§ 2. Обслуживание тормозов и механизмов их привода
Безопасность движения автомобиля зависит от его тормозных качеств, которые определяются длиной тормозного пути, одновременностью и надежностью действия тормозов колес.
При движении нагруженного автомобиля по сухому горизонтальному асфальтовому шоссе со скоростью 8,33333 м/сек(30 км/ч) тормозной путь должен быть в пределах 6 м для легковых автомобилей и 8 - 12 м для грузовых автомобилей и автобусов.
Регулировка тормозов должна обеспечить одновременное торможение колес и исключить самопроизвольное их притормаживание или заклинивание тормозных колодок при отпущенной педали тормоза.
В целях повышения долговечности и надежности действия колесных колодочных тормозов на задних (ведущих) колесах модернизированных автомобилей (ЗИЛ-130 - 66) применяются колодки шириной до 140 мм . Кроме того, накладки тормозных колодок задних колес имеют специальный профиль, который выполнен с учетом износа фрикционного материала. У тормозов задних колес автомобиля ЗИЛ-130 - 66 значительно уменьшилась удельная нагрузка на фрикционные накладки и, следовательно, сократился износ колодок при одновременном повышении эффективности действия тормозов на больших скоростях движения.
Эффективность действия тормозов передних колес на грузовых автомобилях ГАЗ-66 повышается за счет применения тормозов с разнесенными опорами колодок и раздельным приводом для каждой колодки. Такой привод ранее применялся только для легковых автомобилей. При движении этого автомобиля вперед, тормозной момент повышается за счет самозахватывания и заклинивания колодок тормозным барабаном, торможение осуществляется за счет прижатия двух колодок.
Обычно центральные тормоза располагают за коробкой передач на 2-осных автомобилях и на 3-осных - за раздаточной коробкой. На автомобилях МАЗ-500 и его модификациях центральный тормоз барабанного типа расположен на заднем мосту.
На новом автомобиле "Волга" ГАЗ-24 ручной тормоз с тросовым приводом действует на задние колеса, а в систему ножного гидравлического привода введено разделительное устройство для передних и задних колес, отключающее поврежденную часть системы привода.
Для проверки в эксплуатационных условиях эффективности действия тормозов автомобиля можно применять переносный прибор - деселерометр, дающий возможность оценить техническое состояние тормозной системы автомобиля по величине его максимального замедления при торможении. Прибор - инерционный, с пластинчатой пружиной 1 (рис. 141).
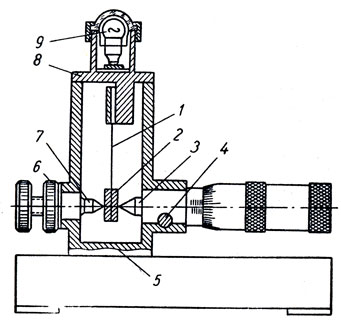 Рис. 141. Схема десселерометра механического типа: 1 - пластинчатая пружина; 2 - грузик; 3 - микрометрический винт; 4 - стопорный винт; 5 - корпус; 6 - контргайка; 7 - поджимной винт; 8 - крыша корпуса; 9 - сигнальная лампочка
Его устанавливают на полу кабины микрометрическим, винтом 3 по направлению движения автомобиля. Исправность тормозной системы определяют по сигнальной лампочке 9, которая должна загореться при достижении автомобилем определенной, заранее заданной предельной величины замедления, для легковых автомобилей без нагрузки наименьшее допустимое замедление 5,8 м/сек2, для грузовых автомобилей ГАЗ и ЗИЛ без груза - 5,0 м/сек2 и с полной нагрузкой - 4,0 м/сек2. Действие тормозов проверяется ежедневно перед выпуском автомобиля из гаража. В пути и по возвращении в гараж следует периодически проверять нагрев тормозных барабанов колес. Обычно зазор между накладками колодок и тормозным барабаном находится в пределах 0,1 - 0,4 мм . Так например, у автомобилей ГАЗ-53А и ГАЗ-66 (рис. 142) при замене фрикционных накладок 3 поверхность их обрабатывают так, чтобы диаметр тормоза, замеренный по поверхности накладок, после их приклепки был на 0,2 - 0,4 мм меньше внутреннего диаметра тормозного барабана 1.
Прилегание колодок 14 передних колес на автомобиле ЗИЛ-130 (рис. 143) к тормозному барабану 3 на расстоянии 20 - 30 мм от наружных концов накладок должно быть таковым, чтобы щуп 5 толщиной 0,1 мм не проходил вдоль всей ширины накладок. Эти зазоры увеличиваются до 0,4 мм у разжимного кулака 6 и до 0,2 мм у осей колодок, которыми служат эксцентриковые опорные пальцы 2. В результате износа рабочих поверхностей тормозных барабанов и фрикционных накладок тормозных колодок зазор между колодками и барабаном увеличивается, при этом осуществляется частичная регулировка тормозов колес (обычно при ТО-1).
Перед любой регулировкой тормоза колеса проверяют правильность затяжки подшипников ступицы и в случае необходимости доводят ее до нормы. Далее колесо вывешивают и производят регулировку.
