Устранение повреждений в кузове заменой негодных панелей ремонтными
Такой ремонт не представляет особой трудности при замене негодной панели, укрепленной к каркасу заклепками или гвоздями (у кузова автобуса с деревянным каркасом). Гораздо сложнее выполнить такой ремонт на цельнометаллическом кузове сварной конструкции, с панелями сложной геометрической формы. Работа осложняется еще тем, что некоторые ремонтные панели не входят в номенклатуру запасных частей и их приходится изготовлять непосредственно в цехах авторемонтного предприятия.
Изготовление кузовных ремонтных деталей (ДР). Основными этапами подготовки производства к изготовлению ремонтных деталей являются: выявление наименований (типоразмеров) деталей, подлежащих изготовлению; разработка технологического процесса изготовления деталей. Первый этап заключается в изучении большого количества металлических кузовов (кабин, оперения), поступивших в ремонт, и выявлении наиболее часто разрушающихся участков панелей и оперения. На основании исследования выявляются коэффициенты сменности деталей и составляются спецификации панелей, подлежащих изготовлению. Так, в результате анализа повреждений на кузовах и оперении автомобилей ГАЗ-24 "Волга" выявлено, что при капитальном ремонте около 40 деталей могут иметь повреждения (коррозию, разрывы и др.), поддающиеся ремонту только заменой разрушенной части панели ремонтной деталью.
Большинство кузовных ремонтных деталей может быть приведено к сравнительно небольшому числу групп (типов), которые имеют одинаковый план обработки. В основу типизации принята классификация изготавливаемых деталей по технологическим признакам, которые определяют характер технологического процесса их изготовления. Главнейшим технологическим признаком Для деталей кузова является их форма. С этой точки зрения все кузовные детали, изготавливаемые из листовой стали, можно разбить на три группы: неглубокие пологие детали, выполняемые вырезкой по контуру и простой гибкой; пространственные детали, выполняемые более сложной гибкой или неглубокой формовкой; полые пространственные детали неправильной геометрической формы - асимметричные или симметричные, выполняемые вытяжкой различной степени.
От технологии изготовления деталей в значительной степени зависит и их качество. Типовой состав процесса изготовления ремонтных деталей на авторемонтных заводах слагается из следующих основных операций: правки листа стали; раскроя листа; резки заготовок по разметке; загиба деталей или формовки на специальном оборудовании; обрезки готовых деталей; сверления, правки и зачистки. Последние три операции выполняют при постановке и подгонке деталей на постах ремонта кузова.
На специализированных кузоворемонтных производствах при наличии большой производственной программы ремонтные детали кузова изготавливают штамповкой на прессах или обтяжкой.
Правка листовой стали. Листовая сталь, применяемая для ремонта и изготовления панелей кузовов и оперения автомобилей глубокой вытяжкой, в процессе штамповки или формовки другими способами на специальном оборудовании часто испытывает напряжения, близкие к пределу прочности. Поэтому такая листовая сталь должна удовлетворять требованиям в отношении механических и технологических свойств, микроструктуры, чистоты поверхности, не иметь расслоений и быть однородной по толщине.
В зависимости от назначения детали металлического корпуса кузова можно разделить на лицевые детали (крыша, двери, капот, крылья и т. п.), к качеству поверхности которых предъявляются более высокие требования, а не только чтобы его свойства соответствовали требуемой сложности деформации этих деталей; внутренние детали (пол, брызговики, внутренние панели т. п.) и детали каркаса кузова (стойки, усилители и т. п.), для изготовления которых необходимо соответствие свойств металла листа требуемой сложности вытяжки.
Для деталей кузова автомобиля применяется в основном низкоуглеродистая сталь (ГОСТ 9045-70) с содержанием углерода не более 0,08% двух категорий: ОСВ - для штамповки деталей с особо сложной вытяжкой и СВ - со сложной вытяжкой. Обе эти категории листов выпускаются трех марок: 08Ю и 08Фкп - нестареющие и 08кп - стареющие.
Одним из главных параметров, учитываемых при определении сложности вытяжки кузовных деталей, является максимальное относительное удлинение, получаемое каким-либо элементом детали в процессе ее деформирования.
В случае применения листовой стали, подверженной старению, ее твердость под влиянием старения значительно увеличивается, ударная вязкость падает, повышаются пределы упругости и прочности и понижается пластичность с образованием длинной площади текучести.
Во избежание разрыва заготовок в процессе вытяжки такую листовую сталь до передачи в производство правят на листоправильных многовалковых машинах, предназначенных для правки листов в холодном состоянии. Правке подлежат также листы металла, которые часто поступают на авторемонтные заводы с дефектами, нарушающими плоскостность листа (волнистость, местная выпуклость и т. п.). Листы из металла с пределом прочности до 28 кгс/мм2 и толщиной до 3 мм правят на листоправильных машинах с 11-29-ю валками. Чем тоньше выправляемый лист, тем больше должно быть валиков и тем меньше их диаметр. Валки в машинах имеют постоянный диаметр и расположены в два ряда в шахматном порядке с параллельными или непараллельными рядами валков. Листы толщиной до 4 мм обычно правят на листоправильных многовалковых машинах с непараллельными рядами валков, расположенных под углом друг к другу. Вследствие такого расположения рядов расстояние между валками увеличивается в направлении от входных валков к выходным. Поэтому кривизна перегиба листа от валка к валку постоянно уменьшается и у предпоследнего валка становится близкой к кривизне упругого изгиба.
