Выравнивание неровностей в панелях кузова при помощи пластических масс
Заделку вмятин в панелях кузова и оперения с применением пластических масс можно осуществить двумя методами: заполнением и напылением. Для заделки вмятин заполнением обычно применяют композиции на основе эпоксидных смол. Для эгого можно также применять шпаклевки Э-4020 (ВТУКУ 496-57), Э-4022 (ВТУУХ 56-58) или ЭП-00-10 (ГОСТ 10277-76).
Перед применением этих шпаклевок в них добавляют отверди- тель № 1 (50%-ный раствор гексаметилендиамина в этиловом спирте): 8,5% - для шпаклевки Э-4020 или ЭП-00-10 и 5% - для шпаклевки Э-4022. Шпаклевкой ЭП-00-10 можно выправить вмятины до 2 мм глубиной, а с наполнителем из стального и чугунного порошка - до 5 м. Для заделки углублений до 8 мм применяют шпаклевку Э-4020, а углубления до 15-20 мм - Э-4022. Все указанные шпаклевки имеют хорошую адгезию к металлу и высыхают при температуре 18-20°С за 24 ч, а при 60-70°С шпаклевка Э-4020 - за 6 ч, шпаклевка ЭП-00-10 - за 7 ч, а шпаклевка Э-4022 - за 8 ч.
Эпоксидные композиции могут быть изготовлены на месте потребления из составных частей, чаще всего из эпоксидной сколы ЭД-16 или ЭД-20 (ГОСТ 10587-76), пластификатора - добутилфталата (ГОСТ 22102-76), наполнителя и отвердителя. Эпоксидные смолы в полимерных композициях являются связующими, пластификаторы уменьшают хрупкость, увеличивают удельную ударную вязкость и эластичность отвержденных эпоксидных смол, наполнители увеличивают теплопроводность, повышают коэффициент линейного расширения и понижают усадку смолы. Поэтому наполнители влияют на физико-механические и технологические свойства компаунда.
В качестве наполнителей применяют слюдяную пыль, измельченный асбест, стальной или чугунный порошок и др. Вид и количество отвердителя обусловливают скорость и степень изменения физического состояния композиции. Для заделки вмятин в кузовах и оперении обычно пользуются аминными отвердителями (полиэтиленполиамином или гексаметилендиамином), при которых отверждение композиции может произойти без подогрева в нормальных температурных условиях.
В табл. 1 приведены некоторые составы композиций, которые применяются при ремонте кузова.
Таблица 1
Составы композиций для ремонта кузова
Для приготовления мастики смолу ЭД-16 или ЭД-20 нагревают до температуры 50-60°С, вводят в нее при тщательном перемешивании дибутилфталат и полученную смесь перемешивают в течение 5-6 мин до получения однородной массы. Затем в смесь вводят наполнитель и после пятиминутного перемешивания смесь охлаждают до комнатной температуры и помещают в герметически закрывающийся сосуд. Наполнители перед введением в смолу необходимо подсушить и проверить, чтобы не было посторонних включений, а размеры частиц должны быть не более 75-100 мкм.
Полиэтиленполиамин вводят в смесь перед употреблением небольшими порциями, чтобы избежать самопроизвольного разогрева смеси, в результате чего она может быстро отвердеть. Полиэтиленполиамин до его употребления предварительно нагревают до температуры 105-110°С для удаления влаги и выдерживают при этой температуре 3 ч.
Чтобы обеспечить точную дозировку компонентов состава, тщательность перемешивания и соблюдения при этом правил техники безопасности, эпоксидную мастику следует приготавливать механизированным способом с использованием установки (рис. 48), предложенной Сибирским филиалом ГОСНИТИ. Эта установка имеет смеситель, устройство для подготовки и дозировки эпоксидной смолы, для выпаривания и дозировки полиэтиленполиамина и пластификатора.