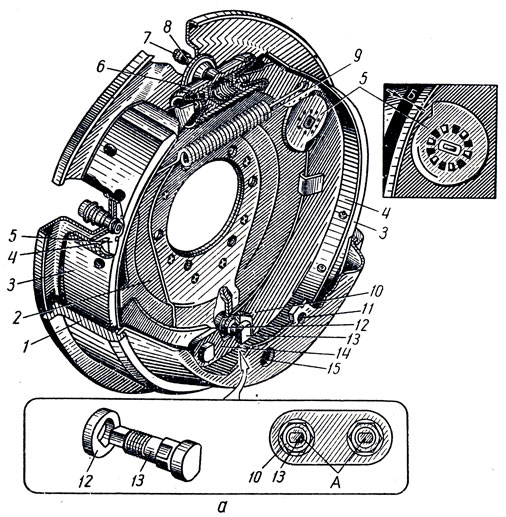 Рис. 142. Колесный (ножной) тормозной механизм автомобилей ГАЗ-53А и ГАЗ-66: а - механизм регулировки установки колодок; А - метки на опорных пальцах; Б - регулируемый зазор; 1 - тормозной барабан; 2 - щит тормозных колодок; 3 - фрикционная накладка; 4 - тормозная колодка; 5 - регулировочный эксцентрик колодки; 6 - цилиндр гидропривода колесного тормоза; 7 - защитный колпачок клапана; 8 - перепускной клапан прокачки тормозного привода; 9 - стяжная пружина тормозных колодок; 10 - гайка опорного пальца; 11 - отверстия (три) для винтов крепления фланца барабана к ступице колеса; 12 - регулировочный эксцентрик опорного пальца; 13 - опорный палец тормозной колодки; 14 - пластина опорных пальцев; 15 - отверстия (шесть) под шпильки крепления диска колеса
На автомобилях ГАЗ (см. рис. 142) частичную регулировку осуществляют поворотом эксцентрика 5, поворачивая при этом колесо вместе с барабаном 1 до тех пор, пока колодка не начнет его тормозить и далее, продолжая поворачивать колесо, постепенно отпускают эксцентрик до положения, когда колесо начинает вращаться свободно. При регулировке передней колодки колесо вращают вперед, а когда регулируют заднюю колодку, колесо вращают назад.
В тормозах с пневматическим приводом необходимость частичной регулировки тормозов колес определяется по увеличению хода штоков тормозных камер 13 (см. рис. 143), например, на автомобиле ЗИЛ-130 для передних колес ход штоков увеличивается с 15 до 35 мм и для задних - с 20 до 40 мм . На автомобилях МАЗ-500 ход штока тормозной камеры должен находиться в пределах 15 - 25 мм , а зазор между накладками и барабаном должен быть равен 0,4 мм . Тормоз колеса регулируют при увеличении хода штоков до 40 мм и превышении разницы в ходах штоков на каждом мосту автомобиля на 5 мм . Частичная регулировка тормоза на автомобиле ЗИЛ-130 осуществляется вращением регулировочного вала 10 червячного механизма поворота разжимного кулака 6. Колодки 14 в результате регулировки приближаются к тормозному барабану 3, и зазор между накладками и внутренней (рабочей) поверхностью барабана уменьшается.
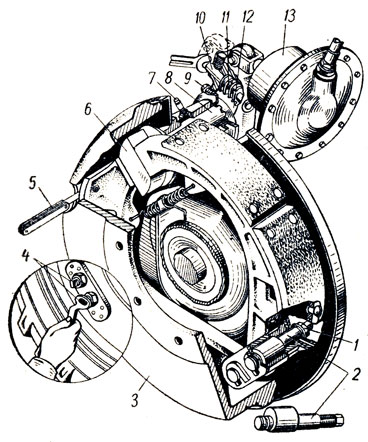 Рис. 143. Регулировка колесного тормоза переднего колеса автомобиля ЗИЛ-130: 1 - гайка опорного пальца; 2 - эксцентриковый опорный палец колодки; 3 - тормозной барабан; 4 - метки опорных пальцев; 5 - щуп; 6 - разжимный кулак; 7 - масленка вала разжимного кулака; 8 - вал разжимного кулака; 9 - пробка смазочного отверстия червячного механизма; 10 - регулировочный вал червяка; 11 - червяк; 12 - червячное колесо; 13 - тормозная камера
При ТО-2 необходимо снять тормозные барабаны, очистить детали тормоза и его привода, проверить состояние рабочей поверхности барабанов, накладок, опор и пружин колодок, опорных дисков, цилиндров гидропривода тормозов колес, тормозных камер и валов разжимных кулаков пневматического привода и защитных деталей тормозов. На рабочей поверхности барабанов не должно быть глубоких рисок и задиров, биение рабочей поверхности тормозного барабана ГАЗ-66 после его расточки не должно превышать 0,12 мм . Не допускается замасливание тормозных накладок. В случае замасливания хотя бы одной тормозной накладки или значительного износа поверхности накладки, когда расстояние от нее до головки заклепки крепления накладки менее 0,5 мм , все тормозные накладки левого и правого тормозов одного моста автомобиля заменяют. При наличии на накладках масла следует устранить причины, вызывающие его попадание в тормоза колес. В случае замасливания накладок и при отсутствии новых допускается промывка их в неэтилированном бензине в течение 20 - 30 мин с последующей очисткой поверхности накладок металлической щеткой, но такие тормоза будут действовать ненадежно, и при первой возможности накладки следует заменить. В случае расточки тормозного барабана и значительного увеличения зазора между накладками и его рабочей поверхностью допускается постановка металлических прокладок между поверхностью колодок и накладками.
Если колодки вращаются на своих осях с заеданием, то следует, не изменяя установки регулировочных эксцентриков опорных пальцев, снять колодки, очистить рабочие поверхности эксцентрикоз и проушин колодок от ржавчины и смазать их солидолом. После установки колодок лишнюю смазку необходимо удалить.