При пропуске между валками лист втягивается в вальцы и проходит через все валки, получая повторные пластические изгибы в противоположные стороны, вследствие чего он принимает плоскую форму. Количество проходов (пропусканий) листа или полосы через рабочие валки машины, необходимое для полного выправления листа или полосы, зависит от механических свойств металла, из которого изготовлены листы и полосы, толщины выпрямляемых листов и полос. Полная правка тонких листов и полос требует большего количества проходов, чем листов и полос средней и большой толщины. Количество проходов - от одного до четырех в зависимости от указанных выше дефектов.
Деформация при вальцовке сопровождается появлением внутри кристаллических сдвигов, которые, изменяясь последовательно в зависимости от направления изгиба листа и будучи равновеликими, так как радиус валков постоянный, взаимно компенсируют друг друга, не вызывая остаточной деформации общего объема. Значительный изгиб при вальцовке перераспределяет существующие напряжения, вследствие чего в провальцованном листе первоначально неравномерное распределение напряжений стремится стать более однородным по сечению листа.
В результате такой обработки лист несколько упрочняется - площадка текучести на кривой растяжения почти совсем исчезает, получается плавный переход кривой от упругого к пластическому состоянию металла и увеличивается способность металла к пластическому деформированию.
Большое значение придается также микроструктуре листовой стали. Чистота поверхности штампованных деталей может быть получена при наличии однородных мелких зерен феррита в пределах баллов № 6, 7, 8 по ГОСТ 5639-65. Применение стали с размером зерен № 1-4 ведет к разрывам при вытяжке и получению шероховатой поверхности. Допускается наличие структурно свободного цементита не более балла 2 по ГОСТ 5640-68. Для штампуемости металла имеет значение низкая твердость с узкими пределами ее колебания (HRC-45÷48).
Раскрой листового металла. Раскроем листового металла называется технологический процесс рационального расположения на листе шаблонов, очерчивания по ним контуров заготовок. В результате раскроя достигается комплектность требуемых заготовок и получение наименьшего отхода листового металла. Проведению раскроя листового металла предшествует трудоемкая работа по подбору деталей, одинаковых по материалу, толщине, комплектности, форме и габариту.
При раскрое листового металла пользуются шаблонами, изготовленными из листовой углеродистой стали, листового алюминия или фанеры, причем применяют шаблоны заготовок, позволяющие вырезать с припуском на последующую обработку или так называемые шаблоны развертки деталей, позволяющие вырезать точные заготовки, не требующие обрезки припуска после формообразования из них деталей.
Очерчивание контура или деталей по контуру шаблонов осуществляется стальной чертилкой.
На оборудовании для криволинейного разрезания заготовки вырезают сразу по их контуру, на оборудовании для прямолинейного разрезания листовой металл вначале разрезают на полосы, из которых затем вырезают заготовки требуемых размеров.
Резку заготовок выполняют ножницами с механическим приводом (криволинейными и наклонными ножами - гильотинными) двухдисковыми одностоечными ножницами с наклонными ножами, вибрационными (высечными) ножницами и ручным механизированным инструментом (дисковыми пневматическими или электрическими ручными ножницами) и др.
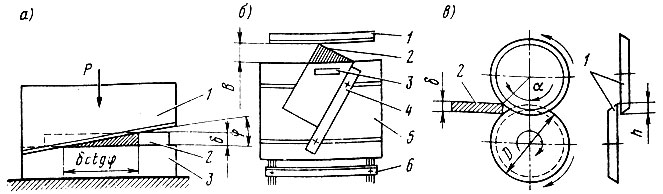 Рис. 53. Способы резки по прямым линиям: а - гильотинными ножницами: 1 - верхний нож; 2 - разрезаемый лист; 3 - нижний нож; б - схема настройки упоров на гильотинных ножницах; 1 - задний упор; 2 - отрезаемая заготовка; 3 - прижим; 4 - боковой упор или направляющая линейка; 5 - стол ножниц; 6 - передний упор; В - расстояние между режущей кромкой нижнего ножа и задним упором; в - роликовыми ножницами; 1 - нож; 2 - разрезаемый полуфабрикат; аα=7÷14° - угол захвата; D=(30÷70) δ-диаметр ножей; h=(0,2÷0,35) δ-величина захода ножей
Существует несколько способов резки листовых заготовок по прямым линиям и по криволинейным открытым и замкнутым контурам. Резку по прямым линиям осуществляют на гильотинных и роликовых ножницах (рис. 53). Усилие резки на гильотинных ножницах подсчитывают по формуле (кгс)
где φ - угол створа ножей (угол взаимного наклона режущих кромок ножей), град; σср - предел прочности материала при срезе; δ - толщина полуфабриката, мм.
С увеличением φ усилие резко уменьшается. Однако при увеличении φ возрастают потребный ход верхнего ножа и деформации изгиба и скручивания отрезаемой заготовки. Наивыгоднейший угол створа φ в зависимости от толщины разрезаемого листа (0,5-2,5 мм) составляет 1-6°.
Оптимальный зазор между режущими кромками, при котором получаются наилучшая поверхность среза материала, более высокая точность резки, наименьшее усилие резки и наибольшая стойкость режущих кромок, в большинстве случаев близок к 8-10% толщины металла.
Для резки сравнительно тонких листов, когда предъявляются повышенные требования к качеству реза, используют ножницы с параллельными ножами. Зазор s между ножами в этом случае определяют из выражения s=Lδ, где L - длина линии разделения заготовки.
Резку листов на гильотинных ножницах осуществляют по упорам, пример настройки которых приведен на рис. 53, б. Если размер В полосы или заготовки превышает 200-600 мм соответственно для толщины материала 0,5-2,0 мм, то резку выполняют по переднему упору. В этом случае отрезаемая полоса (заготовка) не провисает и точность резки выше, чем при резке по заднему упору.
