроводов, проверка работы механизмов управления подачей топлива и останова двигателя, смазка их сочленений, слив отстоя из топливного бака;
ТО-2 - промывка корпусов топливных фильтров и замена фильтрующих элементов, промывка воздушного фильтра и смена в нем масла, проверка работы форсунок, снятых с двигателя, регулировка, при необходимости, установочного угла опережения впрыска топлива;
через каждые три ТО-2 или 750 ч работы - проверка и регулировка топливного насоса высокого давления, снятого с двигателя, опрессовка топливной системы;
два раза в год (при подготовке к осенне-зимнему и весенне-летнему периодам эксплуатации автомобилей) - промывка топливных баков и фильтра топливоприемника бака, проверка топливоподкачивающего насоса.
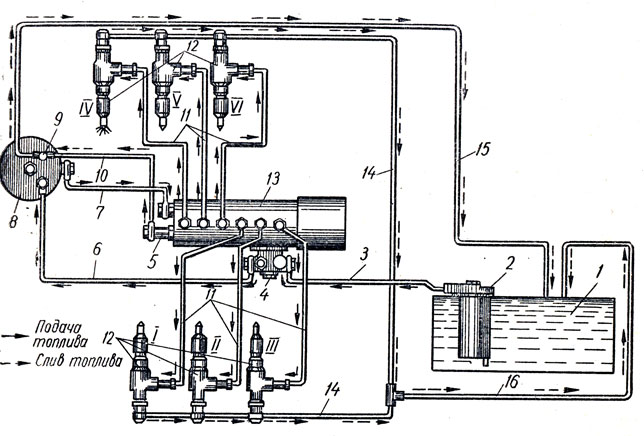 Рис. 92. Схема системы питания топливом дизеля ЯМЗ-236: 1 - топливный бак; 2 - фильтр предварительной очистки; 3 - трубопровод от фильтра предварительной очистки к топливоподкачивающему насосу; 4 - топливоподкачивающий насос; 5 - перепускной клапан; 6 ~ отводящий трубопровод топливоподкачивающего насоса; 7 - подводящий трубопровод насоса высокого давления; 8 - фильтр тонкой очистки; 9 - жиклер; 10 - отводящий трубопровод насоса высокого давления; 11 - трубопроводы от секций насоса высокого давления к форсункам; 12 - форсунки; 13 - насос высокого давления; 14 - дренажный трубопровод; 15 - отводящий трубопровод от фильтра тонкой очистки к баку; 16 - отводящий трубопровод к баку
Проверка герметичности топливной системы. Топливная система четырехтактного дизельного двигателя (рис. 92) состоит из систем низкого и высокого давления. Система низкого давления (топливный бак 1, фильтр 2 предварительной очистки топлива, топливоподкачивающий насос 4, фильтр 8 тонкой очистки топлива и соединяющие их топливопроводы 3 и 6) до топливоподкачивающего насоса находится под разрежением, а после него - под давлением, создаваемым насосом.
К системе высокого давления относятся топливный насос 13, форсунки 12 и их трубопроводы 11.
При попадании воздуха в топливную систему, особенно в магистраль, находящуюся под разрежением, затрудняется запуск двигателя, его работа становится неустойчивой. Для проверки герметичности системы питания надо установить малые обороты коленчатого вала и слегка отвернуть пробку фильтра тонкой очистки топлива;
при наличии воздуха в системе из-под пробки будет вытекать пена или топливо с пузырьками воздуха. После появления чистой струи топлива пробку завертывают.
В случае невозможности запуска двигателя проверку герметичности и заполнение системы от топливоподкачивающего насоса до насоса высокого давления 13 производят с помощью ручного насоса, расположенного на топливоподкачивающем насосе. Для этого отсоединяют отводящий топливопровод у бака и закрывают его пробкой. После подкачивания топлива насосом по месту подтекания топлива или появления пузырьков определяют неисправность.