Полная регулировка тормоза колеса осуществляется после его разборки со снятием колодок, при замене накладок, ослаблении креплений осей колодок и когда частичная регулировка не дает результата. Полная регулировка колесного тормоза ГАЗ (см. рис. 142) осуществляется поворотом опорных пальцев 13 с регулировочными эксцентриками 12, а у колесного тормоза ЗИЛ (см. рис. 143) - поворотом опорных пальцев 2 при ослабленных гайках 1. Перед регулировкой опорные пальцы устанавливают выбитыми на их торцах метками А (см. рис. 142) или 4 (см. рис. 143) внутрь, что соответствует начальному положению эксцентриков, т. е. максимальному зазору между колодками и барабаном. На автомобилях ГАЗ (см. рис. 142), нажимая на педаль тормоза с постоянной силой 117,68 - 156,906 н (12 - 16 кГ), поворачивают против часовой стрелки опорные пальцы 13 так, чтобы нижняя часть накладки упиралась в тормозной барабан 1, и затягивают гайки 10. Далее, поворачивая регулировочные эксцентрики 5, устанавливают верхнюю часть накладки в такое положение, чтобы она упиралась в тормозной барабан. После этого прекращают нажимать на педаль тормоза и поворачивают регулировочные эксцентрики 5 в обратном направлении при свободном вращении колес. На автомобилях ЗИЛ (см. рис. 143) отсоединяют шток тормозной камеры 13 от рычага разжимного кулака и поворотом последнего прижимают колодки к барабану или, не отсоединяя шток, подают в тормозную камеру сжатый воздух под давлением 98066,5 - 147100 н/м2 (1 - 1,5 кГ/см2 ). Затем пальцы 2 поворачивают в одну или другую сторону, пока не будет обеспечено плотное прилегание колодок к барабану, чтобы при этом щуп толщиной 0,1 мм не проходил в зазор по всей ширине накладки в ее верхней части. Замер производят на расстоянии 20 - 30 мм от наружного конца накладки. Не отпуская рычага разжимного кулака и удерживая пальцы от проворачивания, затягивают гайки 1 пальцев. После этого рычаг соединяют со штоком тормозной камеры 13 и поворотом регулировочного вала 10 устанавливают ход штока в пределах 15 - 25 мм - для передних и 20-30 мм - для задних тормозов колес. После регулировки следует убедиться, что при включении и выключении подачи воздуха штоки тормозных камер перемещаются быстро и без заеданий.
Через 1000 - 1800 км пробега автомобиля (при ТО-1) надо смазать через масленки 7 консистентной смазкой УС-1 или УСс "автомобильная" валы разжимных кулаков 6. Через 10 000 - 18 000 км пробега той же смазкой смазывают червячные пары рычагов разжимных кулачков. Для нагнетания смазки необходимо вместо пробки 9 поставить пресс-масленку.
Систему гидравлического привода тормозов колес заполняют тормозной жидкостью, которую заливают в резервуар главного цилиндра 3 (рис. 144) через отверстие, закрываемое пробкой 4.
В качестве тормозной жидкости наиболее широко применяют гликолиевую жидкость ГТЖ-22 с антикоррозионной присадкой ТАФ. Эта жидкость обладает удовлетворительными температурно-вязкостными свойствами, что позволяет ее использовать летом и зимой по всей территории страны. Кинематическая вязкость ее при +50° С равна (7,9 - 8,3 сет) · 10-6 м2/сек, при 0° С она повышается до (80 - 70 ест) · 10-6 м2/сек, а при - 40° С до (1800 - 2200 сст) · 10-6м2/сек. Температура застывания жидкости не выше 65° С. Однако жидкость не обладает хорошими смазывающими свойствами и плохо защищает детали от коррозии. Поэтому при разборке узлов рекомендуется подвижные детали (манжеты и поршни) смазывать касторовым маслом. Жидкость ГТЖ-22 окрашивается в зеленый цвет. Она ядовита, поэтому, работая с ней, необходимо соблюдать меры предосторожности. В качестве заменителей применяют спиртокасторовые жидкости БСК (оранжевого или красного цвета) или ЭСК (красного или светло-желтого цвета), которые обладают хорошей смазывающей способностью, но недостаточными температурно-вязкостными свойствами. При температуре - 40° С эти жидкости застывают. Кроме того, спиртокасторовые жидкости обладают недостаточной стабильностью, при летней эксплуатации из них испаряются спирты, при температуре -5° С начинается кристаллизация касторового масла, которая интенсивно протекает при минус 20 - 22° С, в связи с чем жидкость рекомендуется применять при температурах не ниже минус 15 - 17° С. Эти жидкости недостаточно стабильны и при попадании в них воды.
Новым заменителем является тормозная жидкость ГТН, приготовленная на нефтяной основе. Она обладает хорошими температурно-вязкостными свойствами. При +50° С ее вязкость не менее (10 ест) · 10-6 м2/сек; при 0°С - (50 - 60 ест) · 10-6 м2/сек; при 40° С - (600 - 700 сет) · 10-6 м2/сек. Температура застывания жидкости не выше минус 63° С. Смазывающая способность ее удовлетворительная. Жидкость ГТН подкрашена в красный цвет. Она обладает активной способностью растворять резиновые детали (манжеты и шланги). Использование ее в системах гидропривода тормозов допустимо только в случае применения для изготовления деталей специальной нефтестойкой резины.