Для продольной резки ленточного материала (со скоростью перемещения разрезаемой заготовки 15-36 м/мин) применяют роликовые ножницы.
Резку по криволинейным контурам выполняют дисковыми и вибрационными ножницами, а также штампами.
У наклонно поставленных под углом 45° ножей дисковых ножниц (рис. 54) режущие кромки образованы пересечением конических поверхностей. Это позволяет в процессе резки поворачивать лист относительно ножей и вырезать заготовки и детали, контур которых очерчен кривыми с относительно небольшими радиусами. Надежный "захват" листа при резке возможен в том случае, если диаметр ножей D≥30 мм. Но с увеличением диаметра ножей затрудняется резка по криволинейным контурам с малыми радиусами кривизны. Поэтому на практике применяют ножи, Диаметр которых не превышает 60-70 мм. Такими ножами возможна резка по кривой с радиусами кривизны менее 40-50 мм. Толщина о разрезаемого материала при этом не должна превышать - 1/30 D, Т. е. 2,5 мм.
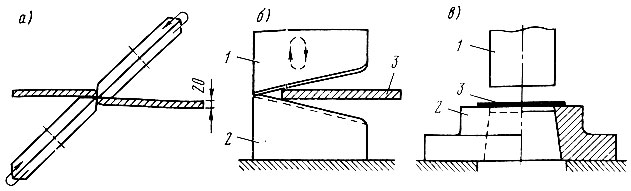 Рис. 54. Способы резки по криволинейным контурам: а - дисковыми ножницами; б - вибрационными ножницами; 1 - подвижный нож; 2 - неподвижный нож; 3 - разрезаемый лист; в - штампом; 1 - пуансон; 2 - матрица; 3 - полуфабрикат
Усилие резания дисковыми ножами определяют по формуле (кгс)
где h - величина захода ножей, равная σср - предел прочности материала при срезе, кгс/см2.
Если учесть наличие изгиба при резке, неравномерность толщины материала и притупление ножей, то расчетное усилие следует увеличить на 25%.
Схема резки на вибрационных ножницах показана на рис. 54, б. Верхний нож с амплитудой 2-3 мм совершает 1200-2000 возвратно-поступательных движений в минуту по замкнутой кривой. Нижний нож в процессе резки опускается и поднимается, что позволяет в широком диапазоне изменять величину захода ножей и вырезать как по наружным, так и по внутренним прямолинейным и криволинейным контурам заготовки с минимальным радиусом кривизны 12-15 мм.
Процессы формообразования холодным деформированием. Холодное деформирование является одним из наиболее прогрессивных методов изготовления заготовок и деталей. Наиболее широко применяемыми процессами для формообразования ремонтных деталей кузовов являются гибка, обтяжка и формовка.
К гибке относят все процессы формообразования деталей одинарной кривизны, основанные на упруго-пластическом изгибе внешними нагрузками листовой заготовки. При гибке волокна металла, расположенные у внутренней поверхности изогнутой заготовки, сжимаются и укорачиваются в продольном направлении и растягиваются в поперечном, а у внешней поверхности растягиваются и удлиняются в продольном и укорачиваются в поперечном направлении. Между удлиненными и укороченными волокнами (слоями) имеется нейтральный слой, длина которого равна первоначальной длине заготовки. Величина деформации материала в зоне гибки зависит от величины радиусов R гибки и толщины 6δ металла. Чем меньше радиус кривизны детали, тем больше деформация крайних волокон. При одном и том же радиусе кривизны детали большей толщины имеют большую деформацию. При очень малых радиусах гибки может произойти разрыв наружных волокон. Поэтому большое значение имеет правильный выбор радиуса гибки. Минимальный радиус загиба определяется из зависимости r=δk, где r - радиус загиба, мм; 6δ - толщина материала, мм; k -коэффициент, зависящий от свойства металла (качество металла, его пластичность и др.). Минимальное значение k для мягкой стали, алюминия и его сплавов равно 0,5, а дюралюминия отожженного или свежезакаленного - 2.
Опасность разрыва наружных волокон при гибке с соблюдением заданного радиуса кривизны повышается в том случае, если линия гибки располагается вдоль направления проката листа. Поэтому необходимо линию гибки заготовки располагать перпендикулярно к направлению волокон проката или под углом не менее 30°. Во избежание разрушения при гибке деталей с малыми радиусами гибки необходимо удалять заусенцы с кромок заготовок.
Гибка машинным способом осуществляется на специализированном оборудовании: кромкогибочных станках, листогибочных кривошипных прессах, профилегибочных прессах, профилегибочных роликовых станках, профильных растяжных станках, листогибочных станках и др.
Для изготовления ремонтных деталей одинарной кривизны из листов наиболее широко применяют методы свободной гибки и гибки профилированным инструментом. В последнем случае получаемая деталь по форме соответствует деформирующему инструменту. При свободной гибке формообразование детали осуществляется путем пластической деформации заготовки системой сил и создаваемая форма не зависит от инструмента.
Свободная гибка практически осуществляется двумя способами: на универсально-гибочном штампе и прокаткой на валковых или роликовых станках.