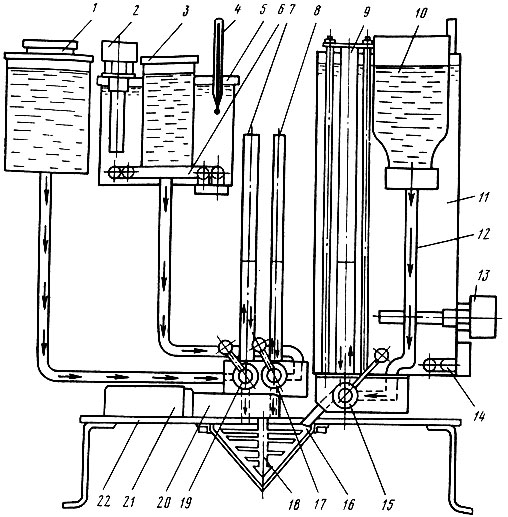 Рис. 48. Схема установки для приготовления эпоксидной мастики: 1, 3 и 10 - сосуды для дибутилфталата, полиэтиленполиамина и эпоксидной смолы: 2 и 13 - температурные реле; 4 - термометр; 5 и 11 - баки для выпаривания полиэтиленполиамина и разогрева смолы; 6 и 14 - электронагреватели; 7, 8 и 9 - мерные цилиндры; 12 - гибкий шланг; 15, 17 и 19 - перепускные трехходовые краны; 16 - смеситель; 18 - мешалки; 20 - редуктор; 21 - электродвигатель; 22 - рамка
Перед началом работы из бака 11 извлекают гибкий шланг 12 с крышкой сосуда 10 и заполняют бак водой, уровень которой должен быть на 15 мм ниже верхнего края. Бак 5 до того же уровня заполняют трансформаторным маслом, сосуд 10 соединяют с гибким шлангом 12 и помещают в бак 11. Сосуды 1, 3 и 10 заправляют соответственно дибутилфталатом, полиэтиленполнамином и эпоксидной смолой. При этом трехходовые краны 15, 17 и 19 должны быть закрыты. Затем сосуд 10 соединяют шлангом 12, помещают в бак 11 и включают в сеть электронагреватели 6 и 14. Реле 2 и 13 должны быть отрегулированы на температуру соответственно 110±5 и 85±5°С.
Как только вода нагреется до необходимой температуры, переключают трехходовые краны и заполняют мерные цилиндры 7, 8 и 9. После этого засыпают в бачок смесителя наполнитель, выдерживают его в течение 0,5-1 мин, отбирают из цилиндров необходимое количество компонентов в смеситель и включают электродвигатель 21 привода мешалки. По окончании перемешивания бачок снимают и ставят на подставку на рабочем месте.
Для повышения производительности к установке прилагается несколько таких бачков. Чтобы клеевой состав не прилипал к бачку и мешалке 18, их рекомендуется изготовлять из полимерного материала - фторопласта.
Применение установки обеспечивает объемную дозировку, механическое смешивание компонентов и тем самым повышает качество клеевых составов. Производительность процесса при этом увеличивается и что особенно важно, улучшаются условия труда.
Время отверждения приведенных в табл. 1 составов при естественной температуре 18-23°С - 24 ч, а с повышением температуры оно резко сокращается. Так, при 40°С время отверждения составляет 10-12 ч, при 60°С - 3-4 ч, при 80°С - 1,5-2 ч, а при 100°С - 0,5-1 ч. Для сушки отремонтированного участка можно применять передвижную рефлекторную (терморадиационную) установку.
Подготовка поверхности поврежденного участка при ремонте эпоксидными составами заключается в тщательной очистке ее от всяких загрязнений, шероховании наждачным полотном или шлифовальным диском на фибровой основе и обезжиривании поверхности протиркой ветошью, смоченной в органическом растворителе (ацетоне, бензине Б-70 или др.). Шероховатость металлической поверхности в пределах 4-5-го класса чистоты поверхности по ГОСТ 2789-73 способствует лучшему сцеплению с полимерным покрытием. Эпоксидную мастику наносят шпателем, слегка смазанным глицерином, чтобы к нему не приставала мастика.