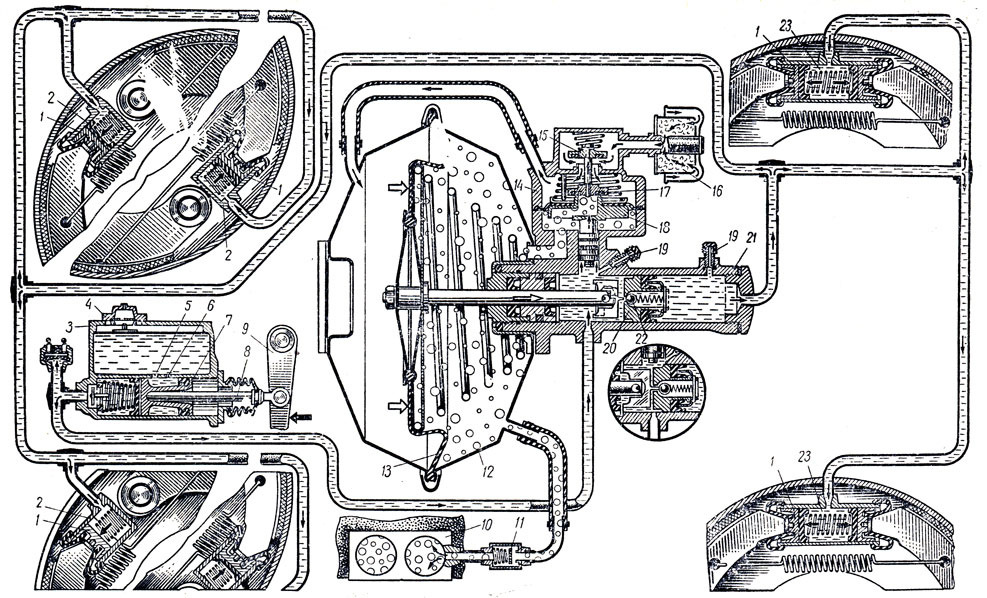 Рис. 144. Схема гидравлического привода тормозов колес автомобиля ГАЗ-66 с гидровакуумным усилителем
Наличие подтеканий жидкостей следует проверять ежедневно. Уровень жидкости в главном цилиндре проверяют при ТО-1. Он должен быть на 15 - 20 мм ниже наружной кромки заливного отверстия. Доливать до уровня необходимо только жидкость той же марки, которая заправлена в систему тормозов. В случае применения жидкости ГТЖ-22 рекомендуется сливать жидкость из системы через одно ТО-1, профильтровать ее и снова залить в систему. При ТО-2 и не реже, чем два раза в год, старую жидкость следует сливать, главный цилиндр 3 и колесные цилиндры 2 и 23, а также всю систему гидропровода промывать свежей тормозной жидкостью или спиртом, после этого подвижные детали смазы-гают касторовым маслом или жидкостями БСК и ЭСК и заправляют свежей тормозной жидкостью. Категорически запрещается применение для промывки и заправки ацетона и минеральных масел, так как это вызовет быстрое разрушение резиновых деталей.
Свободный ход педали-тормоза проверяется при ТО-1.
В системе гидропривода автомобиля ГАЗ свободный ход педали 9 должен быть равен 8 - 14 мм . Он зависит от величины зазора между штоком 8 и днищем поршня 7 главного тормозного цилиндра. В отторможенном состоянии этот зазор должен быть равен 1,5 - 2,5 мм , причем поршень 7 не должен перекрывать перепускное отверстие 6, а своей манжетой компенсационное отверстие 5. Поршень должен находиться между отверстиями. Зазор регулируют применением эксцентрикового устройства в месте сопряжения промежуточного рычага педали 9 со штоком 8 (на автомобиле ГАЗ-66) или применением резьбовой муфты, которая соединяет шток с резьбовым пальцем педали (на ГАЗ-53Ф, ГАЗ-51А, ГАЗ-53А). При максимальном нажатии на педаль она не должна доходить до упора в пол. Так, например, зазор между площадкой педали и полом у ГАЗ-53А и ГАЗ-66 должен быть не менее 25 мм .
Ход педали увеличивается при увеличенном зазоре между тормозными колодками и барабаном или при неправильной установке колодок.
Если педаль "проваливается", это значит, что тормозная жидкость просочилась из системы, и в систему гидропривода попал воздух. Для устранения подтеканий необходимо заменить поврежденные манжеты, трубки, штуцера, колесные цилиндры и подтянуть крепления. Удаление воздуха - прокачка тормозов также выполняется при каждом заполнении системы тормозной жидкостью. Для этого необходимо удалить грязь с главного 3 и колесных 2 и 23 цилиндров, заполнить тормозной жидкостью главный цилиндр 3 и на цилиндре 23 правого заднего колеса снять резиновый колпачок 7 (см. рис. 142) перепускного клапана 8 и надеть вместо него резиновый шланг, который опустить в стеклянный сосуд емкостью 0,5 л, заполненный наполовину тормозной жидкостью. После этого отворачивают на 1/2 - 3/4 оборота перепускной клапан и несколько раз быстро нажимают на тормозную педаль 9 (см, рис. 144), а затем медленно ее отпускают. При этом пузырьки воздуха выходят в банку с тормозной жидкостью. Когда выход пузырьков прекратится, нужно затянуть клапан, снять шланг и далее производить прокачку в следующем порядке: верхний цилиндр переднего правого колеса, потом нижний и, в такой же последовательности,- верхний цилиндр переднего левого колеса, потом нижний и далее - заднего левого колеса. По окончании прокачки колесных тормозов нужно прокачать цилиндр 21 гидровакуумного усилителя через клапаны 19, на которые поочередно надеваются резиновые шланги.
В процессе всей прокачки нужно следить за уровнем тормозной жидкости в главном цилиндре, систематически доливая жидкость до уровня.
Прокачивать систему можно также с помощью переносного бака для заправки тормозной жидкости. В бак заливают 6,5 л тормозной жидкости и ручным насосом для накачки шин доводят давление в баке до 147 100 - 196 133 н/м2 (1,5 - 2,0 кГ/см2 ), затем соединяют бак с главным цилиндром, завернув его штуцер вместо заливной пробки. При этом тормозная жидкость вытекает из цилиндра колеса под давлением сжатого воздуха, и нажимать на тормозную педаль не следует.
Тормозную жидкость, выпущенную из системы при прокачке, нельзя сразу использовать для доливки, так как в ней содержатся пузырьки воздуха и механические примеси. Необходимо отфильтровать жидкость и дать ей отстояться.
Для проверки работы гидровакуумного усилителя необходимо при неработающем двигателе несколько раз нажать на тормозную педаль, освобождая всю систему от разрежения. При исправном запорном клапане 11 разрежение в системе должно обеспечить одно-два эффективных торможения. Затем нажимают на педаль 9 усилием 294,200 - 490,332 н (30 - 50 кГ) и запускают двигатель. При исправном усилителе педаль несколько переместится к полу и будет слышен свист воздуха, выходящего через фильтр 16, который расположен в кабине. Если в момент запуска двигателя педаль не перемещается к полу и воздух из системы не выходит, это сигнализирует о неисправности запорного клапана 11 или трубок и шлангов, отводящих воздух от корпуса 12 усилителя. Для проверки клапана 11 впускного трубопровода 10 двигателя к нему подключают вакуумметр, который при работе двигателя на холостом ходу должен показывать разрежение 49033,2 н/м2 (0,5 кГ/см2 ). О негерметичности клапана судят по снижению разрежения после остановки двигателя. Оно должно снижаться не более чем на 19613,3 н/м2 (0,2 кГ/см2 ) в течение 3 - 5 мин.