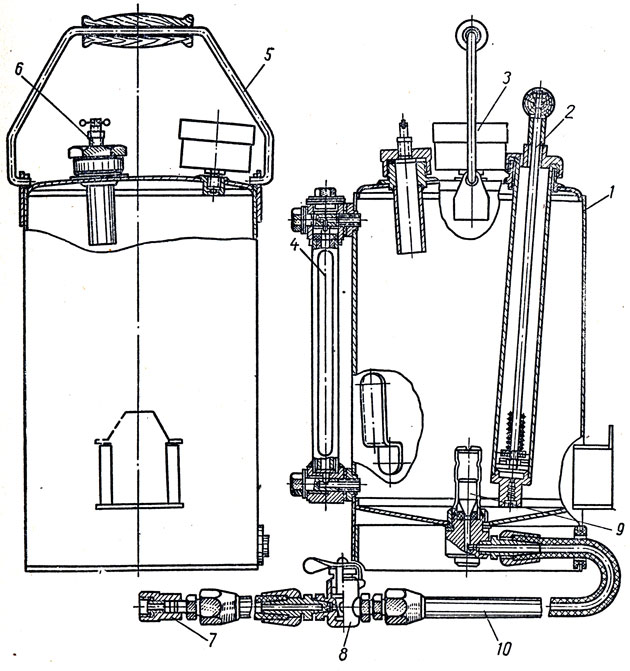 Рис. 93. Прибор для проверки герметичности системы питания (модель НИИАТ-383): 1 - бачок; 2 - воздушный насос; 3 - манометр; 4 - контрольная трубка; 5 - дужка; 6 - кран сброса давления; 7 - сменный штуцер; 8 - двухходовый кран; 9 - запорный клапан; 10 - шланг
Герметичность всей системы можно проверить прибором модели НИИАТ-383 (рис. 93). В бачке 1 ручным насосом создают давление 294 200 н/м2 (3 кГ/см2 ), предварительно закрыв кран 8 и залив 5 - 6 л профильтрованного топлива. Затем отсоединяют от топливного бака отводящий и подводящий топливопроводы, первый из них глушат, а второй соединяют со шлангом 10. После поворота крана 8 топливо из бачка под давлением заполняет всю топливную систему, и неисправность обнаруживают способом, указанным выше.
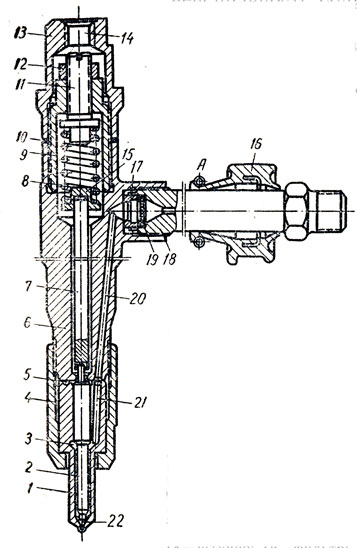 Рис. 94. Форсунка: 1 - распылитель; 2 - игла распылителя; 3 - кольцевая камера; 4 - гайка распылителя; 5 - кольцевая проточка; 6 - корпус форсунки; 7 - штанга; 8 - пружина; 9 - гайка пружины; 10 - уплотнительная прокладка; 11 - регулировочный винт; 12 - контргайка; 13 - колпак; 14 - отверстие для отвода топлива в бак; 15 - тарелка; 16 - резиновый уплотнитель; 17 - гнездо фильтра; 18 - штуцер; 19 - фильтр; 20 - топливный канал в корпусе форсунки; 21 - топливный канал в корпусе распылителя; 22 - седло иглы
Неплотности в соединениях устраняют подтяжкой резьбовых соединений или заменой уп-лотнительных прокладок и топливопроводов, а затем вновь проверяют герметичность топливной системы. Проверка и регулировка форсунок. Форсунка закрытого типа обеспечивает требуемые мел- кость распыливания и форму факела впрыскиваемого топлива на всех режимах работы двигателя. В процессе эксплуатации двигателя качество работы форсунки постепенно ухудшается. Основной причиной неисправности форсунок является ухудшение качества распыления топлива вследствие снижения давления начала подъема иглы 2 (рис. 94) из-за ослабления или поломки пружины 8, а также закоксовывания или засорения отверстий в корпусе распылителя 1 и заедания иглы распылителя. В результате этого мощность и экономичность двигателя снижаются, работа его на малых оборотах становится неустойчивой, повышается дымность отработавших газов.
Проверка форсунок на двигателе является предварительной и заключается в последовательном выключении цилиндров на работающем двигателе путем ослабления накидной гайки у штуцера проверяемой форсунки так, чтобы в нее не поступало топливо. Если при этом число оборотов коленчатого вала (на слух) понижается, а дымность отработавших газов не изменяется, то форсунка исправна. На неисправность форсунки указывает неизменность числа оборотов коленчатого вала и уменьшение дымности отработавших газов. Неисправные форсунки направляют в цех по ремонту топливной аппаратуры.
Предварительную проверку форсунок можно производить и на неработающем двигателе, проворачивая вручную коленчатый вал при максимально вдвинутой рейке топливного насоса высокого давления. При этом исправные форсунки в момент впрыска издают характерный сильный звук. Глухой, трудно уловимый звук указывает на подтекание топлива из форсунки и отсутствие распыливания.
Проверка форсунок, снятых с двигателя, а также регулировка их после ремонта может быть произведена на приборе КП-1609А (рис. 95), который позволяет определить их герметичность, величину давления начала подъема иглы и качество распыливания топлива.