Для выравнивания поверхностей кузовов, кабин и оперения методом напыления широкое применение получили порошки ТПФ-37 (СТУ 12-10212-65). Эти порошки выпускаются промышленностью и отвечают требованиям, предъявляемым к порошкообразным материалам, применяемым для газопламенного напыления.
Одним из основных факторов, определяющих работоспособность полимерных покрытий, является адгезия материала покрытия к подложке и ее устойчивость в эксплуатационных условиях. Существенное влияние на адгезионную прочность покрытий из полимеров на металлах оказывают температурно-временные условия формирования адгезионных металлополимерных соединений. Варьируя температуру и время термического воздействия, можно в значительных пределах изменять прочность соединений и их устойчивость в условиях эксплуатации. Основным технологическим фактором при формировании покрытий из термопластичных полимеров является температура предварительного нагрева металла.
Качество деталей и изделий с полимерным покрытием во многом зависит от предварительных операций подготовки поверхностей, подлежащих покрытию, и подготовки полимерных материалов. Отсутствие систематических исследований длительной устойчивости адгезионной прочности полимерных покрытий в процессе эксплуатации ведет к заимствованию рекомендаций по подготовке поверхностей из смежных областей (лакокрасочные, гальванические покрытия) без учета специфики металлополимерного комплекса. Однако существуют общепринятые приемы подготовки, что позволяет облегчить выбор того или иного способа.
Любому виду подготовки покрываемых поверхностей должна предшествовать их очистка от жировых загрязнений, т. е. операция обезжиривания. Обычно для обезжиривания применяются органические растворители (уайт-спирит, бензин и др.), специальные щелочные растворы или эмульсии.
Использование эмульсионных составов привело к удешевлению процесса очистки, снижению пожароопасности и токсичности при обеспечении высокой эффективности.
Для очистки поверхности участков от ржавчины и окалины и обеспечения необходимой шероховатости следует руководствоваться указаниями, приведенными в предыдущей и последующих главах. Лучше всего пользоваться для этой цели иглофрезой. Поверхность, подлежащая напылению, должна не только быть обезжиренной, чистой и сухой, но и быть открытой, доступной для напыления, не иметь незачищенных сварных швов, острых ребер и углов.
На металлические панели, отдельные участки которых имеют разное сечение без плавных переходов, наносить покрытие трудно вследствие разной температуры нагрева таких участков.
Подготовленную поверхность детали следует подогреть до температуры, равной температуре растекания наплавленного порошка.
Качество покрытия в значительной степени зависит от теплового режима, т. е. температуры в период прохождения частиц полимера через пламя, температуры поверхности и температуры оплавления наносимого материала. Для нанесения покрытия из полимерных порошковых материалов при заделке вмятин в панелях кузова могут быть применены три основных способа: газопламенный, теплолучевой и струйно-электростатический.
Газопламенный метод нанесения покрытия. На автотранспортных предприятиях и авторемонтных заводах термопластик ТПФ-37 обычно наносят на ремонтируемую поверхность газопламенным напылением при помощи аппарата УПН-6-63. Его суть заключается в нагреве поверхности, подлежащей покрытию, открытым пламенем, через факел которого подается дисперсный полимерный материал. Частицы полимера размягчаются, расплавляются и при условии прогрева поверхности до температуры, превышающей температуру плавления используемого материала, образует покрытие.
При нанесении покрытия предварительно прогревают участок поверхности без подачи полимерного материала до температуры 215-220°С, Детали небольшой теплоемкости (толщина стенки l-2 мм) могут быть прогреты за один медленный проход газопламенной горелки. Более теплоемкие детали прогреваются за три-четыре прохода. После прогрева поверхности включают подачу дисперсного материала и ведут последовательный обдув полимером нагретого участка. Покрытия наносят при скорости перемещения горелки-распылителя около 1,5 м/мин. Первый тонкий слой порошка укатывают металлическим катком, наносят второй и последующие слои пластмассы до полного заполнения неровности. Каждый вновь нанесенный слой укатывают катком, обеспечивающим получение плотного монолитного слоя пластической массы. Во избежание прилипания металлического катка к пластмассе его необходимо по мере нагревания охлаждать в воде.