Гибкой универсально-гибочным штампом преимущественно изготовляют детали с малым относительным радиусом изгиба (обычно r≤8÷10 мм). Форму таких деталей в основном характеризует угол изгиба φ, являющийся сопрягаемым параметром при установке деталей в узлах и агрегатах. Угол φ (рис. 55, а), на который необходимо изогнуть заготовку, чтобы с учетом его последующего изменения вследствие пружинения получить заданный угол педали, а также потребное для гибки усилие Р со стороны пуансона, можно определить по формулам:
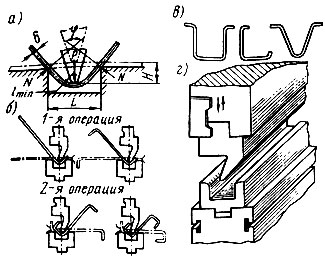 Рис. 55. Схемы свободной гибки на универсально-гибочном прессе
где Qmin - минимальный относительный радиус кривизны (при вершине угла), который для деформируемых материалов (алюминиевых сплавов и сталей) равен 2-7 (при несоблюдении этого условия наружная поверхность заготовки в процессе изгиба разрушается); m - константы деформируемого материала; cφ, ср ~ коэффициенты, зависящие от механических свойств металла, например для Д16А-М m-0,265; сφ=0,06, коэффициент ср при изгибе широких заготовок равен 4,50, а при изгибе узких заготовок (полосок) - 3,77.
По известным значениям Qmin определяют ширину ручья матрицы и ход Н пуансона.
Универсально-гибочные штампы используют в единичном и серийном производстве для изготовления из листового материала за несколько переходов или операций профилей различного сечения (рис. 55, б, в).
Штамп устанавливают на специальный гибочный пресс И-135 (рис. 55, г) с узкой длинной станиной и эксцентриковым приводом подвижной траверсы.
Гибка прокаткой на валковых и роликовых станках по силовому воздействию на заготовку (рис. 56) не отличается от гибки универсально-гибочным штампом. Процесс гибки прокаткой заключается в непрерывном изменении формы заготовки при приложении к ней через вращающиеся валки (или ролики) изгибающего усилия, обеспечивающего требуемую пластическую деформацию. Гибка прокаткой может быть осуществлена на станках, выполненных по трех- или четырехвалковой схеме.
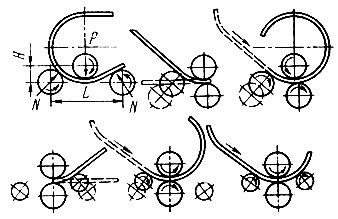 Рис. 56. Схема гибки прокаткой на валковых и роликовых станках
Оснастка, используемая при свободной гибке, является универсальной и позволяет путем подбора параметров настройки L и H (см. рис. 55, а) получать детали необходимой формы. Благодаря этому свободная гибка экономически наиболее целесообразна для деталей больших габаритов (например, угловых панелей кузовов автобусов, различных профилей из листового материала).
Наиболее распространенный вид оборудования для гибки прокаткой - трехвалковые станки с ручным приводом, у которых положение гибочного валка в процессе гибки не изменяется.
Гибка обтягиванием по оправке (гибка с растяжением) применяется для изготовления деталей переменной кривизны из гнутых и прессованных профилей симметричного или несимметричного сечения обычно на профилегибочных растяжных станках ПГР-6, ПГР-7, ПГР-8. Станки ПГР-6 и ПГР-8 предназначены для получения деталей однозначной кривизны с углом изгиба 180-220° из заготовок длиной 1000-9000 мм. Схема процесса гибки с растяжением деталей однозначной кривизны приведена на рис. 55.
На станке ПГР-7 с передней передвижной установкой, выполненной в виде самостоятельного отъемного агрегата, изготовляют по приведенной на рис. 56 схеме детали знакопеременной кривизны с наибольшей стрелой вогнутости до 600 мм.
Гибка обтягиванием по пуансону на профилегибочных растяжных станках обеспечивает высокую производительность и достаточную точность изготовляемых деталей. Область применения способа ограничивается возможностью получения деталей из профилей с углом изгиба 180-220° и относительным радиусом изгиба не менее 10 мм вследствие дополнительного нагружения профиля растягивающим усилием при его изгибе.
Обтяжка. Обтяжкой называют процесс формообразования деталей двойной кривизны растяжением листовых заготовок до полного прилегания последних к профилированной оправке. Этот процесс находит широкое применение при изготовлении крупногабаритных обшивок и деталей двойной кривизны с высоким отношением радиуса кривизны к толщине материала.
Обтягивание сопровождается изгибом, значительным утонением и упрочнением материала заготовки. Поэтому обтягиванием плоской заготовки удается получать лишь весьма неглубокие детали. Возможности процесса значительно расширяются, если обтягивать не плоские, а предварительно изогнутые листовые заготовки.
Простая обтяжка выполняется в основном на обтяжных прессах типа ОП с закреплением продольных кромок полуфабриката в самоустанавливающихся зажимах, оси поворота которых неподвижны относительно станины пресса. Формообразование деталей осуществляется за счет удлинения поперечных сечений заготовки под действием усилия, прикладываемого к подвижному пуансону.
Процесс обтяжки имеет свои ограничения, определяемые степенью деформации материала, которую он может претерпевать без разрушения. За меру степени деформации принимают коэффициент обтяжки Кобт, представляющий собой отношение длины Lд наиболее растянутого волокна после обтяжки к его первоначальной длине Lп:
где δ - относительное удлинение наиболее растянутого волокна. По данным НИИАвтопрома методом обтяжки и на универсальном оборудовании рекомендуется изготавливать детали при размере партии от 31 до 300 шт., а при размере партии деталей свыше 300 формовку целесообразно выполнять на листоштамповочных молотах с применением пластмассовых штампов или в штампах из цинкоалюминиевых сплавов или на прессах большой мощности по типу, установленных на ВАРЗе и других АРЗах.
Разновидностью операции листовой формовки является посадка кромок заготовки, при которой изменяется форма детали в результате сокращения длины кромки при одновременном ее утолщении. Достигается посадка тем, что вдоль кромки детали искусственно создают гофры, а затем, разглаживая эти гофры, добиваются утолщения кромки. Комбинация процессов гофро- образования и разглаживания гофров приводит к сокращению длины кромки. Эта операция выполняется на специальном посадочном станке типа И-006.