Для проверки герметичности форсунки следует, прокачивая топливо рычагом 1 насоса, медленно завертывать регулировочный винт 11 (см. рис. 94) испытуемой форсунки, пока давление, показываемое манометром прибора, не достигнет 29 420 000 н/м2 (300 кГ/см2 ). Быстрое падение давления от 27 458 600 (280) до 24 516 600 н/м2 (250 кГ/см2 ), время падения давления должно быть не менее 30 - 45 сек, указывает на нарушение герметичности форсунки, которое возможно в запорной или в направляющей частях иглы 2, а также в сопряжении корпуса распылителя 1 с корпусом 6 форсунки.
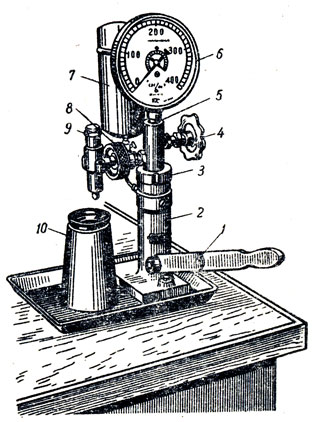 Рис. 95. Прибор КП-1609А для проверки и регулировки форсунок: 1 - рычаг; 2 - корпус; 3 -гайка корпуса; 4 - кран отключения манометра; 5 - корпус распределителя; 6 - манометр; 7 - бачок; 8 - маховик крепления форсунки; 9 - испытуемая форсунка; 10 - глушитель
Неплотное прилегание запорной части иглы (на что указывает влажнение носика распылителя), а также торца корпуса 6 фор-унки к распылителю устраняют притиркой. При неплотном приле-ании направляющей части иглы к распылителю, о чем свидетельствует подтекание топлива из-под гайки 9 пружины, распылитель аменяют.
Для проверки величины давления начала подъема иглы медленно повышают давление в полости форсунки, наблюдая за показаниями манометра. Скорость дальнейшего повышения давления топлива сверх 12 258 033,2 н/м2 (125 кГ/см2 ) не должна превышать 490332 н/м2 (5 кГ/см2 ) в секунду. Величина давления фиксируется в момент начала впрыска топлива. В случае необходимости форсунку регулируют, завертывая регулировочный винт, если давление меньше 14 710 000 н/м2 (150 кГ/см2 ), или отвергшая его, если давление больше 15 200 332 н/м2 (155 кГ/см2 ).
Проверку качества распиливания топлива производят на отрегулированной форсунке. Завернув кран 4 прибора (см. рис. 95), рычагом 1 насоса несколько раз резко прокачивают топливо, а затем перемещают рычаг со скоростью примерно 50-60 ходов в минуту и наблюдают за качеством распыления топлива.
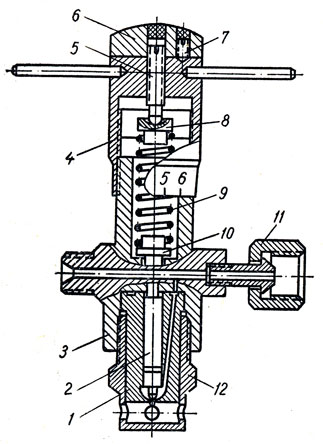 Рис. 96. Максиметр: 1 - распылитель; 2 - игла распылителя; 3 - корпус; 4 - микрометрическая головка; 5 - установочный винт; 6 - контргайка; 7 - стопорный винт; 8 - упор; 9 - пружина; 10 - нажимной штифт; 11 - штуцер; 12 - гайка
Качество распыления считается удовлетворительным, если топливо впрыскивается в атмосферу в туманообразном состоянии и равномерно распределяется по поперечному сечению конуса рас-пыливания без заметных на глаз отдельных капель, сплошных струй и местных сгущений. Начало и конец впрыска должны быть четкими и сопровождаться характерным резким звуком отсечки. Проверку и регулировку форсунок при отсутствии прибора КП-1609А можно произвести с помощью переносного прибора-максиметра (рис. 96). По принципу работы максиметр аналогичен форсунке, но имеет микрометрическую головку, позволяющую устанавливать давление начала подъема иглы распылителя до 49 033 200 н/м2 (500 кГ/см2 ). Поворот микрометрической головки на один оборот изменяет упругость пружины на 4 903 320 н/м2 (50 кГ/см2 ).
Проверяемую форсунку снимают с двигателя и присоединяют к секции топливного насоса высокого давления последовательно с максиметром, на шкале которого устанавливают величину давления, равную 14 710 000 н/м2 (150 кГ/см2 ). Затем ослабляют затяжку накидных гаек всех топлизопроводов высокого давления и стартером проворачивают коленчатый вал двигателя. Начало впрыска топлива через максиметр и форсунку должно происходить одновременно, и через них должно подаваться одинаковое количество топлива. В случае необходимости форсунку регулируют, как указано выше.