Для получения качественного покрытия очень важно придерживаться рекомендуемой температуры предварительного подогрева металла обрабатываемой поверхности. Недостаточно подогретый металл не будет способствовать расплавлению и прилипанию порошка к выравниваемой поверхности; на перегретом металле может появиться окалина и резко ухудшиться адгезия пластмассы к поверхности металла. Для контроля температуры металла перед нанесением термопластика можно пользоваться термоиндикатором, термохромовым карандашом или термощупом.
В качестве горючих газов применяют ацетилен, природный газ, пропанбутановую смесь. Предпочтение отдают ацетилену, который дает более высокую температуру пламени и выделяет относительно меньшее количество воды, катализирующей окисление полимерных материалов.
В последнее время для полимерных материалов начинает использоваться плазменное напыление. Несмотря на высокую температуру факела, полимер разлагается лишь частично вследствие чрезвычайно непродолжительного контакта с плазмой в инертной атмосфере. Высокая температура процесса приводит к мгновенному прогреву тонкого поверхностного слоя металла, что позволяет уменьшить энергетические затраты. Способом плазменного напыления могут быть нанесены любые полимеры.
Таким образом, технологическая схема процессов плазменного напыления проста, но получить покрытия высокого качества достаточно сложно. Закономерность пленкообразования в таких процессах не изучена, имеющиеся сведения носят характер рекомендаций.
Теплолучевой метод, разработанный в отделе механики полимеров АН БССР, по всем параметрам превосходит газопламенный, являясь более универсальным и высокопроизводительным.
Сущность метода состоит в том, что струя порошкообразного полимера подается в мощный поток светотепловых лучей, где частицы материала плавятся и с большой скоростью наносятся на покрываемую поверхность. Ударяясь о поверхность, полимер сцепляется с ней, образуя покрытие.
В качестве источников лучистой энергии используются газонаполненные кварцевые лампы накаливания типа КИ-200, специально предназначенные для интенсификации технологических процессов, связанных с нагревом и расплавлением.
В комплект прибора (рис. 49, а) входят: аппарат 1, где создается воздушно-порошковая смесь, поступающая по шлангу 2 к щелевому распылителю 4; нагреватель, состоящий из нескольких параболических отражателей 6, в фокусах которых расположены кварцевые лампы 5, специально предназначенные для интенсификации технологических процессов, связанных с нагревом и расплавлением. Нагреватель снабжен рукояткой 3, а отражатели укреплены шарнирно и могут поворачиваться на определенный угол для наиболее целесообразного регулирования фокусировки суммарного потока. Установка имеет электрорегулирующие устройства, позволяющие изменять интенсивность теплового потока в широком диапазоне.
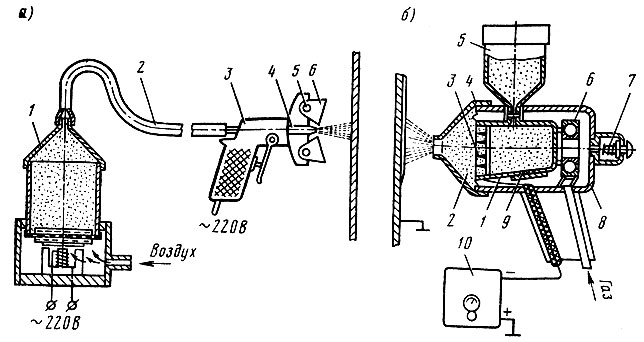 Рис. 49. Прибор для нанесения полимеров: а - теплолучевым методом; б - струйно-электролитическим методом
Для увеличения производительности в одном агрегате можно применять несколько ламп. Воздушно-порошковая смесь создается вибро-вихревым аппаратом установки. Для этой цели может быть использован также питательный бачок установки газопламенного напыления УПН-6-63.