Ремонт кузова постановкой ДР. Процесс ремонта кузова постановкой ремонтных деталей (ДР) начинают с подготовки ремонтируемого участка к ремонту, включающей следующие работы: освобождение участка, подлежащего ремонту, от укрепленных к нему деталей и деталей, которые могут помешать выполнению ремонтного процесса или могут быть повреждены в процессе ремонта; разметка границы участка панели, подлежащего удалению (по результатам дефектации) по шаблонам; удаление поврежденного участка кузова; ремонт деталей каркаса кузова, находящихся под удаленной панелью; правка панелей, сопряженных с удаленным участком и обработка их кромок, не снятых с кузова; устранение сваркой трещин и разрывов на кузове. На подготовленный таким образом участок устанавливают новые панели или часть панелей (ДР).
Сложность удаления негодных панелей зависит в основном от способа их крепления к каркасу кузова.
В цельнометаллических кузовах сварной конструкции панели соединены между собой различными видами сварки (контактной, газовой или электросваркой). В автобусных кузовах имеются сварные и заклепочные соединения. На кузовах-фургонах с деревянным каркасом панели укреплены к каркасу гвоздями.
Панели, являющиеся частью всего корпуса сварной конструкции, вырезают газовым резаком (кислородная резка с использованием ацетилена или сжиженных газов), электрифицированным фрезерным инструментом или пневматическим резаком. Клепаные швы разъединяют удалением головки заклепки. Детали, укрепленные точечной сваркой, можно разъединить, предварительно наметив сварные точки керном, а затем просверлить места сварки через верхний лист. Иногда такие соединения удается разрубить острым тонким зубилом без разрушения годных деталей, к которым необходимо приварить новую панель.
После снятия разрушенной детали (панели, крыло), приваренной к кузову точечной сваркой, необходимо удалить тонким острым заточенным зубилом оставшиеся полоски снятой детали в соединениях с кузовом и зачистить шлифовальной машинкой посадочные места элементов кузова.
Сложность операций и объем работы при постановке новых панелей (часть панелей) на кузов зависят от тщательности изготовления панели и от способа ее крепления к кузову. Вновь изготовленные на авторемонтных заводах панели обычно требуют пригонки по месту их крепления на кузове. Пригоночные работы чаще всего сводятся к разметке панели по проему в кузове и вырезке детали по разметке или с допуском для крепления внахлестку; сверлению отверстий в панелях, крепление которых осуществляется при помощи заклепок; зачистке заусенцев и подгонке кромок при сварке встык.
Для выявления излишка металла новую панель накладывают на проем в кузове по месту ее крепления и размечают по кромкам контуров сопряженных с нею панелей. При креплении панели встык выявленный излишек металла отрезают по разметке, а при креплении внахлестку - по допуску, намеченному параллельно линии разметки.
Соединение панелей встык обычно осуществляется сваркой в среде углекислого газа или газовой сваркой, а соединение внахлестку - теми же способами, что при соединении встык, а также точечной сваркой. В кузовах клепаной конструкции применяются обычные заклепки и элетрозаклепки.
В нахлесточных соединениях в наружных поверхностях деталей кузовов целесообразна подштамповка или подсадка на зиг-машине одной из кромок во избежание появления "ступеньки" в соединении. При отсутствии необходимого оборудования подсадку можно выполнить ударным и опорным инструментом.
Подсадка кромок придает некоторую жесткость соединению и образует своеобразную подкладку, препятствующую короблению металла при правильном ведении процесса сварки и протеканию припоя, если применяется последующая спайка соединения. Такой тип соединения позволяет за счет нахлестки несколько смещать детали при сборке для соблюдения общего размера и тем самым исправлять неточность сборки. В отличие от сварки деталей встык не требуется точное совпадение кромок, однако необходимо совпадение поверхностей по плоскости. Поверхности металла в местах нахлестки должны быть защищены от коррозии и покрыты специальными красками, клеем или другими антикоррозионными составами.
Ремонтная деталь может быть закреплена зажимами для сварки или прихваткой в нескольких точках при помощи сварки. Во избежание коробления металла панелей в процессе сварки при отсутствии подсадки кромок, как указано выше, для ограничения распространения тепла горелки вдоль линии сварки укладывают влажный асбест.
При отсутствии контактно-сварочной машины приварку можно осуществлять газовой сваркой, предварительно просверлив по периметру посадочных мест новой детали отверстия диаметром 3-4 мм через 40-50 мм. Сварку следует вести по местам отверстий, применяя в качестве присадочного материала отожженную мягкую проволоку СВ-08 диаметром 1,5-3 мм. В процессе сварки и по ее окончании сварочные швы проковывают. После приварки ремонтных деталей сварные швы зачищают и панели кузова рихтуют.
Выше были рассмотрены общие вопросы, связанные с процессами изготовления ремонтных панелей и порядком постановки их на кузов взамен разрушенных.
В настоящее время некоторые автомобилестроительные заводы (АЗЛК, ВАЗ, ГАЗ) выпускают специальные ремонтные комплекты узлов для замены частей корпуса кузова при аварийных разрушениях. Поскольку в несущих конструкциях кузовов агрегаты ходовой части автомобиля и некоторые механизмы укреплены к полу кузова, после аварийных случаев необходимо проверить, не нарушились ли из-за деформаций точки крепления указанных агрегатов. Для этой цели, а также для правильной установки новых узлов взамен разрушенных применяются приспособления. Так, для контроля пола кузова автомобиля ВАЗ предложено приспособление (рис. 57), при помощи которого проверяют правильность расположения точек крепления деталей и узлов к полу кузова. Для этой цели в зарубежной практике применяют измерительное устройство, снабженное электрическим прибором, направляющими брусьями с рулеткой и скользящим прибором для измерения отклонений в точках крепления агрегатов. Измерительное устройство снабжено также прозрачными шкалами, градуированными в миллиметрах, устанавливаемыми на базовых точках основания кузова.