Неисправные форсунки разбирают, все детали промывают в чистом дизельном топливе и тщательно осматривают. Отверстия и каналы в корпусе форсунки прочищают волосяными ершами, а наружные поверхности - мягкими металлическими щетками. Риски, царапины и следы коррозии с торцовой поверхности устраняют притиркой, а корпуса с грубыми механическими повреждениями заменяют. Внутреннюю поверхность корпуса распылителя очищают мягким латунным стержнем диаметром 4,5 мм , обернутым папиросной бумагой, сопловые отверстия прочищают струной диаметром 0,3 мм , риски и царапины на запорной части иглы устраняют притиркой. При наличии рисок и царапин на направляющей части иглы, а также матовых пятен или следов перегрева, распылители заменяют. Износ сопловых отверстий контролируют струной диаметром 0,36 мм . Распылители с изношенными отверстиями, а также следами оплавления носика подлежат замене. Распылитель заменяют только комплектно с иглой. Фильтр 19 (см. рис. 94) форсунки продувают сжатым воздухом под давлением 490 332 - 686 466 н/м2 (5 - 7 кГ/см2 ) в направлении, противоположном потоку топлива. Пружина форсунки в свободном состоянии должна быть длиной не менее 27,5 мм , а под нагрузкой (30 кГ) 294,200 н - не менее 26 мм . Все детали с неисправной резьбой подлежат замене.
При сборке форсунки необходимо гайку распылителя и контргайку регулировочного винта затянуть с моментом 68,6466 - 78,4532 н · м (7 - 8 кГм). При окончательно затянутой гайке игла должна легко перемещаться. Для штуцера форсунки установлен момент затяжки 39,2266 - 49,0332 н · м (4 - 5 кГм).
После проверки надо установить форсунки в те же цилиндры и затянуть гайки скобы крепления с моментом 49,0332 - 58,8399 н · м (5 - 6 кГм).
Проверка и регулировка топливных насосов высокого давления. Топливный насос высокого давления обеспечивает дозирование топлива при работе двигателя на различных режимах и подачу топлива в цилиндры двигателя в соответствии с порядком их работы под давлением, необходимым для впрыска топлива в цилиндры.
В процессе эксплуатации двигателя вследствие износа плунжерных пар, нагнетательных клапанов, кулачкового вала, толкателей и других деталей насоса снижается подача топлива его секциями, изменяется начало подачи топлива в цилиндры, что приводит к снижению мощности и экономичности двигателя. Износ нагнетатель-ых клапанов по запорному конусу и разгрузочному пояску изме-яет начало и характер впрыска, ухудшает отсечку подачи топлива иглой форсунки, что приводит к подтеканию топлива через распылитель и закоксовыванию сопловых отверстий. Кроме износа прецизионных деталей, работа насоса может быть нарушена из-за поломки пружин толкателей, износа перепускного клапана и его гнезда, срыва резьбы штуцеров и др.
Топливный насос высокого давления проверяют и регулируют на начало, величину и равномерность подачи топлива отдельными секциями. Для этой цели используют стенд СДТА-1 (рис. 97), оборудованный вариатором числа оборотов приводного вала и автоматическим переключателем количества впрысков.
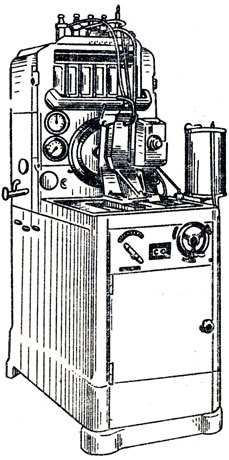 Рис. 97. Общий вид стенда СДТА-1
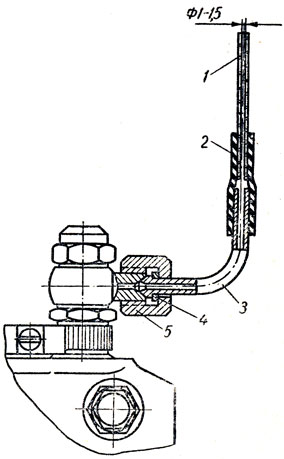 Рис. 98. Моментоскоп: 1 - стеклянная трубка; 2 - переходная резиновая трубка; 3 - топливопровод высокого давления; 4 - шайба; 5 - накидная гайка
Регулировка начала подачи топлива секциями насоса. Насос со снятой автоматической муфтой опережения впрыска топлива укрепляют на стенде и к штуцерам секций насоса присоединяют моментоскопы (рис. 98). Вращением кулачкового вала насосы заполняют стеклянные трубки 1 моментоскопов до половины объема, затем медленно вращают вал и следят за уровнем топлива в трубках. Начало подачи топлива секциями насоса определяют по началу движения топлива в стеклянных трубках моментоскопов, замечая в это время угол поворота указателя на муфте, соединяющей приводной вал стенда с кулачковым валом насоса, относительно градуированного диска, укрепленного на стенде.