Неисправность привода гидровакуумного усилителя также имеет место в случае засорения фильтра 16, при повреждении рабочей поверхности поршня 20 и цилиндра 21, при заедании поршенька клапана 18 управления и в случае уменьшения хода воздушного клапана 15. Для проверки хода воздушного клапана 15 снимают крышку корпуса 14 и нажимают на тормозную педаль. При этом воздушный клапан 15 должен переместиться в клапане 18 управления вверх на 2 - 3 мм . Если шипение воздуха слышно, но педаль к полу не перемещается, то причиной этого может быть негерметичность диафрагмы 13 корпуса усилителя или диафрагмы корпуса 14 клапана управления. При этом в случае торможения при работающем двигателе он будет работать с перебоями или заглохнет.
При неплотном прилегании шарикового клапана 22 к седлу поршня 20 или при разрушении манжеты поршня гидравлические полости низкого и высокого давления не разобщаются, что выявляется по обратному перемещению нажатой педали. После замены деталей усилителя систему необходимо промыть, заполнить жидкостью и прокачать.
Если после прекращения нажатия на педаль тормоза не растормаживаются, следует проверить регулировку свободного хода педали 9, прочистить компенсационное отверстие 5, проверить состояние резиновых манжет поршней 7 и 1 и, если они разбухли (что имеет место при попадании масла или другой нефтяной жидкости), сменить манжеты и заменить тормозную жидкость. К нерастормаживанию тормозов может также привести заедание поршня клапана 18 вследствие разбухания его манжеты или ослабления пружины клапана, которые необходимо заменить.
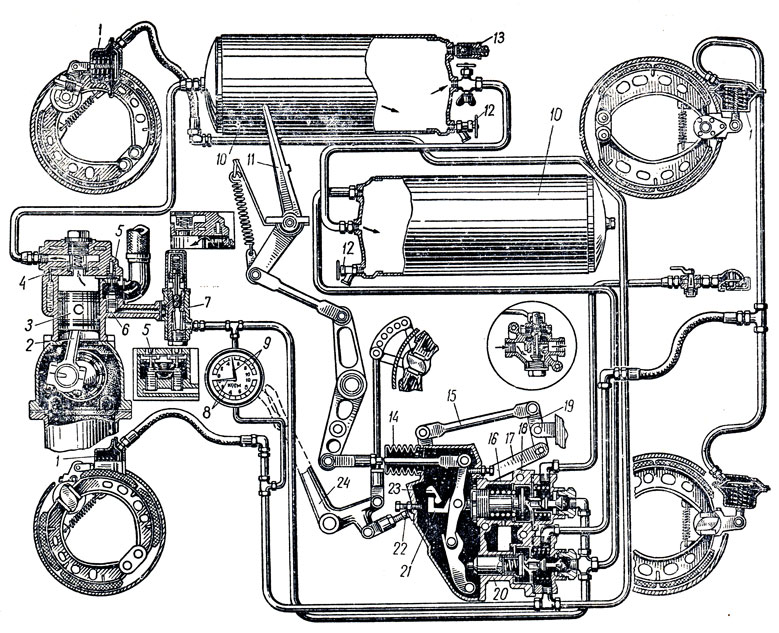 Рис. 145. Система пневматического привода тормозов автомобиля ЗИЛ-130
Основным показателем, характеризующим техническое состояние пневматического привода тормозов, является давление воздуха в системе, проверяемое манометром. Давление воздуха в баллонах 10 (рис. 145) автомобиля ЗИЛ-130, замеренное по верхней шкале 9 манометра, перед троганием автомобиля с места должно быть не ниже 441 299 н/м2 (4,5 кГ/см2 ), а при его движении должно быть в пределах 549 172 - 725 692 н/м2 (5,6 - 7,4 кГ/см2 ). Допускается лишь кратковременное снижение указанного давления при частых повторных торможениях. В случае торможения при неработающем двигателе давление не должно падать более чем на 98066,5 - 147 100 н/м2 (1,0 - 1,5 кГ/см2 ) при одном нажатии на педаль 11 ножного привода тормозного крана или при перемещении рычага 24 ручного привода центрального тормоза. При этом усилие от рычага 19 к тормозному крану передается через тягу 17. Для предохранения от полного расхода запаса воздуха при частых торможениях на длинных спусках запрещается выключать двигатель. Недостаточное давление воздуха в системе может быть следствием его утечки, ослабления натяжения ремня привода компрессора, износа деталей поршневой группы компрессора, неплотного прилегания клапанов 4 и 5, деталей тормозного крана 18, регулятора давления 7, предохранительного клапана 13 и нарушения их регулировок.
Не допускается утечка воздуха из системы пневматического привода. При неработающем двигателе и нажатой педали тормоза давление не должно падать более чем на 49033,2 н/м2 (0,5 кГ/см2 ) за один час. Необходимо тщательно следить за плотностью всех соединений в системе пневмопривода. Не допускается самопроизвольное торможение или плохое оттормаживание вследствие неплотной посадки клапанов тормозного крана.
Не допускаются перегрев компрессора, трещины на стенках его цилиндров, течи масла и появление в конденсате большого количества масла, стуки поршней 5, пальцев, подшипников и клапанов 4 и 5. Все крепления регулятора 7 должны быть плотно затянуты, его шарики и гнезда не должны иметь повреждений. При повышении давления воздуха в пневматической системе до 686 466 - 725 692 н/м2 (7,0 - 7,4 кГ/см2 ) регулятор должен отключать подачу воздуха компрессором.