После аварии в первую очередь необходимо проверить, не нарушилась ли из-за деформаций установка передней или задней подвески, системы рычагов рулевого управления и т. и. Обнаруженную деформацию необходимо устранить и проверить точки крепления агрегатов и механизмов к полу.
Ниже для примера приводятся процессы ремонта стойки передка и замены переднего крыла автомобиля ВАЗ (предполагается, что с кузова сняты агрегаты ходовой части и обивка), заднего крыла и рамы автомобиля "Москвич-412".
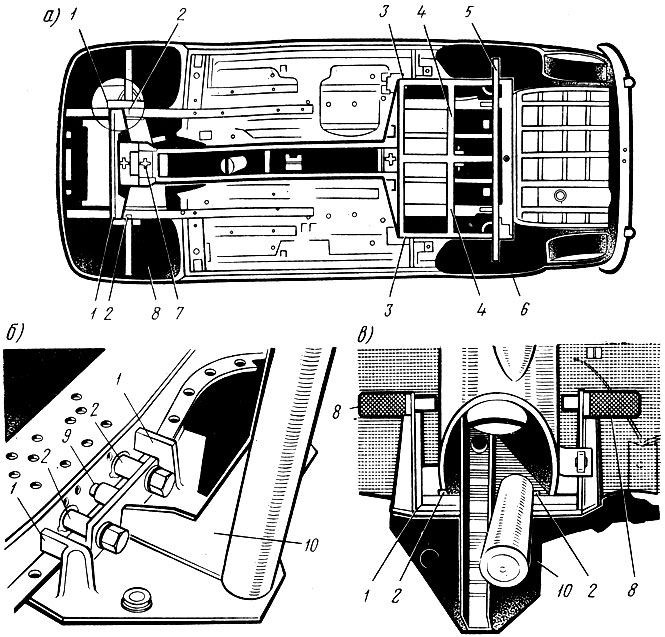 Рис. 57. Контроль пола кузова приспособлением A78124/R: а - установка приспособления; б - контроль положения болтов крепления поперечины передней подвески; в - контроль положения отверстий для крепления верхнего рычага передней подвески; 1 - упоры плоскости; 2 - установочные полые пальцы на болтах крепления поперечины передней подвески; 3 - установочные штифты крепления нижних продольных штанг задней подвески; 4 - установочные упорные поверхности контроля крепления к кузову верхних продольных штанг задней подвески; 5 - задняя часть приспособления; 6 - установочный штифт крепления к кузову поперечной штанги задней подвески; 7 - барашек, соединяющий переднюю и среднюю подвески; 8 - установочные пальцы по отверстиям для оси верхнего рычага подвески; 9 - установочный штифт; 10 - передняя часть приспособления
К стойке передка приварен кронштейн буфера передней подвески и в случае его деформации необходимо прежде всего проверить линейкой расстояние а между кромкой отверстия в кронштейне и кромкой чашки буфера (рис. 58). Этот размер должен быть на кузове автомобиля ВАЗ не менее 32 мм; если он меньше, то кронштейн необходимо заменить. Для снятия кронштейна очищают поверхность фланца от мастики, чтобы найти точки сварки, и высверливают их сверлом диаметром 6 мм на глубину толщины металла кронштейна. Затем выправляют выколоткой вмятины (если они небольшие) на стойке в месте приварки кронштейна через среднее отверстие в брызговике со стороны отсека двигателя до получения плоской поверхности стойки, после чего зачищают поверхность стойки и приваривают новый кронштейн электродуговой сваркой электродами Э-34 или Э-42 диаметром 1,6-2 мм. Кронштейн приваривают по периметру прерывистым швом.
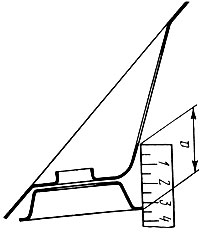 Рис. 58. Замер деформации кронштейна буфера хода сжатия передней подвески
Расстояние от края кронштейна до криволинейной поверхности стойки (рис. 59) должно быть 9,5 мм.
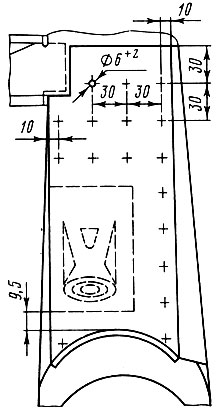 Рис. 59. Установка накладки на стойке передка
Если стойка сильно деформирована, то после удаления кронштейна и правки стойки следует изготовить по месту накладку из листовой стали толщиной 1,5 мм для усиления стойки и просверлить в ней отверстие диаметром 6-8 мм, выдерживая размеры, указанные на рис. 59. Затем зачищают поверхность стойки и приваривают накладку электродуговой сваркой по периметру и отверстиям.