Начало подачи топлива первой секцией насоса должно происходить за 38 - 39° до оси симметрии профиля кулачка. Для определения оси симметрии кулачка первой секции надо отметить на градуированном диске момент начала движения топлива в моментоскопе при повороте кулачкового вала насоса по часовой стрелке, затем повернуть вал по часовой стрелке на 90° и отметить на градуированном диске момент начала движения топлива в моментоскопе при повороте вала против часовой стрелки. Ось симметрии профиля кулачка проходит через середину между отмеченными точками на градуированном диске и ось кулачкового вала насоса.
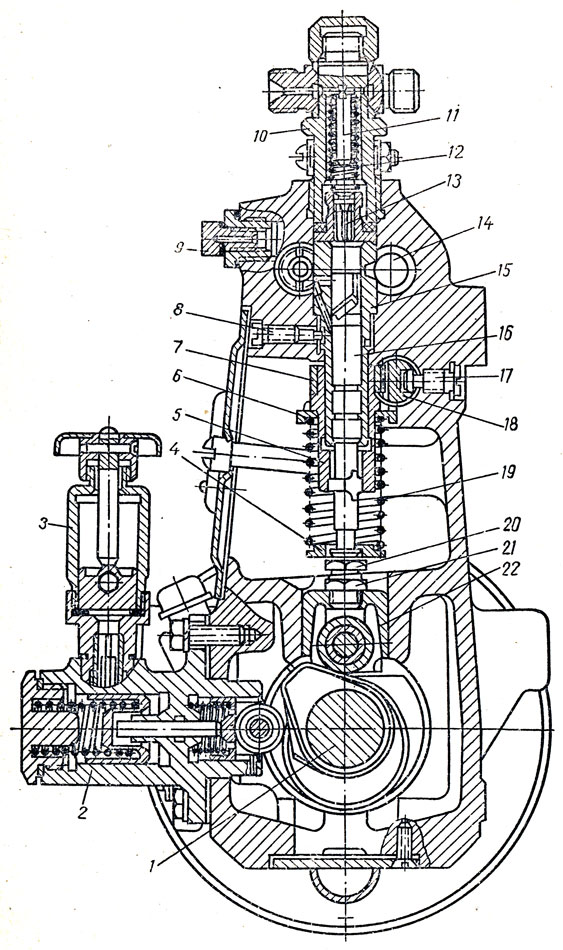 Рис. 99. Секция топливного насоса высокого давления: 1 - кулачковый вал; 2 - корпус топливоподкачнвающего насоса; 3 - цилиндр ручного насоса; 4 - нижняя тарелка; 5 - поворотная втулка; 6 - верхняя тарелка; 7 - зубчатый венец; 8 - стопорный винт; 9 - пробка; 10 - штуцер; 11 - упор нагнетательного клапана; 12 - пружина нагнетательного клапана; 13 - нагнетательный клапан; 14 - канал; 15 - гильза плунжера; 16 - плунжер; 17 - винт ограничения хода рейки; 18 - рейка; 19 - пружина; 20 - регулировочный болт; 21 - контргайка; 22 - толкатель
Если принять условно начало подачи топлива секцией № 1 насоса за 0°, то подача топлива остальными секциями шестиплунжерного насоса должна осуществляться в следующем порядке: секция № 4 через 45°, секция № 2 - 120°, секция № 5 - 165°, секция № 3 - 240° и секция № 6 - 285°. В восьмиплунжерном насосе подача топлива секциями должна производиться через 45°.
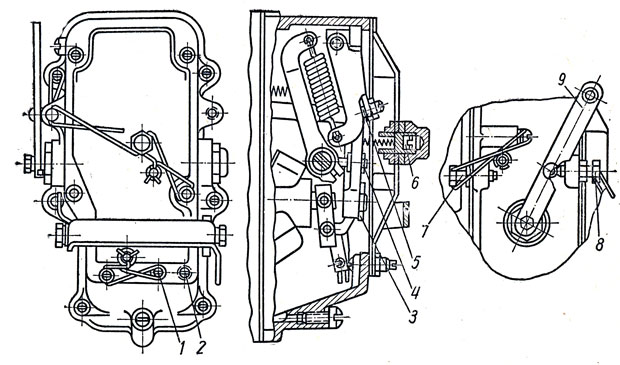 Рис. 100. Регулировочные точки регулятора числа оборотов коленчатого вала: 1 - винт ограничения мощности на период обкатки; 2 - винт кулисы; 3 - контргайка корректора; 4 - винт регулировки подачи топлива; 5 - винт двуплечего рычага; 6 - винт буферной пружины; 7 - болт ограничения максимальных оборотов; 8 - болт минимальных оборотов холостого хода; 9 - рычаг управления
Неточность интервала между началом подачи топлива любой секцией насоса относительно первой допускается в пределах ±20. При большем значении неточности интервала начало подачи топлива изменяют поворотом регулировочного болта 20 (рис. 99) толкателя при отпущенной контргайке 21 (при завертывании болта момент начала подачи запаздывает, при вывертывании - наступает раньше). После регулировки необходимо надежно затянуть контргайку и повторить проверку.