Не допускается неплотная затяжка креплений предохранительного клапана 13. Рабочий поясок седла и его шарик не должны иметь царапин или повреждений. Повышение давления в системе до 980 665 н/м2 (10 кГ/см2 ) указывает на неисправность предохранительного клапана.
При ежедневном обслуживании проверяют крепления компрессора и натяжения его приводного ремня. Нормальный прогиб ремня должен составлять 10 - 15 мм при нажатии силой 29,42 - 39,2266 н (3 - 4 кГ) на его середину.
Во избежание замерзания конденсата в баллонах 10 и образования ледяных пробок в трубках зимой конденсат сливают из баллонов через краны 12 ежедневно. Слив конденсата из баллонов 10 нужно производить только при наличии в них сжатого воздуха. Запрещается подогрев баллонов открытым огнем. Если количество масла в конденсате за сутки превышает 10 - 15 см3, это является признаком неисправности компрессора.
В обычных условиях конденсат следует выпускать при каждом техническом обслуживании.
При ТО-1 дополнительно к работам, выполненным при ЕО, проверяют герметичность и состояние трубопроводов, исправность предохранительного клапана, привод тормозного крана, шплинтовку пальцев штоков тормозных камер, а также подтягивают крепления головки блока цилиндров компрессора, его картера, крышек подшипников и приводного шкива. Гайки шпилек и болты крепления головки компрессора следует затягиЕать равномерно в два приема, в установленной заводом последовательности. Окончательный момент затяжки должен быть в пределах 11,768 - 16,6713 н · м (1,2 - 1,7 кГм).
Исправность предохранительного клапана 13 проверяют, выпуская через него воздух из баллона. Для этого необходимо потянуть за стержень клапана. Клапан должен открываться самостоятельно при давлении воздуха в пневматической системе, равном 882 598 - 931 632 н/м2 (9,0 - 9,5 кГ/см2 ). Регулировка клапана осуществляется его винтом, закрепленным контргайкой. Касание между собой витков пружины шарика клапана не допускается. Седло клапана должно быть надежно затянуто в бобышке баллона 10. Периодически проверяют герметичность клапана, с этой целью его смачивают мыльной водой. Перед проверкой герметичности клапан разбирают, его детали промывают в керосине, просушивают, проверяют их состояние, и, в случае необходимости, заменяют. Герметичность считается достаточной, если при давлении 784 532 н/м2 (8 кГ/см2 ) на омыленном клапане образуется пузырь диаметром 25 мм за время не более 5 сек, а также прочищают отверстие, соединяющее внутреннюю полость клапана с атмосферой.
При ТО-2 дополнительно проверяют: крепление воздушных баллонов, крепление тормозного крана к раме, работу регулятора давления, работу системы привода, герметичность тормозных камер и кранов.
Уход за регулятором давления. Компрессор должен включаться в работу при давлении 549 172 - 588 399 н/м2 (5,6 - 6,0 кГ/см2). Это обеспечивается вращением регулировочного колпака регулятора 7Гпри завинчивании колпака давление, при котором включается компрессор, увеличивается, при отвинчивании - уменьшается. Положение колпака фиксируется с помощью контргайки.
Компрессор должен отключаться при давлении 686 466- 725 692 н/м2 (7,0 - 7,4 кГ/см2). Это обеспечивается с помощью прокладок под седлом регулятора 7; при уменьшении числа прокладок давление, при котором отключается компрессор, увеличивается; при увеличении - уменьшается.
Утечка воздуха через резьбовые соединения регулятора не допускается. Периодически следует очищать сетчатый и металлокера-мический фильтры регулятора давления и проверять его герметичность при помощи мыльной пены.
В холодное время неработающий или нечетко работающий регулятор следует отогреть обтирочными концами, смоченными горячей водой.
Проверка пневматического привода тормозов производится при работе двигателя на холостом ходу, когда давление воздуха в системе по показаниям верхней шкалы 9 манометров будет равно 686 466 - 725 692 н/м2 (7 - 7,4 кГ/см2). При этом давление воздуха в тормозных камерах 1, показываемое нижней шкалой 8 манометра, должно быть равно нулю. Для проверки необходимо нажать на конец педали 11 привода тормозов колес с силой 10 - 12 кГ. Давление воздуха в тормозных камерах 1 и баллонах 10 должно быть одинаковым и не ниже 441 299 н/м2 (4,5 кГ/см2), а конец педали 11 не должен доходить до упора в пол на 10 - 30 мм . Регулировку этого зазора и свободного хода педали 11 осуществляют (при правильно отрегулированном тормозном кране) изменением длины тяги 14 при помощи регулировочной вилки. При правильно отрегулированном приводе свободный ход конца тормозной педали на автомобилях, оборудованных комбинированным краном, должен быть равен 40 - 60 мм у а с одинарным краном - 10 - 25 мм .
При проверке герметичности тормозных камер 1 смачивают мыльной водой кромки фланца, места расположения болтов, стягивающих фланцы и место прохождения штока через корпус камеры. Нажатием на тормозную педаль 11 заполняют камеры воздухом и по появлению мыльных пузырей судят о наличии утечки воздуха. Для устранения утечки равномерно подтягивают все болты крепления крышки. Если утечка воздуха продолжается, то причиной ее могут быть деформации корпуса или крышки, которые устраивются правкой. Причиной утечки воздуха может быть также повреждение диафрагмы, которая в этом случае заменяется.
Уход за тормозными кранами заключается в их периодическом осмотре, проверке работоспособности и очистке от грязи, проверке герметичности и регулировке. Нужно следить за состоянием защитного резинового кожуха и креплением крышек к корпусу, так как попадание грязи внутрь может привести к прекращению его работы. Необходимо следить за очисткой воздуха от воды и масла, так как попадание последнего на резиновые клапаны и диафрагмы крана может вывести их из строя.