Ниже приводятся процессы замены переднего крыла автомобиля ВАЗ и заднего крыла автомобиля "Москвич-412" после общей разборки кузова. Чтобы снять крыло автомобиля ВАЗ, срубают по крылу тонким остро заточенным зубилом: соединение остова на 280 мм от фары вниз; соединение крыла с панелью передка, отступив 2-3 мм от линии соединения крыла с передней стойкой боковины остова длиной 580 мм и 5 мм от линии изгиба вертикального усилителя; соединения крыла с нижней частью боковины кузова по вертикали 120 мм и по горизонтали 180 мм, отступив от кромки крыла 25 мм. Затем засверлива- ют на горизонтальном усилителе крыла точки контактной сварки усилителя с элементами передней части кузова на расстоянии 900 мм и отсоединяют крыло от кузова плоским тонким зубилом с отогнутым концом. После снятия крыла удаляют оставшиеся полоски крыла в соединениях с кузовом острозаточенным тонким зубилом и зачищают шлифовальной машинкой посадочные места элементов кузова и нового крыла.
Устанавливают на кузов и подгоняют новое крыло по месту посадки, прихватывают струбцинами и приваривают крыло газовой сваркой: по концам горизонтального усилителя крыла, в местах соединения крыла с кожухом фары и нижней накладкой боковины.
Затем проверяют посадку крыла и приваривают его к кузову контактной сваркой с шагом 40-50 мм (рис. 60).
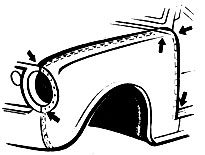 Рис. 60. Линия сварки переднего крыла, обозначенная точками (места предварительной приварки газовой сваркой указаны стрелками)
В процессе сварки и по ее окончании сварной шов проковывают при помощи молотка и поддержки, затем сварной шов тщательно зачищают.
Замену заднего крыла, приваренного к кузову автомобиля "Москвич-412" или ГАЗ-24 "Волга", осуществляют следующим образом: намечают карандашом или мелом линию среза по всему периметру крыла таким образом, чтобы оставить полосы шириной 20-30 мм на передней части крыла и по арке проема колеса, а по верхней части крыла - до его фланца (рис. 61). Старое крыло вырезают по разметке зачистной машинкой с отрезным абразивным кругом или зубилом и ножницами для резки листового металла, проявив при этом осторожность, чтобы не повредить внутренние детали корпуса, укрепленные к кузову под крылом в местах выреза. Если после удаления старого крыла оставшиеся на кузове фланцы верхней его части не позволяют тщательно подогнать новое крыло по месту его крепления, эти фланцы удаляются высверливанием точек контактной сварки со стороны приваренного фланца на глубину его толщины с последующим отсоединением фланца от кузова при помощи плоскогубцев или тонкого острого зубила. Для высверливания сварных точек следует пользоваться сверлом диаметром 6 мм, заточенным под углом 150-160°.
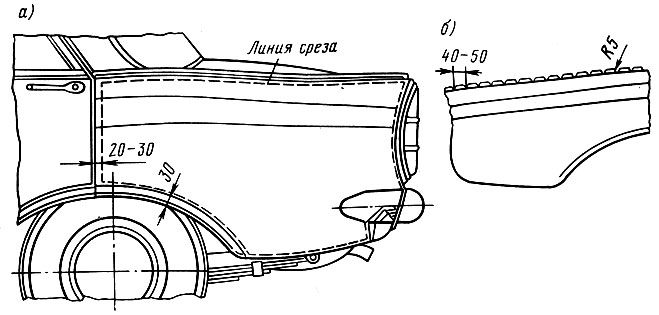 Рис. 61. Замена заднего крыла легкового автомобиля: а - разметка линии среза крыла; б - вырезы на фланцах
При сверлении отверстий следует учитывать особенность конструкции, чтобы не просверлить внутренние детали. По этим же соображениям обрезку по арке проема колеса и нижней части крыла производят без применения сверла.
После отрезки крыла тщательно подравнивают и зачищают до металлического блеска поверхности фланцев, к которым надлежит приварить новое крыло. На последнем делают вырезы радиусом 5-7 мм с шагом 45 мм по всему периметру, подлежащему приварке. Устанавливают и подгоняют по месту крепления новое крыло и плотно прижимают его при помощи струбцин. Сварка производится только по кромкам выкусов. Последовательность приварки должна быть следующей: приваривают сначала в трех-четырех местах верхнюю переднюю часть, затем нижнюю заднюю часть сверху в районе фонаря, а после этого по арке проема колеса и т. д. до окончательной приварки крыла. В процессе сварки и по ее окончании сварной шов проковывают молотком и поддержкой и сварной шов тщательно зачищают.
Если продольные балки рамы двигателя автомобиля "Москвич-412" значительно деформированы, необходимо заменить раму. Автомобильный завод имени Ленинского комсомола поставляет в запасные части ремонтный комплект № 412-2801950, включающий собственно раму, брызговики передних крыльев и полку щитов радиатора с щитами в сборе. Заменяют раму в следующей последовательности. Сначала отрезают пламенем газовой горелки продольные балки рамы в местах приварки их к полу, щиту передней части кузова, угольнику щита и распоркам продольных балок рамы, а затем брызговики передних колес и косынки брызговиков от щита передней части кузова.
Продольные балки и брызговики следует отрезать в местах, показанных жирными линиями на рис. 62, возможно ближе к углам их полок 1 и 2, а в местах соединения усилителя щита и передней части кузова с брызговиками и косынкой продольной балки рамы - на расстоянии 10-15 мм от щита передней части кузова. После отрезки продольных балок и брызговиков тщательно зачищают поверхности и кромки деталей, к которым должны быть приварены новая рама и сопряженные с ней узлы, от наплывов и выполняют необходимый ремонт деталей передней части кузова (выправляют панели пола и щита, заваривают трещины и разрывы с усилением мест сварки постановкой накладок из листовой стали и др.).