Регулировка величины и равномерности подачи топлива секциями насоса. Величину подачи топлива каждой секцией проверяют при
(1030 + 10 об/мин )× |
π |
рад/сек |
|
30 |
кулачкового вала насоса и упоре рычага 9 (рис. 100) управления в болт 7 ограничения максимальных оборотов. Проверку выполняют с комплектом форсунок, отрегулированных на давление впрыска 14 710000 + 490 332 н/м2 (150 + 5 кГ/см2 ), и при температуре топлива 25 - 30° С.
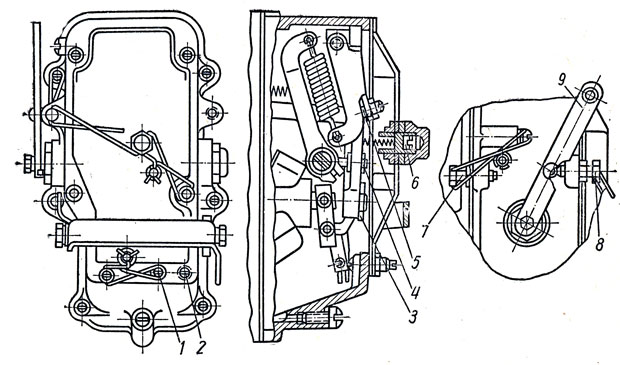 Рис. 101. Гидравлическая схема стенда СДТА-1: 1 - испытуемый насос; 2 - форсунка; 3 - мерный цилиндр; 4 - указатель уровня топлива; 5 - термометр; 6 - верхний топливный бак; 7 - насос стенда; 8 - топливный фильтр; 9 - манометр; 10 - распределитель топлива; 11 - нижний топливный бак; 12 - стол стенда
Устанавливают требуемое число оборотов кулачкового вала насоса, включают автоматический выключатель электродвигателя на определенное число секунд работы насоса и одновременно подводят мензурки под каждую форсунку. После автоматического выключения электродвигателя по количеству топлива в мерных цилиндрах 3 (рис. 101) определяют величину подачи топлива секциями насоса.
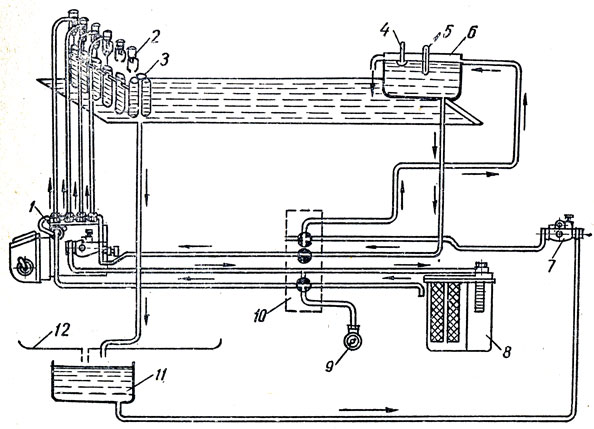 Рис. 101. Гидравлическая схема стенда СДТА-1: 1 - испытуемый насос; 2 - форсунка; 3 - мерный цилиндр; 4 - указатель уровня топлива; 5 - термометр; 6 - верхний топливный бак; 7 - насос стенда; 8 - топливный фильтр; 9 - манометр; 10 - распределитель топлива; 11 - нижний топливный бак; 12 - стол стенда
Количество топлива, подаваемого каждой секцией за один ход плунжера, должно быть 105 - 107 мм 3 (107 - 111 см3/мин). В случае отклонения величины подачи от нормы следует произвести регулировку насоса в следующей последовательности:
1. Замеряют давление топлива в магистрали на входе в насос. Оно должно быть в пределах 127 486 - 147 100 н/м2 (1,3 - 1,5 кГ/см2) при номинальном числе оборотов
(1050 об/мин )· |
π |
рад/сек |
|
30 |
кулачкового вала насоса. Если давление не соответствует указанному значению, необходимо снять перепускной клапан и поворотом седла отрегулировать давление по манометру стенда, после чего седло клапана зачеканить.
2. Проверяют герметичность нагнетательных клапанов. При положении рейки, соответствующем выключенной подаче, нагнетательные клапаны не должны пропускать топливо под давлением 166 713 - 196 133 н/м2 (1,7 - 2,0 кГ/см2 ) в течение двух минут. В случае течи топлива нагнетательный клапан необходимо заменить.