При проверке герметичности тормозного крана утечку воздуха обнаруживают по появлению мыльных пузырей. Для этого предварительно проверяемые места покрывают мыльной эмульсией. В случае негерметичности клапанов, регулируется при помощи регулировочных прокладок их ход или клапаны заменяются.
Если при проверке одинарного крана воздух выходит через выпускное отверстие при торможении, то это указывает на негерметичность атмосферного клапана, а в отторможенном положении - на негерметичность впускного клапана. Если утечка воздуха продолжается и после двух-трех торможений, то клапан вынимают и при повреждениях или износе резиновых конусов клапаны заменяют. При сборке ставят на место все прокладки седла клапана, и пробку крышки затягивают до отказа.
Если при проверке комбинированного крана воздух выходит через выпускное отверстие в отторможенном положении, то это указывает на негерметичность атмосферного клапана тормозов прицепа или впускного клапанатормозов автомобиля. При полном торможении воздух из магистрали прицепа должен выйти через выпускное отверстие. Если после нажатия на педаль еще через 1 - 2 сек воздух продолжает выходить, то это указывает на негерметичность впускного клапана прицепа или атмосферного клапана тормозов автомобиля. Клапаны нужно вынуть, осмотреть и заменить, если после двух-трех торможений продолжается выход воздуха.
Во всех кранах впускные клапаны должны иметь определенную величину открытия, равную 2,5 - 3 мм , которую регулируют прокладками, установленными между корпусом крана и штуцерами.
При регулировке комбинированных тормозных кранов свободный ход рычагов, не вызывающий перемещения диафрагм, в цилиндрах 16 и 20 тормозного крана регулируют упорными болтами. Он должен быть равен 1 - 2 мм . Рабочий ход штока 21 полости прицепа должен быть равен 5 мм .
При давлении в системе привода тормозов 686 466 - 725 692 н/м2, равном (7,0 - 7,4 кГ/см2 ), показание манометра, характеризующего давление в тормозных камерах, должно составлять 470719 - 519752 н/м2 (4,8 - 5,3 кГ/см2 ). Эго давление регулируют вращением направляющей штока 21 у изменяющей затяжку пружины полости тормозов прицепа. После регулировки ее положение направляющей фиксируется контргайкой.
Регулировка совместного действия ручного тормоза и комбинированного тормозного крана должна обеспечивать полное торможение при перемещении рычага 24 ручного тормоза назад на 4 - 6 зубьев сектора. Одновременно через тягу 22, уравнительный рычаг 19 и тягу 15 поворачивается вперед нижний конец кулака 23, который перемещает шток 21 тормозов прицепа. При этом впускной клапан цилиндра 16 закрывается, а атмосферный клапан открывается, и воздух из трубопровода прицепа выходит через отверстие крана в атмосферу, в результате чего срабатывает воздухораспределитель прицепа, включая его тормоза. Синхронность действия приводов ручного тормоза и атмосферного клапана тормозов прицепа обеспечивается изменением длины тяги 22.
Через 25 000 - 30 000 км пробега тормозные краны снимают, очищают, промывают керосином и их трущиеся поверхности смазывают тонким слоем смазки ЦИАТИМ-201.
При дополнительном уходе за компрессором через 25000 - 30000 км пробега необходимо очистить от смолистых отложений трубку, по которой масло сливается самотеком из картера компрессора.
Головку компрессора снимают через 40 000 - 50 000 км пробега. При этом очищают поршни, клапаны, их седла и пружины. Изношенные клапаны притирают или заменяют. Проверяют состояние уплотнительных резиновых колец плунжеров 6. При необходимости их заменяют. Перед установкой плунжеры смазывают тугоплавкой смазкой ЦИАТИМ-201.
Герметичность стенок головки цилиндров и ее соединений с трубопроводами проверяют воздухом под давлением 637 432 н/м2 (6,5 кГкм2). Она достаточна, если в мыльной воде, покрывающей головку цилиндров, при проверке происходит незначительное образование мелких пузырей. Для подтяжки подшипников нижних головок шатунов 2 удаляют их регулировочные прокладки. Не допускается подпиливание плоскостей разъема подшипников после удаления прокладок. Момент затяжки болтов шатунов должен составлять 14,71 - 16,6713 н · м (1,5 - 1,7 кГм).
Ручным тормозом можно пользоваться только на стоянках. Во время движения автомобиля разрешается пользоваться им в аварийных случаях. Шофер должен помнить, что сигнал торможения, как правило, не зажигается при затормаживании автомобиля ручным тормозом.
На подъемах и спусках с сухим дорожным полотном груженый автомобиль должен надежно удерживаться в неподвижном положении затянутым ручным тормозом.
При полном торможении рычаг ручного тормоза должен быть перемещен не более, чем на 3/4 его возможного хода по зубчатому сектору, и не должен упираться в сидение.
Не допускается заклинивание или заедание ручного тормоза. Во время движения автомобиля, фрикционные накладки колодок и тормозной барабан не должны быть загрязнены или замаслены и не должны иметь трещин, обломов, короблений, неравномерного износа и ослабления стяжных пружин. Не допускаются ненадежная фиксация рычага в затянутом состоянии и ослабление крепления деталей привода тормоза, кронштейна колодок, тормозного барабана, диска, храпового механизма, а также отсутствие шплинтов. Во время движения автомобиля, когда тормоз не затянут, барабан его не должен нагреваться.
При ежедневном техническом обслуживании проверяют работу ручного тормоза и в случае необходимости его регулируют.
При ТО-1 проверяют состояние и действие ручного тормоза; подтягивают крепления зубчатого сектора, деталей привода, кронштейна колодок, тормозного барабана, опорного диска тормоза; проверяют фиксацию рычага при полном торможении и величину хода рычага. Если ход рычага недостаточен, тормоз регулируют.
Один раз в год следует разобрать ручной тормоз, очистить детали и проверить их состояние. Ось колодок и трущиеся детали привода смазывают тонким слоем консистентной смазки и тщательно регулируют положение колодок. Зазор между колодками и барабаном при этом уменьшится.