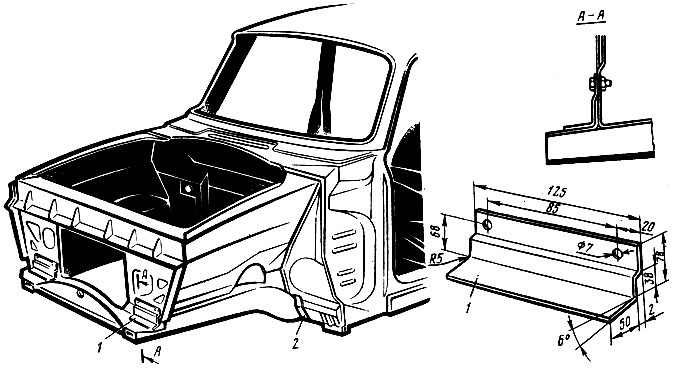 Рис. 62. Передняя часть кузова автомобиля 'Москвич-412'
Перед установкой рамы, брызговиков и полки щитов радиатора с поверхностей, подлежащих сварке, должно быть снято защитное покрытие (окраска их или грунтовка производится на заводе).
Новую раму устанавливают на приспособлении (рис. 63) так, чтобы задние концы продольных балок рамы вошли в пазы боковых фиксаторов 2, а в передней части закреплялись к фиксаторам 1 двумя болтами. Затем несколько приподнимают переднюю часть кузова, подводят под нее приспособление в сборе с установленной на него рамой, опускают переднюю часть кузова на продольные балки так, чтобы они плотно прилегали к полу, а средний фиксатор 4 вошел в туннель, проходящий вдоль пола, и прикрепляют приспособление задними фиксаторами 3 к передним кронштейнам рессор на кузове.
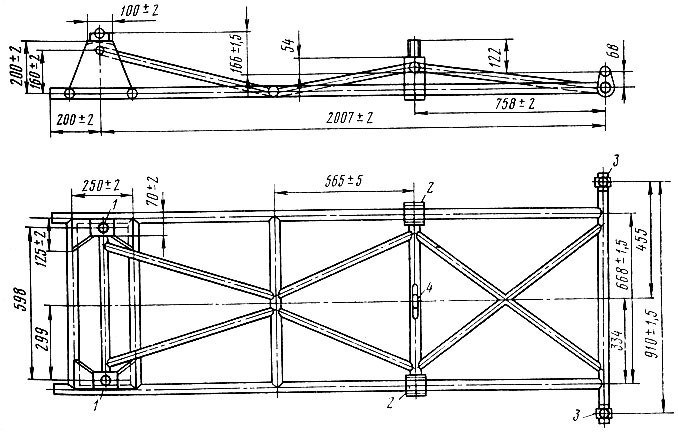 Рис. 63. Приспособление для замены рамы двигателя
Правильность положения рамы относительно кузова проверяют прикреплением картера рулевого механизма к продольной балке рамы; при этом отверстия верхней точки крепления рулевой колонки должны совпадать с отверстиями в поперечине передка кузова.
После проверки правильности установки рамы приваривают продольные балки рамы к полу кузова и сопряженных с ней других узлов (брызговики передних крыльев, полка щитов радиатора) в следующей последовательности.
Приваривают продольные балки рамы к полу кузова и щиту передней части кузова. При помощи накладок 2 (см. рис. 62) соединяют распорки продольных балок рамы с рамой. Накладки приваривают сплошным швом. Устанавливают при помощи угольников полку щитов радиатора. Угольники прикрепляют к щитам радиатора болтами М6×1, используя резьбовые отверстия для болтов крепления брызговика облицовки радиатора. Приваривают предварительно щиты в нескольких местах к косынкам первой поперечины рамы. Устанавливают брызговики передних крыльев и приваривают их в нескольких точках к щиту передней части кузова, продольным балкам рамы, полке щитов и щитам радиатора. Проверяют правильность положения брызговиков и полки щитов радиатора по отношению к кузову, для чего предварительно устанавливают крылья, капот и брызговик облицовки радиатора. Проверяют зазоры по капоту и дверям, а также совпадение отверстий для крепежных деталей в панелях кузова. Зазоры должны быть равномерными и равными 5-7 мм. Отверстия для крепежных деталей должны совпадать.
В случае большого несовпадения отверстий или же большей неравномерности зазоров, предварительную приварку брызговиков и полки срубают и корректируют их положение.
В случае соединения деталей дуговой сваркой рекомендуется применять электроды диаметром 3-5 мм и осуществлять сварку постоянным током при силе тока 110-130 А. Во избежание прожогов металла свариваемые детали тщательно подгоняют друг к другу (по месту). Сварку ведут прерывистым швом с длиной участка 30-40 мм и с промежутками между участками 25-35 мм. Сварку можно проводить также контактным способом.
После проверки всех мест сопряжения рамы, брызговиков и полки щитов радиатора снимают с кузова установочное приспособление и распорку, соединяющую задние концы продольных балок (распорка ставится при отправке рамы с завода).
После сварки швы зачищают под грунтовку и окраску. Чтобы не ослабить шов, его зачищают только по поверхности.
Приспособление (см. рис. 63) для установки рамы изготавливают из стальных труб (диаметром 42 мм, толщиной стенки 2 мм для рамы и диаметром 25мм, толщиной 1,25мм для диагоналей), а основание передних фиксаторов - из листовой стали толщиной 6-8 мм. При изготовлении приспособления очень важно выдержать размеры, указанные на рис. 63, и обеспечить высокую жесткость конструкции во избежание появления серьезных неполадок в процессе эксплуатации автомобиля после установки новой рамы (увод в сторону, перегрузка узлов и деталей рулевого управления и др.).
Кроме приспособления, следует еще изготовить два угольника для фиксации полки щитов радиатора относительно продольных балок рамы. Материалом служит листовая сталь толщиной 2,0-2,5 мм.
|