3. Проверяют и при необходимости регулируют в пределах
(225 - 275 об/мин )· |
π |
рад/сек |
|
30 |
число оборотов полного автоматического выключения подачи топлива регулятором при упоре рычага 9 (рис. 100) управления в болт 8 минимальных оборотов холостого хода. При вывертывании болта 8 и винта 6 буферной пружины обороты уменьшаются.
4. Проверяют число оборотов кулачкового вала, соответствующее автоматическому уменьшению подачи топлива. Начало перемещения рейки в сторону уменьшения подачи (выдвиг рейки) должно происходить при
(1060 + 10 об/мин )· |
π |
рад/сек |
|
30 |
кулачкового вала насоса, а конец (полное выключение подачи) - при
(1120 + 1150 об/мин )· |
π |
рад/сек. |
|
30 |
Начало перемещения рейки регулируют болтом 7, при этом рычаг 9 управления должен упираться в него.
Если конец перемещения рейки не происходит при требуемом числе оборотов кулачкового вала насоса, следует, изменив положение винта 5 двуплечего рычага, установить болтом 7 начало перемещения рейки при
(1060 + 10 об/мин )· |
π |
рад/сек, |
|
30 |
затем проверить число оборотов в конце перемещения рейки и при необходимости вновь произвести регулировку; завертывая винт 5, уменьшают число оборотов конца перемещения рейки, вывертывая - увеличивают.
5. Проверяют величину подачи топлива каждой секцией насоса, как указано выше, и определяют неравномерность подачи топлива.
Неравномерность подачи топлива секциями насоса допускается не свыше 3% и подсчитывается по формуле:
где gmakc и gмин - максимальная и минимальная подача топлива секцией (за время проверки).
Количество подаваемого секцией топлива зависит от положения отсечных винтовых кромок плунжера 16 (см. рис. 99) относительно перепускного нижнего отверстия гильзы 15. Для одинаковой подачи топлива всеми секциями насоса надо обеспечить одинаковый активный ход плунжеров, т. е. закрытие впускного и открытие перепускного отверстий гильзы при данном положении рейки должно происходить за один и тот же промежуток времени у всех секций насоса. Это достигается изменением положения плунжера, связанного с поворотной втулкой 5, относительно зубчатого венца 7 при ослабленном стяжном винте венца. При повороте втулки влево подача топлива уменьшается, при повороте вправо - увеличивается.
6. Проверяют и в случае необходимости регулируют ход рейки, обусловливающий номинальную подачу топлива насосом. Нормальный вдвиг рейки от крайнего выдвинутого положения при
(1030 ± 10 об/мин )· |
π |
рад/сек |
|
30 |
кулачкового вала насоса и при упоре рычага 9 (рис. 100) управления в болт 7 ограничения максимальных оборотов коленчатого вала двигателя должен быть равен 13 ± 0,2мм. Регулируют вдвиг винтом 4.
7. Проверяют выключение подачи топлива скобой останова. При повороте скобы в нижнее положение на 45° подача топлива всеми секциями насоса должна полностью прекратиться. Если подача не выключается, следует проверить легкость хода рейки и устранить ее заедание.
Кроме того, проверяют и при необходимости регулируют пусковую подачу топлива при (80 ± 10 об/мин ) o рад/сек кулачкового вала насоса. Она должна составлять 17 - 20 см3/мин. Регулировку производят винтом 2: при вывертывании винта подача топлива увеличивается, при завертывании - уменьшается.
После регулировки топливный насос и регулятор пломбируют и устанавливают автоматическую муфту опережения впрыска топлива, затянув ее гайку с моментом 78,4532 - 98,0665 н (8 - 10 кГм). Рабочие части ведущей и ведомой полумуфт смазывают смазкой ЦИАТИМ-201. В собранную муфту набивают 180 г этой смазки.
Подшипники, кулачки и толкатели топливного насоса высокого давления, а также детали всережимного регулятора числа оборотов смазываются дизельным маслом (летом ДС-11, зимой ДС-8), заливаемым в картер насоса в количестве 0,15 л и в корпус регулятора - 0,1 л. Количество масла контролируют с помощью стержневых измерителей уровня.
Проверка топливоподкачивающих насосов. Топливоподкачивающий насос обеспечивает подачу топлива в необходимом количестве из бака к топливному насосу высокого давления. Вследствие износа сопряженных деталей топливопод-качивающего насоса работа его ухудшается, и два раза в год необходимо проверять производительность и величину давления, развиваемого насосом. Эту проверку производят на стенде СДТА-1.