Регулировка центрального колодочного тормоза автомобилей ЗИЛ-130, ЗИЛ-131, ЗИЛ-157К должна обеспечить полное торможение при отходе рычага 4 (рис. 146) назад на четыре-шесть зубьев сектора 7. При большом ходе рычага, указывающем на наличие больших зазоров между накладками и барабаном, необходимо отъединить от регулировочной вилки 5 рычаг 4, отпустить контргайку 6 вилки и навернуть вилку на тягу 9. Затем контргайку затягивают и вилку соединяют с рычагом 4. Регулировку проверяют, вращая рукой тормозной барабан 1 при вывешенных колесах; начало торможения должно наступать, когда стопорная защелка 8 попадает во вторую впадину зубчатого сектора 7.
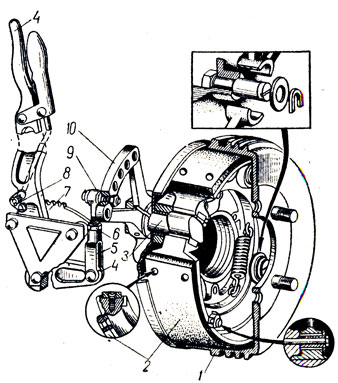 Рис. 146. Ручной (центральный) тормоз автомобиля ЗИЛ-130: 1 - барабан тормоза; 2 - фрикционная накладка колодки; 3 - вал с разжимным кулаком; 4 - ручной рычаг; 5 - регулировочная вилка тяги привода; 6 - контргайка вилки; 7 - зубчатый сектор ручного рычага; 8 - стопорная защелка привода; 9 - тяга привода; 10 - регулировочный сектор-рычаг
При значительном износе фрикционных накладок 2, когда с помощью навертывания регулировочной вилки 5 не удается установить требуемую величину хода рычага ручного тормоза, необходимо изменить исходное положение разжимного кулака 3. Для этого палец тяги 9 соединяют со следующим вышерасположенным отверстием регулировочного сектора-рычага 10. Затем в случае необходимости корректируют длину тяги 9. После регулировки тщательно шплинтуют соединение и затягивают контргайку 6. Окончательно регулировку проверяют во время движения автомобиля.
Особенности регулировки ручного тормоза грузового автомобиля ГАЗ заключаются в следующем. При вывешенном заднем колесе автомобиля рычаг 10 (рис. 147) ручного тормоза устанавливают в переднее положение и регулировочный винт 11 завертывают до отказа, чтобы тормозной барабан 3 нельзя было повернуть усилием рук. При ввертывании винта 11 происходит продольное перемещение сухаря 14, который своими коническими поверхностями с помощью пальцев 13 раздвигает колодки 4, прижимая их к тормозному барабану 3. Затем регулируют длину тяги 8. Для этого отвертывают контргайку 5 и завертывают регулировочную гайку 6 до упора рычага 7 в разжимной стержень 2, после чего гайку 6 отпускают на 2 - 3 оборота. Далее регулировочный винт 11 отпускают нa 1/3 - 1/2 оборота, что соответствует 4 - 6 щелчкам концов плоской пружины 12. Эта пружина посредине укреплена штифтом к головке регулировочного винта 11, имеющей двенадцать прорезей, а своими концами входит в прорезь сухаря 14. После отпускания винта 11 проверяют возможность свободного вращения тормозного барабана без задевания колодок и затягивают контргайку 5.
После окончания регулировки рычаг 10 перемещают так, чтобы фиксирующая защелка 9 попала в третью впадину зубчатого сектора 1 (считая от тормоза). При этом барабан 4 должен проворачиваться с трудом.
Окончательно регулировку проверяют при движении автомобиля. Тормоз должен надежно останавливать автомобиль, движущийся со скоростью 1,38889 м/сек(5 км/ч). Тормозной барабан не должен нагреваться.
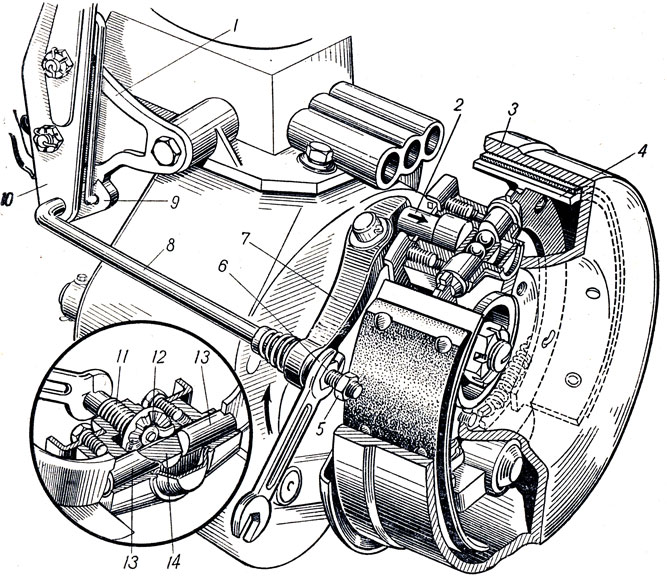 Рис. 147. Ручной (центральный) тормоз грузовых автомобилей ГАЗ: 1 - зубчатый сектор; 2 - разжимный стержень; 3 - тормозной барабан; 4 - тормозная колодка; 5 - контргайка; 6 - сферическая гайка; 7 - приводной рычаг; 8 - тяга; 9 - защелка; 10 - рычаг ручного тормоза; 11 - регулировочный винт; 12 - пружина; 13 - палец колодки; 14 - плавающий сухарь
На автомобиле МАЗ-500 тормозной барабан 15 (см. рис. 132) ручного тормоза установлен на фланце вала главной передачи, а тормозные колодки на суппорте картера редуктора заднего моста. Регулировку действия тормоза осуществляют изменением длины тяг и тросов привода.
|