По сравнению с газопламенным теплолучевой метод более экономичен, так как при этом порошка полимера расходуется на 25-30% меньше при меньшей энергоемкости (в 3,5-4 раза) процесса. Метод в 1,5-1,8 раза более эффективен, чем газопламенный. Наносимые теплолучевым методом покрытия имеют лучшие физико-механические свойства и адгезию к подложке. Покрытия теплолучевым методом можно наносить в инертной и взрыво-огнеопасных средах, так как нет соприкосновения с открытым пламенем.
Лучевые нагреватели находят широкое применение для интенсификации всех процессов нанесения полимерных покрытий, в том числе в автоматизированных установках.
Струйно-электростатический метод. Сущность его состоит в том, что частицы полимера, находящиеся во взвешенном состоянии, заряжаются на электрической сетке и преодолевают сопротивление мелкоячеистого фильтра лишь при возникновении электрического поля между электродом и деталью.
Устройство выполнено в виде пистолета-распылителя и имеет питательный бачок, укрепленный непосредственно на его корпусе 8 (рис. 49, б). Основным элементом распылителя является рабочая камера 1, внутри которой расположена электродная сетка 3 с зарядными иглами. Один торец камеры закрыт мелкоячеистым фильтром 2, к другому прикреплен пневматический вибратор 6.
Работает устройство следующим образом. Заполнив питательный бачок 5 и рабочую камеру полимером, подают высокое напряжение на электродную сетку и включают подачу газа. Газ приводит в действие вибратор и через клапан 7 выходит в атмосферу. Распылитель подносят к покрываемой поверхности изделия, которое обычно заземляется, т. е. имеет потенциал, обратный по знаку потенциалу электродной сетки. Заряженные частицы под действием возникшего электростатического поля преодолевают сопротивление фильтра и устремляются к изделию. Для интенсификации процесса выход газа в атмосферу ограничивается: газ проходит через пористую перегородку 9 в рабочую камеру, создает дополнительный напор и улучшает псевдоожижение дисперсного материала. Процесс нанесения покрытий автоматически прекращается при удалении устройства от покрываемой поверхности. Величина высоковольтного потенциала, подаваемого на электродную сетку, устанавливается с таким расчетом, чтобы предотвратить возникновение коронного разряда при максимальном приближении устройства к заземленной поверхности.
Клапан 7 служит для регулирования процесса и выпуска избыточного газа в атмосферу. Пистолет имеет сменные насадки 4. В качестве высоковольтных генераторов 10 могут быть применены любые источники, позволяющие получать напряжения 10-20 кВ. Наиболее удобен в работе аппарат АФ-3, выпускаемый Московским заводом электромедицинской аппаратуры.
Струйно-электростатический метод имеет ряд положительных особенностей. Во-первых, покрытия получаются хорошей сплошности и равномерной толщины. Процесс нанесения покрытий регулируется автоматически. Это объясняется тем, что высокое электрическое сопротивление налипшего слоя частиц заставляет силовые линии искать места с меньшим сопротивлением, т. е. направлять к участкам поверхности, более углубленным или еще не покрытым. Во-вторых, отсутствует потеря материала, так как частицы полимера преодолевают сопротивление фильтра только под действием электрического поля.
Процесс нанесения покрытия безопасен, так как питающее напряжение может быть отрегулировано на отсутствие коронного разряда при максимальном приближении устройства к поверхности покрываемой детали.
После отверждения нанесенный слой пластмассы зачищают ручным или механизированным инструментом.
Для механизации процесса обработки поверхности после нанесения термопластика или эпоксидной мастики применяют пневматический абразивный инструмент и шлифовальные диски на фибровой основе.
|