Установив число оборотов вала привода стенда в пределах 1050 ± 10 в минуту и противодавление, равное 147 100 - 166 713 н/м2 (1,5 - 1,7 кГ/см2 ), определяют производительность насоса по объему топлива, поданного насосом в мерный цилиндр в течение 1 мин. Он должен быть не менее 2,2 л. Затем при тех же оборотах вала привода стенда, перекрыв кран распределителя стенда, наблюдают за показаниями манометра. Максимальное давление для топливопод-качивающего насоса должно быть не менее 392 266 н/м2 (4,0 кГ/см2 ).
Установка топливного насоса высокого давления на двигатель. Установка топливного насоса высокого давления на двигатель должна обеспечивать впрыск топлива в камеру сгорания с таким опережением, чтобы сгорание топлива происходило вблизи в. м. т. При этом рабочий процесс двигателя протекает с наименьшими тепловыми потерями. Установочный угол начала подачи топлива должен быть равен 20 ± 1°.
Для правильной установки топливного насоса высокого давления на двигатель необходимо совместить нулевые метки на корпусе 3 (рис. 102) автоматической муфты опережения впрыска топлива, на полумуфте 2 вала привода топливного насоса и на ведущем фланце 1 полумуфты к отрегулировать опережение впрыска топлива с помощью моментоскопа, присоединенного к первой секции насоса.
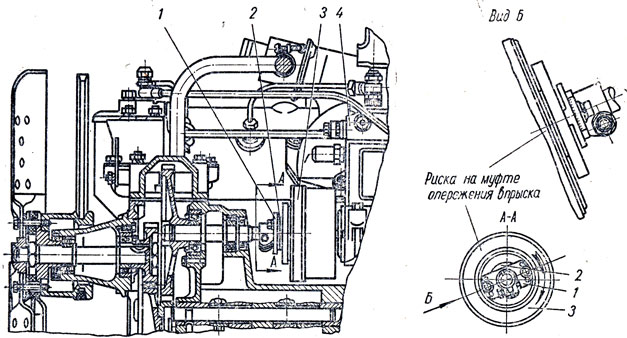 Рис. 102. Схема установки топливного насоса высокого давленя на двигателе 1 - ведущий фланец полумуфты; 2 - полумуфта вала привода; 3 - муфта опережения впрыска топлива; 4 - топливный насос высокого давления
В момент начала движения топлива в трубке моментоскопа риска на шкиве коленчатого вала двигателя должна находиться против метки на крышке распределительных шестерен. При несовпадении меток прибегают к изменению установки автоматической муфты опережения впрыска топлива.
Угол опережения впрыска топлива регулируют, ослабив болты крепления, смещением полумуфты 2 вала привода топливного насоса высокого давления относительно ведущего фланца 1. Для увеличения угла опережения впрыска топлива полумуфту нужно смещать по направлению ее вращения, причем ее смещение на одно деление шкалы фланца соответствует 4° поворота коленчатого вала или четырем делениям на крышке распределительных шестерен.
После установки топливного насоса регулируют минимальные обороты холостого коленчатого вала в пределах
(450 - 550 об/мин )· |
π |
рад/сек. |
|
30 |
Для этого отвертывают винт 6 (см. рис. 100) буферной пружины на 5 - 6 мм , затем постепенно уменьшают число оборотов коленчатого вала, отвертывая болт 8 до появления уловимых на слух перебоев в работе двигателя, после чего ввертывают винт 6 до некоторого повышения числа оборотов вала.
Устойчивость минимальных холостых оборотов двигателя проверяют увеличением числа оборотов до 1200 - 1300 в минуту, а затем резким поворотом рычага 9 управления до упора в болт 8. При этом двигатель не должен глохнуть.
Уход за топливными фильтрами и баком. Для безотказной работы двигателя исключительное значение имеет чистота дизельного топлива (отсутствие в нем механических примесей и воды). Поэтому отстой из фильтров предварительной и тонкой очистки топлива сливают ежедневно. Из фильтров, отвернув их сливные пробки и слегка ослабив пробки в крышках корпусов, сливают по 0,1 л топлива. Затем, вывернув пробки из отверстий в крышках, доливают в фильтры чистое топливо до заполнения корпусов, завертывают пробки и пускают двигатель на 3 - 4 мин для удаления воздушных пробок.
При ТО-2 производят разборку фильтров, промывку их в чистом дизельном топливе и замену фильтрующих элементов. После сборки фильтры заполняют топливом и пускают двигатель на 5 - 6 мин.
Топливный бак необходимо заполнить топливом сразу же по возвращении в гараж, так как охлаждение стенок бака может привести к конденсации паров воды, находящихся в свободном от топлива объеме бака. При ТО-1 сливают отстой из бака, выпуская не менее 3 л топлива. Эту операцию надо производить не раньше, чем после 5 ч стоянки автомобиля. Два раза в год топливный бак необходимо тщательно промывать.
|